فرصتهای علاقهمندی ویژه در ساخت ایمپلنتهای پزشکی شامل توانایی ساخت هندسههای دقیق و راحت برای بیماران، یا بر اساس اطلاعات تصویری پزشکی و یا بسته به نیازی که در حین جراحی توسط رباتهای جراحی و با فیلمبرداری داخلی صورت میگیرد]4[؛ تولید ساختارهای شبکهای پیچیده برای موقعیتهایی که رفتار مکانیکی از استخوان مادر قابل تشخیص نباشد]5[، ساخت ایمپلنتهای شبکهای که بهصورت الگوریتمی طراحی شدهاند که در نتیجه باعث طراحی ایمپلنتهای ارزان قیمت با خواص مکانیکی و هندسه ویژه بیمار میشود]6[.
باوجود این فرصتهای ویژه، یکسری قوانین و چالشهای تکنیکی برای کاربردهای AM در طراحی ایمپلنتهای دائمی، بایستی رعایت شوند. این چالشها شامل نیازهای قانونی برای تأیید تولید انبوه ایمپلنتهای AM، و چالش برانگیزتر، گواهی راهنمای ساختار ویژه- بیمار، میباشند]7[. چالشهای تکنیکی شامل قیدهای هندسی متناسب با مواد و فرآیندهای AM ؛ پیشبینی قبلی از میدانهای دمایی و اثراتشان بر خواص هندسی و مکانیکی؛ اثر هندسه خاص که بر تمرکز تنش ایجاد میکند؛ و بیولوژیک مرتبط با پارامترهای هندسی شامل سختی سطح و حضور ذراتی که به صورت جزئی چسبیدهاند.
موانع مشخص در برابر کاربردهای تجاری AM در طراحی ایمپلنت، عدم وجود ابزارهای طراحی که فرآیندهای خودکار طراحی ایمپلنت AM را فراهم میکنند]9و8[. در این کار، خلاصهای از فرصتهای تکنیکی مرتبط با طراحی ابزار AM (DFAM) برای طراحی ایمپلنت آورده شده و همچنین یک مروری بر ابزار موجود و چالشهای مرتبط با آنها جمع آوری شده است که شامل:
-
فرآیندهای AM در دسترس برای ساخت ایمپلنتهای تیتانیومی.
-
اطلاعات تجربی بر روی تولید ساختارهای AM تیتانیومی.
-
ساختارهای سلولی و پاسخ مکانیکی شبکه.
-
ذخیره اطلاعات و چالشهای مرتبط با ذخیرهسازی اطلاعات و اندازه فایلها.
-
دستیابی به سازگاری هندسی مطابق با هندسهی کاشت ایمپلنت.
-
بهبود خواص سطحی.
این فرصتهای DFAM با ارجاع به فلسفهی ایمپلنتهای درجا (JIT)، نشان داده شدهاند که طراحی شبکههای الگوریتمی، مدیریت اطلاعات و تولید افزایشی AM با رباتهای جراح و تصویرسازی به منظور تهیهی ایمپلنت خاص بیمار براساس شرایط مورد نیاز در همان محل جراحی را شامل میشود.
3-1-2 تولید افزایشی
AM اشاره به تولید قطعات یکپارچه از مواد خام]2[، به صورت لایهنشانی میباشد]10[. AM بهطور اساسی با روشهای ساخت کاهشی همانند، روشهای قدیمی ماشینکاری]11[، متفاوت است، که در نتیجه منجر به یکسری فرصتهای اقتصادی و مهندسی از جمله هزینههای رقابتی برای تولیدهای حجمی پایین]12[، طراحی محصول سفارشی بهصورت انبوه]13[، کاهش اثرات زیست محیطی تولید]14[، و افزایش طراحیهای پیچیده]15[ میشود. تولید افزایشی فلزی MAM، اشاره به یکی از زیرمجموعههای AM دارد که مطابق شکل 3-1-1 ]16[، از مواد فلزی به عنوان ورودی استفاده میشود؛ که برای طراحی ایمپلنتهای تیتانیومی بسیار مورد توجه قرار گرفته است.
MAM توسط سیستمهای تجاری متعددی اجرا میشود[17]. یکی از این سیستمهای تجاری، سیستمهای ذوب بستر پودر PBF بوده، که ویژگیهایی مانند اندازه، خواص مکانیکی و هزینههای واحدی سازگار برای نیازهای کلینیکی، ساختاری و اقتصادی برای تولید ایمپلنتهای پزشکی فراهم میکند.
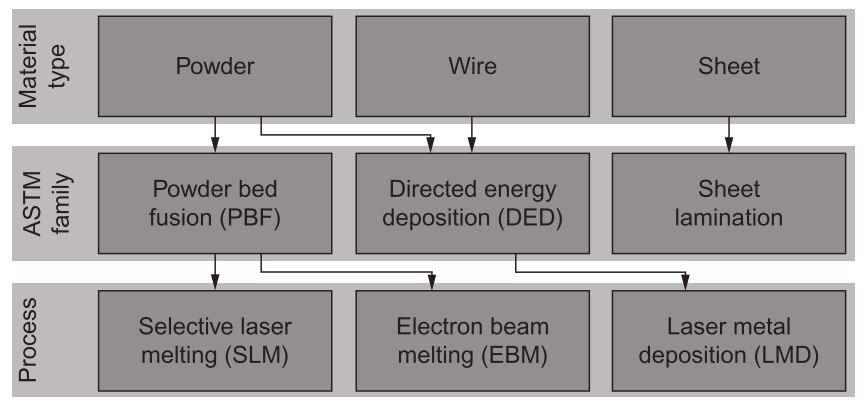
شکل 1-1-3 دستهبندی تولید افزایشی فلزات MAM مطابق با استاندارد ISO/ASTM ]16[
3-1-2-1 ذوب بستر پودر
فرآیند PBF اشاره به یکی از فرآیندهای MAM دارد که در آن هندسههای فلزی با رسوب و ذوبکردن پودر بر یک بستر پودری ایجاد میشود. این پودر در اثر قرارگرفتن در معرض منبع گرما، که معمولاً لیزر یا پرتوی الکترونی میباشد، ذوب شده و از طریق خلأ یا گاز محافظ، از اکسیداسیون محافظت میشود. تولید بهصورت تکرار شونده به شرح زیر است:
-
دستگاه پوششدهی، لایههای از پورد فلزی را روی بستر پودر توزیع میکند]18[.
-
یک منبع گرما بهطور انتخابی پودر را با مواد جامد اطرافش ذوب میکند]19[.
-
بستر پودر به صورت تدریجی به ضخامت لایه مورد نظر کاهش مییابد ]20[.
سیستمهای PBF از نظر فنی به خوبی توسعه یافتهاند و میتوانند به وضوح هندسی با پیچیدگیهای بالا دست یابند. علاوهبراین، چگالی قطعات تولیدشده به 100% نزدیک بوده و خواص مکانیکی ماده تولیدشده، بالا میباشند]21-23[، که استحکام و سفتی ویژهی بالایی را ایجاد میکند]24,25[. این ویژگیهای فنی کاملاً با انتظارات هندسی و مکانیکی بالک ایمپلنتهای قدیمی و ساختار شبکهای پیشرفته، سازگار است (شکل 1-1-3). از بین سیستمهای PBF موجود، ذوب لیزر انتخابی (SLM) و پرتو الکترونی انتخابی (SEBM) فناوریهای بالغ تجاری هستند.
3-1-2-2 ذوب لیزر انتخابی
SLM توسط مؤسسهی Fraunhofer گسترش یافته است]1[، و یک فرآیند PBF بوده که از یک منبع گرمای لیزر استفاده میکند تا بهطور انتخابی، پودر را در یک استخر از پودر، ذوب کند. شدت لیزر SLM از W100 تا KW1 متغیر است]26,27[، و معمولاً از توزیع گوسین تبعیت میکند. این لیزر توسط گالوانومتر در راستای بستر پودر اسکن میشود تا استخر مذاب تولید کند و پودرهای ذوب نشده را ذوب کند. بستر پودر ممکن است گرم شود و اکسیداسیون با استفاده از گاز محافظ بیاثر کنترل میشود]17[. ضخامت لایهی SLM معمولاً در حدود µm30-90 میباشد]28[. بهمنظور جلوگیری از ایجاد نواقص در حین تولید در لایههای مختلف، جهت اسکن در کل مراحل تولیید تغییر میکند]29[. SLM بهطور گسترده در ساخت قطعات با ارزش بالا و سازههای شبکهای مهندسیشده مورد استفاده قرار گرفته است (شکل 1-1-3) که بهطور مثال در شکل 2-1-3 آورده شده است]30-33[.
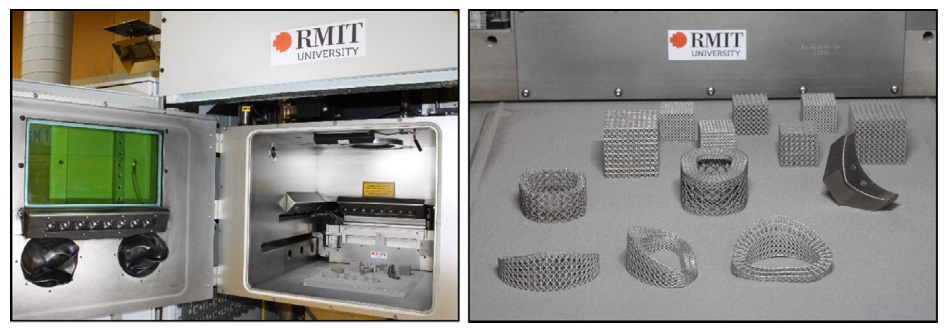
شکل 2-1-3 ذوب لیزر انتخابی سازههای ایمپلنتی شبکهای تیتانیومی.
3-1-2-3 ذوب پرتو الکترونی انتخابی
SEBM بهطور تجاری توسط شرکت Arcam AB گسترش یافته است]34[. SEBM از یک پرتوی الکترونی برای تولید گرمای موضعی استفاده میکند]35[. سیستم پرتوی الکترونی به خلأ بالایی نیاز دارد که به از بین بردن اکسیداسیون نیز کمک میکند]36,37[. ضخامت لایهی SEBM در حدود µm50-150 میباشد]36[. فنآوریهای تجاری SEBM امکان پیشگرم کردن بستر پودری بسیار بالایی را فراهم میکند که در نتیجه تنشهای باقیمانده را کاهش میدهد]38,39[. SEBM یک فرآیند تولید تجاری تأسیسشده برای کاربردهای پزشکی و ساختاری است]40-47[.
3-1-2-4 نامزد مواد PBF
فرآیندهای PBF باهرمادهی قابل استفادهای، سازگار است، اگرچه برخی فلزات که شامل بازتابندگی بالا یا پایین هستند، از نظر فنی چالش برانگیز میباشند. با این حال، موادی مانند فولاد ضدزنگ L316 و آلیاژهای کبالت- کروم]48[ برای ساخت ایمپلنت مورد استفاده قرار میگیرند، در حالی که مواد جایگزین مانند آلیاژهای تانتالیوم در حال گسترش هستند]49,50[. تیتانیوم یکی از متداولترین مادهی ایمپلنتی فلزی است]51-56[.
تیتانیوم بهخوبی برای ایمپلنتهای ساختاری در نظر گرفته میشود، زیرا زیستسازگاری استثنائی]57-59[ و استحکام نسبی استاتیک و دینامیکی بالایی را فراهم میکند]60[. Ti-6Al-4V بهطور تجاری در دو ردهی 5 و 23 بینابین کم و زیاد (ELI) تولید میشود. رده 23 ELI انعطافپذیری بالاتر (ولی استحکام پایینتر) نسبت به رده 5 دارد و معمولاً برای ایمپلنتهای اورتوپدی اختصاص مییابند (شکل 1-1-3). باوجود مزایای فنی Ti-6Al-4V به عنوان مادهی ایمپلنتی، ساختن آن با روشهای قدیمی دشوار است؛ به عنوان مثال، ریختهگری و ماشینکاری به ترتیب، به دلیل واکنشپذیری و هدایت حرارتی کم تیتانیوم، چالش برانگیز هستند]61[. این چالشهای فنی کمتر به AM مربوط میشوند، در نتیجه فرصتی برای ایجاد تغییر در روشهای ساخت و ایجاد محیط جدیدی از طراحی ایمپلنتها فراهم میشود.
3-1-3 قابلیت ساخت و تولید
PBF یک برهمکنش بسیار پیچیده میان پدیدههای متعدد فیزیکی بسیار گذرا میباشد]63[. علاوهبراین، پیچیدگی بدستآوردن دادههای تجربی در فرآیند، همراه با ماهیت بسیار تصادفی PBF، منجر به عدم اطمینان قابل توجهی در پیشبینی قبل از تولید میشود. تحقیقات تجربی مجموعهای از حالتهای شکست احتمالی تولیید را که میتواند در PBF رخ دهد را شناسایی کرده است که شامل (شکل 3-1-3) شکست ساختار حمایتکننده برای بارگذاری حرارتی زمینه که در نتیجه منجربه خرابی ترمومکانیکی ساختار شبکه میشود (شکل a3-1-3)؛ گرمشدن بیش از حد بندهای شبکه با یک شیب تند به سمت بستر ساخت پودر به دلیل افزایش دمای موضعی (شکل b3-1-3)؛ اعوجاج حرارتی (شکل c3-1-3)؛ اکسیداسیون ناشی از خرابشدن گاز محافظ (شکل d3-1-3).
فرآیند PBF با بیش از 130 پارامتر مستقل از نفوذ، بسیار ابعادی است]64,65[. این ابعادی بودن، همراه با چالشهای دستیابی به دادههای آزمایشی درجا و همچنین ماهیت تصادفی بودن MAM، منجر به عدم اطمینان ویژهای بر تأثیر پارامترهای فرآیند بر کیفیت بخشهای تولید شده، میشود]66,67[. بهینه پارامتر فرآیند بهصورت تجربی بدست میآید، بهطور مثال شکل 4-1-3 تخلخل بالایی از نمونه را نشان میدهد.

جدول 3-1-1 ترکیب مشخص شدهی Ti-6Al-4V برای ردههای 5 و 23 ELI ]62[
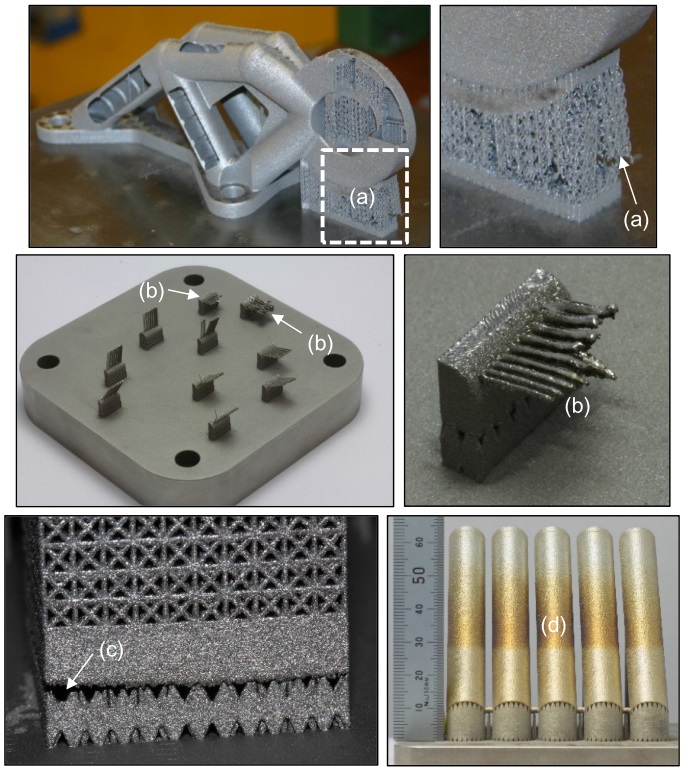
شکل 3-1-3 عیوب نمونهی PBF تولید شده
a) استحکام ناکافی در ساختار حمایتی. b) هندسه مشبک با یک شیب بسیار تند با انحراف بیش از حد چشمه گرما که منجر به گرمای اضافی شده.
c) اعوجاجات گرمایی. d) خراب شدن گاز محافظ که منجر به اکسیداسیون شده.
3-1-3-1 وضوح هندسی و دقت
نواقص تولید بهطور طبیعی مسائل مربوط به وضوح هندسی و دقت نمونه را ایجاد میکند بهطوری که محصول تولیید شده دقیقاً هندسهی مورد نظر را نشان نمیدهد (بخش 1-3-1-3). منابع این عیوب هندسی شامل (شکل 5-1-3)، خطاهای پلهپلهای همراه با گسستگی هندسی در جهت ساخت؛ کاهش مواد مذاب چسبناک در منطقه مذاب و ناحیهی دما بالا؛ مشکلات انجماد که به دلیل عدم تطابق میان توزیع منبع انرژی و هندسه در نظر گرفته شده رخ میدهد؛ و ذرات پودری ذوبشدهی جزئی که تمایل به چسبیدن به هندسه بالک بهویژه در مناطق که دارای سطوح روبه پایین هستند را دارند.
فرآیند AM، معمولاً هندسه را به برشهای منشوری عمود بر بستر پورد تفکیک میکند. در نتیجه، هندسهی تولیدشده، یک تقریب گسستهای از هندسهی پیوستهی مورد نظر است. این خطا بهدلیل مشکل ظاهری ایجاد شده، بهصورت پلهپلهای شناخته میشود، که فقط در هندسهی صفحاتی عمود بر بستر پورد رخ میدهد. این مشکل در ضخامتهای لایهای زیاد و زمانی که هندسه در نظر گرفتهشده دارای زاویه تند نسبت به بستر پورد باشد، تشدید میشود (شکل a5-1-3). با چرخش مؤلفهها در حجم ساخت به منظور کاهش اثرات پلهپلهای در مکانهای بحرانی]68[، و با کاهش ناصافی سطح با فرآیندهای نهایی شیمیایی و مکانیکی]69[، میتوان به مدیریت این خطاهای پلهپلهای دست یافت.
همجوشی MAM، زمانی اتفاق میافتد که منبع انرژی که معمولاً لیزر یا پرتوی الکترونی است، با پودرهای فلزی جامد برهمکنش داشته باشد (بخش 1-2-1-3). برای PBF، استخر مذاب بهطور فیزیکی توسط ترکیبی از فلز و پودر جامد، حمایت میشود. نیروهای گرانشی استخر مذاب را به سمت بستر پودر جذب میکنند که منجر به اعوجاج هندسهی تولییدی توسط 2 مکانیزم میشود. در ابتدا، نیروهای گرانشی استخر مذاب را به سمت بستر پودر معوجج میکنند. در ادامه، این اعوجاج منجر به ارتباط بیشتر میان استخر مذاب و پودر جامد میشود، که انتقال حرارت را تشویق کرده و اندازه استخر مذاب را در جهت بستر پودر افزایش میدهد. از ترکیب این مکانیزمها میتوان به عنوان سقوط استفاده کرد، زیرا منجر به بزرگشدن هندسه تولید شده در جهت بستر پودر میشود (شکل b3-1-5).
فرآیندهای MAM، از جمله PBF و LMD، از یک منبع انرژی متمرکز برای ذوب کردن انتخابی مواد پودر استفاده میکنند. این منبع انرژی دارای توزیع هندسی خاص و زمان پاسخ به منبع انرژی است. این محدودیتهای عملی، خطاهای انجمادی همانند تخلخل و خطای هندسی را در مناطقی با ناپیوستگی در مسیر استخر ذوب وجود دارند، مانند آنچه که در لبههای تیز رخ میدهد را ایجاد میکند (شکل c3-1-5). خطاهای انجماد را میتوان با پارامتر فرآیند و بهینه سازی استراتژی اسکن و با اطمینان از این امر که مناطق با احتمال تخلخل بالا، عملکرد ساختاری مورد نظر را به خطر نمیاندازند، مدیریت کرد.
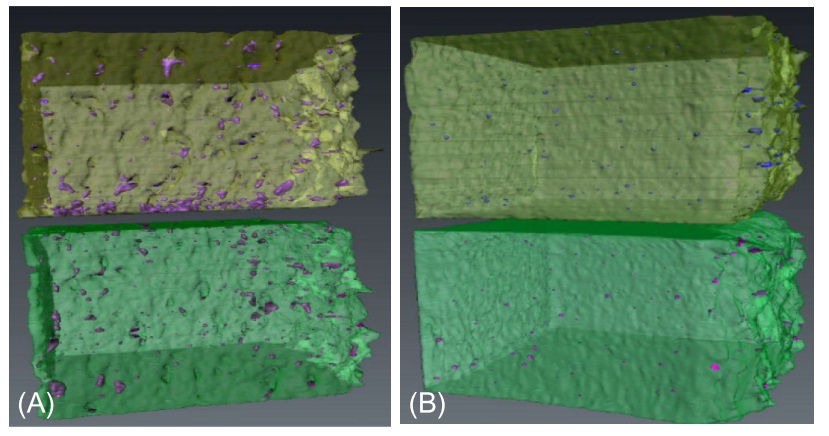
شکل 4-1-3 آنالیز CT میکرونی از نمونه SLM با:
A) پارامترهای فرآیند میکرونی، تخلخلهای قابل توجهی را نشان میدهند. B) نتیجه بهبود پارامترهای آزمایشی.
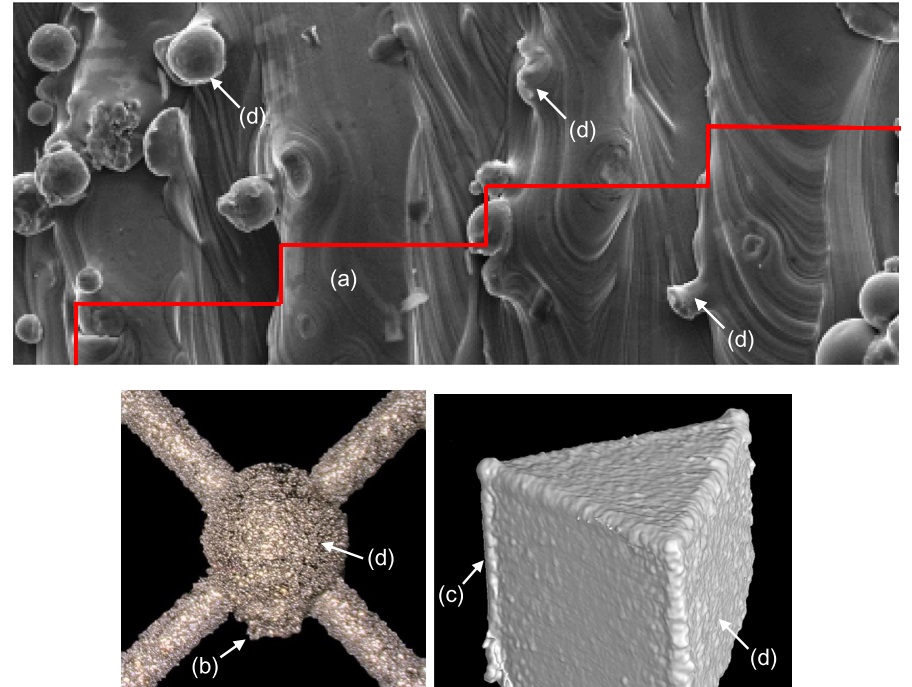
شکل 5-1-3 عیوب هندسی مرتبط با Ti-6Al-4V تولیدشده.
a) خط قرمز اثر پلهای شدن را نشان میدهد بهطوری که هندسهی AM جدایش یافته، سعی در تولید مجدد هندسهی پیوستهی ورودی را دارد. b) عیب سقوط ناشی از اثر گرانشی رشد هندسه پشتیبانی نشده به سمت بستر پودر.
c) عیوب انجمادی میتواند باعث بروز تخلخل و خطاهای هندسی شود و بهدلیل ناپیوستگی در مسیر استخر ذوب رخ میدهد. d) پودر ذوب شدهی جزئی همانطور که در بخش 2-3-1-3 توضیح داده شد.
3-1-3-2 انجماد استخر مذاب
انجماد استخر مذاب یک اتفاق سیال- حرارتی بسیار گذرا است]63[. پودر در مجاورت استخر مذاب با توجه به عوامل متعددی از جمله نزدیک بودن استخر ذوب، مقاومت در برابر تماس حرارتی، مورفولوژی پودر و نفوذ حرارتی، گرم میشود. بسته به این عوامل، پودر یا توسط استخر ذوب، جذب میشود و جامد و بدون دستخوردنی باقی میماند، یا تا حدودی ذوب میشود و به محصول جامد متصل میشود.
پودر جزئی ذوب شده به طور پیوسته به ساختار بالک متصل است، اما از لحاظ هندسی و ریزساختاری متمایز است. پودر جزئی جذب شده ترجیحاً در مناطقی با سطوح رو به پایین به دلیل دمای موضعی بالا و قرارگرفتن در معرض مستقیم سطوح روبه پایین در برابر پودر غیرقابل استفاده در معرض پودر پشتیبان، ایجاد میشود (شکل 6-1-3). بهطور عکس، سطوح روبه بالا فقط در حین فازهای پوششی بعدی در معرض پودر بلااستفاده قرار میگیرند که در این زمان، دمای موضعی کاهش یافته است. اثر هندسی پودر جزئی ذوب شده تابعی از خصوصیات حرارتی مواد، میدانهای دماهای موضعی و چرخش جزئی است؛ که اثر آن در تمرکز تنش و رشد استخوان بایستی در طراحی شبکه AM مورد توجه قرار گیرد.
3-1-4 طراحی شبکه و ساختار سلولی
مواد سلولی، ساختارهای تکرار شوندهای هستند که به صورت خود به خود فضا را پرکردهاند. مواد سلولی خواص مکانیکی و بیولوژیکی منحصربهفردی را از خود نشان میدهند و در تمام مواد طبیعی وجود دارند]70[. پاسخ مکانیکی مواد سلولی به آرایش و هندسهی موضعی که میتواند یا به صورت سلولی باز یا بسته و یا به صورت تناوبی یا منظمشده باشد.
مواد سلولی مهندسیشده شامل فومهای فلزی که نمونهای از ساختار سلولی منظمشده میباشد، است. فومهای فلزی به دلیل نسبت سفتی به جرم ویژه و جذب انرژی بالا تا کرنشهای زیاد، فرصتهای مهندسی زیادی را فراهم کردهاند]71[. چالشهای استفاده از فومهای فلزی در طراحی ایمپلنت شامل محدودیت در برهمکنشهای بیولوژی بهدلیل وجود ساختار سلولی بسته و مشکل در کاهش سفتی سلول به استخوان بیمار مورد نظر، به دلیل پاسخ ساختاری غالب سلول در برابر خمیدگی میباشد (بخش 1-4-1-3). ساخت افزایشی مواد سلولی به دلیل فراهم شدن طراحی منفرد سلولها با ساختارهای باز یا بسته و با آرایش ویژه سلولی مهندسیشده، بر این چالشها غلبه کرده است.
3-1-4-1 پاسخ ساختاری شبکه
ساختارهای مشبک به ساختارهای سلولی با آرایش سلولی باز گفته میشود. چنین ساختارهایی با MAM بسیار سازگاری برجستهای دارند، زیرا جز حجمی کاهش یافته باعث افزایش میزان تولید میشود و باعث از حذف پودر استفاده نشده میشود. سازههای مشبک با کاربردهای طراحی مهندسی که در آنها بایستی خصوصیات مکانیکی مانند مقاومت و سفتی تنظیم شود تا با یک پاسخ خاص (که در اینجا استخوان است) تطابق داشته باشد، سازگاری خوبی دارند. این حالت با طراحی ساختارهای که هم خمیده و هم کشیده هستند، بدست میآید. سازههای مشبک از نظر آماری معادل سازههای خرپایی سه بعدی هستند]70[. چنین سازههایی با توجه به روشی که بارهای خارجی باعث ایجاد تنشهای داخلی میشوند، میتوانند طراحی شوند (شکل 7-1-3). اگر بارهای خارجی منجر به فشارهای خمشی شوند، ساختار نسبتاً سازگار بوده و همانند یک فنر مکانیکی عمل میکند (شکل b7-1-3). اگر چنین شبکه خمیدهای از مواد انعطافپذیر ساخته شده باشد، یک منطقه عملکرد انعطافپذیر دیده میشود با افزایش یکنواخت تنش پلاستیک، یک تنش ثابت دیده میشود (شکل c7-1-3). اگر بارهای خارجی منجر به تنشهای کششی شود، ساختار کشیدهای با سفتی بالا که نسبت به سازههای خمشی، مدول یانگ بالاتری دارند، دیده میشود. با افزایش کرنش، نقواص موضعی منجر به تمرکز کرنش شده و یک استحکام نهایی مجزایی دیده میشود که منجر به کمانش ستون یا تغییر شکل موضعی تودهای میشود (شکل a7-1-3). با افزایش کرنش فشاری، به دلیل شکست متوالی هندسههای موضعی، یک تغییرات چرخهای تنش مشاهده میشود (شکل d7-1-3). بسته به این که تنشهای داخلی مرتبط با کشش یا خمش هستند، ساختار شبکه در نهایت یک منطقه متراکم را نشان میدهد که در آنجا، ساختار شبکه به یک ناحیه جامد افت میکند و منجر به افزایش نمایی تنش میشود (شکل e7-1-3).
3-1-4-2 اثر تمرکز تنش هندسی
بسته به این که خمش یا کشش غالب هستند، هندسه موضعی در رفتار تغییرشکلی سازههای مشبک MAM نقش مهمی ایفا میکنند. شکل 1-8-3 یک نمونه از چگونگی این که هندسه دیجیتالی ورودی نشاندهنده محصول تهیه شده نمیباشد را نشان میدهد که منجر به تمرکز تنش که باعث شکست پلاستیک موضعی غیرقابل پیشبینی میشود. بسته به این که خمش یا کشش غالب هستند، هندسه موضعی نقش بحرانی در رفتار تغییرشکلی سازههای مشبک MAM دارد. در این مرحله تأثیر تغییرپذیری تولید بر پاسخ ساختاری به خوبی درک نشده است و یک منطقه تحقیقاتی فعال در بهینهسازی ساختارهای ایمپلنت MAM است.
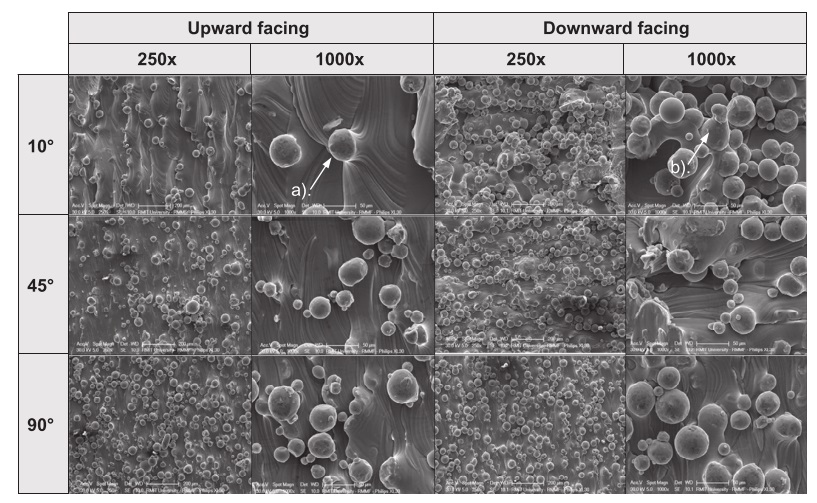
شکل 6-1-3 تصاویر SEM (250X-1000X) که نشاندهنده سطح بالایی و پایینی SLM نمونه Ti-6Al-4V با شیبهای 10، 45 و 90 درجه نسبت به بستر پودر هستند.
(a) پودر ذوبشدهی جزئی ابتدایی در محیط لایه در سطوح رو به بالا (b) مجموعهای از پودرهای جزئی جذب شده روی سطوح روبه پایین.
3-1-5 مدیریت اطلاعات
یک چالش فنی مهم در ایمپلنتهای MAM، سختی و هزینه محاسباتی مدیریت دادههای ایمپلنت است. بهطور خاص، از آنجا که MAM به یک فایل دیجیتالی به عنوان ورودی نیاز دارد، لازم است مشخصات هندسی ایمپلنت در نظر گرفته شده با وضوح کافی تعریف شود تا به نتیجه مهندسی لازم برسد. همچنین باید از بازدهی محاسباتی لازم برای انتقال و پردازش پرونده در پهنای باند قابل قبول برخوردار باشد.
سازههای مشبک امکان طراحی ایمپلنتهای پزشکی نوآورانه MAM مخصوص بیمار را با مزایای بالینی و تجاری بهتری نسبت به ایمپلنتهای قدیمی فراهم میسازد. با این حال، نمایش هندسههای مشبک میتواند هزینههای محاسباتی قابل توجهی را متحمل شود که میتواند کاربردهای MAM را محدود سازد]72[. چالشهای اصلی و فرصتهای فنی برای مدیریت دادههای کاشت در زیر ارائه شده است.
ابزار طراحی به کمک کامپیوتر (CAD) معمولاً از نمایش مرزی هندسه (B-rep) طراحی استفاده میکند. اساساً B-rep در نمایش سازههای مشبک پیچیده که شامل تعداد زیادی ویژگیهای خاص است، ناموفق بوده و منجر به هزینههای بالای محاسباتی میشود]73-75[. در ارتباط با چالشهای محاسباتی، طراحی CAD سازههای مشبک قدیمی فرصتهای محدودی را برای طراحی ایمپلنت فراهم میکند زیرا زمان مدلسازی بسته به تجربه طراح محدود است]72[.
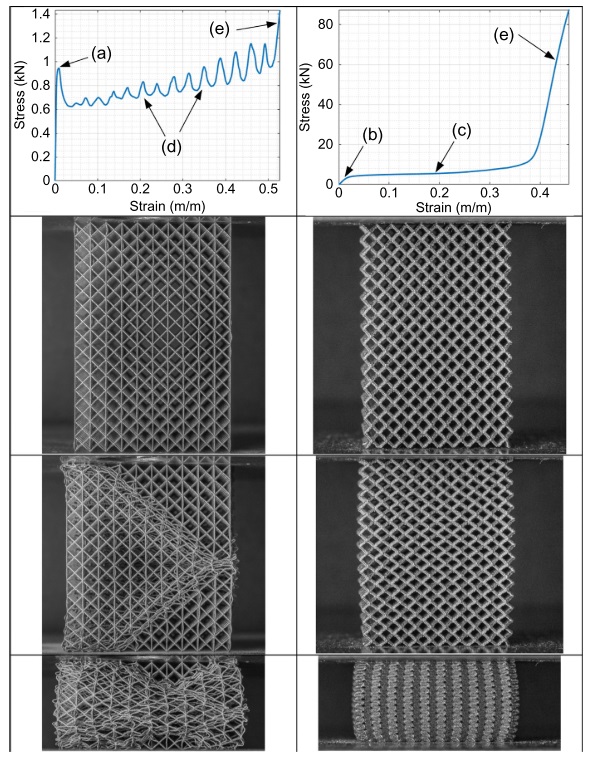
شکل 7-1-3 سازه مشبک SLM که رفتار غالب کششی (سمت چپ) و رفتار غالب خمشی را نشان میدهد. این یک نمونه از اینکونل 625 بوده که مناسب ایمپلنت نمیباشد، ولی به دلیل انعطافپذیری متمایزی که دارد یک مثال عالی از مکانیزمهای تغییرشکلی که بایستی برای طراحی سازه ایمپلنتهای AM فراهم شود، میباشد. شکل (a) استحکام نهایی (b) منطقه انعطافی (c) تنش پلتو (d) افت موضعی متوالی (e) ناحیهی متراکم.
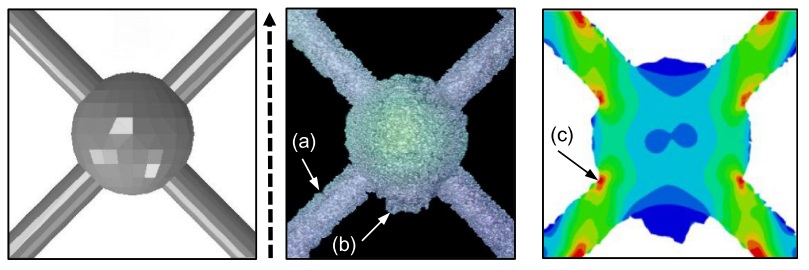
شکل 8-1-3 نمایش دیجیتالی سازه مشبک (سمت چپ)، تصویر نوری با نور پس زمینه از سازه مشبک که با AM تهیه شده است (وسط)، نمایش شماتیک از شدتهای تنشی زمانی که در جهت ساخت بارگذاری شده است (سمت راست). جهت ساخت با پیکان نشان داده شده است. (a) زبری سطح مرتبط با پلهپلهای شدن و ذرات جزئی چسبنده. (b) اثر سقوط همراه با استخر مذاب پشتیبانی نشده (c) تمرکز تنش ناشی از تغییرات در هندسه ورودی و نمونه تهیه شده. Ti-6Al-4V ساخته شده با SLM با قطر کروی 2500 میکرون و قطر بند 1000 میکرون.
فرمت فایل قدیمی AM به صورت فایل استریولیتوگرافی (STL) است که یک حجم جامد با گوشههای مثلثی مجزا و بردارهای نرمال مرتبط را نشان میدهد]76,77[. بهعلاوه، فرمت STL از نظر محاسباتی ناکارآمد است]75-80[ و چون هندسههای انحنادار بهصورت گسسته هستند، فرصتی برای ایجاد خطاهای هندسی فراهم میکند]78[. چالش ذخیرهسازی اطلاعات برای برای سازههای مشبک مهندسی، تشدید میشود، زیرا کارآمدی نمایش اجزای چارچوب شبکه با گوشههای مثلثی بسیار ضعیف بوده که منجر به نیاز به حافظه و زمان پردازش قابل توجهی میشود]78,81[.
فرمتهای پیشرفته AM در مقابل محدودیتهای فایل STL به خصوص فرمت ساخت افزایش منبع باز AMF، ارائه میشوند]76,82[. سخت افزارها و نرمافزارهای امروزی، مستلزم محدودیتهای فرمتهای STL در کوتاه مدت است. در پاسخ به این نیاز، نسل جدیدی از ابزارهای تولید شبکه برنامهنویسی (PGL) در حال توسعه است که موارد زیر را فراهم میکند]72[:
-
تعریف محاسباتی بهینه از سازههای مشبک با مجموعه دادههای بزرگ.
-
تعریف برنامهای از معماریهای مشبک (به گونهای که طراحی الگوریتمی فعال باشد).
-
کنترل بر وضوح عنصر شبکه بهگونهای که کیفیت هندسی با نیاز خاص بخشی که تولید میشود، تطابق داشته باشد.
ابزارهای PLG وضوح فایل دیجیتالی (شکل 9-1-3) را به صورت موضعی با وضوح سیستم MAM مطابقت میدهد به طوری که اندازهی فایل و هزینههای محاسباتی مرتبط بدون هیچگونه تخریبی در کیفیت، کاهش مییابند.
3-1-6 تطابق هندسی
ساخت ایمپلنتهای پیشرفته مستلزم آن است که هندسه ایمپلنت به صورت اورتومورفیک یا شکل آن، خاص بیمار باشد. طراحی ساختارهای مشبک تطابقی برای هندسههای معمولی امری بیاهمیت است. با این حال، هندسههای آلی مانند ساختارهای TO یا ایمپنتهایی که از حاشیههای جراحی تبعیت میکنند، برای محصورکردن با شبکههای متناوب از نظر محاسباتی به چالش کشیده شدهاند. در فضای تحقیق AM، روشهای مختلفی برای تولید ساختارهای مشبک که مطابق با شکل آلی هستند، پیشنهاد شده است[83-85]. یکی از این روشها، نرم افزار تجاری DFAM ، که به طور معمول از تقاطع بولی هندسه در نظر گرفتهشده AM و یک آرایهی شبکهی معمولی استفاده میکند[86]. روش بولی یک زیرمجموعهای از طراحی ایمپلنت شبکه MAM است، زیرا در بردارندهی نیازهای تولیدی نبوده و میتواند خواص مکانیکی را به خطر بیندازد. نسل جدیدی از ابزارهای مشبک DFAM ایجاد شده است که امکان ایجاد ساختارهای شبکه تطابقی را مستقیماً از دادههای تصویربرداری پزشکی فراهم میکند و نیازهای تولیدی و مکانیکی را فراهم میکند[112].
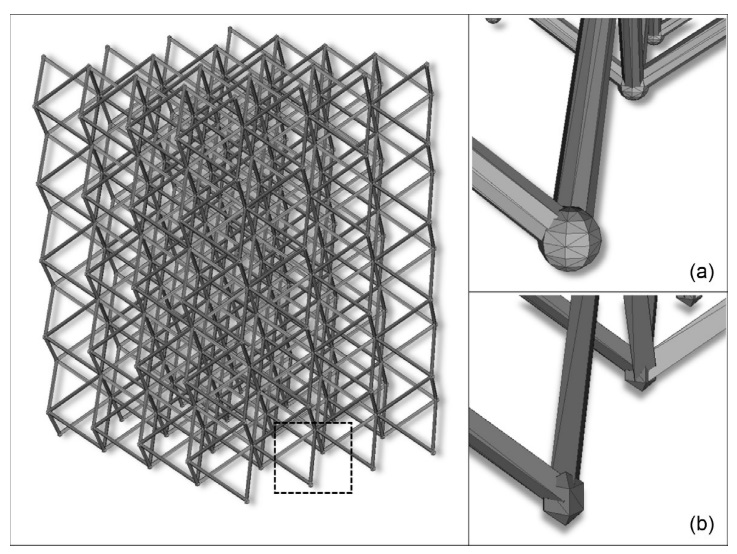
شکل 9-1-3 نمایش استریوگرافی از ساختار مشبک کشیده که وضوح اجزای شبکه STL را به صورت (a) بالا و (b) پایین نشان میدهد.
3-1-7 بهینهسازی توپولوژی
متمایز از هندسه، توپولوژی به اتصال مکانهای خاص در یک ساختار کلی اشاره دارد]87[. انتخاب دستی توپولوژی کار فشردهای است و به دلیل پیشتصورات طراح میتواند منجر به نتایجی زیر حد نهایی شود. با این حال، انتخاب خودکار توپولوژیهای قوی به دلیل بالا بودن ابعادی تنظیمات ممکن، از نظر محاسباتی چالش برانگیز است. در پاسخ به این چالش، گروههای تحقیقاتی متعددی روشهای بهینهسازی توپولوژی (TO) را ارائه دادهاند]88[. این روشها، بینشی در توزیع بهینه مواد برای محدودیتهای داده شده و اهداف ساختاری را ارائه میدهند. با این حال، مسئلهی توپولوژی مطلوب به عنوان یک سوال تحقیق باز به خصوص برای کاربردهای AM، میباشد]89[.
3-1-7-1 روشهای بهبود توپولوژی
از کارهای میشل اغلب به عنوان پژوهش بنیانگذار در رشته TO استفاده میشود، زیرا در سال 1904، او روشهای تحلیلی را برای به حداقل رساندن جرم یک قاب گسسته ارائه داد]90[. روش ساختار پایه یک رویکرد مرتبط است که بهوسیلهی آن یک سیستم خرپا با عناصر مثلثی متعدد در کوچکترین مقیاس فیزیکی که مربوط به سیستم است تولید میشود. آنالیز ساختاری به طور تکراری، زیرمجموعه این عناصر خرپایی اولیه را که عملکرد هدف مرتبط را بهینه میکند، شناسایی میکند. اخیراً توجه زیادی به روشهای TO پیوسته جلب شده است که در آن پاسخ ساختاری فضای طراحی موجود، مورد تجزیه و تحلیل قرار گرفته و بهطور تکراری به منظور بهینهسازی توپولوژی که شامل اصلاح هندسه موضعی میباشد، تغییر مییابد. روشهای پیوسته مورد توجه شامل]87,88,91-95[ روشهای برپایهی چگالی]96[ و مواد همسانگرد جامد (SIMP) ]97,98[؛ بهینهسازی ساختار تکاملی (ESO) ]99[ و روشهای توسعهی دو طرفه (BESO) که بهطور مکرر اجازه افزودن و برداشتن مواد را میدهد]100,101[؛ و روشهای تعیین سطح (LSM) که بهطور ضمنی ساختار مطلوب توسط برخی از عملکردهای سطح تنظیمشده تعریف میکند]102[. خروجی این روشها بهطور معمول شامل ناپیوستگیهای موضعی و اثرات مش است که یا در داخل الگوریتم TO و یا بعد از پردازش خروجی TO، قرار میگیرند.
روشهای TO بهطور معمول، ساختارهای آلی با ویژگیهای بسیار خمیده تولید میکنند که ثبت آنها با طراحیهای مهندسی قدیمی چالش برانگیز است و شامل پیچیدگیهایی است که با روشهای تولید قدیمی سازگار نیست]89[. این روشها بهدلیل ماهیت دیجیتالی فایلهای ورودی و توانایی MAM برای تولید سازههای پیچیده که با ناسازگار با روشهای تولید قدیمی هستند، کمتر مرتبط با MAM هستند]4,5,103[.
3-1-7-2 کاربرد ایمپلنتهای MAM
اگرچه TO برای طراحی محصولات مهندسی با ارزش بالا مانند ساختار ایمپلنت فلزی مختص بیمار، با MAM سازگار است، محدودیتهای تولید خاص بایستی قابل قبول باشند تا بتوان به یک خروجی MAM قوی دست یافت. به عنوان مثال، سیستمهای MAM اثرات پیچیده و گذرای حرارتی را برای پارامترهای فرآیند دادهشده و هندسه تولیدی القا میکنند]104,105[. این تأثیرات یک میدان دما را نشان میدهد که قابلیت تولید، زبری موضعی، رشد دانه]106[ و ریزساختار را تعریف میکند و بهطور مستقیم خصوصیات ماده را تعیین میکند]107[.
علیرغم ضرورت پذیرش محدودیتهای AM در روشهای بهینهسازی توپولوژیکی، تعداد کمی از ابزارهای DFAM برای ادغام الزامات AM با روشهای TO وجود دارد]8[. روشهای DFAM موجود، یا محدودیتهای AM را مستقیماً با الگوریتمهای TO ادغام میکند یا روشهای بعد از پردازش را برای برآوردن محدودیتهای AM اعمال میکند. روشهایی که محدودیتهای AM را ادغام میکنند، به عنوان مثال]89,108-110[، به عملیات پردازش کمتری نیاز دارند. با این حال، ممکن است بهینهبودن اجزای تولیدشده با قراردادن مستقیم محدودیتهای AM در داخل اجزای AM نهایی، بهخطر بیفتد. مزیت روشهای پس از پردازش، به عنوان مثال]111[، این است که هندسه توپولوژیکی بهینه حفظ میشود؛ با این حال، به منظور اطمینان از تولیدپذیری ممکن است ساختارهای پشتیبان نیاز باشد. با وجود این رویکردهای پیشنهادی، جایگاه تولید AM در TO همچنان یک مسئله تحقیق باز است]108[، که از کاربرد بالینی MAM برای طراحی ایمپلنت استفاده میکنند.
3-1-8 فلسفه ایمپلنت درجا
قابلیتهای مختلکننده MAM همراه با پیشرفت در رباتیکهای جراحی و تصویر برداری پزشکی، فلسفه جراحی JIT را قادر میسازد. مطابق با فلسفه JIT، ایمپلنت بهصورت الگوریتمی طراحی شده، از لحاظ ساختاری بهینهسازی شده، تولیدشده، تحت عملیات پس از پردازش قرار گرفته و با محدودیتهای زمانی یک عمل جراحی منفرد، ایمپلنت شده است]112[. فلسفه JIT بهویژه برای عملیات جراحی سرطان بدخیم استخوان مناسب است، زیرا به دلیل پتانسیل گسترش تومور و کاهش تراکم استخوان در نزدیکی منطقه برداشتن استخوان پیشنهادی که وجود دارد، تعیین پروتزهای پیشنهادی پیش از عمل با محدودیتهایی روبهرو است. فلسفه JIT، فرصتی را برای بهبود نتایج جراحی با کاهش زمان بهبودی است. ابزارهای DFAM ارائهشده در این فصل برای استفاده از ایمپلنتهای JIT در کاربردهای بالینی ضروری است، بهخصوص در:
-
دادههای تجربی قوی در مورد ساخت MAM سازههای تیتانیومی مورد نیاز است بهگونهای که اثرات پارامتر فرآیند و انتخاب مواد بر هندسه جز MAM بهوضوح تعریف شود (بخش 3-1-3).
-
استخوانی که بهطور طبیعی وجود دارد، یک ماده کامپوزیتی با هندسه موضعی و توپولوژی پیچیده است. این فاکتورها باید توسط شبکه MAM در فلسفه JIT همگام شوند و نیاز به درک پیچیدهای از اثرات تنظیم سلول شبکه و پردازش MAM بر پاسخ مکانیکی ایمپلنت تولیدی دارد (بخش 4-1-3).
-
ساخت ایمپلنت JIT نیازمند طراحی الگوریتمی خاص با یک روش بهینهی محاسباتی است. با تطابق دادن وضوح فایل دیجیتال ورودی با وضوح سیستم MAM، زمان محاسبات بدون تخریب کیفیت تولیدی، کاهش مییابد (بخش 5-1-3).
-
روشهای جدید طراحی شبکه، تولید ساختارهای مشبک تطابقی را مقدور میسازد که مطابق با نیازهای تولیدی و مکانیکی است]112[.
-
جراحی رباتیکی منجر به تعریف هندسه دیجیتالی برشی میشود. تلفیق این دادهها با الگوریتمهای طراحی ایمپلنت، امکان کاهش زمان طراحی و افزایش اطمینان را فراهم میسازد.
روشهای ایمپلنت JIT ارائه شده است که با استفاده از فرآیند MAM به سختی ساخته میشوند؛ دستیابی به تطابق هندسی با هندسه جراحی خاص بیمار؛ و از نظر آماری از خصوصیات مکانیکی استخوان انسان قابل تشخیص نیستند]112[. در این فصل یک مرجع برای تصحیح عناصر بنیادی DFAM لازم برای تبدیلشدن به فلسفه JIT به یک واقعیت بالینی ارائه شده است.
تقدیر
این فصل ماحصل تحقیق در زمینه طراحی ایمپلنتهای MAM تیتانیومی در مرکز تولید مواد افزودنی، دانشکده مهندسی، دانشگاه RMIT، ملبورن استرالیا است. بهطور خاص، سهم پروفسور ماکیان و پروفسور میلان برانت در زمینههای مربوط به متالورژی تیتانیوم و کاربردهای لیزر برای این تحقیق اساسی هستند که با کمکهای دکتر دارپان شیدید، دکتر مکیج ماژور، متیو مک میلان، احمد الغمدی و آویک سارکر پشتیبانی میشود.
References
[1] I. Gibson, D.W. Rosen, B. Stucker, Additive Manufacturing Technologies—Rapid Prototyping to Direct Digital Manufacturing, Springer, New York, 2010.
[2] Y. Zhai, D.A. Lados, J.L. LaGoy, Additive manufacturing: making imagination the major limitation, JOM 66 (2014) 808–816.
[3] M. Tarik Arafat, I. Gibson, X. Li, State of the art and future direction of additive manufactured scaffolds-based bone tissue engineering, Rapid Prototyp. J. 20 (2014) 13–26.
[4] D. Shidid, M. Leary, P. Choong, M. Brandt, Just-in-time design and additive manufacture of patient-specific medical implants, Phys. Procedia 83 (2016) 4–14.
[5] X. Wang, S. Xu, S. Zhou, W. Xu, M. Leary, P. Choong, et al., Topological design and additive manufacturing of porous metals for bone scaffolds and orthopaedic implants: a review, Biomaterials 83 (2016) 127–141.
[6] G. Reinhart, S. Teufelhart, Load-adapted design of generative manufactured lattice structures, Phys. Procedia 12 (2011) 385–392.
[7] A.V. Gubin, V.P. Kuznetsov, D.Y. Borzunov, A.A. Koryukov, A.V. Reznik, A. Y. Chevardin, Challenges and perspectives in the use of additive technologies for making customized implants for traumatology and orthopedics, Biomed. Eng. 50 (2016) 285–289.
[8] Z. Doubrovski, J.C. Verlinden, J.M.P. Geraedts, in: Optimal design for additive manufacturing: opportunities and challenges, Proceedings of the Asme International Design Engineering Technical Conferences and Computers and Information in Engineering Conference, 2011, vol. 9, 2012, , pp. 635–646.
[9] W.E. Frazier, Direct digital manufacturing of metallic components vision and roadmap, Direct Digital Manufacturing of Metallic Components: Affordable, Durable, and Structurally Efficient Airframes. Solomons, MD, 2010.
[10] K.V. Wong, A. Hernandez, A review of additive manufacturing, ISRN Mech. Eng. 2012 (2012) 1–10.
[11] ASTM standard F2792-12a, F2792-12a. Standard Terminology for Additive Manufacturing Technologies, ASTM International, West Conshohocken, PA, 2012.
[12] B. Berman, 3-D printing: the new industrial revolution, Bus. Horiz. 55 (2012) 155–162.
[13] B. Vandenbroucke, J.P. Kruth, Selective laser melting of biocompatible metals for rapid manufacturing of medical parts, Rapid Prototyp. J. 13 (2007) 196–203.
[14] A. Drizo, J. Pegna, Environmental impacts of rapid prototyping: an overview of research to date, Rapid Prototyp. J. 12 (2006) 64–71. 218 Titanium in Medical and Dental Applications
[15] I. Gibson, D.W. Rosen, B. Stucker, Additive Manufacturing Technologies, Springer, New York, 2010.
[16] ISO/ASTM, Additive Manufacturing—General Principles—Terminology, 52900, ISO/ ASTM, Switzerland, 2015.
[17] W.E. Frazier, Metal additive manufacturing: a review, J. Mater. Eng. Perform. 23 (2014) 1917–1928.
[18] T. Marcu, M. Todea, I. Gligor, P. Berce, C. Popa, Effect of surface conditioning on the flowability of Ti-6Al-7Nb powder for selective laser melting applications, Appl. Surf. Sci. 258 (2012) 3276–3282.
[19] S. Clijsters, T. Craeghs, S. Buls, K. Kempen, J.P. Kruth, In situ quality control of the selective laser melting process using a high-speed, real-time melt pool monitoring system, Int. J. Adv. Manuf. Technol. 75 (2014) 1089–1101.
[20] A.A. Antonysamy, Microstructure, Texture and Mechanical Property Evolution During Additive Manufacturing of Ti-6Al-4V Alloy for Aerospace Applications, PhD Thesis, The University of Manchester, Manchester, UK, 2012.
[21] Bourell DL, Marcus HL, Weiss WL. Selective Laser Sintering of Parts by Compound Formation of Precursor Powders, Google Patents, 1992.
[22] A. Gebhardt, F.-M. Schmidt, J.-S. H€otter, W. Sokalla, P. Sokalla, Additive manufacturing by selective laser melting the realizer desktop machine and its application for the dental industry, Phys. Procedia 5 (2010) 543–549.
[23] S.S. Babu, W. Peter, R. Dehoff, L. Love, in: Recent advances in metal additive manufacturing at manufacturing demonstration facility: role of in situ process monitoring, computational modeling, and advanced characterization, 8th Annual Laser Additive Manufacturing (LAM®) Workshop, Orlando, FL, 2016.
[24] D.W. Rosen, Research supporting principles for design for additive manufacturing, Virtual Phys. Prototyp. 9 (2014) 225–232.
[25] V.J. Challis, X. Xu, L.C. Zhang, A.P. Roberts, J.F. Grotowski, T.B. Sercombe, High specific strength and stiffness structures produced using selective laser melting, Mater. Des. 63 (2014) 783–788.
[26] D. Becker, K. Wissenbach, Additive manufacturing of copper components, Fraunhofer ILT annual report, Fraunhofer ILT, Aachen, Germany, 2009.
[27] H. Meier, C. Haberland, Experimental studies on selective laser melting of metallic parts, Exp. Untersuchung. Laserstrahlg. Metallisch. Bauteile 39 (2008) 665–670.
[28] M. Mazur, M. Leary, M. McMillan, S. Sun, D. Shidid, M. Brandt, Mechanical properties of Ti-6Al-4V and Al-Si-12Mg lattice structures manufactured by selective laser melting (SLM), in: Laser Additive Manufacturing: Materials, Design, Technologies, and Applications, Woodhead Publishing, Duxford, UK, 2016, p. 119.
[29] P. Lott, H. Schleifenbaum, W. Meiners, K. Wissenbach, C. Hinke, J. B€ultmann, Design of an optical system for the in situ process monitoring of selective laser melting (SLM), Phys. Procedia 12 (Part A) (2011) 683–690.
[30] S.L. Sing, W.Y. Yeong, F.E. Wiria, B.Y. Tay, Characterization of titanium lattice structures fabricated by selective laser melting using an adapted compressive test method, Exp. Mech. 56 (2016) 735–748.
[31] V. Weißmann, P. Drescher, R. Bader, H. Seitz, H. Hansmann, N. Laufer, Comparison of single Ti-6Al-4V struts made using selective laser melting and electron beam melting subject to part orientation, Metals 7 (2017) 91.
[32] M. Mazur, M. Leary, S. Sun, M. Vcelka, D. Shidid, M. Brandt, Deformation and failure behaviour of Ti-6Al-4V lattice structures manufactured by selective laser melting (SLM), Int. J. Adv. Manuf. Technol. (2015). Design of titanium implants for additive manufacturing 219
[33] Q.C. Liu, J. Elambasseril, S.J. Sun, M. Leary, M. Brandt, P.K. Sharp, The effect of manufacturing defects on the fatigue behaviour of Ti-6Al-4V specimens fabricated using selective laser melting, Adv. Mater. Res. 891 (2014) 1519–1524.
[34] M. Ameli, B. Agnew, P.S. Leung, B. Ng, C.J. Sutcliffe, J. Singh, et al., A novel method for manufacturing sintered aluminium heat pipes (SAHP), Appl. Therm. Eng. 52 (2013) 498–504.
[35] X. Gong, T. Anderson, K. Chou, Review on powder-based electron beam additive manufacturing technology, Manuf. Rev. 1 (2014) 2.
[36] C. K€orner, Additive manufacturing of metallic components by selective electron beam melting—a review, Int. Mater. Rev. 61 (2016) 1–17.
[37] Y. Kok, X. Tan, S.B. Tor, C.K. Chua, Fabrication and microstructural characterisation of additive manufactured Ti-6Al-4V parts by electron beam melting, Virtual Phys. Prototyp. 10 (2015) 13–21.
[38] H.P. Tang, J. Wang, C.N. Song, N. Liu, L. Jia, J. Elambasseril, et al., Microstructure, mechanical properties, and flatness of SEBM Ti-6Al-4V sheet in as-built and hot isostatically pressed conditions, JOM 69 (2017) 466–471.
[39] S.L. Lu, H.P. Tang, Y.P. Ning, N. Liu, D.H. StJohn, M. Qian, Microstructure and mechanical properties of long Ti-6Al-4V rods additively manufactured by selective electron beam melting out of a deep powder bed and the effect of subsequent hot isostatic pressing, Metall. Mater. Trans. A 46 (2015) 3824–3834.
[40] M. Jamshidinia, L. Wang, W. Tong, R. Ajlouni, R. Kovacevic, Fatigue properties of a dental implant produced by Electron Beam Melting® (EBM), J. Mater. Process. Technol. 226 (2015) 255–263.
[41] M. Jamshidinia, L. Wang, W. Tong, R. Kovacevic, The bio-compatible dental implant designed by using non-stochastic porosity produced by Electron Beam Melting® (EBM), J. Mater. Process. Technol. 214 (2014) 1728–1739.
[42] R.K. Mahdi Jamshidinia, The numerical modeling of fatigue properties of a biocompatible dental implant produced by Electron Beam Melting® (EBM), Proceeding of the Twenty Forth Annual International Solid Freeform Fabrication Symposium, August 12–14, Austin, TX, 2013, 2013, p. 15.
[43] L.E. Murr, S.M. Gaytan, E. Martinez, F. Medina, R.B. Wicker, Next generation orthopaedic implants by additive manufacturing using electron beam melting, Int. J. Biomater. 2012 (2012) 245727.
[44] X. Li, Y. Luo, C. Wang, W. Zhang, Y. Li, Fabrication and in vivo evaluation of Ti-6Al- 4V implants with controlled porous structure and complex shape, Front. Mech. Eng. 7 (2012) 66–71.
[45] L.E. Murr, S.M. Gaytan, F. Medina, H. Lopez, E. Martinez, B.I. Machado, et al., Next-generation biomedical implants using additive manufacturing of complex, cellular and functional mesh arrays, Philos. Trans. A Math. Phys. Eng. Sci. 368 (2010) 1999–2032.
[46] P. Heinl, L. Muller, C. Korner, R.F. Singer, F.A. Muller, Cellular Ti-6Al-4V structures with interconnected macro porosity for bone implants fabricated by selective electron beam melting, Acta Biomater. 4 (2008) 1536–1544.
[47] O.L.A. Harrysson, O. Cansizoglu, D.J. Marcellin-Little, D.R. Cormier, H.A. West, Direct metal fabrication of titanium implants with tailored materials and mechanical properties using electron beam melting technology, Mater. Sci. Eng. C 28 (2008) 366–373.
[48] S.L. Sing, J. An, W.Y. Yeong, F.E. Wiria, Laser and electron-beam powder-bed additive manufacturing of metallic implants: a review on processes, materials and designs, J. Orthop. Res. 34 (2016) 369–385. 220 Titanium in Medical and Dental Applications
[49] C.Y. Lin, T. Wirtz, F. LaMarca, S.J. Hollister, Structural and mechanical evaluations of a topology optimized titanium interbody fusion cage fabricated by selective laser melting process, J. Biomed. Mater. Res. A 83 (2007) 272–279.
[50] A. Tsao, J. Roberson, M. Christie, D. Dore, D. Heck, D. Robertson, et al., Biomechanical and clinical evaluations of a porous tantalum implant for the treatment of early-stage osteonecrosis, J. Bone Joint Surg. Am. 87 (2005) 22–27.
[51] N. Taniguchi, S. Fujibayashi, M. Takemoto, K. Sasaki, B. Otsuki, T. Nakamura, et al., Effect of pore size on bone ingrowth into porous titanium implants fabricated by additive manufacturing: an in vivo experiment, Mater. Sci. Eng. C 59 (2016) 690–701.
[52] Z. Zhang, D. Jones, S. Yue, P.D. Lee, J.R. Jones, C.J. Sutcliffe, et al., Hierarchical tailoring of strut architecture to control permeability of additive manufactured titanium implants, Mater. Sci. Eng. C Mater. Biol. Appl. 33 (2013) 4055–4062.
[53] D. Xiao, Y. Yang, X. Su, D. Wang, J. Sun, An integrated approach of topology optimized design and selective laser melting process for titanium implants materials, Biomed. Mater. Eng. 23 (2013) 433–445.
[54] De Wild M, M€uller T, Tschumi S, Schumacher R, Albrecht H. Production and in-vitro characterization of micro-structured implant surfaces, Innovative Developments in Virtual and Physical Prototyping—Proceedings of the 5th International Conference on Advanced Research and Rapid Prototyping, 2012, pp. 111–4.
[55] S. Ponader, C. von Wilmowsky, M. Widenmayer, R. Lutz, P. Heinl, C. Korner, et al., In vivo performance of selective electron beam-melted Ti-6Al-4V structures, J. Biomed. Mater. Res. A 92 (2010) 56–62.
[56] Y.J. Chen, B. Feng, Y.P. Zhu, J. Weng, J.X. Wang, X. Lu, Fabrication of porous titanium implants with biomechanical compatibility, Mater. Lett. 63 (2009) 2659–2661.
[57] J. Vaithilingam, S. Kilsby, R.D. Goodridge, S.D. Christie, S. Edmondson, R.J. Hague, Functionalisation of Ti-6Al-4V components fabricated using selective laser melting with a bioactive compound, Mater. Sci. Eng. C Mater. Biol. Appl. 46 (2015) 52–61.
[58] M.T. Andani, N. Shayesteh Moghaddam, C. Haberland, D. Dean, M.J. Miller, M. Elahinia, Metals for bone implants. Part 1. Powder metallurgy and implant rendering, Acta Biomater. 10 (2014) 4058–4070.
[59] S.A. Yavari, R. Wauthle, J. van der Stok, A.C. Riemslag, M. Janssen, M. Mulier, et al., Fatigue behavior of porous biomaterials manufactured using selective laser melting, Mater. Sci. Eng. C Mater. Biol. Appl. 33 (2013) 4849–4858.
[60] I. Polmear, D. StJohn, J.-F. Nie, M. Qian, Light Alloys: Metallurgy of the Light Metals, Butterworth-Heinemann, Oxford, UK, 2017.
[61] M. Qian, W. Xu, M. Brandt, H. Tang, Additive manufacturing and post-processing of Ti-6Al-4V for superior mechanical properties, MRS Bull. (2016) 775–784.
[62] I. Polmear, S.J. DH, J.F. Nie, M. Qian, Light Alloys: Metallurgy of Light Metals, Butterworth-Heinemann, Elsevier, 2017 (Chapter 7).
[63] M. McMillan, M. Leary, M. Brandt, Computationally efficient finite difference method for metal additive manufacturing: a reduced-order DFAM tool applied to SLM, Mater. Design 132 (2017) 226–243.
[64] R. Olaf, E. Claus, Rapid manufacturing of lattice structures with selective laser melting, Proc. of SPIE 6107 Laser-Based Micropackaging, 2005.
[65] F.G. Bachmann, O. Rehme, C. Emmelmann, W. Hoving, Y. Lu, K. Washio, Rapid Manufacturing of Lattice Structures With Selective Laser Melting, vol. 6107, (2006) 61070K-K-12.
[66] M.R. Alkahari, T. Furumoto, T. Ueda, A. Hosokawa, R. Tanaka, A. Aziz, M. Sanusi, Thermal conductivity of metal powder and consolidated material fabricated via selective laser melting, Key Eng. Mater. 523 (2012) 244–249. Design of titanium implants for additive manufacturing 221
[67] A.V. Gusarov, T. Laoui, L. Froyen, V.I. Titov, Contact thermal conductivity of a powder bed in selective laser sintering, Int. J. Heat Mass Transf. 46 (2003) 1103–1109.
[68] M. Leary, M. Babaee, M. Brandt, A. Subic, Feasible build orientations for self-supporting fused deposition manufacture: a novel approach to space-filling Tesselated geometries, Adv. Mater. Res. 633 (2013) 148–168.
[69] Y.Y. Sun, S. Gulizia, C.H. Oh, D. Fraser, M. Leary, Y.F. Yang, et al., The influence of as-built surface conditions on mechanical properties of Ti-6Al-4V additively manufactured by selective electron beam melting, JOM 68 (2016) 791–798.
[70] L.J. Gibson, M.F. Ashby, Cellular Solids: Structure and Properties, Cambridge University Press, Cambridge, UK, 1997.
[71] M.F. Ashby, T. Evans, N.A. Fleck, J. Hutchinson, H. Wadley, L. Gibson, Metal Foams: A Design Guide: A Design Guide, Elsevier, Burlington, USA, 2000.
[72] M. Mcmillan, M. Jurg, M. Leary, M. Brandt, Programmatic generation of computationally efficient lattice structures for additive manufacture, Rapid Prototyp. J. 22 (2016) 486–494.
[73] J. Brennan-Craddock, D. Brackett, R. Wildman, R. Hague, The design of impact absorbing structures for additive manufacture, J. Phys. Conf. Ser. 382 (2012) 012042.
[74] D.W. Rosen, Design for additive manufacturing: a method to explore unexplored regions of the design space, Eighteenth Annual Solid Freeform Fabrication, 2007, pp. 402–415.
[75] D.L. Bourell, M.C. Leu, D.W. Rosen, Roadmap for Additive Manufacturing - Identifying the Future of Freeform Processing, The University of Texas at Austin, Austin, TX, 2009 pp. 11–15.
[76] J.D. Hiller, H. Lipson, in: STL 2.0: a proposal for a universal multi-material additive manufacturing file format, Proceedings of the Solid Freeform Fabrication Symposium, 2009, pp. 266–278.
[77] D. Ma, F. Lin, C.K. Chua, Rapid prototyping applications in medicine. Part 2: STL file generation and case studies, Int. J. Adv. Manuf. Technol. 18 (2001) 118–127.
[78] T. Wu, E.H.M. Cheung, Enhanced STL, Int. J. Adv. Manuf. Technol. 29 (2005) 1143–1150.
[79] C.B. Williams, J.K. Cochran, D.W. Rosen, Additive manufacturing of metallic cellular materials via three-dimensional printing, Int. J. Adv. Manuf. Technol. 53 (2010) 231–239.
[80] J. Nguyen, S.-i. Park, D.W. Rosen, in: Conformal lattice structure design and fabrication, Solid Freeform Fabrication Symposium, Austin, TX, 2012, pp. 138–161.
[81] B. Koc, Y. Ma, Y.S. Lee, Smoothing STL files by max-fit biarc curves for rapid prototyping, Rapid Prototyp. J. 6 (2000) 186–205.
[82] ISO/ASTM, Standard Specification for Additive Manufacturing File Format (AMF) Version 1.1, IHS: IHS, West Conshohocken, Pennsylvania, 2013, 15.
[83] A. Pasko, O. Fryazinov, T. Vilbrandt, P.-A. Fayolle, V. Adzhiev, Procedural functionbased modelling of volumetric microstructures, Graph. Model. 73 (2011) 165–181.
[84] H.V. Wang, A Unit Cell Approach for Lightweight Structure and Compliant Mechanism, PhD Thesis, Georgia Institute of Technology, Georgia, 2005.
[85] F. Melchels, P.S. Wiggenhauser, D. Warne, M. Barry, F.R. Ong, W.S. Chong, et al., CAD/CAM-assisted breast reconstruction, Biofabrication 3 (2011) 1758–5082.
[86] Y. Chen, An accurate sampling-based method for approximating geometry, Comput. Aided Des. 39 (2007) 975–986.
[87] H.A. Eschenauer, N. Olhoff, Topology optimization of continuum structures: a review, Appl. Mech. Rev. 54 (2001) 331. 222 Titanium in Medical and Dental Applications
[88] G.I.N. Rozvany, A critical review of established methods of structural topology optimization, Struct. Multidiscip. Optim. 37 (2008) 217–237.
[89] D. Brackett, I. Ashcroft, R. Hague, in: Topology optimization for additive manufacturing, Proceedings of the Solid Freeform Fabrication Symposium, Austin, TX, 2011, pp. 348–362.
[90] A.G.M. Michell, LVIII. The limits of economy of material in frame-structures, Lond. Edinburgh Dublin Philos. Mag. J. Sci. 8 (1904) 589–597.
[91] N.P. van Dijk, K. Maute, M. Langelaar, F. van Keulen, Level-set methods for structural topology optimization: a review, Struct. Multidiscip. Optim. 48 (2013) 437–472.
[92] J.D. Deaton, R.V. Grandhi, A survey of structural and multidisciplinary continuum topology optimization: post 2000, Struct. Multidiscip. Optim. 49 (2013) 1–38.
[93] X. Huang, Y.-M. Xie, A further review of ESO type methods for topology optimization, Struct. Multidiscip. Optim. 41 (2010) 671–683.
[94] G. Rozvany, Stress ratio and compliance based methods in topology optimisation—a critical review, Struct. Multidiscip. Optim. 21 (2001) 109–119.
[95] O. Signmund, J. Peterson, Numerical instabilities in topology oiptimisation: a survey on procedures dealing with checkerboards, mesh-dependancies and lcoal minima, Struct. Optim. 16 (1998) 68–75.
[96] M.P. Bendsøe, N. Kikuchi, Generating optimal topologies in structural design using a homogenization method, Comput. Methods Appl. Mech. Eng. 71 (1988) 197–224.
[97] M.P. Bendsøe, Optimal shape design as a material distribution problem, Struct. Optim. (1989) 193–202.
[98] O. Sigmund, A 99 line topology optimization code written in Matlab, Struct. Multidiscip. Optim. 21 (2001) 120–127.
[99] Y. Xie, G.P. Steven, in: Shape and layout optimization via an evolutionary procedure, Proceedings of the International Conference on Computational Engineering Science, 1992.
[100] O. Querin, V. Young, G. Steven, Y. Xie, Computational efficiency and validation of bi-directional evolutionary structural optimisation, Comput. Methods Appl. Mech. Eng. 189 (2000) 559–573.
[101] O. Querin, G. Steven, Y. Xie, Evolutionary structural optimisation (ESO) using a bidirectional algorithm, Eng. Comput. 15 (1998) 1031–1048.
[102] M.Y. Wang, X. Wang, D. Guo, A level set method for structural topology optimization, Comput. Methods Appl. Mech. Eng. 192 (2003) 227–246.
[103] M. Leary, M. Mazur, J. Elambasseril, M. McMillan, T. Chirent, Y. Sun, et al., Selective laser melting (SLM) of Al-Si-12Mg lattice structures, Mater. Des. 98 (2016) 344–357.
[104] B. Baufeld, B. OVd, R. Gault, Additive manufacturing of Ti-6Al-4V components by shaped metal deposition: microstructure and mechanical properties, Mater. Des. 31 (2010) S106–S111.
[105] H. Krauss, M. Zaeh, Investigations on manufacturability and process reliability of selective laser melting, Phys. Procedia 41 (2013) 815–822.
[106] O. Rehme, C. Emmelmann, in: Rapid manufacturing of lattice structures with selective laser melting, Proc of SPIE 6107 Laser-Based Micropackaging, 2005.
[107] H. Krauss, C. Eschey, M. Zaeh, in: Thermography for monitoring the selective laser melting process, Proceedings of the Solid Freeform Fabrication Symposium, 2012.
[108] M. Langelaar, Topology optimization of 3D self-supporting structures for additive manufacturing, Addit. Manuf. 12 (2016) 60–70.
[109] A.T. Gaynor, N.A. Meisel, C.B. Williams, J.K. Guest, Multiple-material topology optimization of compliant mechanisms created via PolyJet three-dimensional printing, J. Manuf. Sci. Eng. 136 (2014) 061015. Design of titanium implants for additive manufacturing 223
[110] A.T. Gaynor, N.A. Meisel, C.B. Williams, J.K. Guest, in: Topology optimization for additive manufacturing: considering maximum overhang constraint, 15th AIAA/ISSMO Multidisciplinary Analysis and Optimization Conference, 2014, p. 2036.
[111] M. Leary, L. Merli, F. Torti, M. Mazur, M. Brandt, Optimal topology for additive manufacture: a method for enabling additive manufacture of support-free optimal structures, Mater. Des. 63 (2014) 678–690.
[112] Shidid D, Leary M, Brandt M, Choong P, A Method for Producing a Customised Orthopaedic Implant, Google Patents, 2015. 224 Titanium in Medical and Dental Applications