مزایای استفاده از تیتانیوم یا آلیاژهای تیتانیوم برای کاربردهای پزشکی عبارتند از:
-
زیست سازگاری.
-
سخت تر از استخوان (MPa 80-120)، فولادهای زنگ نزن و سایر مواد ایمپلنت.
-
حد خستگی بالا (50% مستحکمتر از آلیاژ Co-Cr ریخته گری شده).
-
مقاومت بالا در برابر بارگذاری ضربه ای.
-
مقاومت به خوردگی خوب.
-
مدول الاستیک کمتر نسبت به آلیاژهای کبالت یا فولاد.
-
چگالی کم.
1-4-1 فرآیندهای عمومی برای آلیاژهای تیتانیوم: از سنگ معدن تا جنس میله
مراحل اصلی فرآوری محصولات تیتانیوم عبارت است از: تبدیل سنگ معدن تیتانیوم به "اسفنج" (به شکل فلز متخلخل)، ذوب اسفنج (اسفنج به اضافه عناصر آلیاژی برای تولید شمش)؛ ساخت مواد اولیه (جایی که یک شمش به محصولات عمومی کارخانه مثل بیلتها یا اسلبها فورج میشود) و در نهایت امکان نورد به محصولاتی از قبیل: ورق، تسمه، میله گرد/ مفتول/ سیم یا لوله (شکل 1-4-1 تا 1-4-5). عمدتاً شمش به یک بلوم تبدیل و با دستگاه نورد دو طرفه به بیلت نورد شده است. پس از آمادهسازی بیلت ، بیلت نیز به میله و مفتول نورد شده است (شکلهای 1-4-6 تا 1-4-8).
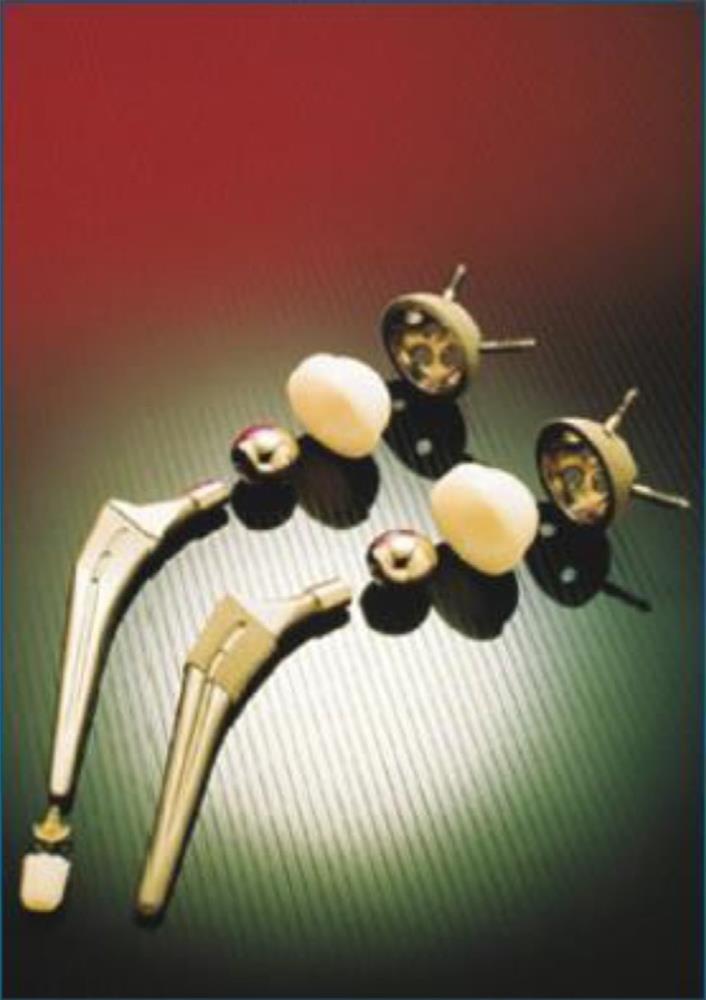
شکل 1-4-1 سیستمهای ساقه لگن (Timet)
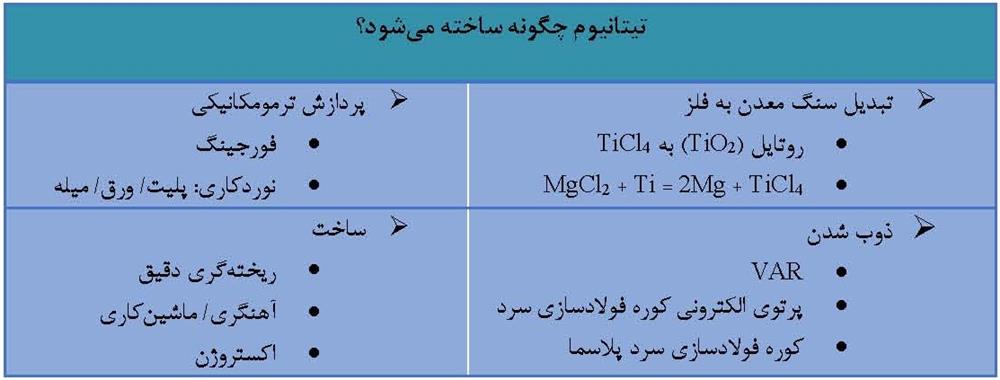
شکل 1-4-2 فلز تیتانیوم (Timet)
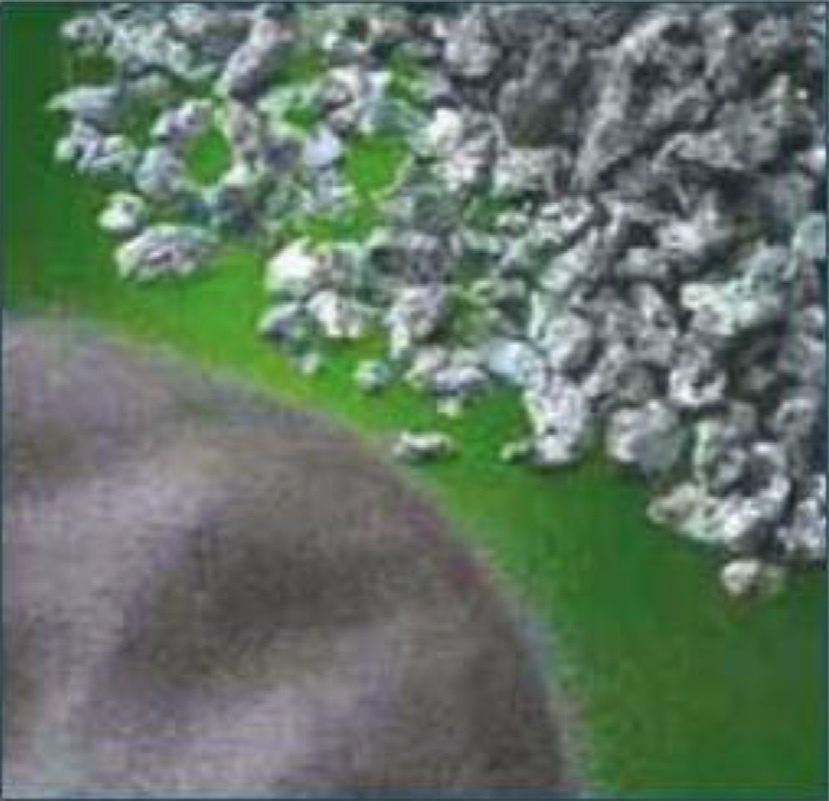
شکل 1-4-3 روتایل و اسفنج تیتانیوم (Timet)
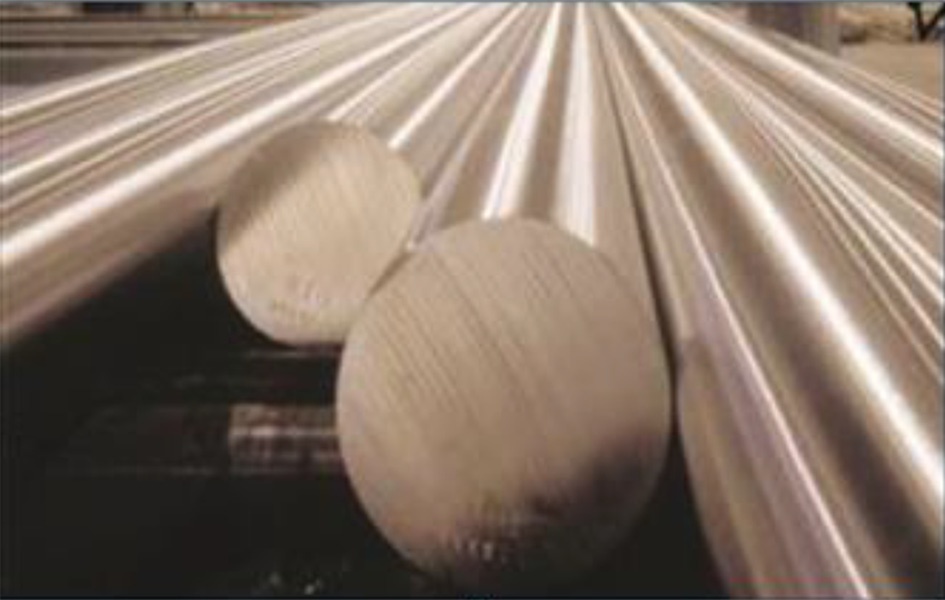
شکل 1-4-4 شمش تیتانیومی (Timet)
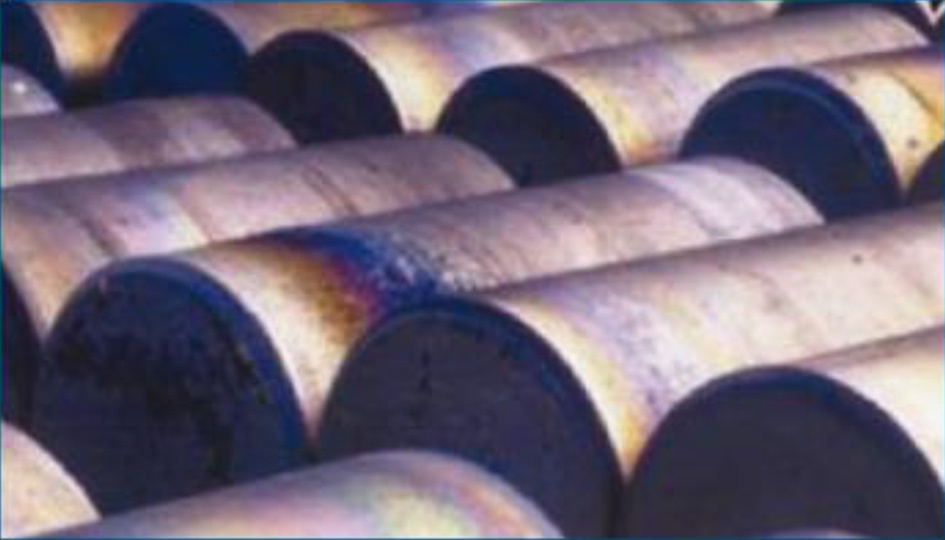
شکل 1-4-5 شمش تیتانیومی (Timet)
1-4-2 خانواده های تیتانیوم و آلیاژهای تیتانیومی برای جراحی ارتوپدی
1-4-2-1 پردازش بیشتر شکل نزدیک به دقیق آلیاژهای تیتانیوم
1-4-2-1-1 فورجینگ
ایمپلنت های ترمیمی ساخته شده از فلزات را می توان با روش ماشینکاری میله گردها یا ریخته گری به دست آورد، اما بسیاری از آنها با عملیات فورج دقیق ساخته شده اند. صنعت ارتوپدی یک عامل محرک در بهبود تکنولوژی های عملیات فورج بوده است. فورجینگ یکی از قدیمی ترین فرآیندهای شکل دهی فلز در جهان است که قدمت آن به 4500 سال قبل از میلاد باز می گردد. در طول قرن 10 میلادی، فورجینگ فرآیندی اولیه تنها برای ساخت سلاح، مانند شمشیر بود. اما این روش امروزه برای تولید محصولاتی با کارایی بالا و با مقاومت بالا نیز مورد استفاده قرار می گیرد (شکل 1-4-9 تا 1-4-11).
فورج دقیق ضمن افزایش مقاومت کششی استحکام تسلیم؛ ساختار دانه ریزتر و یکنواخت تری نیز ایجاد می کند. نتیجه استحکام بخشی این عملیات قویتر از نمونه هایی است که توسط هر فرآیند فلزکاری دیگر تولید می شود، زیرا فورجینگ جریان دانه ای جهت دار پیوسته است.
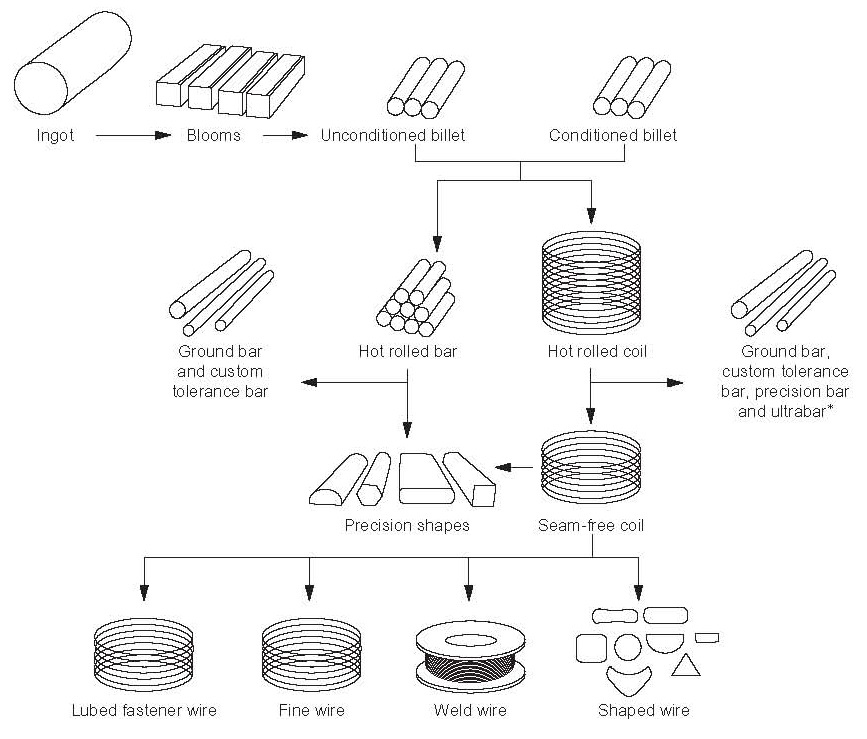
شکل 1-4-6 فرآیندها از شمش به پروفیل های سیم/ میله (شرکت Dynamet)
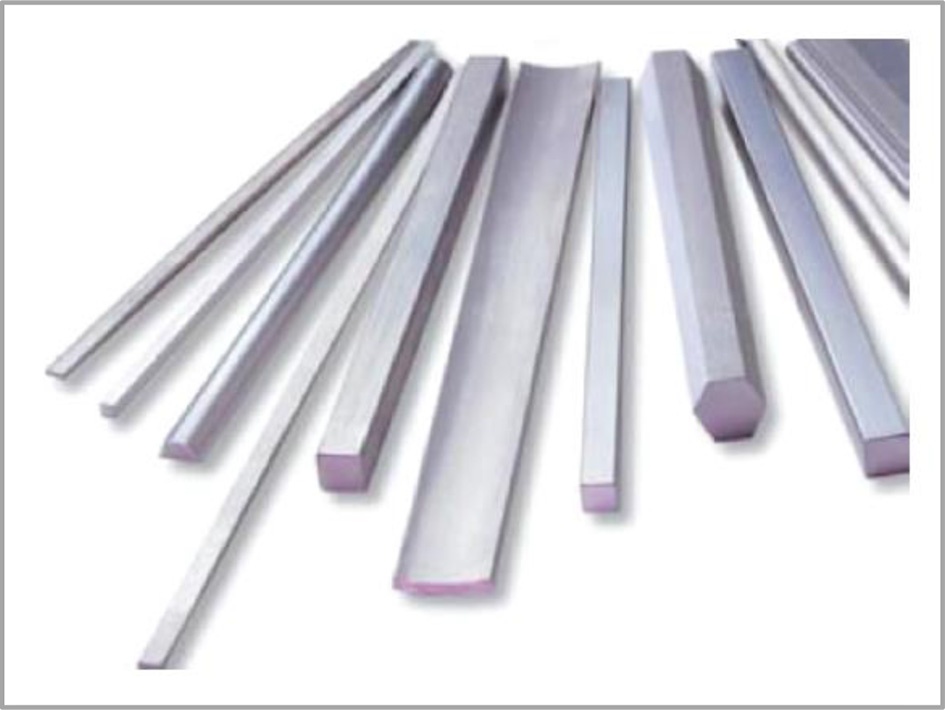
شکل 1-4-7 پروفیل های آلیاژ تیتانیوم (Dynamet)
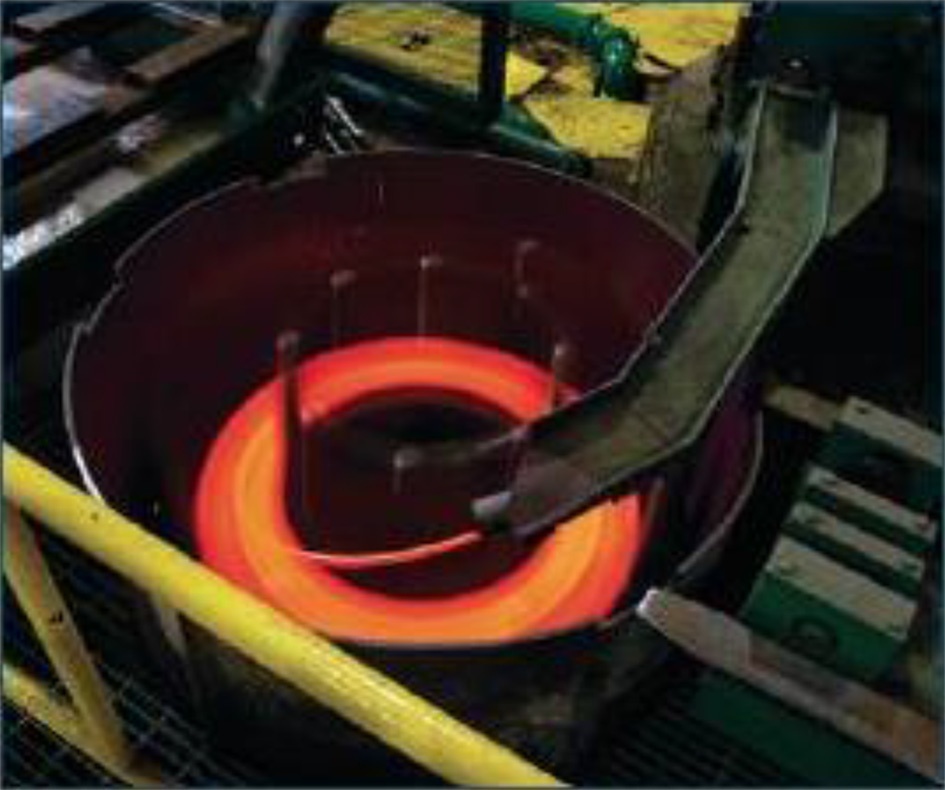
شکل 1-4-8 کلاف پیچی آلیاژ تیتانیوم (Dynamet)
1-4-2-1-2 ریخته گری دقیق
کاربرد روش ریخته گری دقیق، فرآیندی با استفاده از موم فداشونده موسوم به ریخته گری دقیق، به 1000 سال پیش از میلاد در بین النهرین برای ساخت مجسمه های هنری باز می گردد. در این روش باید مدل های مومی ساخته شود و همانند روش ساخت قطعه فلزی، مونتاژ آنها، پوشش آنها با شیب های مختلفی در سرامیکهای مایع و سپس اسپری آنها با ماسه های نسوز انجام شود. با ذوب کردن موم یک خوشه خالی به دست می آید که با فلز مذاب ریخته می شود (شکلهای 1-4-12 و 1-4-13). پردازش بیشتر شامل حذف سرامیک، از بین بردن مونتاژ، پرداخت، عملیات حرارتی و تست های غیرمخرب مانند بازرسی اشعه ایکس یا تست های دیداری با نفوذ فلوئورسنت است.
1-4-2-1-3 تولید به روش مواد افزودنی
فنآوری تولید مواد افزودنی (AM) اساساً با فرآیندهای حذف مواد سنتی مانند آسیاکاری، تراشکاری و فرسایش جرقه ای متفاوت است، زیرا این روش با افزودن مواد اضافی به جای حذف تراشه ها، اجزای فلزی را ایجاد می کند. شروع این کار با نمایش سه بعدی CAD از یک قطعه و ورقه ورقه کردن قطعه به مجموعه ای از لایه های دو بعدی است. این لایه ها سپس با موفقیت تلفیق می شوند و در بالای یکدیگر ادغام می شوند تا بتوانند شی سه بعدی را از نو بسازند (شکل 1-4-14 تا 1-4-16). فنآوری های AM که چندین دهه است توسعه یافته، در ابتدا به عنوان فنآوری های نمونه سازی پلاستیک استفاده شد. در طول دهه گذشته، فناوری های فلزی AM به منظور بهره مندی از مزایای AM برای ساخت قطعات فلزی توسعه یافت. ذوب انتخابی لیزری (SLM) و ذوب پرتو الکترونی بهترین فناوری های AM برای ساخت فلز با کیفیت بالا است. در این فرآیندها، لایه های نازک پودر فلزی (به طور معمول 20-40 میکرومتر) براساس یک سیستم رسوب پودر پخش می شوند. در مرحله بعد، از یک پرتو متمرکز لیزری برای اسکن یک لایه دو بعدی از مؤلفه سه بعدی استفاده می شود. این روند تا زمانی که کل جسم سه بعدی چاپ شود، تکرار خواهد شد.
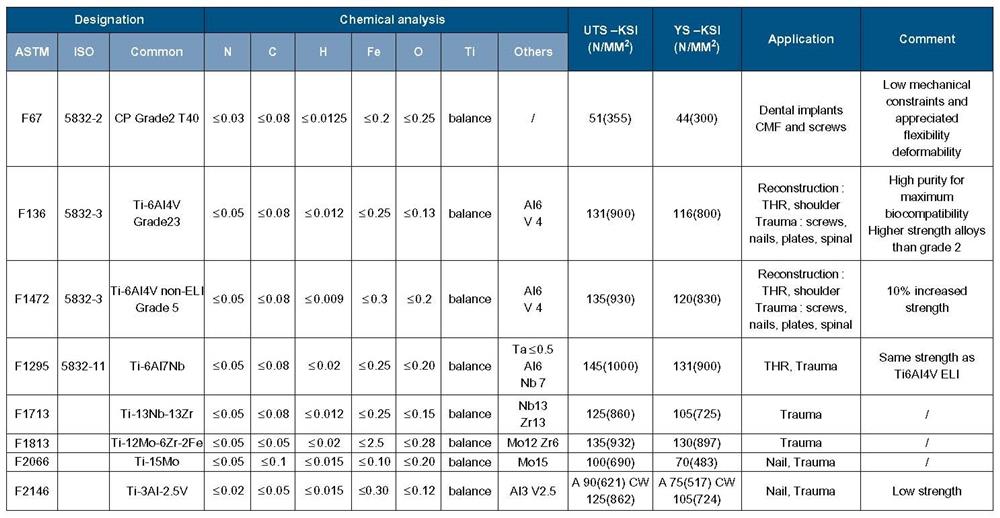
شکل 1-4-9 خانواده های تیتانیوم و آلیاژهای آن
تولید ایمپلنت های خاص با فناوری SLM به علت دامنه آزادی هندسی نامحدود کاملاً مناسب است. علاوه بر ایمپلنت های سفارشی، این فناوری ها همچنین امکانات جدیدی را برای تولید ایمپلنت های استاندارد و ابزار دقیق ارائه می دهند. به عنوان مثال، ایمپلنت های ارتوپدی با مناطق متخلخل یکپارچه برای بهبود پیوند استخوانی طراحی می شوند. شکل 1-4-3 بکارگیری تیتانیوم در استخوان ران را نشان می دهد که شامل چهار طرح داربست مختلف و درجات مختلف پرداخت سطح است.

شکل 1-4-10 عملیات فورج ساقه لگن (پزشکی SMB، سوئیس)
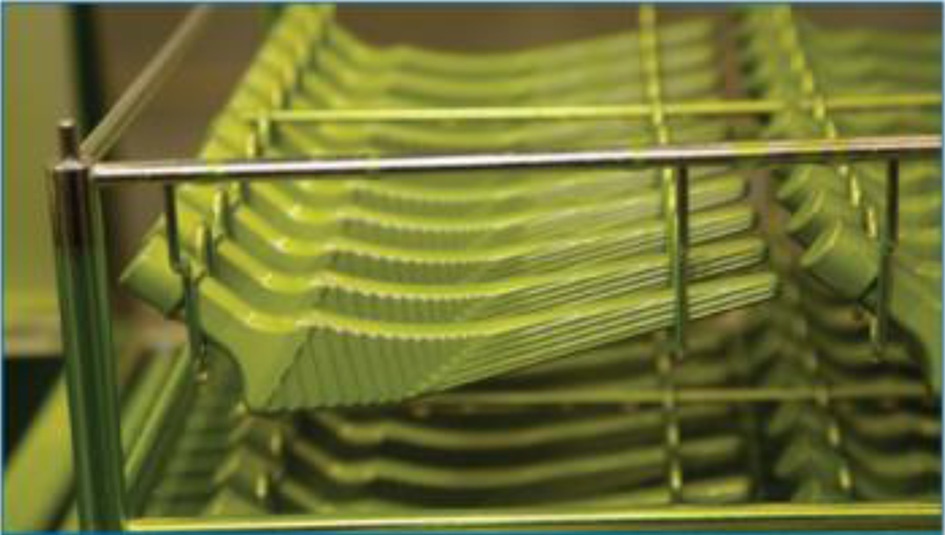
شکل 1-4-11 نفوذ رنگ (پزشکی SMB، سوئیس)
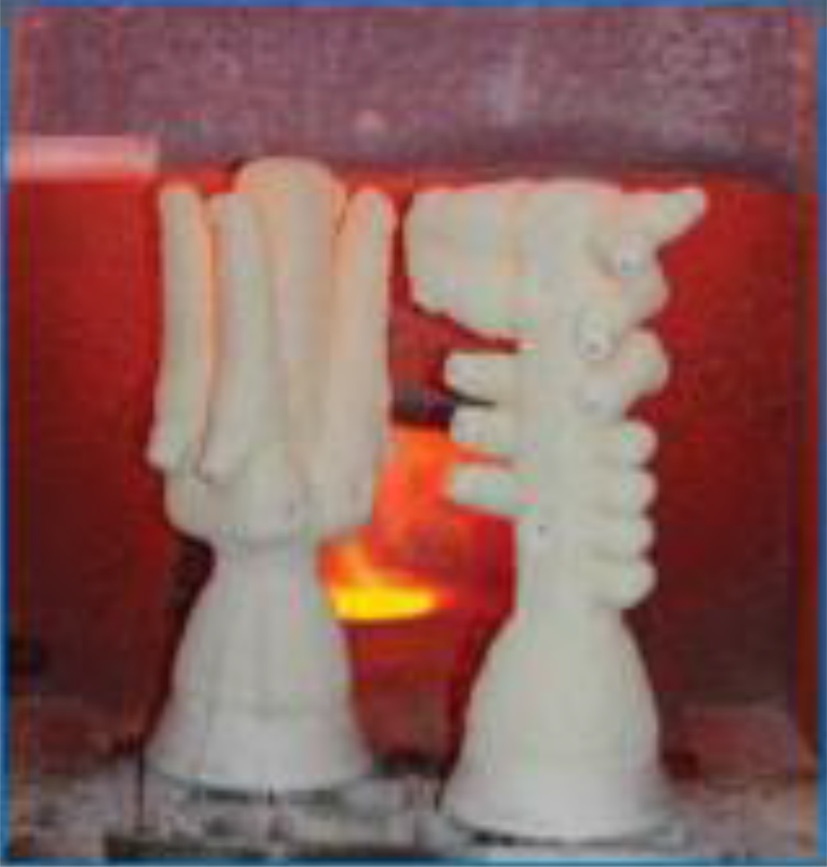
شکل 1-4-12 ریخته گری دقیق، شرکت MediMet GmbH آلمان
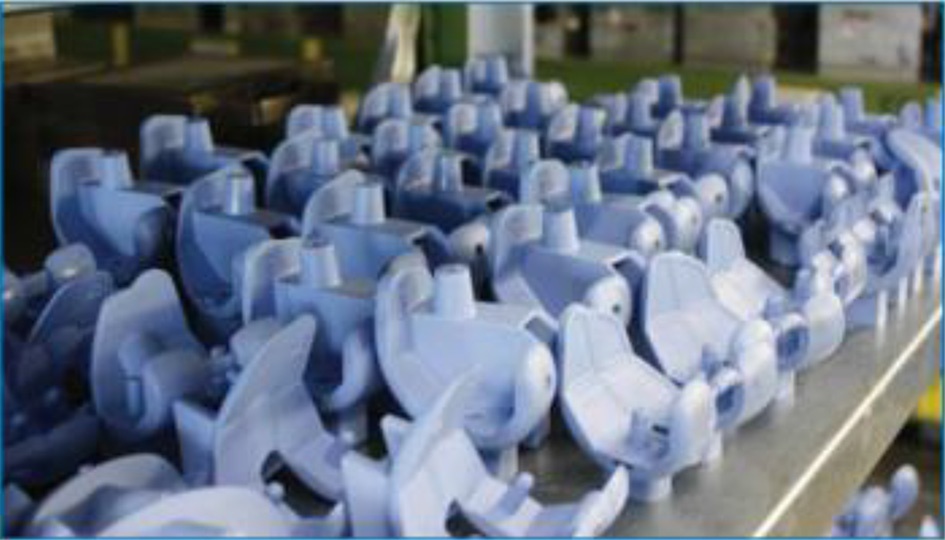
شکل 1-4-13 مفصل کامل زانو، شرکت MediMet GmbH آلمان
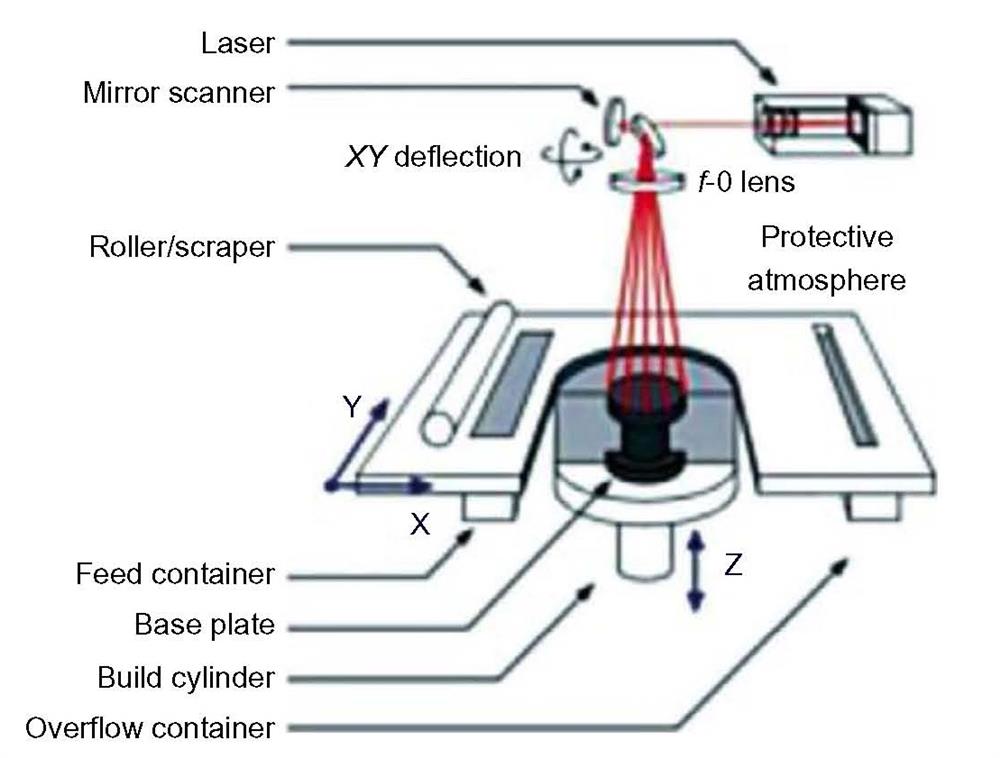
شکل 1-4-14 شماتیکی از فرآیند ذوب انتخابی لیزری
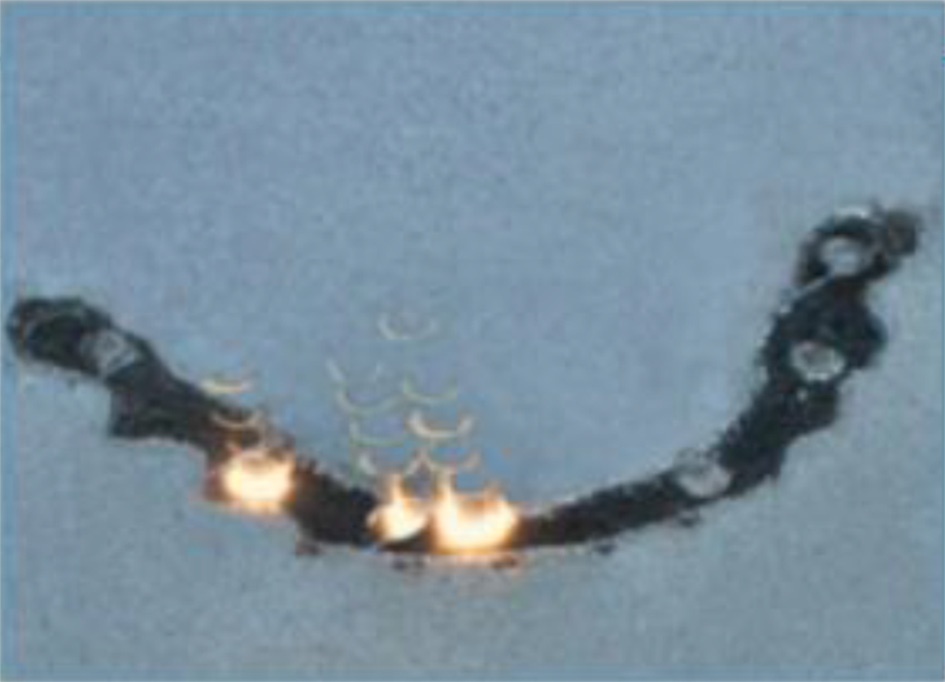
شکل 1-4-15 تولید SLM از یک ابرساختار ایمپلنت دندانی در Ti-6Al-4V(سیستمهای 3D، بلژیک).
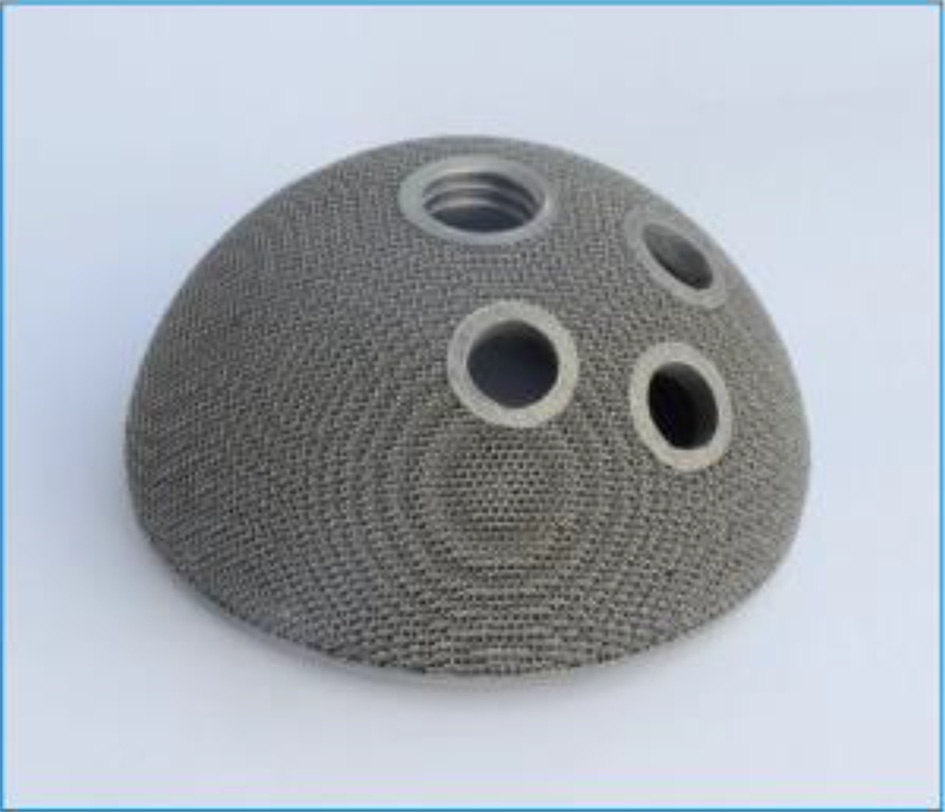
شکل 1-4-16 ایمپلنت لگن تولید شده با داربست استخوانی یکپارچه، استحکام اولیه و طولانی مدت را بهبود می بخشد (سیستمهای 3D، بلژیک).
1-4-2-1-4 ماشینکاری ارتوپدی
محصولات و فنآوری های پزشکی در سلامت انسان نقش بسیار زیادی دارند و تحرک و نشاط را در پیری ترویج می دهند. افزایش تقاضا و استانداردهای بالای تحمیل شده بر کیفیت محصولات پزشکی، تعیین کننده توسعه بخشی است که علیرغم بحران اقتصادی، در حال رشد می باشد. پیشرفت پایدار در مهندسی پزشکی به مراتب تقاضاهای جدید روی دستگاهها را مقرر می سازد که برای تولید محصولات با دقت بالا مورد استفاده قرار می گیرد.
پنجاه سال پیش، ایده ایمپلنت ها و مفاصل مصنوعی در جراحی هنوز انقلابی بود، اما امروزه این موضوع یک بخش ثابت از پزشکی روزمره است. شکستگی های پیچیده با پیچ ها و پلیت های استخوانی ترمیم می شوند و این روزها مفاصل فرسوده لگن نیز قابل تعویض هستند. با این وجود، برای چنین اقداماتی در جراحی به محصولات مناسب و باکیفیت بالا نیاز است. این موارد نه تنها مستلزم استفاده از مواد عالی که معمولاً ماشینکاری آنها دشوار است، می باشند؛ بلکه باید بالاترین تقاضا را روی دقت، کیفیت سطح و دقت ابعادی محصولات پزشکی قرار داد (شکل 1-4-17).
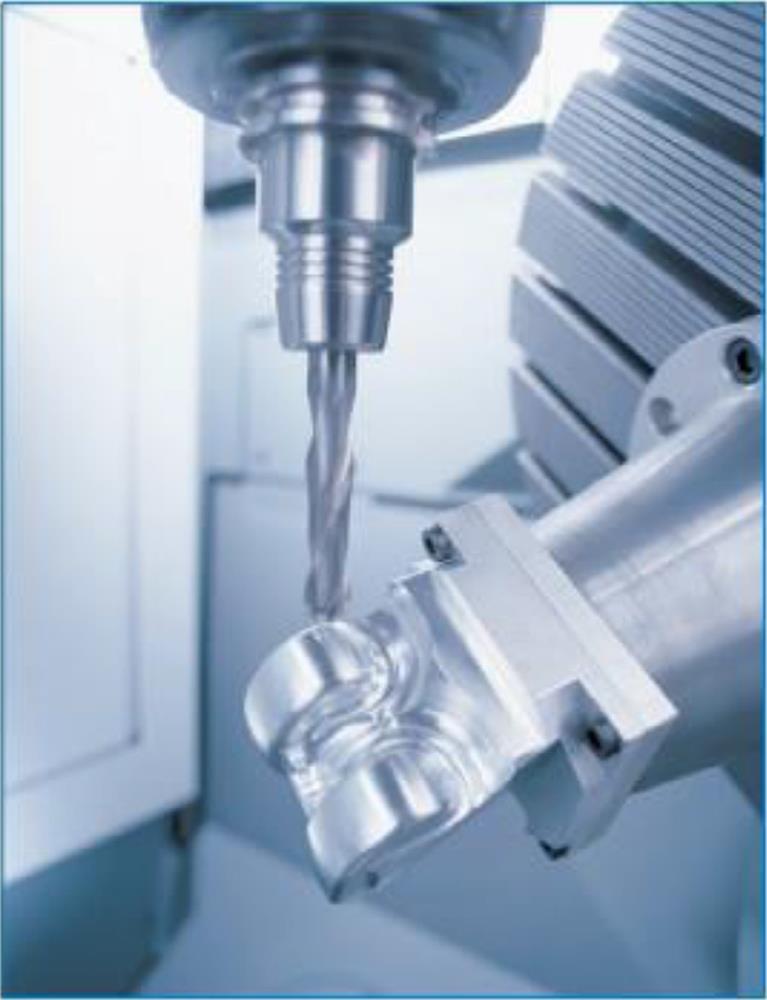
شکل 1-4-17 ماشینکاری مفصل زانو (شرکت موری DMG، آلمان).
نمونه ای از مفاصل مصنوعی نشان می دهد که ماشینکاری کارآمد تنها در دستگاه های فرزکاری با کارایی بالا قابل انجام است. مواد عالی مانند تیتانیوم و همچنین مواد ویژهای از قبیل: زیرکونیوم، سرامیک ها و پلاستیک های مخصوص دلایل کافی برای استفاده از روش های نوین ساخت مانند فرزکاری HSC، هستند. یک استدلال مشابه در مورد ایمپلنت ها نیز صادق است، که در آسیب شناسی معمولاً فقط به صورت موقت وارد می شوند و استخوانها بهبود می یابند. در این حالت، بیشترین تقاضا روی پرداخت سطح است تا ایمپلنت به استخوان نچسبد (شکلهای 1-4-18 و 1-4-19).
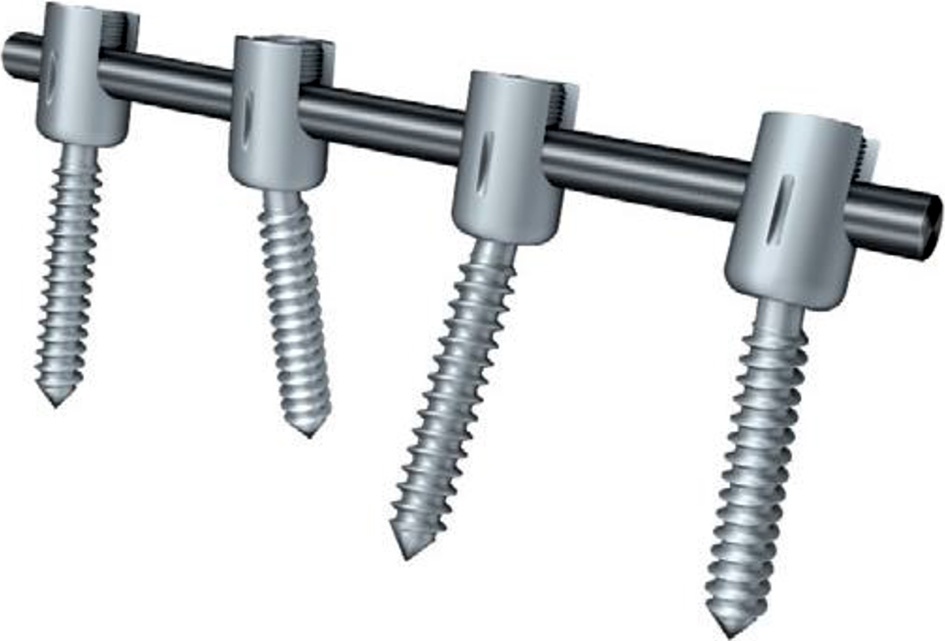
شکل 1-4-18 پیچ های ستون فقرات نخاعی (شرکت سندویک سوئد)
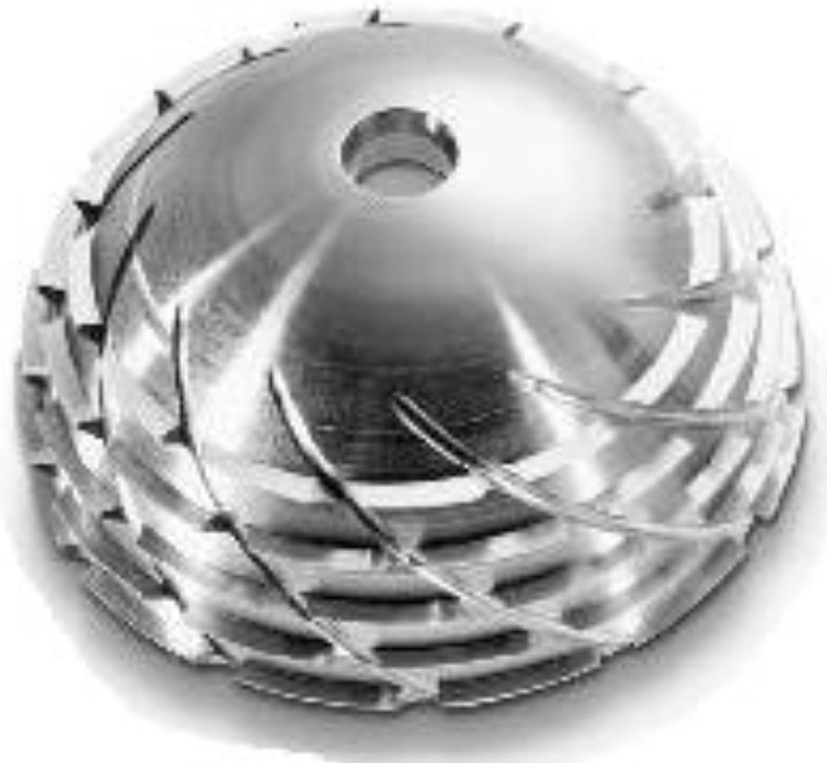
شکل 1-4-19 هیپ فنجانی شکل (شرکت DMG موری، آلمان)
1-4-3 رویکرد اختصاصی برای تولید میله های کانوله شده(توخالی) برای نیلها و پیچ های تروما
1-4-3-1 تمرکز روی حالت کانوله شده(توخالی)
1-4-3-1-1 روش گاید سیم کیشنر با حداقل تهاجم
دکتر کیشنر برای اولین بار در سال 1910 میلادی روش گاید سیم را معرفی کرد تا بتواند شکستگی را با استفاده از دستگاهی برای تروما رفع کند. از آن زمان، این روش جراحی با موفقیت در آرتروسکوپی، پزشکی ورزشی، قطعات کوچک، اندام ها و درمان ستون فقرات گسترش یافته است.
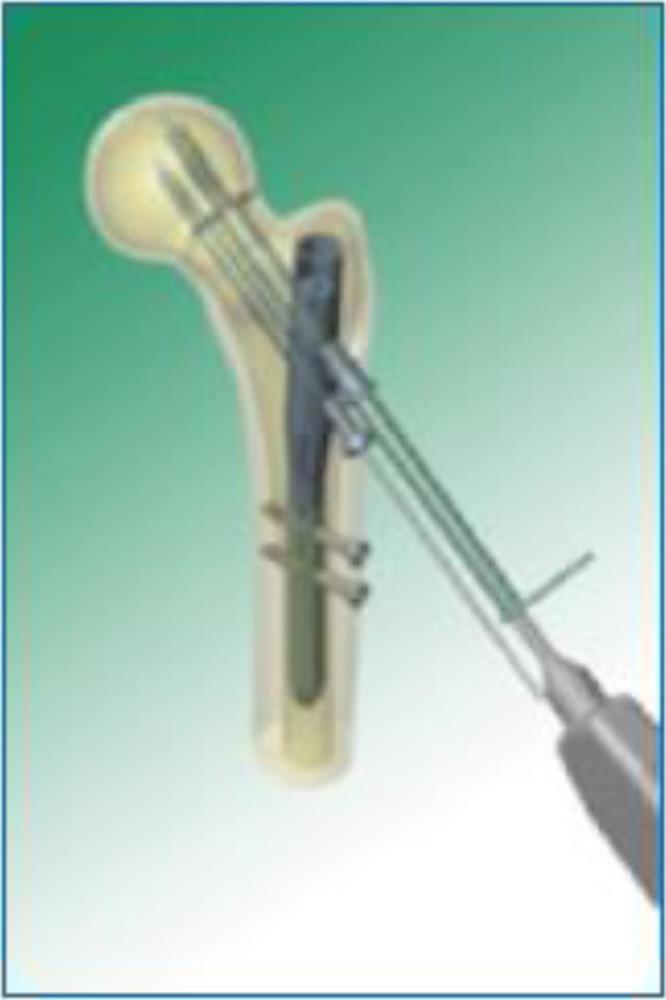
شکل 1-4-20 جراحی ارتوپدی با سیم K.
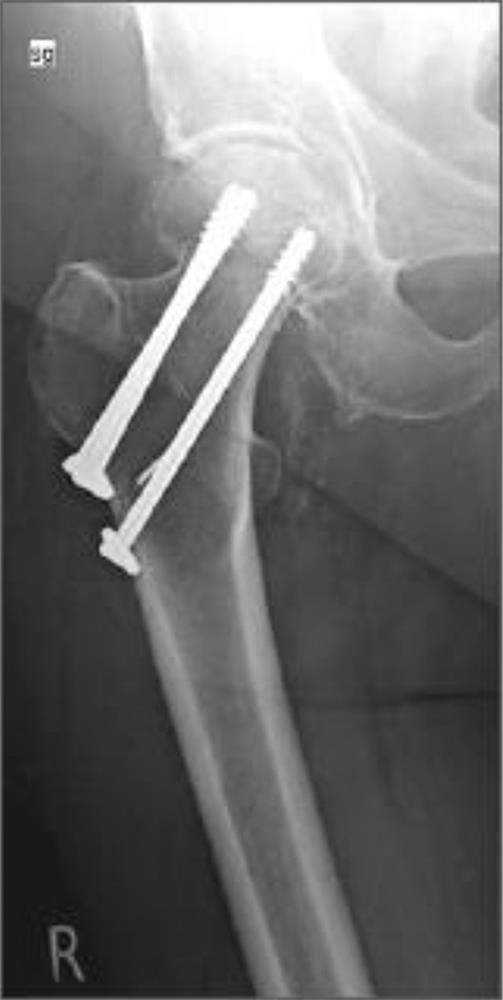
شکل 1-4-21 اشعه ایکس فشرده سازی پیچ هیپ (Forecreu، فرانسه)
این گاید سیم از یک سیم فولادی زنگ نزن سخت معمولاً از جنس L316، آلیاژ 630 پیرسختی شده و آلیاژ حافظه دار Nitinol یا CoCrMo با استحکام تسلیم بالا ساخته شده است. محدوده قطرهای معمول 0.6 تا 3.2 میلیمتر است که به اندازه ایمپلنت ها وابسته می باشد. دارای یک نقطه تیز یا رشته ای است که می تواند با ترومای محدود وارد استخوان شود. ایده این است که این سیم را در استخوان قرار دهید و از آن به عنوان راهنما برای مراحل بعدی که معمولاً کنترل عمق، سوراخ کاری، مته کاری و غیره است، استفاده می شود. بنابراین جراح ارتوپدی می تواند ضمن نگه داشتن سیم K در استخوان، پیچ کانوله شده را با یک محرک وارد کند. با استفاده از این تکنیک، دسترسی دقیق و مطمئن به مواد کمیاب استخوان برای رفع شکستگی تضمین می شود (شکلهای 1-4-20 و 1-4-21).
1-4-3-1-2 ابزار و ایمپلنت های ازپیش سوراخ شده (کانوله شده)
از طرف جراحان تقاضای سیستمهای جراحی با حداقل تهاجم (MIS) وجود دارد. برای این کار نیاز به ارائه ابزارها، نیل ها و پیچ ها با یک سوراخ مرکزی داریم. محصولات تروما معمولاً در تراش های CNC روی میل گردها ماشینکاری می شوند. ایجاد سوراخ طولی متمرکز یک روش آسان نیست و می توان از چنین فناوری هایی از جمله بورینگ/ سوراخکاری، استفاده از لوله های دیواره ضخیم و میله های از پیش سوراخ شده اختصاصی استفاده کرد (شکلهای 1-4-22 تا 1-4-24).
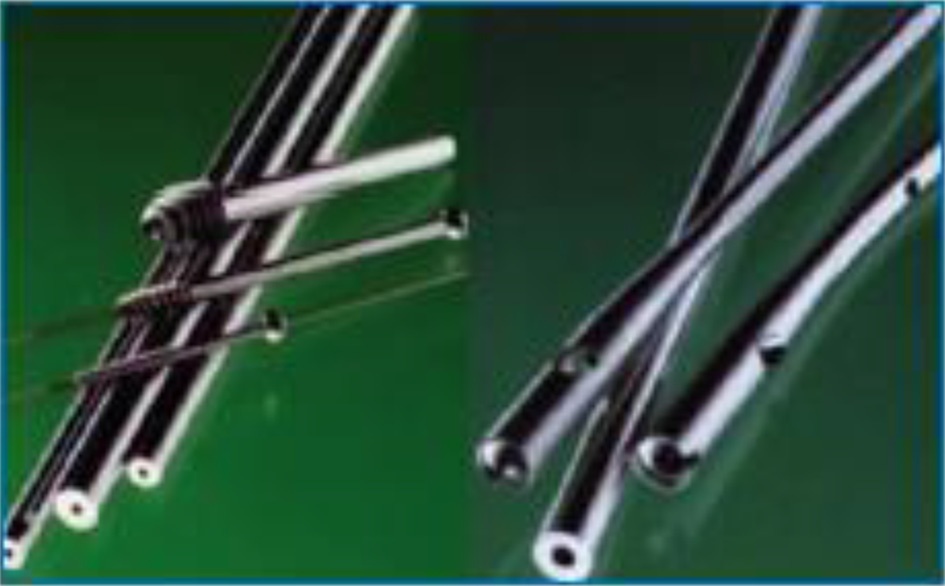
شکل 1-4-22 میله ها، پیچ ها و نیل های کانوله شده (Forecreu، فرانسه)
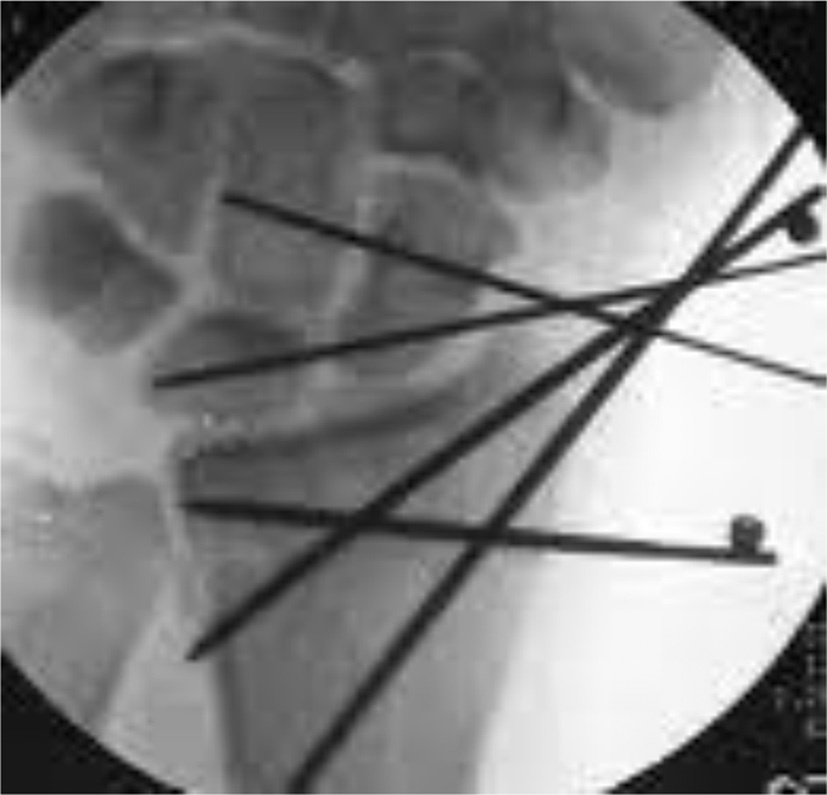
شکل 1-4-23 اشعه ایکس قطعات کوچک (Forecreu، فرانسه)
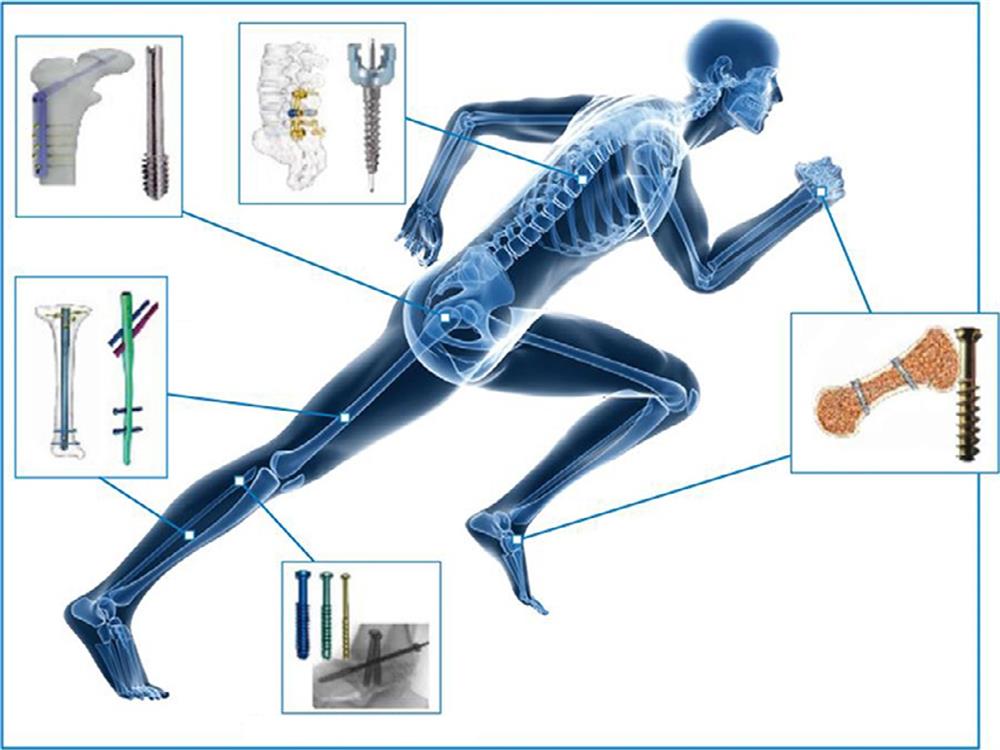
شکل 1-4-24 کاربرد ابزار کانوله (Forecreu، فرانسه)
1-4-3-1-3 لوله مغزی در مقابل میله های کانوله شده(توخالی)
لوله های مرسوم با دیواره ضخیم یا متوسط مطابق مراحل زیر تولید می شوند. یک بیلت (شکل 1-4-25) به صورت طولی و سرتاسری سوراخکاری می گردد. تا دمای آهنگری گرم و اکسترود می شود. اینسرت قرارداده شده در پیشانی بیلت باعث ایجاد یک لوله توخالی می شود، زیرا ماده بین قالب و این قطعه جریان می یابد.
چندین روش کشش لوله همانطور که در شکل نشان داده شده ترکیب و اعمال می شوند.
محدودیت های این روش هندسه سطح حاصل از فرآیند، فرورفتگی ها و خطر احتمالی واکنش روانساز با پلاگ کاربید یا فرآیند ماندریل سخت است. از آنجایی که مراحل آنیلینگ برای کاهش مقطع لازم است، اثرات روغنکاری شده باقیمانده می توانند به خوردگی بین دانه ای تبدیل شوند. با کوچکتر شدن قطر داخلی و ضخیم تر شدن دیواره، این روند دشوارتر می شود.
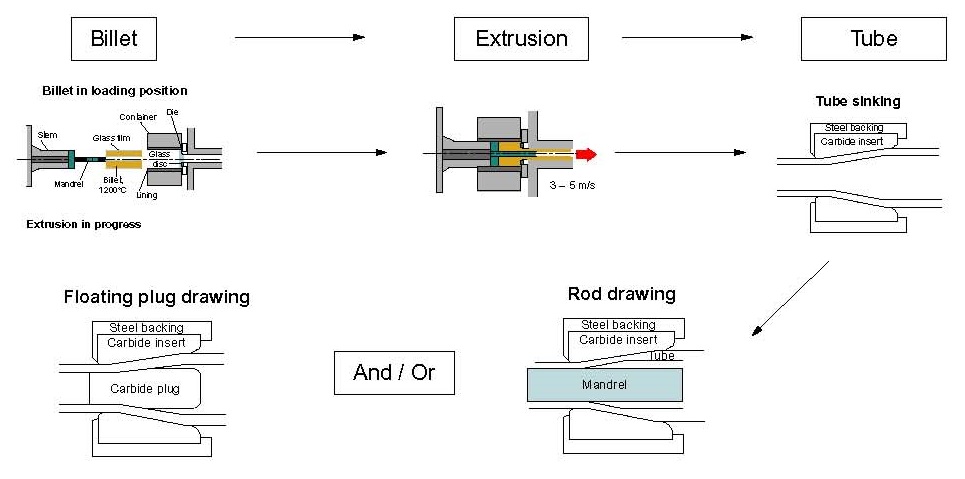
شکل 1-4-25 فرآیند لوله سازی مرسوم (Forecreu، فرانسه)
1-4-3-1-4 ساخت کانوله (توخالی)
فرآیند خاصی برای ساخت به وسیله اینسرت کردن یک میله داخل بیلت سوراخ شده طراحی شده، همانطور که در مسیر پردازش زیر نشان داده شده است. خواص این فرآیند عبارتند از:
-
حفظ نرخ هموتتیک
-
بدون پیشامد فرو رفتگی در طول عملیات کشش لوله، از بروز عیوب سطحی جلوگیری می شود.
-
بدون خطر آلودگی به وسیله روانسازها در طول عملیات حرارتی یا آنیلینگ.
-
بدون محدودیت در اندازه گذاری ID برای کوچکترین سیمهای K مانند “0.023(mm 0.6) تا “0.031(mm 0.8).
با استفاده از روشهای اکستروژن دوتایی، نورد و طراحی شکل دهی داغ.
شروع با یک بیلت مدور 100/120 میلیمتری (4-5“) است. سیلندر، استوانه سوراخکاری شده عمیق با طول 400 تا 600 میلیمتر است. سپس یک اینسرت که قبلاً با یک لایه خاص پوشیده شده، داخل سوراخ جاسازی می شود.
مرحله اول شامل اکستروژن سیلندر در دمای فورجینگ است. اکستروژن بیلت گرم را داخل یک قالب با سرعت متوسط 2 تا 4 متر بر ثانیه با حداکثر 25 تا 30 برابر تغییر طول فشار می دهد. پروسه های دیگر شامل نورد سه غلطکه و نهایتا کشش گرم و کالیبراسیون است.
برای به دست آوردن سوراخ نهایی، هسته ماده اینسرت شده که به سیم تبدیل شده باید حذف شود. سیمها به روش کشش و با توجه به خواص شکل پذیری مناسب میله اینسرت شده خارج می شوند (شکلهای 1-4-26 تا 1-4-29).
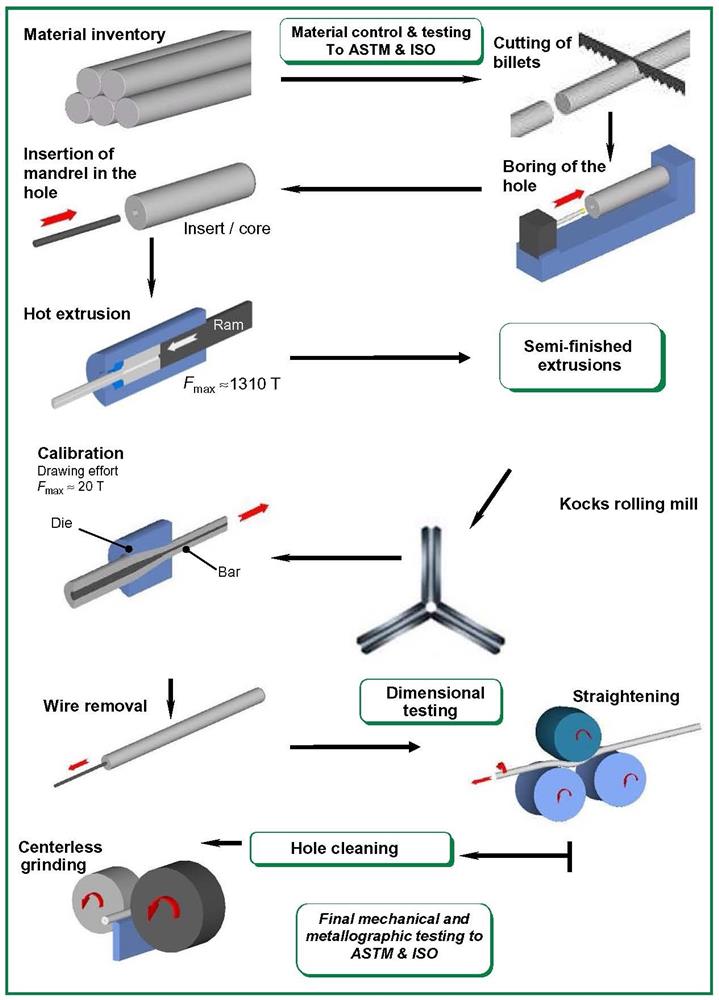
شکل 1-4-26 مراحل پروسه ساخت (Forecreu، فرانسه).
-
تمرکز روی مواد هسته (اینسرت)
اکستروژن گرم کامپوزیت، مستلزم آن است که جریان جداره از درون قالب عبور کند. بسته به دمای فورجینگ، ایده این بود که ترکیبی از هسته- بیلت ساخته شود تا در دماهای اکستروژن دارای استحکام یکسانی باشد، به طوری که هسته به تناسب کاهش یابد. انعطاف پذیری بالا برای استخراج سیم و خروج نهایی موردنیاز بود. سپس مواد مندرل متناسب با این نیاز تولید شدند. نیاز و برنامه ریزی نهایی خواستار یک هسته از بین رونده خود کاهش دهنده بسیار انعطاف پذیر است. خواص و متالورژی این نوع هسته بسیار اختصاصی خواهد بود(شکل 1-4-30).
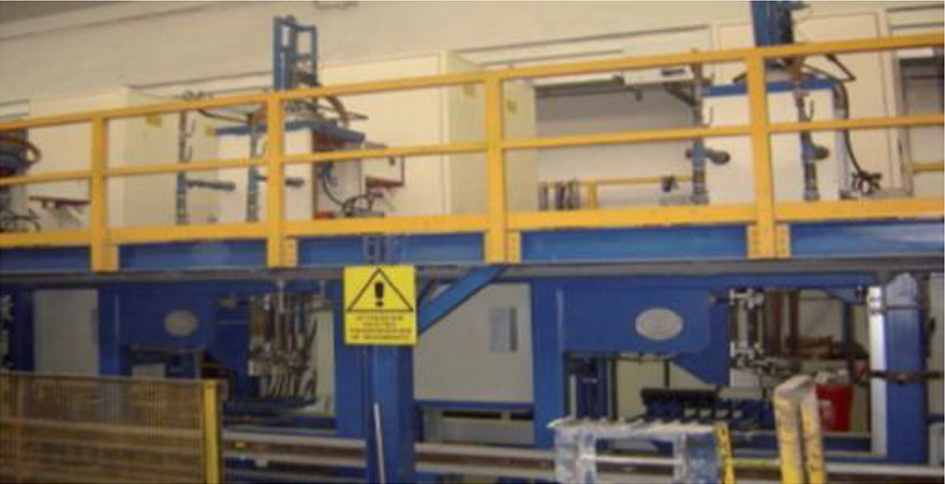
شکل 1-4-27 (بالا) پرس افقی 1310 تنی LOEWY + cells3 kW BANYARD 350
گرمایش القایی (Forecreu، فرانسه).
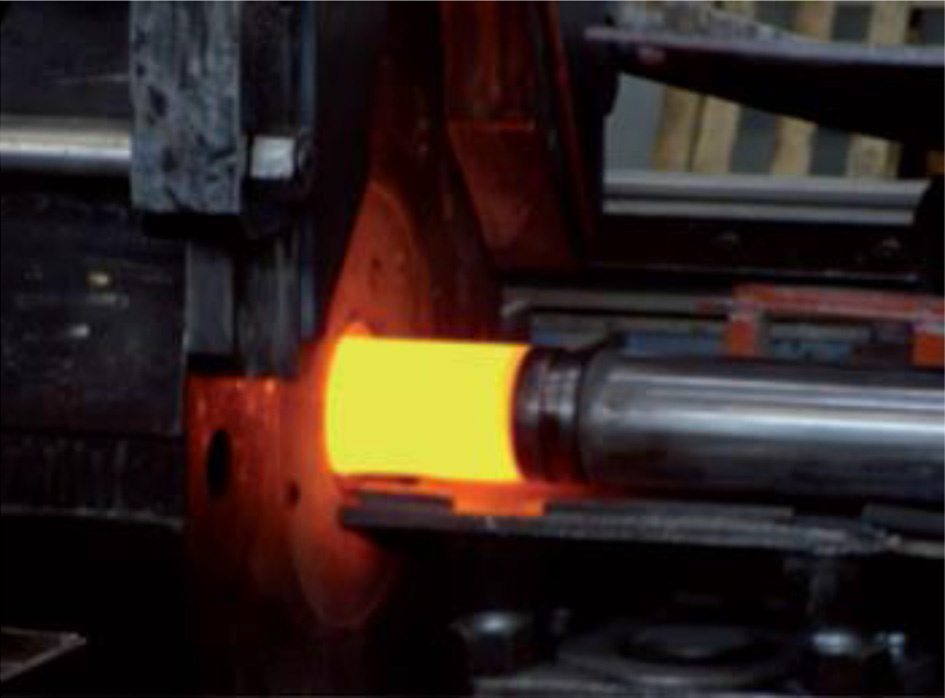
شکل 1-4-28 عملکرد اکستروژن (Forecreu، فرانسه)
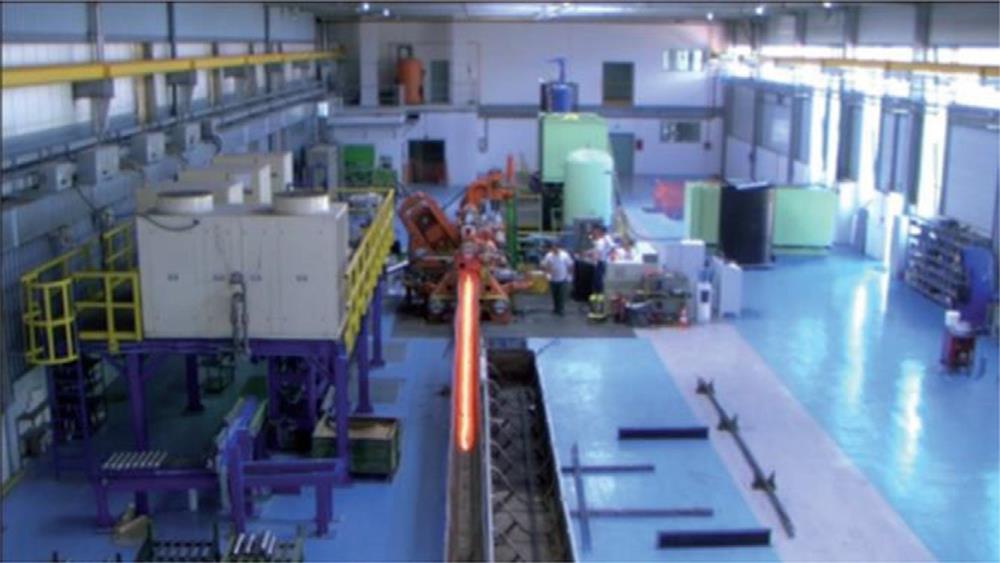
شکل 1-4-29 (پایین) پرس افقی 1310 تنی LOEWY + cells3 kW BANYARD 350
گرمایش القایی (Forecreu، فرانسه)
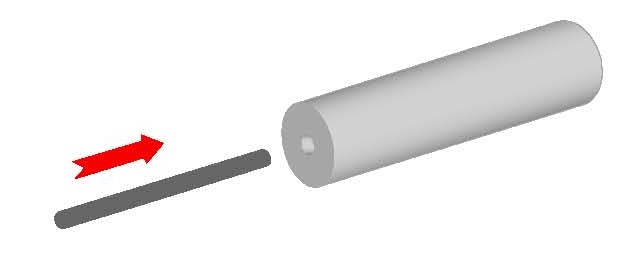
شکل 1-4-30 جایگذاری هسته (Forecreu، فرانسه)
-
تمرکز روی انتخاب فیلم های پوشش
پیش نیاز کاربردهای ارتوپدی پزشکی و فرایندهای فورجینگ گرم، ایجاد ماده بی اثر، غشای توقف و پیشگیری ضد نفطه جوش است و با این حال قابلیت تخلیه و زیست سازگاری در میان چندین ویژگی وجود دارد. چالش، اطمینان حاصل کردن از این پوشش در طول عملیات حرارتی طولانی در برابر ایجاد هر نقطه جوش- اتصال متالورژیکی است.
این روش به طور گسترده در فلزات آهنی و غیر آهنی برای ساخت لوله های توخالی، پروفیل ها یا مواد کامپوزیت و جامد استفاده می شود (شکل 1-4-31).
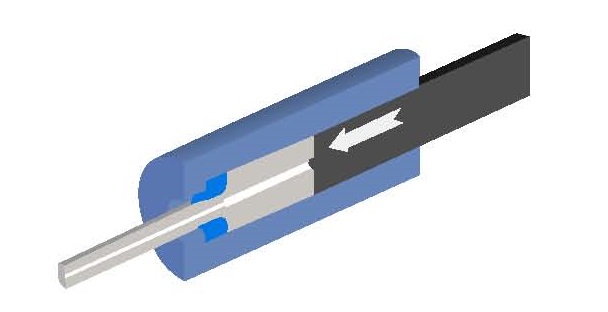
شکل 1-4-31 اکستروژن (Forecreu، فرانسه)
روانساز نقش فعالی در خود فرآیند دارد. روانسازها معمولاً تا دمای 600 درجه سانتیگراد پایه گرافیتی دارند، در حالیکه روانسازهای اکستروژن های فولاد یا دما بالاتر از 900 درجه سانتیگراد مبنی بر شیشه هستند. بیلت و یا کانتینر اکستروژن، هر دو را می توان روغن کاری کرد.
سطوح بیلت تیتانیوم قبل از حرارت دهی روکش می شود و سپس روی یک بستر شیشه ای چرخانده می شود. کانتینر اکتروژن نیز روکش شده است. هر گونه گسستگی در پوشش هنگام عملیات اکسترود، تقارن را به خطر می اندازد، همانطور که در شکل نشان داده شده است.همچنین ثابت شده که اکستروژن تنها فرآیند آهنگری است که می تواند موقعیت مناسب سوراخ اتصال دهنده را حفظ کند.
بنابراین کنترل دمای ذوب شیشه بسیار مهم است، زیرا عملیات اکستروژن 900 یا 950 درجه سانتیگراد به انواع مختلفی از شیشه ها نیاز دارد (شکل 1-4-32 و 1-4-33).
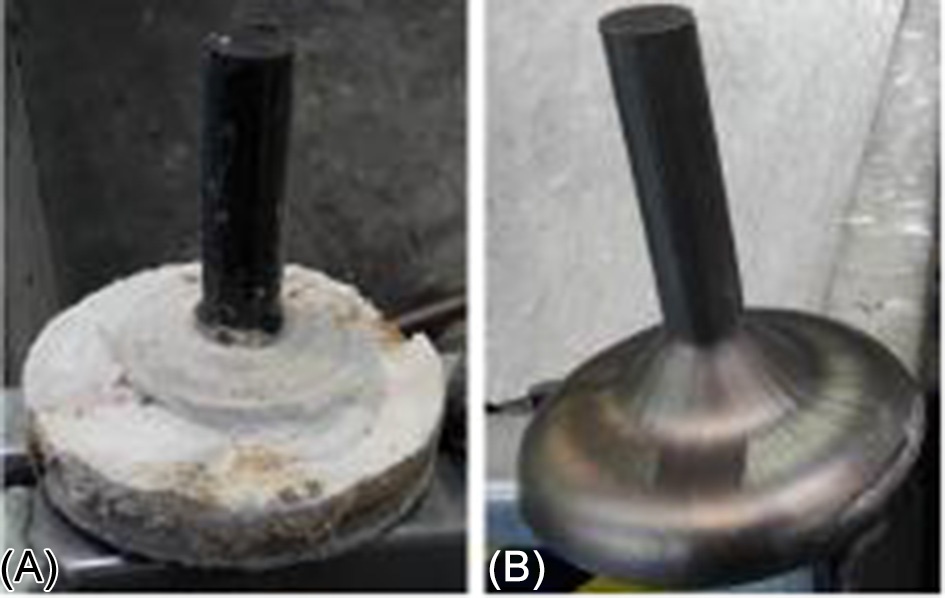
شکل 1-4-32 تغییر شکل بعد از اکستروژن: (A) با روغنکاری، (B) تمیزکاری (Forecreu، فرانسه)

شکل 1-4-33 جریان مواد کامپوزیت در طول اکستروژن (Forecreu، فرانسه)
هنگام ورود به کانتینر، بیلت پوشش داده شده با نیرویی به طور معمول t1300 (athm 200) تحت فشار قرار داده خواهد شد و تا پر شدن کانتینر فشرده می شود. پس از آن جریان ثابت خواهد ماند. شکلهای 1-4-34 و 1-4-35 پیک اولیه فشاری و سپس تا حدودی فشار ثابت را نشان می دهند و سرعت آن به 4 متر بر ثانیه می رسد، تا زمانی که متوقف شود. کنترل ترکیبی پارامترها (دما، سرعت و فشار) کلید تمرکز سوراخ مناسب است.
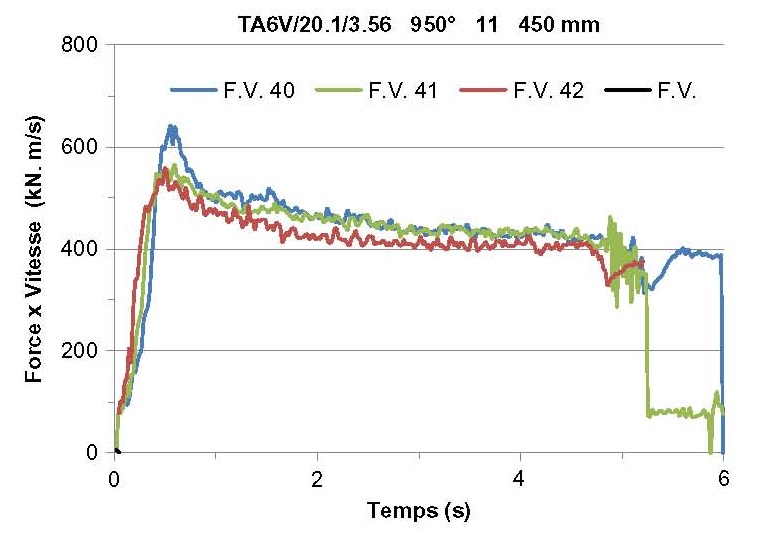
شکل 1-4-34 اکسترود 4-6-Ti (Forecreu، فرانسه)

شکل 1-4-35 اکستروژن 15-5 PH (Forecreu، فرانسه)
وقتی میله کامپوزیتی اکسترود شده برای مرحله بعدی (شکل آنالیز تشخیص تصویر) تمیز می شود، انتهای میله با قالب ریزی به شکل نازکتر ساخته شده و سپس از طریق یک قالب طراحی می شود؛ بنابراین قطر در حال کاهش خواهد بود. میله کامپوزیتی به عنوان ماده جامد کاهش یافت. بر اساس نوع آلیاژ، دما از سرد به ملایم و سپس گرم تنظیم می شود. روانساز اضافه می شود: صابون، MoS2 یا گرافیت. این فرآیند بسیار کند است، زیرا تورفتگی در مقابل فشرده سازی و خطرات وابسته به آن وجود دارد. محدوده سرعت از m/mn 3 تا 5 با کاهش 15 تا 20% مقطع است (شکلهای 1-4-36 و 1-4-37).
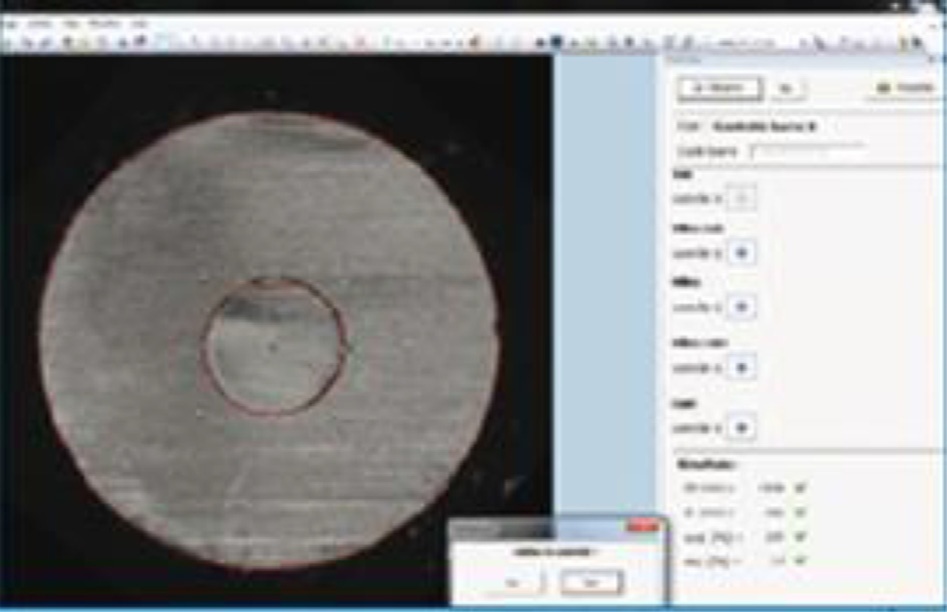
شکل 1-4-36 عکس دوربین (Forecreu، فرانسه)
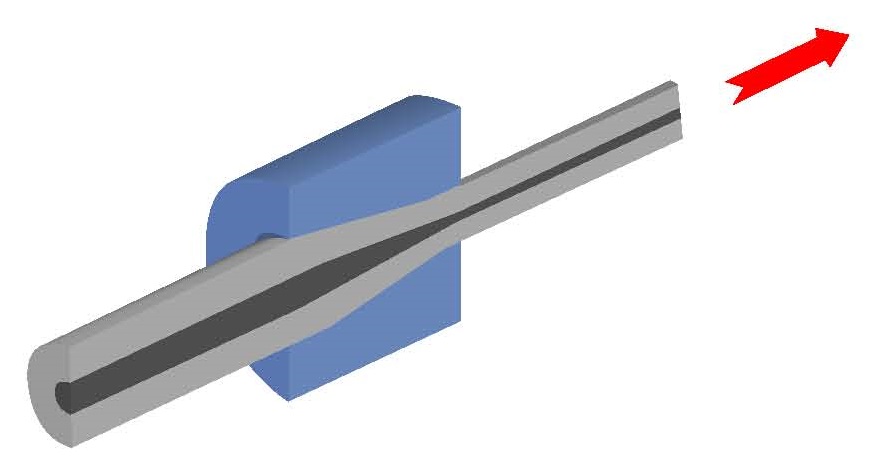
شکل 1-4-37 عملیات کشش (Forecreu، فرانسه)
در بین روش های نورد، دو تا سه روش اصلی نورد وجود دارد. نورد سه غلطکه به دلیل ساختار پیچیده ای که دارد برای مواد سخت قابل فورج طراحی شده است. تیتانیوم و آلیاژهای آن دارای یک ساختار متالورژیکی بسته شش ضلعی هگزاگونال (hcp) است، بنابراین روش نورد سه غلطکه (شکل 1-4-38) کارآمدتر است (شکلهای 1-4-39 و 1-4-40).
سپس میل گرد اکسترود شده با استفاده از کاهش مقاطع مثلثی به طور متوالی با یک نورد دایره ای نهایی به سمت ابعاد کوچکتر نورد می شود، همانطور که در شکلهای 1-4-41 و 1-4-42 نشان داده شده است.
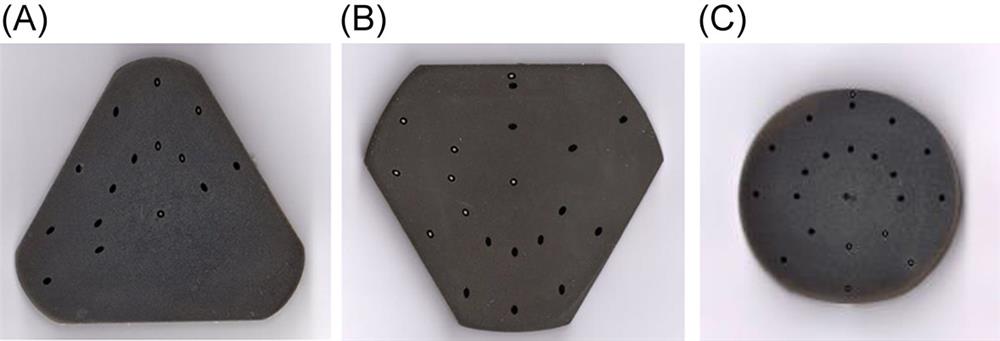
شکل 1-4-38 نورد مثلثی. (A) نورد با استفاده از سه پایه رول (KOCKS)- پاس اول. (B) نورد با سه پایه رول (KOCKS)- پاس دوم. (C) نورد با دو پایه- پاس دوم.
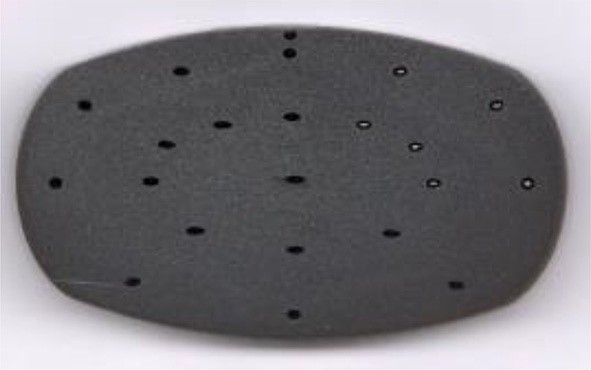
شکل 1-4-39 نورد دوتایی. نورد با دو پایه- پاس اول.
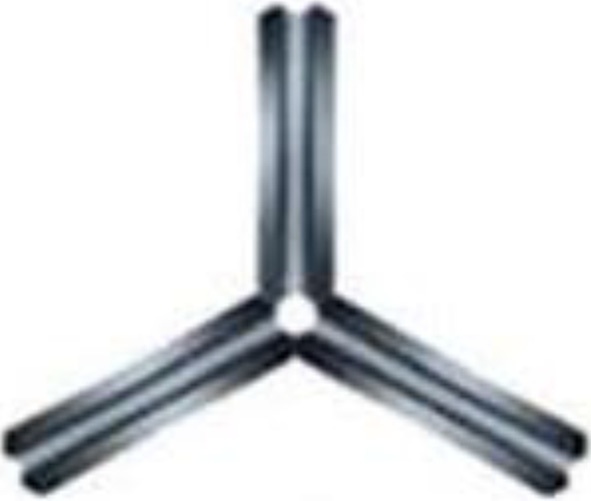
شکل 1-4-40 نورد گرم Kocks (Forecreu، فرانسه).
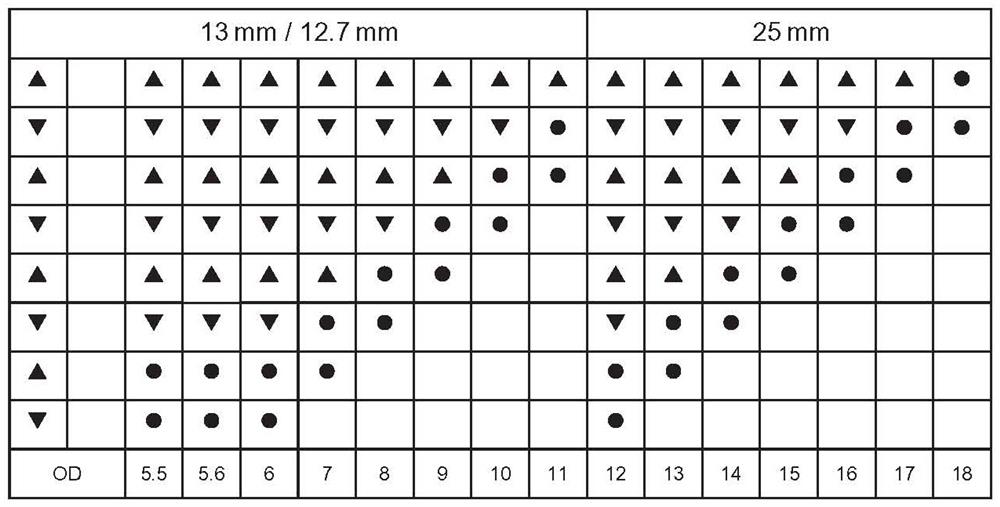
شکل 1-4-41 مقادیر بالا سایز ورودی به نورد - ورق یا میله گرد- و مقادیر پایین سایزخروجی آن هاست (Forecreu، فرانسه).
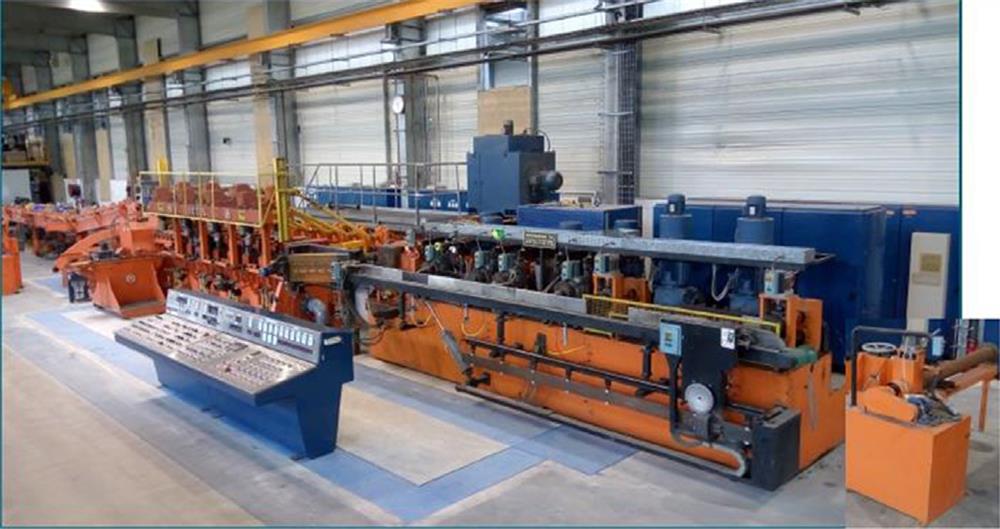
شکل 1-4-42 خط نورد با هشت ایستگاه نورد (Forecreu، فرانسه)
هسته در اصل دایره ای با قطر 10-40 میلیمتری است که طی عملیات اکستروژن، نورد و کشش کوچکتر می شود. تفاوت جنس دو ماده اجازه بیرون کشیدن سیم را می دهد، به اندازه قطر خیلی کوچک 0.6 تا 5 میلیمتر به طول 3 تا 4 متری میله شکل می گیرد (شکل 1-4-43).
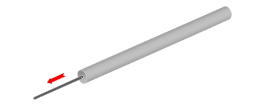
شکل 1-4-43 استخراج سیم (Forecreu، فرانسه)
-
تمیزکاری و کنترل های ابعادی
هنگامی که کنترل های ابعادی و تمیزکاری انجام می شود، میله های کانوله شده از هر گونه آلودگی زدوده می شوند. ترکیبی از روش های تشخیص تصویر برای موقعیت یابی سوراخ، تست اولتراسونیک یا جریان گردابی NDT و همچنین بازرسی فایبرسکوپ انجام می شود (شکل 1-4-44).
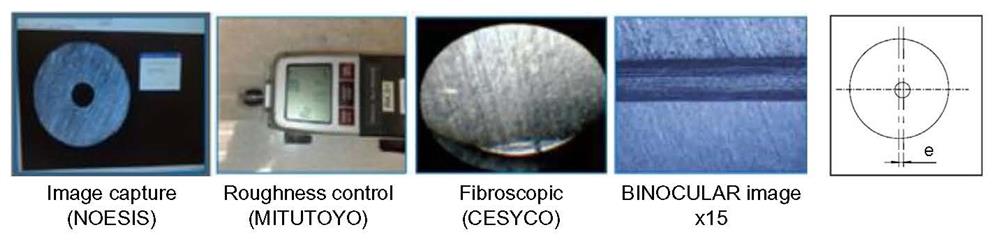
شکل 1-4-44 بازرسی و کنترل کردن (Forecreu، فرانسه).
جریان Eddy: برای ارزیابی ترک های عرضی.
تست اولتراسونیک ممکن است (شکل 1-4-45):
-
برای کنترل عمق عیوب در ID.
-
با عمق A1 در 1.2 میلیمتری از سوراخ پایین سطح صاف.
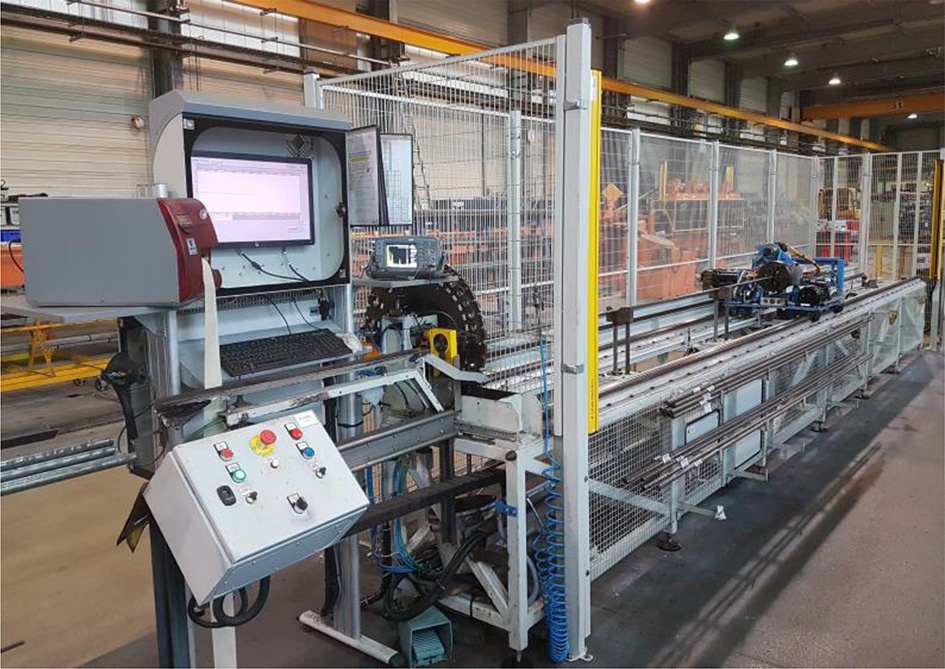
شکل 1-4-45 ماشین تست اولتراسونیک (Forecreu، فرانسه)
مشخصات میکروگرافی و (شکلهای 1-4-46 تا 1-4-48):
-
عاری از آخالهای قابل رؤیت با اندازه میکرو ( 200).
-
با توجه به تصاویر مرجع ETTC2 A1-A9، ساختار هم محور α+β .
-
عاری از فاز α (سطح سوراخ و OD).
-
عاری از شبکه α یا پلاکتهای α.
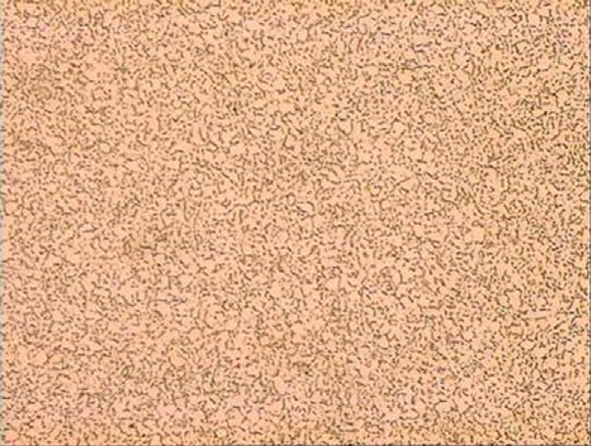
شکل 1-4-46 Ti 6–4 Eli، بزرگنمایی 200 (Forecreu، فرانسه)
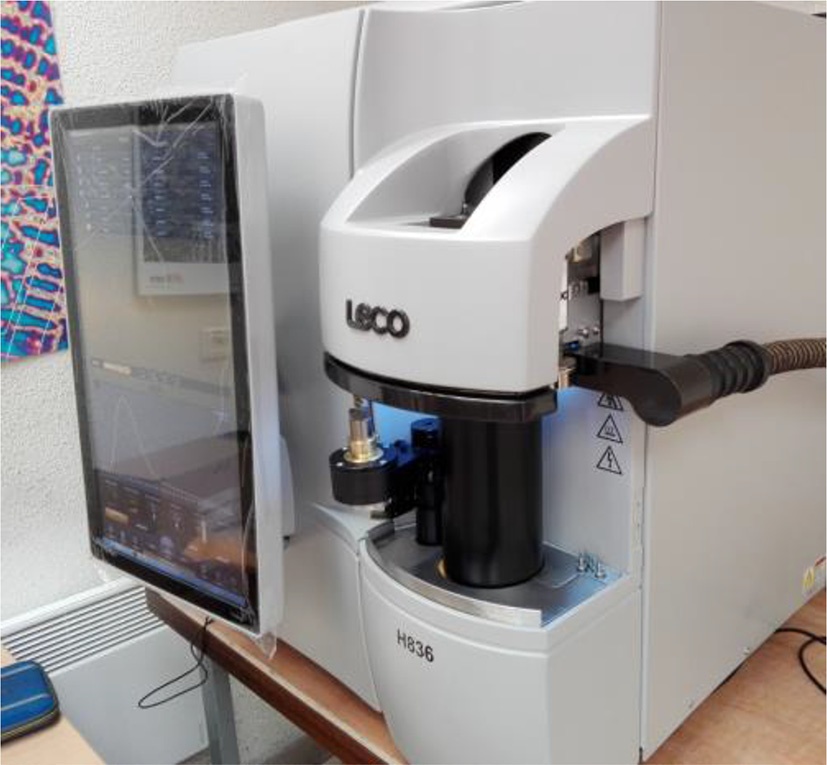
شکل 1-4-47 تجهیزات آنالیز هیدروژن (Forecreu، فرانسه)
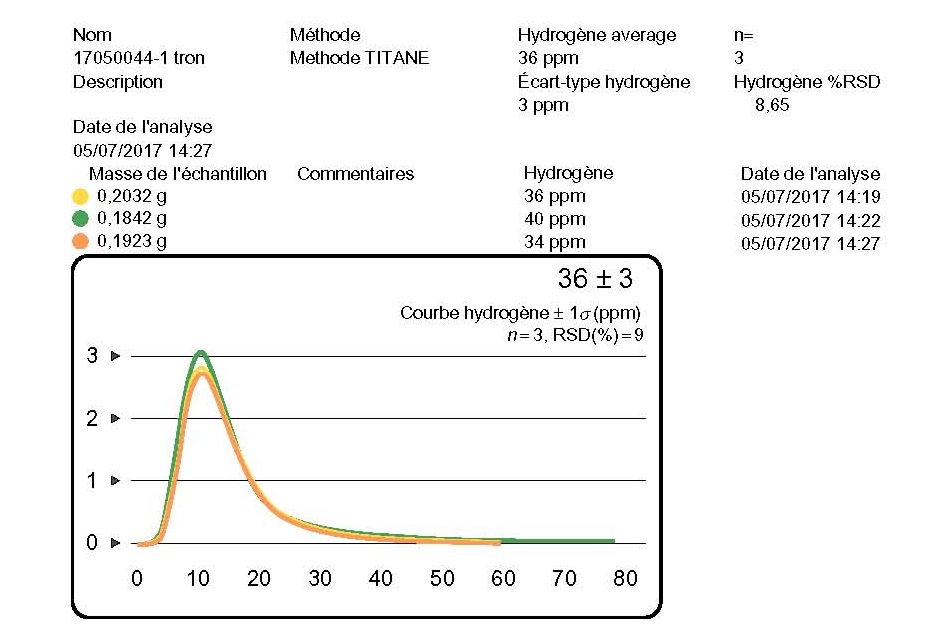
شکل 1-4-48 گزارش آنالیز هیدروژن (Forecreu، فرانسه)
آزمون های مکانیکی طبق ASTM E8/E8M مطابق با مشخصات مرجع (ASTM و ISO) انجام می شوند.
استحکام کششی، استحکام تسلیم، کشیدگی و کاهش سطح برای هر گروهی در آزمایشگاه با دستگاه تست KN 200 آزمایش شد. منحنی تست معمولی به شرح زیر است (شکلهای 1-4-49 تا 1-4-52):
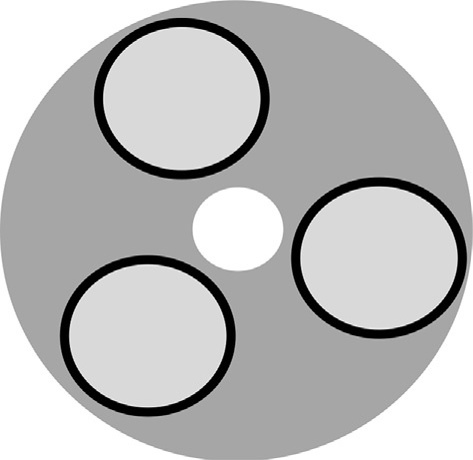
شکل 1-4-49 طرح نمادین برای تولید نمونه (Forecreu، فرانسه).
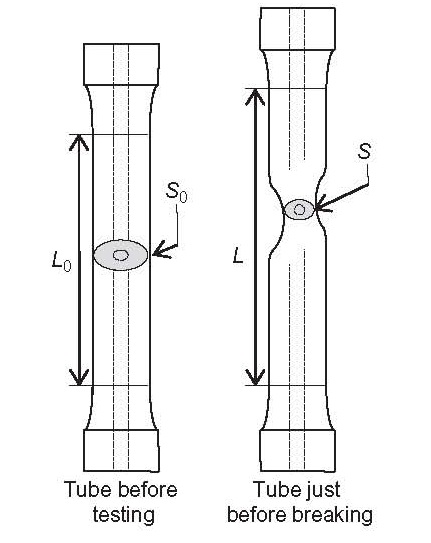
شکل 1-4-50 تست لوله (Forecreu، فرانسه)
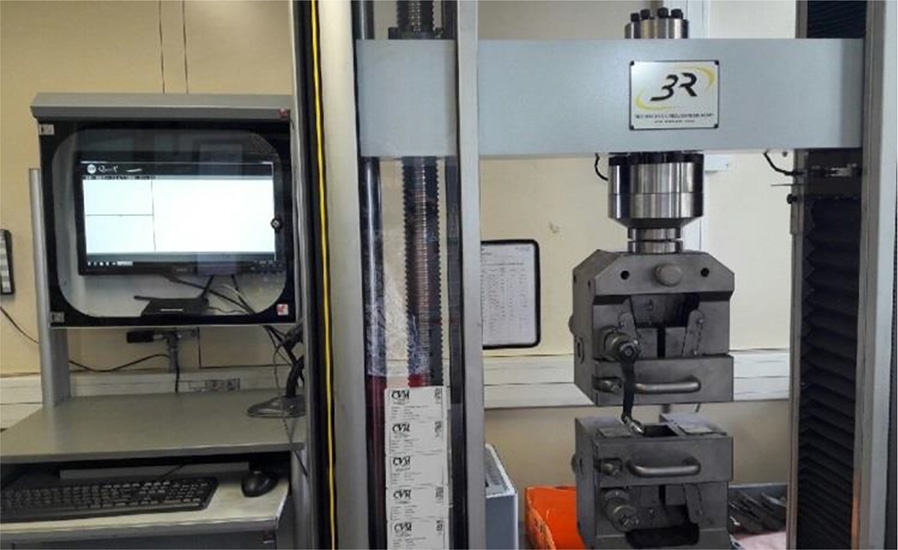
شکل 1-4-51 تجهیزات تست کشش (Forecreu، فرانسه)
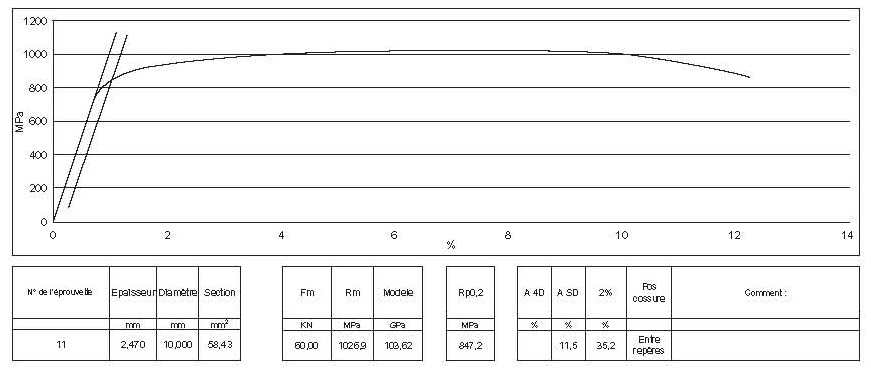
شکل 1-4-52 نوعی منحنی UTS، YS، A% از Ti 6–4 Eli با استاندارد ASTM F136، ISO 5832-3 (Forecreu، فرانسه)
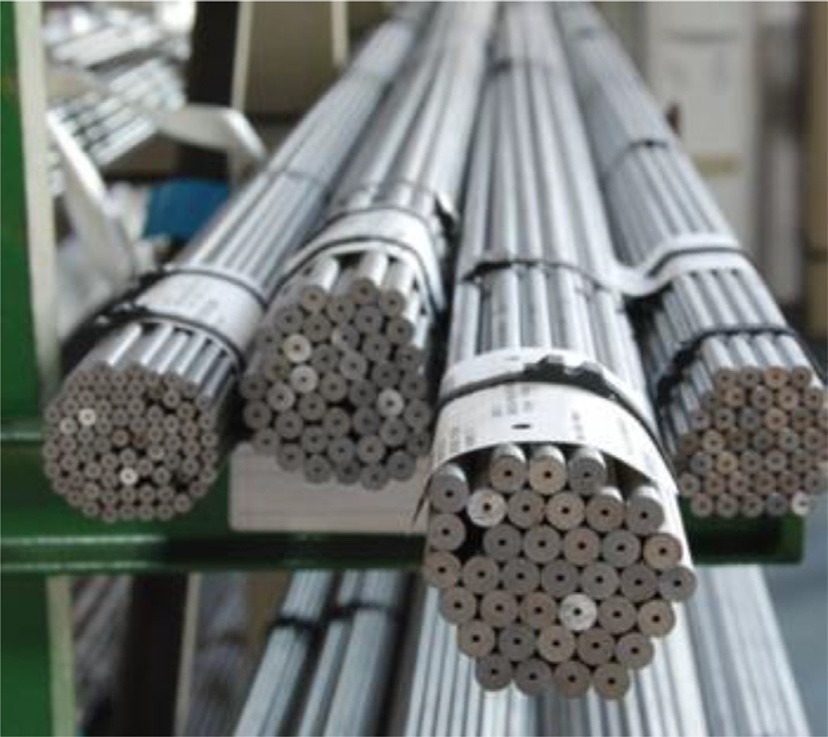
شکل 1-4-53 میله های کانوله شده(محصول نهایی) (Forecreu، فرانسه)
خلاصه
این فصل جنبه های بسیار زیادی از تولید میله های تیتانیومی و فرآیندهای زیر از جمله: ریخته گری، فورجینگ و تولید مواد افزودنی در فناوری های ماشینکاری را پوشش می دهد. روش بسیار خاص برای ترمیم شکستگی، استفاده از میله های کانوله شده می باشد. تسلط به کل فرآیند نیاز به تخصص متالورژیکی دارد، زیرا کامپوزیت فلزی از بیلت تا میله نهایی به طور دائم از ویژگیهای متنوع خواص آلیاژ استفاده می کند. طی عملیات چندین روش فورجینگ استفاده می شود، به لطف روانکاری با شیشه، اکسترود محوری و هیدرواستاتیک می تواند اتفاق بیافتد، به دنبال آن یک نورد گرم محوری مثلثی و سپس یک کشش محوری و در نهایت محصول نهایی به دست می آید (شکل 1-4-53).