ریخته گری به سادگی روشهای دیگر برای تولید تیتانیوم به شکل های مختلف است. این روش را می توان یک روش با شکل نزدیک به نهایی (NNS) درنظر گرفت هرچند نسبت به متالورژی پودر از قابلیت کمتری برای این موضوع برخوردار است. قطعات ریختگی تیتانیوم در حال حاضر بطور گسترده ای در صنعت هوافضا استفاده می شوند و در مقیاسی کمتر اما روبه افزایش، در فرایندهای شیمیایی، دریایی، زیست پزشکی، اتوموبیل و دیگر صنایع بکار می روند. شکل 6-1 یک قطعه ریخته گری شده برای هواپیما از جنس Ti-6Al-2Sn-2Zr-2Mo-2Cr+Si و شکل 6-2 قطعات ریختگی تیتانیومی کوچکتر برای استفاده در محیط خورنده را نشان می دهد.
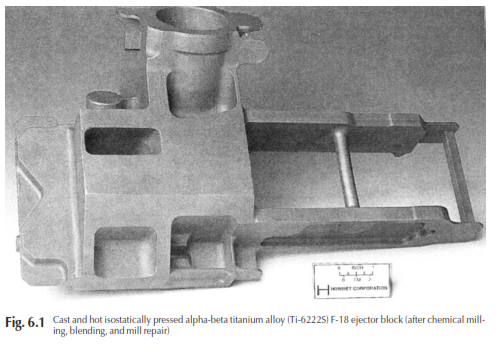
شکل 6-1 بلوک بیرون انداز F-18 ساخته شده از آلیاژ تیتانیومی ریخته گری شده و پرسکاری شده ایزواستاتیک داغ (Ti-6222S)
( پس از فراوری شیمیایی، مخلوط سازی و ترمیم).
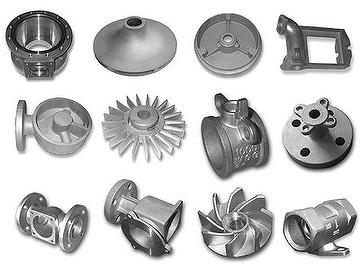
شکل 6-2 قطعات تیتانیومی تولید شده به روش ریخته گری دقیق برای استفاده در محیط های خورنده
برای مدتی در دهه 1990، ابزارهای ورزشی بویژه سر چوب گلف تولید شده به روش ریخته گری دقیق، دومین حوزه کاربردی پیشرو (بعد از صنعت تجاری هوافضا) برای تیتانیوم بودند. اما قطعات ریختگی تیتانیوم سهم کوچکی از صنعت تیتانیوم یعنی فقط چند درصد کل وزن محصولات بارگیری شده در هرسال را تشکیل می دهند.
آلیاژهای بکار رفته برای ریخته گری
هرچند تعدادی از آلیاژهای مختلف تیتانیوم در ابتدا بررسی شدند تلاشها روی آلیاژهایی نظیر Ti-5Al-2/5Sn پس از چند سال کاهش یافت و محققان روی Ti-6Al-4V تمرکز کردند. نتایج این پژوهشگران این ایده را که قطعات ریختگی تیتانیوم را می توان با سطوح استحکام و مشخصاتی نزدیک به آلیاژهای کارشده متداول ساخت تقویت کرد. متعاقبا قطعات بیشتری از تیتانیوم خالص و آلیاژهای آلفا- بتا و بتا تولید شده اند.
در کاربردهای ریخته گری، تیتانیوم خالص (CP) (نظیر گریدهای ASTM 1، 2 یا 3) برای کاربردهای زیادی مربوط به خوردگی فلز بکار می روند. Ti-6Al-4V آلیاژ غالب برای کاربردهای هوافضا و دریایی است. با افزایش مصرف، Ti-6Al-2Sn-4Zr-2Mo-Si برای کاربرد در دمای بالا درحال انتخاب شدن است. قطعات ریختگی همچنین از آلیاژهای Ti-5Al-2/5Sn، Ti-15V-3Cr-3Sn-3Al، Ti-8Al-1Mo-1V، Ti-6Al-2Sn-2Zr-2Mo-2Cr+Si و Ti-6Al-6V-2Sn و نیز چند آلیاژ اروپایی تامین شده اند. نزدیک به 90 درصد قطعات ریختگی تولیدشده از آلیاژ Ti-6Al-4V هستند اما عمده 10 درصد مابقی، از تیتانیوم CP است.
هیچ آلیاژ تجاری تیتانیومی ای وجود ندارد که بطور خاص برای کاربردهای ریخته گری تولید شده باشد. همه قطعات ریختگی تیتانیومی دارای ترکیبات شیمیایی ای بر مبنای آلیاژهای کارشده مرسوم هستند. این شرایط غیرعادی است زیرا آلیاژهای موجود در سیستمهای فلزی غالبا بعنوان آلیاژهای ریختگی و برای غلبه بر مشکلاتی نظیر قابلیت ریخته گری ضعیف در ترکیب شیمیایی یک آلیاژ کارشده ایجاد شده اند. هیچ مشکل نامرسومی در رابطه با قابلیت ریخته گری یا سیالیت در هیچیک از فلزهای تیتانیوم ریخته گریشده تا امروز مشاهده نشده است.
مزایای قابلیت ریخته گری تیتانیوم و آلیاژهای تیتانیوم
در نتیجه توسعه فرایندهای ریخته گری توسط ریخته گران و تولیدکنندگان موتور توربین گازی، نشان داده شد قطعات ریختگی تیتانیومی جایگزین های قابل اتکایی برای آلیاژهای کارشده هستند. پس از آن، قطعات ریختگی تیتانیومی شامل قطعات بزرگتر در صنعت بدنه هواپیما و قطعات کوچکتر در حوزه هایی نظیر زیست پزشکی، سخت افزارهای دریایی، ابزارهای ورزشی و صنایع فراوری شیمیایی گردید. مزایای قطعات ریختگی تیتانیومی بر تیتانیوم کارشده مرسوم عبارتند از :
-
صرفه جویی در هزینه
-
زمان کمتر برای تحویل قطعه
-
قابلیت تولید شکلهای پیچیده نزدیک به شکل نهایی
-
قابلیت استفاده از پیش نمونه سازی سریع برای تولید قطعات آزمایشی بصورت ارزانقیمت (در مقایسه با استفاده از فورج کاری در قالب، ماشینکاری و اتصال دهی)
مزیت هزینه ای از طریق انعطاف پذیری بیشتر در طراحی، استفاده بهتر از فلز در دسترس یا کاهش هزینه ماشینکاری یا شکل دهی قطعات ممکن است حاصل شود. بطور کلی، هرچه قطعه پیچیده تر باشد، استفاده از ریخته گری اقتصادی تر می شود. ادعا شده است که نمونه سازی سریع اولیه با استفاده از مدلسازی کامپیوتری، بیش از 50 درصد از زمان تولید یک قطعه ریختگی پیچیده مربوط به بالگرد کم کرده است. بعلاوه، در مقایسه با طراحی آلیاژ تیتانیوم فورج شده، قطعه ریختگی نهایی با 63 درصد کاهش ماشینکاری و زمان سرهم بندی و کاهش هم زمان در وزن تولید شد.
برخلاف قطعات ریختگی بسیاری از فلزات دیگر، قطعات ریختگی تیتانیومی دارای استحکامی معادل یا تقریبا معادل با همتایان کارشده خود هستند. تضمین استحکام برای قطعات ریختگی تیتانیوم با قطعات کارشده یکسان است. داکتیلیته های محصولات ریختگی که توسط ازدیاد طول و کاهش سطح اندازه گیری می شود کمتر از مقادیر متداول برای محصولات کارشده همان آلیاژها می باشند. اما چقرمگی شکست و مقاومت در برابر گسترش ترک می تواند برابر با یا بیشتر از مقادیر مربوط به ماده کارشده متناظر باشد. هرچند استحکام خستگی تیتانیوم ریختگی کمتر از تیتانیوم کارشده است اما استحکام خستگی تیتانیوم ریختگی را می توان با فراوری ویژه و عملیات حرارتی ارتقاء داد.
تکنولوژی ریخته گری
قطعات ریختگی تیتانیوم در قالبهای گرافیتی ماشینکاری شده، قالبهای گرافیتی تیرکوب و ریخته گری دقیق ریخته گری شده اند. تکنولوژی اصلی ای که باعث ازدیاد قطعات ریختگی در بازار صنعت هوافضا شد روش ریخته گری دقیق ترکیب شده با HIP برای بیشتر قطعات ریختگی حساس بود.
پیچیدگی محسوس طراحی، تلرانس و کنترل پرداخت سطحی حاصل شده و قطعات بزرگ با قطر نزدیک به m 1.5 (ft 5) را می توان ریخته گری کرد. قطعات ریختگی بطور کلی توسط بازذوب قوسی در خلا تیتانیوم در یک بوته مسی آبگرد و ریختن درون قالب تولید می شوند. اگر بتوان سرمایه گذاری اولیه را توجیه کرد، فرایندهای ذوب دهانه ای ممکن است در آینده کاربردی برای بازذوب آلیاژ پیش از ریخته گری پیدا کنند.
چالشهای ریخته گری. سیستمهای قالب ریختگی حتما باید نسبت به تیتانیوم مذاب نسبتا خنثی باشند. سیستمهای انحصاری دارای پوسته سرامیکی و موم از بین رونده توسط شرکتهای ریخته گری مختلف درگیر در ریخته گری تیتانیوم توسعه یافتند. معمولا پوششهای سطحی از پوسته های سرامیکی با پوشش های انحصاری ساخته شده و سیستم های دیرگداز متداول برای افزودن به استحکام پوسته بکار می روند. بدون توجه به نوع قالب (یعنی دقیق یا تیرکوب)، عملیات ریخته گری بر روشهایی برای کنترل گستره واکنش آلیاژ مذاب و قالب و نفوذ بعدی محصولات واکنش از سطح قطعه ریختگی به سمت داخل متمرکز می شود. عمق سطح آلودگی می تواند از صفر در مقاطع بسیار نازک تا بیش از mm 1.5 (in. 0.06) در مقاطع سنگین متغیر باشد. در سازه های هوافضایی حساس، پوسته ترد آلفا توسط حکاکی شیمیایی از بین می رود.
عمق سطح آلودگی را باید در طراحی الگوی مومی اولیه برای ریخته گری دقیق در نظر گرفت. الگوی مومی و قطعه ریختگی حاصل اندکی بزرگتر از اندازه ساخته می شوند و ابعاد نهایی با حکاکی شیمیایی دقیق بدست می آیند. دمای ریختن مذاب، دمای قالب، نیروی ریخته گری (اگر بطور گریز از مرکز ریخته گری شود) و ضریب رسانایی گرمایی فلز و قالب و نیز محیط تبرید، همگی عواملی هستند که در تولید یک قطعه تیتانیومی با ریخته گری دقیق سهیم هستند.
فرآیندهای ریخته گری. فلز مذاب حاصل پس از بازذوب، درون یک قالب دقیق یا یک قالب گرافیتی تیرکوب ریخته می شود. روشهای ساخت الگو و قالب ریخته گری دقیق مشابه با روش های بکار رفته در مورد تکنولوژی سوپرآلیاژها می باشد. هرچند قالبهای گرافیتی تیرکوب با قالبهای دقیق متفاوت هستند اما مشابه با قالبهای ماسه ای متداول هستند. ماهیچه ها برای قطعات توخالی بکار می روند. تخلخل همچنان یک مسئله بالقوه است اما با استفاده از HIP چنانکه متعاقبا توضیح داده خواهد شد میتوان آن را حل کرد.
هنگامی که مسئله واکنش قالب-فلز مطرح می شود، مهمترین مسئله مربوط به قطعات ریختگی تیتانیومی و آلیاژ تیتانیومی دستیابی به سطوح کافی فوق گدازش در فلز مذاب برای بیشینه سازی ویژگی های سیلان فلز و پرکنندگی قالب توسط فلز است. در بسیاری از موارد، یک جدول گریز از مرکزی یا پیش گرمایش قالب (یا هردو) برای اطمیان از مناسب بودن پرشدن قالب بکار می رود. طرح واره ساده شده از یک نوع فرایند ریخته گری تیتانیوم در شکل 6-3 نشان داده شده است.
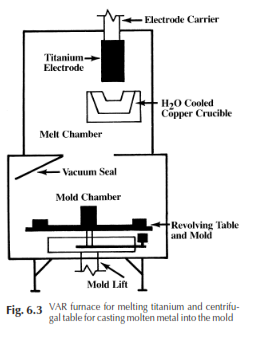
شکل 6-3 کوره VAR مربوط به ذوب تیتانیوم و میز گریز از مرکزی مربوط به ریخته گری فلز مذاب درون قالب
یک مشکل محسوس مربوط به قطعات ریختگی تیتانیومی بزرگ، مسئله تخلخل است. اما با استفاده از HIP، عدم نقص درونی قطعات ریختگی تیتانیومی را می توان تا نقطه ای بهبود داد که هیچ تخلخل یا جای خالی کوچکی را نتوان شناسایی کرد. جوشکاری ترمیمی برای بستن نقایص درشت پس از HIP بکار می رود.
چون با افزایش سطح اکسیژن، استحکام افزایش و داکتیلیته (چقرمگی) کاهش می یابد، مقدار اکسیژن با درنظرگرفتن آلیاژ تیتانیوم از اهمیت برخوردار است. کنترل سطح اکسیژن در قطعات ریختگی غالبا با انتخاب شمش برای ایجاد مذاب حاصل می شود اما مذاب دهانه ای می تواند بهبود بیشتری ایجاد کند. شمشی با یک مقدار کم اکسیژن معمولا منجر به یک قطعه ریختگی با کمترین مقدار اکسیژن می شود. نقش دقیق برگشتی در کنترل مقدار اکسیژن و در جدایش عنصر آلیاژی واضح نیست اما هم برگشتی و هم شمش های استفاده نشده بکار می روند. اکسیژن نیز از برهم کنش سطحی فلز- قالب می تواند در قطعه ریختگی وارد شود.
روش قالب گرافیتی تیرکوب قدیمی ترین روش بکار رفته برای تولید قطعات ریختگی تیتانیومی است. این روش از مخلوط پودر گرفیت، چسبهای مناسب و آب استفاده می کند که برای تشکیل بخشی از قالب، در مقابل یک الگو کوبیده می شوند. قسمت های مجزای قالب سپس پخته شده و برای ریخته گری سرهم بندی می شوند. شکل 6-4، برخی قطعات تیتانیومی تولیدشده توسط فرایند قالب گرافیتی تیرکوب را نشان می دهد.
بیشتر کاربردهای قطعه ریختگی آلیاژ تیتانیوم با عملکرد عالی به روش ریخته گری دقیق بستگی دارد. در اینجا یک الگوی مومی تولید شده و در یک پوسته سرامیکی گذاشته می شود. پس از تکمیل قالب و موم زدایی، قالب پخته شده و سپس برای ریخته گری آماده می شود. برای قطعات کوچک، چند الگو در یک سیستم تغذیه مشابه برای ایجاد قطعات بسیار در یک زمان واحد بکار می روند. این روش می تواند برای کاربردهای زیست پزشکی ایده آل باشد (شکل 6-5 برخی ایمپلنت های ریخته گری شده دقیق از آلیاژهای تیتانیوم را نشان می دهد) اما برای قطعات بزرگ بکار رفته در حوزه هوافضا قابل اجرا نیست.
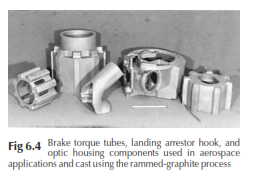
شکل 6-4 لوله های گشتاوری ترمز، قلاب متوقف کننده فرود و قطعات نوری بکار رفته در کاربردهای هوافضایی با استفاده از ریخته گری و فرایند گرافیت- تیرکوب.
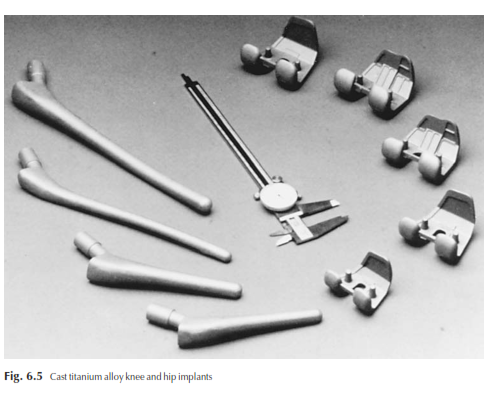
شکل 6-5 ایمپلنت های زانو و استخوان ران از آلیاژ تیتانیوم ریخته گری شده
ملاحظات طراحی
دستورالعمل های زیادی هستند که در طراحی قطعات ریختگی تیتانیومی باید دنبال شوند:
-
تامین کننده و خریدار برای شناخت خواص مطلوب و تعریف شکل مورد نظر باید با هم همکاری کنند.
-
طراحی باید این اطمینان را ایجاد کند که قالب تا حد امکان بطور کامل پر می شود. ( اگر لازم باشد، جوشکاری ترمیمی باید تا حد امکان محدود به نواحی غیرحساس شود.)
-
از پیچیده سازی غیرضروری باید اجتناب شود.
-
قطعه ریختگی برای انتقال های ملایم بین نواحی ضخیم و نازک برای دارا بودن شعاع ها و گوشه های پهناور و برای داشتن مقاطع با دیواره نازک و نازک شونده تدریجی که موجب چگالی بیشینه (یعنی تخلخل انقباضی کمینه) می شوند باید بطور مناسبی طراحی شوند.
-
اگر HIP پساریخته گری برای برآورده سازی الزامات خواص مکانیکی لازم باشد ظرفیت قطری بیشینه واحدهای HIP را باید در نظرگرفت.
اثر جوشکاری ترمیمی
با درنظرگیری دشواری های موجود در پرشدن قالبها در حین ریخته گری تیتانیوم، واضح است که جوشکاری ترمیمی یک مرحله جدایی ناپذیر در فرایند تولید برای قطعات ریختگی تیتانیومی است. جوشکاری ترمیمی برای ترمیم نقایص مربوط به سطح بکار می رود. HIP برای ترمیم نقایص غیرسطحی استفاده می شود. جوشکاری ترمیمی قطعات ریختگی تیتانیومی را باید بدقت اجرا کرد زیرا بدلیل انباشت اکسیژن، هیدروژن و دیگر آلاینده ها در حین جوشکاری، تیتانیوم می تواند ترد شود. جوشکاری قوس با الکترود تنگستن تحت پوشش گاز(GTAW) با میله های آلیاژی پرکننده برای پرکردن حفرات و شانتهای سرد نظیر تورفتگی های سطحی ناشی از HIP یا حفرات متصل به سطحی بکار می رود که در طول چرخه HIP بسته نمی شوند. این میله های پرکننده ممکن است بین نشین فرااندک (ELI) یا بین نشین معمولی برای جلوگیری از انباشت بیش از حد اکسیژن در فلز جوش باشند. هنگامی که عملیات مناسبی بکار رود رسوبات با کیفیت بالایی از جوش معمولا حاصل می شوند. بطور کلی، همه قطعات ریختگی نیازمند به جوشکاری ترمیمی، پس از جوشکاری تحت عملیات آنیل کاری آزادسازی تنش قرار می گیرند.
به دلیل تفاوتهای میکروساختاری ناشی از نرخ تبربد سریع در فرایند جوشکاری و مقدار انباشت اکسیژن، رسوبات جوش می توانند استحکامی بالاتر از فلز اصلی داشته باشند. این تفاوتها را می توان توسط یک عملیات حرارتی دما بالای پسا جوشکاری حذف کرد اما عملیات حرارتی آزادسازی تنش یا آنیل کاری، عملیات استاندارد پس از جوشکاری ترمیمی است.
جوشکاری ترمیمی بدرستی اجراشده، مقاومت به خستگی تیتانیوم ریختگی را تخریب نمی کند. همچنین مطالعات نشان داده اند که جوشکاری چندان بر خواص خزشی Ti-6Al-4V ریختگی تاثیر نمی گذارد و نتایج مشابهی را می توان برای دیگر آلیاژهای تیتانیوم تصور کرد. زمانهای گسیختگی برای میله های جوشکاری شده و جوشکاری نشده Ti-6Al-4V در °C 315 (°F 600) و در °C 650 (°F 1200) مشابه هم بودند. نرخهای کرنش در 2 درصد کرنش خزشی و °C 650 (°F 1200) برای میله های جوشکاری شده و جوشکاری نشده یکسان بودند.
پرسکاری ایزواستاتیک گرم
به منظور تف جوشی موثر جای خالی های غیرمتصل به سطح در قطعات ریختگی پشت به هم، HIP که در واقع کاربرد یک فشار ایزواستاتیک است برای عمل آوری قطعات ریختگی تیتانیومی بکار می رود. این فرایند در دمایی مشخص در یک محیط غیرواکنشی نظیر آرگون اجرا می شود. استحکام خستگی یک ویژگی ضروری برای کاربردهای مرسوم تیتانیوم آلیاژی است. HIP منجر به بهبود محسوس استحکام خستگی آلیاژهای تیتانیوم ریختگی توسط کاهش زیاد تخلخل می شود.
پرسکاری ایزواستاتیک داغ قطعات ریختگی تیتانیوم غیرآلیاژی، در اواخر دهه 1970 تبدیل به یک واقعیت تولید شد. هرچند به نظر می رسد HIP در °C 960 (°F 1750) باعث ایجاد خواصی عالی برای کاربردهای Ti-6Al-4V شود اما فرایند HIP که به یک استاندارد صنعتی تبدیل شده است به مدت 2 ساعت در °C 900 (°F 1650) در محیط آرگون با فشار MPa 105 (ksi 15) انجام شده است. معیارهای مربوط به HIP در °C 960 (°F 1750) در حال جایگزینی با HIP در °C 900 (°F 1650) می باشند.
در ابتدا، HIP با نتایجی فوق العاده برای مصرف دوباره قطعاتی که پس از بازرسی رادیوگرافی رد شده بودند مورد استفاده قرار گرفت. کارآمدی این روش باعث ایجاد برنامه برای استفاده از HIP برای قطعات معمولی شد اما هزینه بالا باعث شد این برنامه مورد تردید قرار بگیرد. اما برای برخی قطعات ریختگی تیتانیومی، تغذیه کافی با استفاده از تغذیه گذاری معمولی واقعا غیرممکن است. در نتیجه، برای حصول بیشینه بی عیبی محصول و بهترین خواص مکانیکی، تقریبا همه قطعات ریختگی هوافضایی تحت پرسکاری ایزواستاتیک داغ قرار می گیرند. HIP موجب می شود قطعات ریختگی، استانداردهای بازرسی غیرمخرب (NDT) را برآورده نمایند. عیوب واضحی نظیر انقباض، توسط جوشکاری از بین می روند. HIP به ابزاری برای جلوگیری یا دست کم کمینه سازی جوشکاری ترمیمی در بسیاری از موارد تبدیل شده و باعث اطمینان بیشتر از برآورده سازی الزامات مشخص شده می شود.
عملیات حرارتی
از دیدگاه فنی، HIP یک عملیات حرارتی است هرچند برخی مطالعات ادعا کرده اند که HIP تاثیر کمی بر ارتقای خواص مکانیکی قطعات ریختگی Ti-6Al-4V دارد. خواص آلیاژهای HIP شده تابعی از دمای HIP نسبت به دمای تحول بتا و عملیات حرارتی پسا HIP می باشند. در قطعات ریختگی با کیفیت کم تا استاندارد، HIP حد پائینی برای پراکندگی داده ها ایجاد کرده و میزان اطمینان به محصولات ریختگی را افزایش می دهد. همانطور که در بالا اشاره شد، یک چرخه HIP دمابالا می تواند منجر به خواص بهتر شود اما ملاحظات عملی برای عملیات تولید منجر به استفاده از چرخه هایی نزدیک به دمای تحول بتا می شود.
پس از ریخته گری و پیش از پرسکاری ایزواستاتیک گرم، یک مرحله آزادسازی تنش ممکن است اعمال شود. اما چون HIP یک عملیات حرارتی است و معمولا بدنبال آن یک عملیات انحلالی دمابالا یا در دمایی بالاتر از دمای HIP انجام می شود، آزادسازی تنش ممکن است دارای هیچ اثر محسوسی بر خواص مکانیکی نهایی قطعات ریختگی تیتانیومی HIP شده نباشد. عملیات حرارتی پس از HIP معمولا بدلیل نرخ تبرید آهسته از دمای HIP ، معمولا لازم است. عملیات بازگرمایش برای اصلاح ساختار قطعه HIP ضروری است. دمای عملیات حرارتی نزدیک به دمای تحول بتا (عملیات حرارتی انحلال بتا) و شاید بالاتر از آن باشد.
یک عملیات حرارتی مربوط به Ti-6Al-4V، از انحلال بتا (در خلا) در °C 25±1038 (°F 25±1900) بمدت 2 تا 3 ساعت بعلاوه کوئنچ در روغن تشکیل می شود. بدنبال آن، فراپیرسازی در خلا در °C 14±704 (°F25±1300) بمدت 2.5 تا 3 ساعت و تبرید در کوره در آرگون تا دمای اتاق انجام می شود. کل فرایند عملیات انحلال بتا/فراپیرسازی (beta-STOA) نامیده می شود. یک عملیات حرارتی متداولتر برای قطعات ریختگی Ti-6Al-4V، انحلال آلفا-بتا در °C 954 (°F 1750) بمدت 1 ساعت است. سپس قطعه ریختگی توسط پنکه و در یک گاز خنثی خنک می شود. سپس در °C 621 (°F 1150) بمدت 2 ساعت پیرسازی می شود.
اگرچه بسیاری از قطعات ریختگی تیتانیومی تولید شده بصورت تجاری در شرایط آنیل شده ارائه می شوند اما استفاده از عملیات انحلالی برای اصلاح ساختار و بهبود خواص می توانند بطور محسوسی بر قابلیت استفاده از تیتانیوم ریختگی اثر بگذارد. بیشتر فرایندهای عملیات حرارتی برای قطعات ریختگی تیتانیومی را می توان بطور برابر برای قطعات تیتانیومی متالورژی پودر استفاده کرد. (متالورژی پودر در فصل 7 توضیح داده می شود.) هدف اصلی، حذف فاز آلفای مرزدانه ای، کلونی های صفحه ای درشت آلفا، صفحات مجزای آلفا برای ایجاد یک ساختار ظریف تر و یکنواختی بیشتر در خواص حاصل و افزایش کلی در استحکام است. این مورد را می توان با عملیات های انحلالی یا با آلیاژسازی موقتی قطعه ریختگی با هیدروژن انجام داد. جزئیات روش های امتحان شده و حوزه های کاربرد آنها در جدول 6-1 ارائه شده اند. نتایج عملیات انحلالی آلفا-بتا (ABST)، عملیات انحلالی بتا (BST)، ساختار شکستهشده (BUS) و هیدروژن زدایی دمابالا (HTH) عبارتند از حذف کلونی های صفحه ای درشت آلفا و فاز آلفای مرزدانه ای. بنابراین، بهبود محسوس در خواص کششی و خستگی حاصل می شود.
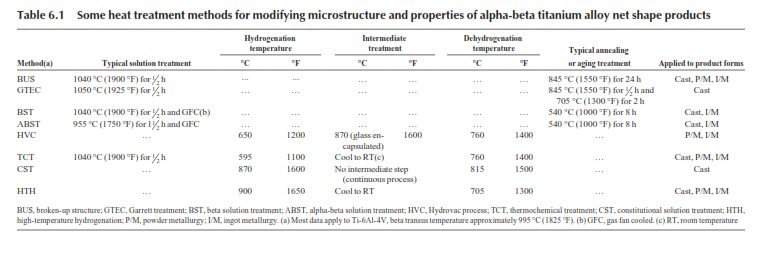
جدول 6-1 برخی روشهای عملیات حرارتی برای اصلاح ریزساختار و خواص محصولات با شکل نهایی از تیتانیوم آلیاژی آلفا- بتا
عملیات حرارتی آزادسازی تنش در پائین تر از دمای HIP مورد نظر و معمولا در دامنه °C 704 تا 843 (°F 1550-1300) بمدت 2 ساعت انجام می شود. این نوع عملیات اثر محسوسی بر ساختار ریختگی ندارد هرچند این دامنه دمایی بر ساختار کارشده تاثیر می گذارد. به منظور کمینه سازی اکسیداسیون، این عملیات در خلا یا تحت اتمسفر خنثی انجام می شود. برخی از قطعات ریختگی بزرگ بقدری آهسته سرد می شوند که نیازی به آزادسازی تنش ندارند.
کاربردهای تیتانیوم ریختگی
قطعات ریختگی تیتانیومی اکنون بطور گسترده ای در صنعت هوافضا و به مقدار کمتر در صنایع شیمیایی، دریایی، زیست پزشکی، ابزارهای ورزشی و دیگر صنایع استفاده می شوند. کاربردهای هوافضایی شامل قطعات عمده سازه ای با وزن بیش از kg 61 (lb 135) برای هرکدام و کلیدهای کوچک با وزن کمتر از g 30 (oz 1) برای هریک می شود. قطعات ریختگی تیتانیومی برای شاتل فضایی در بالها، قطعات موتور، اجزای ترمز، حسگرهای نوری، اردنانس و دیگر اجزای مربوط به هواپیمای نظامی و موشکها و در موتورهای توربین گازی و اجزای ترمز برای هواپیمای تجاری مسافربری به کار برده می شوند. کاربردهای بیشتر هوافضایی شامل توپی روتور برای بالگردها و فلپ ترکها برای جنگنده ها می شود.
در صنعت شیمیایی، اجزای مربوط به پمپ ها، سوپاپ ها و کمپرسورها از تیتانیوم ریختگی ساخته می شوند.کاربردهای دریایی شامل ایجادکننده های جت آب برای پیشرانش هیدروفویل و گوی های دریچه ای آب دریا مربوط به زیردریایی های هسته ای می گردد. قطعات ریختگی تیتانیوم در دیگر کاربردهای صنعتی نظیر سخت افزارهای واردشونده به درون چاه برای صنعت نفت، قطعات خاص خودرو، سخت افزارهایی در عرشه کشتی و ایمپلنت های پزشکی نیز بکار می روند. قطعات ریختگی تیتانیومی نیز برای سر چوب گلف و قطعات سبک دوچرخه بکار رفته اند.
ارزیابی بیشتری از برخی شکل های پیچیده موجود در آلیاژهای تیتانیومی تولید شده توسط ریخته گری بعلاوهHIP را می توان با مطالعه شکل 6-6 بدست آورد.
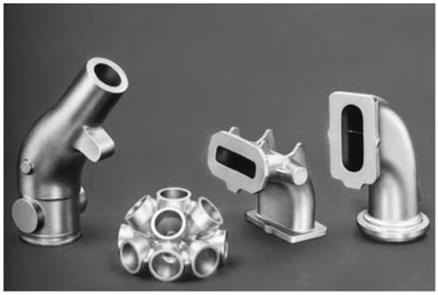
شکل 6-6 شکل های پیچیده ریخته شده از آلیاژهای تیتانیوم
مقایسه قیمت
یک تولیدکننده عمده هواپیما مطالعه عمیفی انجام داد که در آن هزینه های قطعات ریختگی تیتانیوم آلیاژی با هزینه های ضایعات ماشینکاری شده از قطعات فورج شده و بلوک های تیتانیوم و آلومینیوم مقایسه گردید. بطور متوسط، هزینه ماشینکاری حدود 60 درصد هزینه کلی تولید یک هواپیما را تشکیل می دهد. استفاده از قطعات ریختگی تولیدی به روش ریخته گری دقیق، هزینه ماشینکاری را تا 5 درصد قیمت کلی قطعه در مقایسه با 70 تا 80 درصد مربوط به همان قطعه که با فورجکاری ساخته شده یا از یک بلوک استخراج شده، کاهش می دهد.
شکل 6-7 نسبت قیمت به تعداد واحدهای تولیدی برای یک طراحی مشخص از قطعه ای در هواپیما را نشان می دهد. برای همه مقادیر، کم هزینه ترین روش برای تولید این قطعه از طریق ریخته گری دقیق است. برای یک مجموعه 16 قطعه ای از یک مدل مربوط به هواپیمای تجاری، هنگامی که 200 واحد از بلوک تیتانیوم آلیاژی استخراج شدند قیمت متوسط یک قطعه 749 دلار بود. قیمت متوسط برای قطعات ریخته گری دقیق شده در همان مقدار تولید 227 دلار بود. این به معنای 835100 دلار صرفه جویی برای ساخت 100 هواپیماست اگر قطعات از طریق ریخته گری تولید شوند.
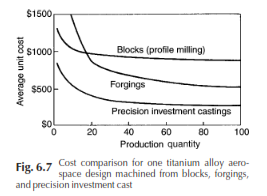
شکل 6-7 مقایسه قیمتی مربوط به یک قطعه آلیاژی تیانیومی ماشینکاری شده از بلوک، قطعات فورج شده و ریخته گری دقیق
خواص مکانیکی
خواص پایه. از آنجا که بیشتر قطعات ریختگی بکار رفته در کاربردهای هوافضایی از جنس Ti-6Al-4V هستند بیشترین داده های برای این آلیاژ ایجاد شده است. خواص کششی در دمای اتاق در جدول 6-2 برای تیتانیوم ریختگی CP و برای 8 آلیاژ تیتانیوم ریختگی ارائه شده اند. بطور کلی، آلیاژهای تیتانیوم ریختگی دارای استحکام استاتیکی برابر یا تقریبا برابر با استحکام استاتیک آلیاژهای کارشده با ترکیب یکسان هستند. اما با اینکه مقادیر داکتیلیته کمتری دارند بازهم بالاتر از مقادیر کمینه تضمین شده مربوط به فلزات کارشده قرار می گیرند.
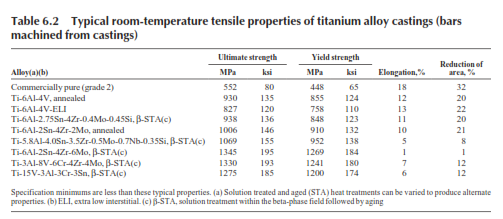
جدول 6-2 خواص کششی قطعات ریختگی تیتانیوم آلیاژی (میله های ماشینکاری شده از قطعات ریختگی) در دمای اتاق
در حالیکه مقادیر مربوط به خواص در مقایسه با خواص آلیاژهای کارشده مطلوب هستند اما رفتار خستگی همواره چندان هم مطلوب نیست که در شکل 6-8 دیده می شود. HIP بطور محسوسی به افزایش محدوده طراحی خستگی کمک می کند اما آن را به سطح آلیاژهای کارشده نمی رساند. بطور کلی، بهبود خواص خستگی و کاهش پراکندگی داده های خستگی از طریق HIP حاصل می شوند. همچنین، اصلاح عملیات حرارتی نظیر انجام beta-STOA ممکن است به بهبود کلی در سطح استحکام خستگی مربوط به قطعات ریختگی آلیاژی کمک کند.
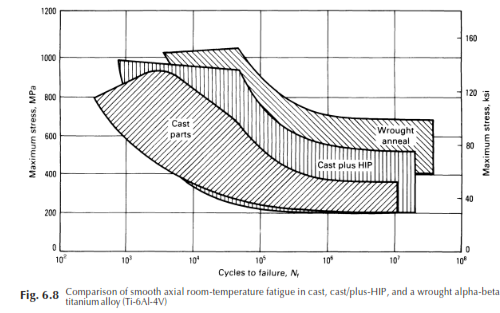
شکل 6-8 مقایسه خستگی محوری در دمای اتاق مربوط به قطعه ریخته گری شده، ریخته گری شده بعلاوه HIP و یک آلیاژ تیتانیومی آلفا- بتای کارشده
اگرچه قطعات ریختگی آلیاژهایی نظیر Ti-6Al-4V دارای خواص استاتیک تقریبا کمتر و خواص خستگی کمتری نسبت به محصولات کارشده هستند اما خواصی نظیر چقرمگی شکست، نرخ رشد ترک خستگی و مقاومت به خوردگی تنشی می توانند بهتر از خواص Ti-6Al-4V کارشده آنیل شده باشند. شکل 6-9 مقادیر چقرمگی شکست کرنش صفحه ای مربوط به قطعات ریختگی Ti-6Al-4V را با ورق Ti-6Al-4V و دیگر آلیاژهای تیتانیوم کارشده مقایسه می کند. چقرمگی بالا بدلیل میکروساختار فراوری شده بتا در قطعات ریختگی پس از عملیات حرارتی پساHIP می باشد. شکل 6-10 نرخ رشد ترک خستگی مربوط به آلیاژ Ti-6Al-4V کارشده آنیل شده بتا را با نسخه های ریختگی و ریختگی بعلاوه HIP این آلیاژ مقایسه می کند. توجه کنید که این داده ها بطور کلی در یک محدوده پراکندگی تقریبا یکسان قرار می گیرند.
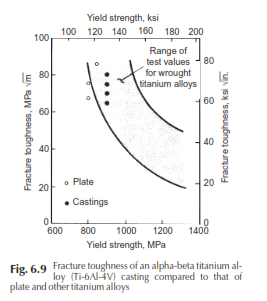
شکل 6-9 چقرمگی شکست یک آلیاژ تیتانیومی ریختگی آلفا- بتا (Ti-6Al-4V) در مقایسه با ورق ضخیم و دیگر آلیاژهای تیتانیوم
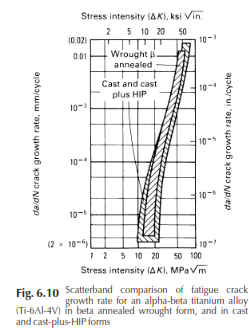
شکل 6-10 مقایسه نوار پراکندگی نرخ رشد ترک خستگی مربوط به یک آلیاژ تیتانیومی آلفا- بتا (Ti-6Al-4V) در شکل کارشده آنیل شده بتا و صورت های ریخته گری و ریخته گری بعلاوه HIP
همانطور که در بالا اشاره شد، عملیات های حرارتی خاصی برای اصلاح میکروساختار قطعات ریختگی تیتانیوم آلیاژی فراوری شده توسط HIP توسعه یافته اند. جدول 6-3 و شکل 6-11 برخی نتایج خواص مکانیکی مربوط به Ti-6Al-4V عملیات حرارتی شده مطابق جدول 6-1 را نشان می دهند.
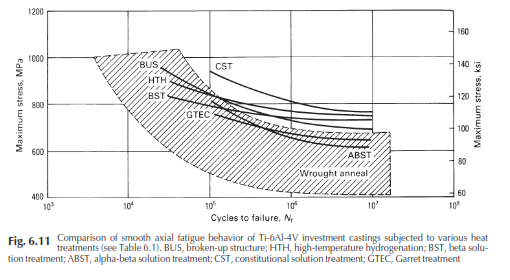
شکل 6-11 مقایسه رفتار خستگی محوری قطعات Ti-6Al-4V تولیدی به روش ریخته گری دقیق قرارگرفته در معرض عملیات های حرارتی مختلف (جدول 6-1 را ببینید).
BUS: ساختار شکسته شده، HTH: هیدروژناسیون دما بالا، :BST عملیات انحلالی بتا، :ABST عملیات انحلالی آلفا- بتا، CST: عملیات انحلالی ترکیبی، :GTEC عملیات Garret
خواص طراحی. هنگام تعیین خواص آلیاژهای ریختگی تیتانیوم، منشا ماده مورد آزمایش، ملاحظه ایست که نباید از آن چشم پوشی کرد. میله های ریختگی جداگانه تحت آزمایش، میله های ریختگی روی قطعات، میله های ماشینکاری شده از قطعات ریختگی برای تعیین خواص بکار رفته اند. معمولا داده ها از میله های ریختگی جداگانه تحت آزمایش که ارزانترین منبع هستند گزارش می شوند. کمترین مقدار داده از میله های تحت آزمایش ماشینکاری شده از قطعات ریختگی که گران قیمت ترین منبع هستند استخراج می شوند. تفاوتهای موجود در خواص را می توان بسته به منشا نمونه تحت تست (جدول 6-3) ذکر کرد. منشا نمونه تحت تست یک واقعیت تاثیرگذار در تولید داده های طراحی می باشند.

جدول 6-3 مقایسه خواص کششی Ti-6Al-4V ریختگی در دمای اتاق از سه منبع مختلف تست ماده
ملاحظه دوم آن است که طراحی مربوط به یک قطعه تیتانیومی ریختگی بدون عیب ممکن است به سطح استحکام کاملا یکسانی نیاز نداشته باشد کما اینکه برای شمش کار شده چنین نیازی وجود دارد.
فقط پس از چند با ریخته گری و تعیین خواص، می توان درباره شایستگی هر روش ریخته گری قضاوت کرد.
پایان فصل ششم