مهمترین این عوامل عبارتند از:
-
مقادیر عناصر آلیاژی خاص و ناخالصیها
-
فرایند ذوب به کار رفته برای ایجاد شمش اولیه
-
روش مربوط به کار مکانیکی روی شمش ها برای تبدیل به محصولات اولیه
-
مراحل فورج کاری یک شکل معین
-
فرایند ریخته گری و حجم ریخته گری به علاوه استفاده از روشهای چگالش نظیر پرسکاری ایزواستاتیک گرم (HIP) برای کاهش تخلخل قطعه ریختگی
-
فرایند متالورژی پودر (P/M) از جمله روش ساخت پودر
-
فرایند اتصال دهی به کار رفته برای تولید یک سازه
-
عملیات حرارتی پسافرآوری یا گام نهایی به کار رفته در کار روی قطعات یا تولید
-
فرایند ماشینکاری و عملیات سطحی
میکروساختار دسته هایی از آلیاژ تیتانیوم (مانند آلفا- بتا) در فصل 3 پوشش داده شده است و آن فصل را باید در هنگام خواندن این فصل، به عنوان یک مرجع به کار برد. برای یادآوری، آلیاژهای تیتانیوم به این دسته ها تقسیم می شوند: آلفا، شبه آلفا، آلفا- بتا (آلفا به علاوه بتا) و بتا. این گروه بندی، وجود مرسوم فاز آلفا (هگزاگونال فشرده) در دمای اتاق و/یا فاز بتا (مکعبی مرکز پر) در یک آلیاژ خاص را منعکس می کند. استحاله های موجود در گرمایش و تبرید (از ناحیه بتای دمابالا) و ترکیب های فازی با افزودنی های آلیاژی که معمولا به عنوان پایدارسازهای آلفا یا پایدارسازهای بتا تقسیم بندی می شوند تغییر می کنند. وانادیوم، مولیبدن، آهن و هیدروژن، پایدارسازهای بتا هستند درحالیکه آلومینیوم، اکسیژن و نیتروژن نمونه هایی از پایدارسازهای آلفا هستند.
خواص اساسی تیتانیوم و آلیاژهای تیتانیوم
تیتانیوم خالص را می توان بطور قابل توجهی با آلیاژسازی، فرآوری و عملیات حرارتی استحکام دهی نمود و آلیاژها باز هم در سطوح کمی از چگالی باقی می مانند. متعاقبا، خواص مکانیکی آنها جذاب است بویژه با توجه به نسبت های استحکام به چگالی. شکل 12-1 این نسبت را برای تیتانیوم خالص، فولاد و آلیاژهای پایه آلومینیوم و پایه منیزیم با استحکام بالا نشان می دهد. جدول 12-1 خواص مرسوم مربوط به تیتانیوم خالص و دو آلیاژ تیتانیوم را با خواص فولاد با استحکام بالا روی مبنایی از یک چگالی مطلق و چگالی تغییریافته مقایسه می کند. این جدول نشان می دهد که آلیاژهای تیتانیوم به طور قابل توجهی در مقایسه کردن استحکام به چگالی (وزن) مستحکم هستند.
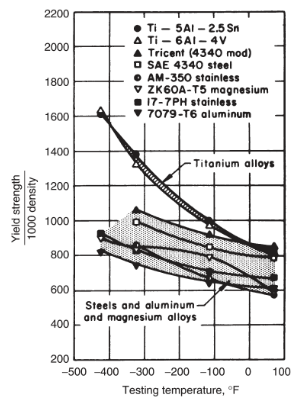
شکل 12-1 نسبت استحکام تسلیم به چگالی به عنوان تابعی از دما برای برخی آلیاژهای تیتانیوم در مقایسه با برخی آلیاژهای فولاد، آلومینیوم و منیزیم
خواص فیزیکی تیتانیوم با فرآوری تغییری نمی کنند. اما سینتیک استحاله های فاز بتای تیتانیوم که در حین گرمایش، تبرید و پیرسازی رخ می دهند تاثیر بسیاری بر میکروساختار و در نتیجه، خواص مکانیکی دارند. بنابراین، خواص مکانیکی آلیاژهای تیتانیوم را به طور مستقیم به ترتیب فرآوری و عملیات حرارتی می توان مربوط کرد.
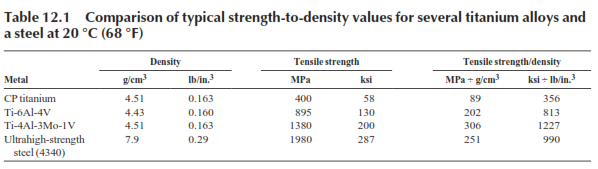
جدول 12-1 مقایسه مقادیر استحکام به چگالی برای برخی آلیاژهای تیتانیوم و فولاد در °C 20 (°F 68)
خواص الاستیک بوسیله ترکیب شیمیایی و بافت تحت تاثیر قرار می گیرند اما این خواص به طور خاصی تحت تاثیر عملیات حرارتی قرار نمی گیرند. مدول تیتانیوم می تواند با نوع آلیاژ از حدود GPa 93 (psi 106*13.5) تا حدود GPa 120.5 (psi106 * 17.5) تغییر کند. این مقدار تقریبا 50 درصد بیش از مدول مربوط به آلیاژهای آلومینیوم و حدود 60 درصد مدول مربوط به فولادها و سوپرآلیاژهای پایه نیکل است.
برای یک فاز معین، این مدول تابعی از جهت اندازه گیری در بلور است. متعاقبا، با قرار گرفتن جهت گیری بلور در راستای آرایش دانه (بافت سازی) آلیاژهای تیتانیوم، می توان به جهت گیری های معینی در دانه دست یافت که منجر به حصول مدول بالاتر (یا مدول کمتر) نسبت به مقادیر معمول یافت شده برای یک آلیاژ می گردد.
ساختار و سخت کردن آلیاژهای تیتانیوم
برای منظور ما، ساختار به شکل ماکروساختار و میکروساختار (یعنی نمای درشت و نمای ریز) یک مقطع پولیش شده و حکاکی شده فلز تعریف می شود که در بزرگنمایی های تا 10000برابر قابل مشاهده است. دو مشخصه دیگر میکروساختاری که نه بطور چشمی بلکه با روشهای دیگر نظیر پراش پرتوی ایکس یا ترکیب شیمیایی تعیین می شوند عبارتند از نوع فاز (یعنی آلفا، بتا و غیره) و بافت دانه ها (جهتگیری دانه ها).
اندازه دانه، شکل دانه و چیدمان های مرزدانه در تیتانیوم دارای تاثیر زیادی بر خواص مکانیکی است. قابلیت کنترل و تغییر فازها/دانه های موجود به عنوان نتیجه ترکیب آلیاژ است که عامل گوناگونی خواصی است که می توان در تیتانیوم و آلیاژهای آن ایجاد کرد. محصولات فاز بتای استحاله شده در آلیاژها می توانند بر استحکام های کششی، داکتیلیته، چقرمگی و خواص چرخه ای تاثیر بگذارند. تاثیرات اساسی عناصر آلیاژی را باید به این تاثیرات افزود.
نقش عناصر آلیاژی دارای اندازه اتمی قابل مقایسه
برخی عناصر آلیاژی از نظر اندازه اتمی به اندازه اتمی تیتانیوم، کم و بیش نزدیک هستند و می توانند در تیتانیوم حل شده و جانشین اتم های تیتانیوم شوند. همین طور، آنها می توانند دو مورد زیرا تشکیل دهند:
-
یک فاز رقیب دیگر نظیر ترکیب بین فلزی Ti3Al
-
یک مخلوط متفاوت (از تیانیوم و عنصر ثانویه) که ساختار بلوری عنصر آلیاژی دوم اما با اندازه ای نزدیک را به خود می گیرد
برخی عناصر آلیاژی معین به پایدارسازی فاز آلفا و دیگر عناصر آلیاژی، به پایدارسازی فاز بتا کمک می کنند. وضعیت حقیقی تا حدی پیچیده تر از این است (فصل 3 را ببینید).
عناصر آلیاژی که در آلیاژهای تیتانیوم حل می شوند موجب استحکام دهی به وسیله تداخل در فرایند تغییرشکل پلاستیک می شوند. چنین استحکامدهی ای به عنوان استحکام دهی محلول جامد (SSS) شناخته می شود. در مورد عناصر آلیاژی با اندازه نزدیک حل شده در تیتانیوم، از سخت کنندگی به عنوان جانشین SSS یاد می شود. عناصری که فازهای ثانویه ایجاد می کنند معمولا به طور موثرتری نسبت به عناصری که حل می شوند در تغییرشکل تداخل ایجاد می کنند و در نتیجه، فازهای ثانویه معمولا باعث سخت کنندگی بیشتر تیتانیوم نسبت به SSS می شوند.
نقش معمول عناصر با اندازه نزدیک در استحکام دهی تیتانیوم، فقط ایجاد SSS مستقیم نیست بلکه به کنترل میکروساختار از طریق تاثیر بر مقادیر فازهای آلفا و بتا، تمایل به تشکیل ترکیبات و نرخ استحاله فازی در میان دیگر مشخصات کمک می کند.
نقش عناصر بین نشین
عناصر بین نشین، عناصری هستند که بطور محسوسی کوچکتر از اتم تیتانیوم هستند و در نتیجه می توانند بدون جایگزینی اتم های تیتانیوم به عنوان محلولهای جامد در شبکه بلوری فاز تیتانیوم حل شوند. البته، برخی عناصر بین نشین نیز می توانند فازهای ثانویه ای با تیتانیوم تشکیل دهند. همانند مورد عناصر با اندازه نزدیک، عناصر بین نشین می توانند تشکیل فازی را نسبت به فاز دیگر در اولویت قرار دهند. تاثیر زیاد بر خواص مکانیکی تیتانیوم خالص تجاری (CP) از حضور هیدروژن، نیتروژن، کربن و اکسیژن ایجاد می شود که به طور بین نشین در تیتانیوم حل می شوند و دارای تاثیر مشهودی بر خواص مکانیکی هستند. این تاثیرات با مقادیر مختلف به آلیاژهای تیتانیوم نیز منتقل می شود.
تاثیرات عناصر بین نشین در تیتانیوم
هیدروژن در تیتانیوم خالص تجاری. حلالیت هیدروژن در تیتانیم آلفا در °C 300 (°F 572) تقریبا 8 درصد اتمی (حدود 0.15 درصد وزنی یا تقریبا ppm 1000) است. هیدروژن محلول تاثیر کمی بر خواص مکانیکی دارد. آسیب بوسیله هیدریدها ایجاد می شود که در حین قرارگیری در معرض یکی از گونه های هیدروژن گازی یا کاتدی با نفوذ به ماده تشکیل می شوند. در رسوب هیدرید، داکتیلیته آسیب می بیند. آسیب هیدروژنی تیتانیوم و آلیاژهای تیتانیوم به عنوان افت داکتیلیته (تردی) و/یا کاهش آستانه شدت تنش مربوط به انتشار ترک مطرح می شود. شکل 12-2 تاثیر هیدروژن را بر کاهش سطح نشان می دهد. توجه داشته باشید که هیچ تردی ای در ppm 20 هیدروژن یافت نمی شود. ppm 20 معادل با حدود 0.1 درصد اتمی هیدروژن است.
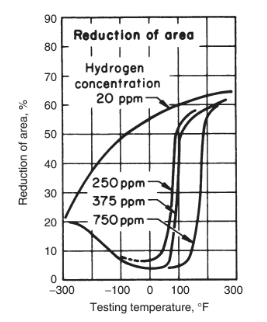
شکل 12-2 داکتیلیته تیتانیوم آلفا بر حسب دمای تست که نشان دهنده تاثیرات تردسازی هیدروژن است
داده های شکل 12-3 و 12-4 نشان می دهند که مستقل از عملیات حرارتی، غلظت ppm 20 تاثیر کمی بر استحکام ضربه ای- معیار دیگری از تردی- دارد. اما توجه کنید که مقدار هیدروژن به کمی 0.5 درصد اتمی (حدود atom ppm 100) می تواند موجب تردی قابل سنجشی گردد. تبرید آهسته از ناحیه آلفا- برای نمونه °C 400 (°F 752)- موجب هیدرید کافی برای رسوب کردن به منظور کاهش انرژی ضربه ای می شود.
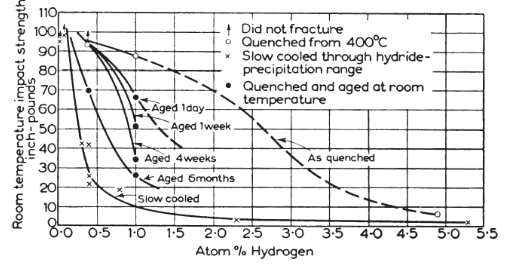
شکل 12-3 تاثیر مقدار هیدروژن و عملیات حرارتی بر انرژی ضربه ای تیتانیوم آلفا
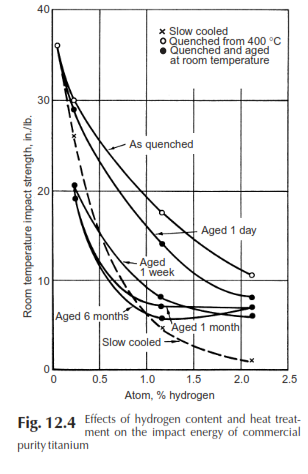
شکل 12-4 تاثیرات مقدار هیدروژن و عملیات حرارتی بر انرژی ضربه ای تیتانیوم خالص تجاری
از آنجا که این پدیده به نفوذ هیدروژن و نیز تشکیل هیدرید وابسته است ممکن است در تردی هیدروژنی، بیشینه ای به عنوان تابعی از دما وجود داشته باشد. سطح دقیق هیدروژن که در آن سطح، فاز هیدرید جداگانه تشکیل می شود به ترکیب آلیاژ و پیشینه متالورژیکی بستگی دارد. اگر در حین فرآوری، هیدروژن انباشته شود، این انباشت را می توان با آنیل کاری در خلاء از بین برد اما این فرآیند به هزینه و مراحل فرآوری می افزاید.
تبرید سریع با کوئنچ در آب از °C400 (°F 752) رسوب هیدروژن را متوقف می کند و در نتیجه، انرژی ضربه ای بالایی را برجا می گذارد. اما پیرسازی در دمای اتاق حتی برای چندین روز موجب رسوب مقدار کافی هیدرید میشود و در نیتجه، انرژی ضربهای را کاهش می دهد (شکل 12-3). در نتیجه، حتی اگر رسوب هیدرید را بتوان با عملیات حرارتی کنترل کرد، پیرسازی در °C 25 (°F 77) منجر به تشکیل رسوب کافی و درشت شدن رسوب برای تردسازی یک آلیاژ می گردد.
تنها روش عملی برای کنترل مشکل هیدروژن، حفظ یک غلظت کم از آلیاژ است. در نتیجه، تیتانیوم CP معمولا دارای یک مقدار هیدروژن مجاز حدود 0.015 درصد وزنی (تقریبا ppm 100 از نظر وزنی) می باشد. برای نمونه، برای گریدهای تیتانیوم CP نشان داده شده در جدول 12-2، سطح مجاز حدود 0.01 درصد بود.
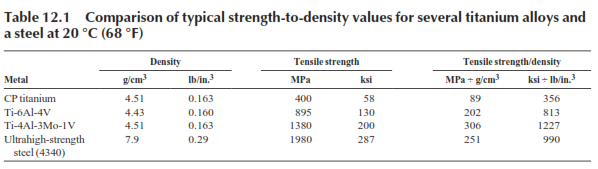
جدول 12-2 مقدار بیشینه بین نشین به علاوه خواص مکانیکی کمینه برای برخی گریدهای آلیاژ تیتانیوم
اکسیژن و نیتروژن در تیتانیوم خالص تجاری مطابق با شکل 12-5، دارای تاثیر بالقوه بر استحکام هستند. با افزایش مقادیر اکسیژن و نیتروژن، چقرمگی کاهش می یابد تا درنهایت، ماده کاملا ترد شود. تردی در غلظتی بسیار کمتر از حد حلالیت رخ می دهد. توجه کنید که مطابق با جدول 12-2 مقدار مجاز اکسیژن بالاتر از مقدار مجاز نیتروژن است. این شکل نشان می دهد که چرا گریدهای تیتانیوم با اکسیژن و نیتروژن بالاتر، دارای استحکام های کششی بالاتری هستند. (جدول 12-2 را برای مقایسه بین گریدها ببینید.)
شایان ذکر است که حتی گرید تیتانیوم CP با بالاترین مقدار بین نشین، دارای داکتیلیته خوبی است اما به دلیل اکسیژن و نیتروژن موجود، در یک تیتانیوم خالص آلفای تشکیل شده از بتا دارای یک ساختار ویدمن اشتاتن بسیار بارزتر نسبت به تیتانیومی است که عاری از این عناصر است (شکل 12-6). اما این موضوع دارای تاثیر کمی بر خواص مکانیکی است. افزودن کربن تا 0.3 درصد، به شدت تیتانیوم را مستحکم کرده و از داکتیلیته تا حدی می کاهد (شکل 12-5).
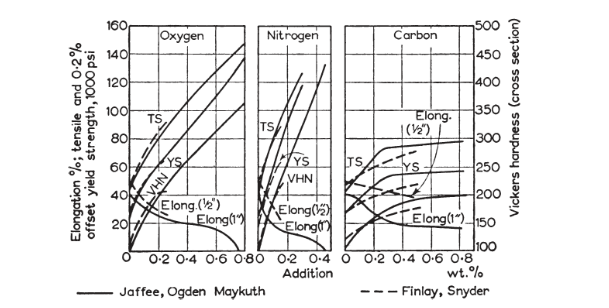
شکل 12-5 تاثیرات هیدروژن، نیتروژن و کربن بر خواص کششی و سختی تیتانیوم آلفا.
داده هایJafee مربوط به نمونه های آنیل شده درC°850 هستند. داده هایFinaly مربوط به نمونه های آنیل شده درC°700 هستند.
بنابراین، هر دو سری داده به نمونه های به خوبی آنیل شده در ناحیه α اشاره دارند.
TS استحکام کششی و YS استحکام تسلیم.
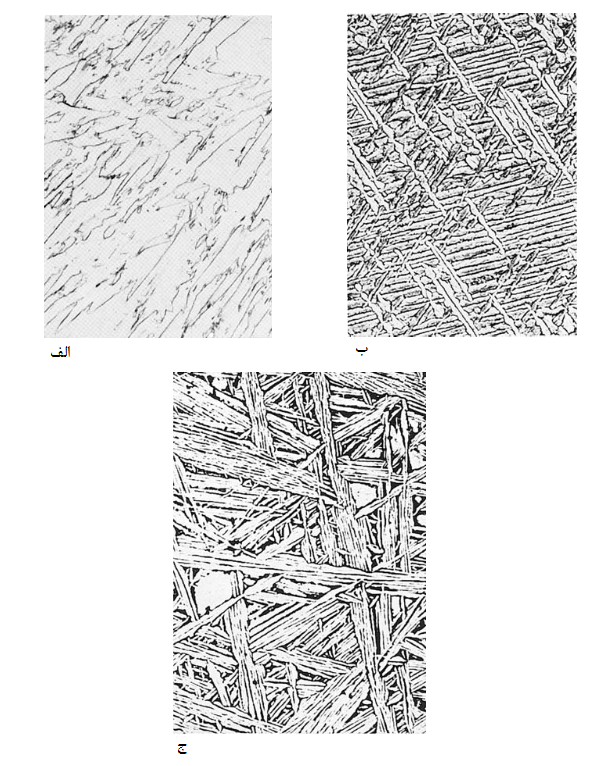
شکل 12-6 میکروساختارهای تیتانیوم خالص تجاری با و بدون اکسیژن و نیتروژن بین نشین
الف- تیتانیوم نسبتا خالص. x 150. ب- Ti-0.3 wt%O به دست آمده پس از آنیل کاری در ناحیه بتا و سپس تبرید تا °C 25 (°F 77)، x 150.
ج- Ti-0.3wt% N، x 150. همه تصاویر از میکروسکوپ نوری هستند.
بین نشین ها در آلیاژهای تیتانیوم
هرچند دو مبحث پیشین درباره تاثیرات عناصر بین نشین در تیتانیوم خالص بودند اما این مفاهیم را می توان به آلیاژهای تجاری موجود نیز منتقل کرد. این مفاهیم برای هر آلیاژ تیتانیومی معتبر هستند زیرا مقادیر اکسیژن و نیتروژن در تعیین استحکام و بویژه داکتیلیته، نقش دارند. سطوح فرا اندک بین نشین (ELI) تعیین شده برای برخی آلیاژهای تیتانیوم، تاثیر بین نشین های کمتر را بر داکتیلیته تصدیق می کنند. ماده از نوع ELI برای کاربردهای حساسی به کار می رود. در این مواد با حفظ بین نشین ها در یک سطح بسیار اندک، داکتیلیته و چقرمگی بیشتری ایجاد می شوند.
برای جلوگیری از تردی، هیدروژن همواره در یک سطح کم حفظ می شود اما باز هم نگرانی درباره بهترین مقدار ممکن هیدروژن در تیتانیوم CP و آلیاژی برای عدم تردی و کم نگهداشتن هزینه تولید وجود دارد.
خواص مکانیکی تیتانیوم خالص
ساختار
تیتانیوم با خلوص بالا (9/99 درصد یا بیشتر) یک ماده تجاری با کاربردهای فراوان نیست. گریدهای تیتانیوم CP- که مقدار تیتانیوم کمتر از 99.55 درصد است- مورد استفاده بوده و بطور کلی خواص مکانیکی چندان متفاوتی نسبت به فلز با خلوص بالا ندارند. تیتانیوم با خلوص بالا و گریدهای تیتانیوم برای بحث درباره خواص در اینجا، یکی در نظر گرفته می شوند.
تیتانیوم خالص، فاز تکی آلفاست. همانند هر آلیاژ تکفازی، میکروساختار تیتانیوم CP به این که آیا این ماده، کارسرد شده یا خیر و نیز به نوع خاص آنیل کاری به کار رفته بستگی دارد. بعلاوه، در تبرید از ناحیه بتا، که از °C 882 (°F 1620) آغاز می شود، ساختار به فرایند تبرید دنبال شده وابسته است زیرا فرآیند مستقیما بر پیشرفت استحاله بتا به آلفا و به اندازه نهایی و شکل نهایی دانه آلفا تاثیر می گذارد.
میکروساختار هم محور تیتانیوم پس از آنیل کاری در °C 800 (°F 1472) در ناحیه آلفا در شکل 12-7 الف نشان داده شده است. در اینجا اندازه دانه و در نتیجه، خواص را می توان صرفا با کار سرد و آنیل کاری تغییر داد. خواص این میکروساختار در زیرنویس شکل فهرست شده اند.
آنیل کاری در ناحیه بتا در °C 1000 (°F 1832) و سپس تبرید سریع تا °C 25 (°F 77) بوسیله کوئنچ در آب باعث ایجاد ساختار نشان داده شده در شکل 12-7ب می شود. حتی تبرید سریع نیز موجب توقف استحاله بتا به آلفا نمی شود و ساختار کاملا به آلفا استحاله می گردد. توجه کنید که مرزدانه های آلفا دندانه دار بوده و کاملا بی قاعده هستند. خواص مربوط به این ساختار در زیرنویس فهرست شده اند. این ساختار از ساختار هم محور ایجادشده با آنیل کاری صرف در ناحیه آلفا مستحکم تر است. برای هر دو عملیات، تیتانیوم همچنان کاملا داکتیل است.
تبرید آهسته –مثلا به مدت 20 ساعت تا °C 25 (°F 77)- باعث ساختاری همانند شکل 12-7 ج می شود. این ساختار هم کاملا آلفاست اما مرزدانه ها نسبت به مرزدانه های ایجاد شده در تبرید سریع کمتر بی قاعده هستند. این ساختار تا حدی ضعیف تر از ساختار ایجاد شده در تبرید سریع است اما همچنان مستحکم تر از ساختار هم محور نشان داده شده در شکل 12-7 ج می باشد.
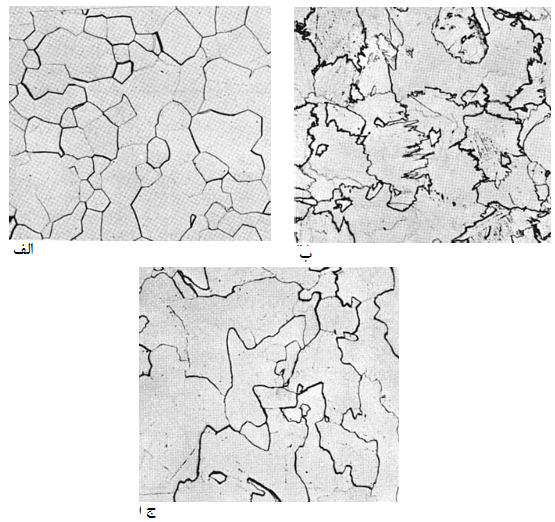
شکل 12-7 میکروساختار تیتانیوم خالص تجاری پس از آنیل کاری در ناحیه آلفا یا ناحیه بتا و تبرید تا دماهای محیط.
الف- آنیل شده به مدت 1 ساعت در °C 800 (°F 1472)، کوئنچ شده در آب، مقدار استحکام تسلیم 0.2 درصد: MPa 124 (ksi 18)، استحکام کششی: MPa 248 (ksi 36)، ازدیاد طول: 80درصد؛ x 100.
ب- آنیل شده به مدت 1 ساعت در °C 1000 (°F 1832)، کوئنچ شده در آب، مقدار استحکام تسلیم 0.2 درصد: MPa 228 (ksi 33)، استحکام کششی: MPa 290 (ksi 42)، ازدیاد طول: 60 درصد؛ x 100
ج- آنیل شده در °C 1000 (°F 1832)، تبریدشده در کوره، مقدار استحکام تسلیم 0.2 درصد: MPa 165 (ksi 24)، استحکام کششی: MPa 262 (ksi 38)، ازدیاد طول: 60 درصد؛ x 100.
همه تصاویر از میکروسکوپ نوری هستند.
خواص
گریدهای تیتانیوم دارای مقادیر متغیری از ناخالصی ها (مانند کربن، هیدروژن، آهن، نیتروژن و اکسیژن) هستند. برخی گریدهای اصلاح شده نیز دارای مقادیر کمی پالادیوم (Pd 0.2) و نیکل- مولیبدن (0.3Mo-0.8Ni) هستند. از آنجا که مقادیر کمی از ناخالصی های بین نشین به شدت بر خواص مکانیکی تیتانیوم خالص تاثیر می گذارند، تمایز بین گریدهای مختلف تیتانیوم غیرآلیاژی بر مبنای آنالیز شیمیایی آسان نیست. گریدهای تیتانیوم به سادگی با خواص مکانیکی تشخیص داده می شوند.
برای سطح معینی از بین نشین ها و/یا عناصر اندک آلیاژی، خواص تیتانیوم گرید خالص عمدتا تابعی از اندازه دانه، شکل دانه و مقدار کار سرد در فلز می باشد. تیتانیوم خالص آنیل شده دارای سطحی از تنش سیلان است که نزدیک به تنش سیلان فولاد نرم می باشد. شکل 12-8، منحنی های تنش- کرنش تیتانیوم با خلوص بالا، یک آلیاژ تیتانیوم آلفا- بتا و یک آلیاژ تیتانیوم بتا را با برخی فولادهای نرم و آلومینیوم خالص مقایسه می کند. خواص کششی کمینه در دمای اتاق در جدول 12-3 برای گریدهای مختلف ارائه شده اند. شکل 12-9، UTS را به عنوان تابعی از دما برای CP و گریدهای تیتانیوم اصلاح شده ارائه می نماید.
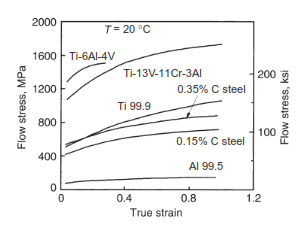
شکل 12-8 منحنی های تنش- کرنش مربوط به برخی آلیاژهای تیتانیوم به علاوه فولاد و آلومینیوم.
ناخالصیهای تیتانیوم (wt%) عبارت بودند از 04/0 O2، 01/0 N2، 002/0 H2، 04/0 Fe . 010/0 C.
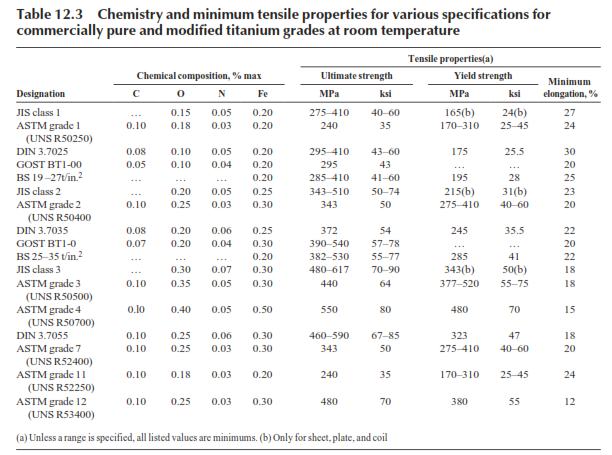
جدول 12-3 ترکیب شیمیایی و خواص کششی مربوط به دسته های مختلف گریدهای تجاری خالص و اصلاح شده تیتانیوم در دمای اتاق
هرچند داده ها در اینجا برای تاثیرات اندازه دانه بر گریدهای تیتانیوم ارائه نشده اند اما بطور کلی این موضوع که ریزی ساختار (اندازه دانه کوچکتر) از دیدگاه TYS در مواد فلزی مطلوب تر است، موضوعی پذیرفته شده است. UTS به طور خاصی با اندازه دانه تغییر نمی کند اما داکتیلیته- که با ازدیاد طول یا کاهش سطح نشان داده می شود- به طور کلی با اندازه دانه کوچکتر بهبود می یابد. داکتیلیته معیاری از چقرمگی است اما معمولا در گریدهای تیتانیوم خالص تجاری، چقرمگی مسئله ای به حساب نمی آید. معیار دیگری از چقرمگی، استحکام ضربه ای شارپی است که برای برخی گریدها در شکل 12-9 مقایسه می شود.

شکل 12-9 استحکام کششی نهایی (UTS) بر حسب دما برای تیتانیوم خالص تجاری (CP) و تیتانیوم اصلاح شده.
رفتار دمابالای گریدهای تیتانیوم مطالعه شده است اما این آلیاژها معمولا در دماهای بالا به کار نمی روند. آلیاژهای شبهآلفا یا آلفا- بتا مواد ترجیحی ای هستند که خواص مکانیکی دما بالایشان مطلوب هستند.
با توجه به تاثیرات اندازه دانه و تغییرات جزئی ممکن در ترکیب شیمیایی، مواد تیتانیوم CP ریختگی باید تا حد زیادی شبیه به مواد کارشده رفتار کنند.
آلیاژهای آلفا/ شبه آلفا
آلیاژهای آلفا نظیر Ti-5Al-2.5Sn، Ti-6Al-2Sn-4Zr-2Mo+Siو Ti-8Al-1Mo-1V (جدول 2-2 را ببینید) عمدتا در توربین گازی به کار می روند. Ti-8Al-1Mo-1V و Ti-6Al-2Sn-4Zr-2Mo+Si در دماهایی بالاتر از معمول برای آلیاژهای آلفا- بتا، آلیاژهای Ti-6Al-4V، Ti-8Al-1Mo-1V و Ti-6Al-2Sn-4Zr-2Mo+Si دارای مقاومت خزشی بهتری نسبت به Ti-6Al-4V هستند و مقاومت خزشی به وسیله یک ساختار سوزنی ظریف (ویدمن اشتاتن) ارتقا می یابد. در شرایط نرمال عملیات حرارتی شده، Ti-6Al-2Sn-4Zr-2Mo+Si که در واقع دارای ساختاری است که بهتر است به عنوان آلفا- بتا تعریف شود، همچنان در اینجا در دسته آلیاژهای آلفا/ شبه آلفا در نظر گرفته خواهد شد.
نکات مربوط به ساختارها و استحکام دهی
آلیاژهای آلفا دارای فاز آلفا به عنوان فاز مرسوم خود در دمای کمتر یعنی کمتر از حدود °C 800 (°F 1472) هستند. به طور کلی، آلیاژهای آلفا دارای فاز بتای بسیار کمتری نسبت به Ti-6Al-4V هستند. در نتیجه، خواص آنها بطور کلی با عملیات حرارتی به شدت تغییر می کند. عملیات های پیرسختی چندان موثر نیستند زیرا این عملیات ها به استحاله های فاز بتا برای بهبود استحکام نیاز دارند. عملیات های حرارتی پیرسختی می توانند برای مقاومت خزشی مضر باشند. بنابراین، آلیاژهای آلفا و شبه آلفا معمولا در شرایط عملیات انحلالی شده و پایدارسازی شده به کار می روند. آنیل کاری انحلالی را می توان در دمایی حدود °C 35 (°F 63) کمتر از دمای تحول بتا انجام داد در حالیکه پایدارسازی معمولا با گرمایش در حدود °C 590 (°F1100) به مدت 8 ساعت ایجاد می شود. این آلیاژها به تشکیل Ti3Al منظم- که موجب ترک خوردگی در اثر خوردگی همراه با تنش (SCC) می شود- مستعدتر هستند. (برای اطلاعات بیشتر درباره SCC فصل 13 را ببینید.)
تنها مکانیزم های استحکام دهی عبارتند از کارسرد، کارسرد و آنیل کاری (برای کنترل اندازه دانه) و افزودنی هایی از عنصر حل شونده برای استحکام دهی با محلول جامد. آلفاسازها نظیر آلومینیوم و قلع می توانند استحکام تیتانیوم را بوسیله استحکام دهی با محلول جامد افزایش دهند. آلومینیوم و قلع دارای تاثیر زیادی بر خواص مکانیکی تیتانیوم هستند یعنی افزایش استحکام تقریبا MPa 55 (ksi 8) برای هر 1 درصد آلومینیوم و MPa 28 (ksi 4) برای هر 1 درصد قلع. اما برای زیرکونیوم، تاثیر محدود به افزایش تقریبا MPa 3.5 (ksi 0.5) برای هر 1 درصد افزودن است. در نتیجه، زیرکونیوم برای استحکام دهی آلیاژهای تیتانیوم آلفا به کار برده نمی شود.
آلیاژهای آلفا- بتا
مهمترین آلیاژ تیتانیوم آلیاژ آلفا- بتای Ti-6Al-4V است. این آلیاژ کاربردهایی برای قطعات هوافضا و حساس به شکست یافته است. با نسبت استحکام به چگالی mm 106*25 (in. 106*1)، این آلیاژ یک ماده سازه ای سبک وزن است و دارای ترکیب های از استحکام- چقرمگی بین مقادیر فولاد و آلیاژهای آلومینیوم می باشد. آلیاژهای آلفا- بتای با استحکام بالا شامل Ti-6Al-6V-2Sn و Ti-6Al-2Sn-4Zr-6Mo می باشند. در همه این آلیاژها، آلفا فاز غالب می باشد اما این برتری در آلیاژهای با استحکام بالا نسبت به Ti-6Al-4V تا حدی کمتر است. این آلیاژها نسبت به Ti-6Al-4V مستحکم تر بوده و با راحتی بیشتر عملیات حرارتی می شوند. این قابلیت از استحکام دهی بیشتر با محلول جامد ناشی از قلع و زیرکونیوم می شود که دارای تاثیرات نسبتا کمی روی دمای استحاله می باشند. همچنین مقادیر زیاد فاز بتا که ناشی از افزودنی های بیشتر وانادیوم و مولیبدن می باشند نیز موثر است.
نکاتی درباره ساختارها و استحکام دهی
پایدارسازهای آلفا یعنی آلومینیوم قلع به تیتانیوم برای پایدارسازی فاز آلفا نسبت به بتا و برای افزایش استحکام آلیاژهای تیتانیوم با سخت گردانی با محلول جامد افزوده می شوند. آلومینیوم با پایدارسازهای بتا متوازن می شود به طوری که محصول دارای مخلوطی از فازهای آلفا و بتای موجود برای کنترل خواص می باشد. تاثیرگذاری قلع خیلی زود متوقف می شود در حالیکه درباره آلومینیوم چنین نیست. حد عملی بالایی برای آلومینیوم حدود 7 درصد است. در بیشتر از این مقدار، انجام کار داغ روی آلیاژ دشوار است و حساسیت به تردی ناشی از محیط بالاست. تردی می تواند در دماهای کم نیز رخ دهد یعنی هنگامی که مقدار آلومینیوم بسیار بالاست. عناصر آلفاساز را می توان برای کمک به سخت گردانی با محلول جامد اضافه نمود اما مقدار آنها را باید در حدود مشخصی حفظ کرد.افزودن عناصر بتاساز می تواند موجب عملیات حرارتی انحلالی در دماهای کمتر شود و می تواند موجب سخت گردانی بیشتر با محلول جامد شود. این عناصر همچنین می توانند تشکیل بتا را کند کنند به طوری که بتا به مارتنزیت استحاله شده یا باقی می ماند تا بعدا در حین بازگرمایش (پایدارسازی، پیرسازی) تا دماهایی از °C 427 تا 816 (°F 1500-800) به آلفا استحاله گردد.
مقادیر نسبی آلفای اولیه (که در عملیات آنیل کاری انحلالی دمابالا موجود است)، بتای باقیمانده و آلفای مارتنزیت تابعی از ترکیب شیمیایی و عملیات گرمایی اولیه و نیز تابعی از پیشینه فراوری مکانیکی انجام شده هستند. یکی از مقاصد اصلی فرآوری آلیاژهای تیتانیوم –که در فصل 5 به آن پرداخته شد- کنترل میکروساختار و در نتیجه کنترل خواص است.
استحکام کششی، استحکام خستگی و چقرمگی و نیز مقاومت خزشی، همگی در قطعات فورج شده بهتر از قطعات ریختگی، پودر یا دیگر شکل های کارشده هستند. انجام کار مناسب روی آلیاژهای آلفا- بتای تیتانیوم، میکروساختار را در دمای کاری قادر می سازد که همگن تر باشد در حالیکه هرگونه مورد غیرعادی میکروساختاری نظیر شکل 12-10 و 12-11 از بین می روند یا از تشکیل آنها جلوگیری می شود.
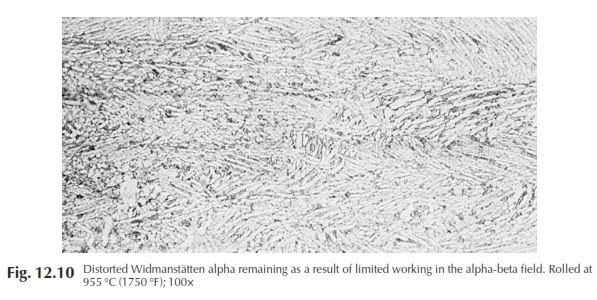
شکل 12-10 آلفای ویدمن اشتاتن دچار اعوجاج شده باقیمانده در نتیجه کار محدود در حوزه آلفا- بتا. نوردشده در °C 955 (°F 1750)؛ x 100.
تاثیرات فرآوری پیشین بر میکروساختار کاملا متغیر است. کار گرم در منطقه آلفا به علاوه بتا برای ایجاد میکروساختار مناسب نشان داده شده در شکل 12-12 مربوط به آلیاژ آلفا- بتای Ti-6Al-4V لازم است. اگر کار گرم روی فازهای آلفا به علاوه بتا محدود شود، میکروساختارهایی نظیر شکل 12-10 رخ خواهند داد. همان طور که بوضوح می توان مشاهده کرد، پلاکت های ویدمن اشتاتن کاملا دچار اعوجاج شده اند اما هنوز شکسته نشده اند. این شرایط به طور ویژه برای چقرمگی شکست مخرب است هرچند که می تواند بر انتشار ترک خستگی (FCP) تاثیر بگذارد.
هنگامی که آلیاژ Ti-6Al-4V پس از گرمایش در منطقه بتا به طور نادرستی فرآوری شود، فاز آلفا می تواند بطور ترجیحی در راستای دانه های اولیه بتا تشکیل شود. کار داغ گسترده ای برای شکستن این ساختارها لازم است. نمونه ای از آلفای مرزدانه ای که به طور کامل شکسته نشده در شکل 12-11 نشان داده شده است. چون ترکها تمایل به انتشار در فصل مشترک ها یا نزدیک آنها دارند، این نوع از ساختار می تواند موجب ایجاد موقعیت برای آغاز ترک و انتشار آن و در نتیجه، منجر به گسیختگی پیش از موعد شود.
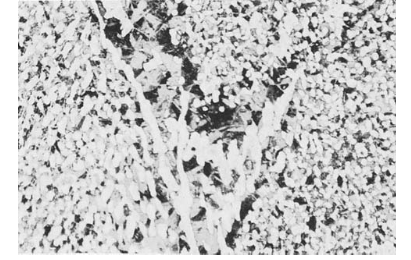
شکل 12-11 بقایای آلفای مرزدانه ای که بوسیله فورج کاری به دلیل تبرید نامناسب از ناحیه بتا دچار شکست نشده است. نورد شده در °C 940 (°F 1725)؛ x 250
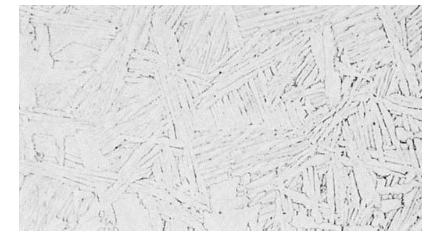
شکل 12-12 میکروساختار آلیاژ تیتانیوم آلفا- بتای Ti-6Al-4V عملیات حرارتی انحلالی شده در نزدیکی تحول بتا. °C 1010 (°F 1850)، 1 ساعت، تبرید در محفظه؛ x 500
کنترل میکروساختاری با استفاده از ترکیب هایی مناسب از کار گرم و عملیات حرارتی انجام می شود. عملیات حرارتی صرف برای تبدیل ساختار ویدمن اشتاتن به شکل هم محور کافی نیست در نتیجه، عملیات حرارتی به تنهایی به کار نمی رود مگر اینکه یک ساختار استحاله شده مطلوب باشد. ریزسازی دانه را نمی توان با عملیات حرارتی بدست آورد و پس از انجام یک استحاله بتا به آلفا بعلاوه بتا، چرخه های اضافی (آلفا بعلاوه بتا به بتا به آلفا بعلاوه بتا) هیچ تاثیری بر بافت کریستالوگرافی پایه ندارند هرچند ساختار ممکن است در نتیجه رشد دانه بتا، درشت شود. جدول 8-1، خلاصه ای از عملیاتهای حرارتی به کار رفته برای آلیاژهای آلفا- بتای تیتانیوم را ارائه می دهد.
توسعه خواص
هنگامی که آلیاژهای تیتانیوم آلفا- بتا در ناحیه بالایی آلفا- بتا تحت عملیات حرارتی قرار گرفته و سپس سرد می شوند، ساختار حاصل به دلیل وجود آلفای اولیه گلبولی (هم محور) در زمینه بتای استحاله شده (پلاکتی)، هم محور نامیده می شود. هنگامی که یک ساختار بتای 100 درصد استحاله شده با تبرید از بالای تحول بتا حاصل می شود، ساختار را می توان سوزنی یا سوزنی شکل نامید. جدول 12-4 مزایای استحکام و معایب مربوط به هر دو نوع ساختار را فهرست می کند. جدول 12-5 به طور بارزی نشان می دهد که استحکام تسلیم بالاتری بوسیله ساختارهای هم محور ایجاد می شود. جدول 12-5 نیز نشان می دهد چقرمگی بهتر مشخصه ساختارهای استحاله شده یا سوزنی است.
به طور کلی، آلیاژهای آلفا- بتا درست زیر تحول بتا آنیل کاری می شوند تا بیشینه ای از بتای سوزنی استحاله شده با حدود 10 درصد آلفای هم محور موجود باشد. برخی آلیاژهای تیتانیوم – برای نمونه Ti-6Al-2Sn-4Zr-2Mo- تحت عملیات های حرارتی بتا برای ارتقای مقاومت خزشی دمابالا قرار می گیرند. (قطعات ریختگی و محصولات پودری را می توان تحت یک آنیل کاری بتا نیز قرار داد تا ساختار بشکند هرچند برای بهینه سازی استحکام خزشی ضروری نیست.)
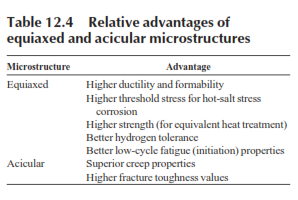
جدول 12-4 مزایای نسبی میکروساختارهای هم محور و سوزنی
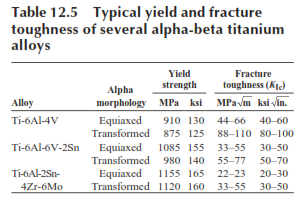
جدول 12-5 چقرمگی شکست و استحکام تسلیم مربوط به برخی آلیاژهای تیتانیوم آلفا- بتا
قابلیت سخت گردانی آلیاژ آلفا-بتا
در قطعات واقعی، ساختار آلیاژهای تیتانیوم آلفا- بتا نه تنها با اینکه چقدر کار انجام می شود و در چه دمایی نزدیک به تحول بتا، آلیاژ فراوری می شود بلکه با اندازه مقطع قطعه نیز تحت تاثیر قرار می گیرد. بطور ایده آل، آلیاژها باید دارای قابلیت سخت گردانی خوبی باشند که عبارتست از قابلیت حصول نرخ های تبرید مطلوب و میکروساختارهای مربوطه در مقاطع نسبتا نازک. آلیاژهای آلفا- بتای فراوانی هستند که قابلیت سخت گردانی خوبی ندارند. Ti-6Al-4V دارای قابلیت سخت گردانی کافی برای عملیات حرارتی شدن موثر تا رسیدن به سطح کاملی از خواص در مقاطعی با ضخامت کمتر از mm 25 (in. 1) است. مقاطع ضخیم تر را می توان تحت عملیات حرارتی قرار داد اما نواحی مرکزی به میکروساختار دلخواه نخواهند رسید و در نیتجه سطح مطلوبی از خواص بهینه ممکن است حاصل نشود.
برای آلیاژهای آلفا- بتا با قابلیت سخت گردانی کم، نرخ های تبرید موثر برای حصول خواص بهینه را می توان به شدت کاهش داد. مقاطع ضخیم می توانند طوری رفتار کنند که انگار در کوره سرد شده اند درحالیکه مقاطع نازکتر در دمای اتاق، میکروساختاری می توانند نشان دهند که مشخصه تبرید سریع است. تبرید سریع، بطور کلی موجب ساختاری ظریفتر و خواصی بهتر می شود، در نتیجه، مقاطع ضخیم دارای استحکام های کششی کمتری نسبت به مقاطع نازکتر هستند. تاثیرات تغییر نرخ تبرید را می توان در جدول 12-6 برای آلیاژ Ti-6Al-4V دید. مشاهده می شود که تبرید در کوره موجب استحکام کمتری نسبت به کوئنچ در آب می شود.
جدول 12-6 عملیات های گرمایی دمابالا را نیز نشان می دهد. در اینجا، دمایی که به تحول بتا نزدیک تر اما کمتر از آن است موجب استحکام های تسلیم بهتری نسبت به عملیاتی پائینتر در محدوده دمایی آلفا- بتا می شود.
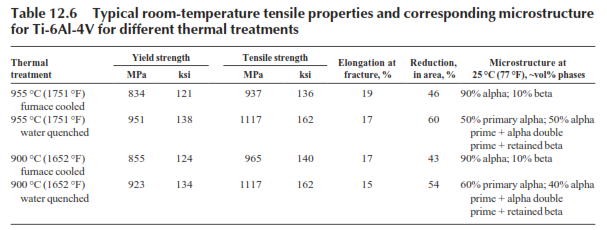
جدول 12-6 خواص کششی در دمای اتاق و میکروساختار متناظر مربوط به Ti-6Al-4V برای عملیات های گرمایی مختلف
پیرسازی و پایداری در آلیاژهای آلفا- بتا
یکی از نکات کمتر فهمیده شده در رفتار آلیاژهای تیتانیوم آلفا- بتا، رفتار پیرسازی آنهاست. به جز چند استثناء، آلیاژهای تیتانیوم به شیوه متداول که در آن یک ترکیب بین فلزی مستحکم و ثانویه تشکیل می شود و زمینه را با پراکندگی خود مستحکم می کند، پیرسازی نمی شوند.
پراکندگی در پیرسازی آلیاژهای آلفا- بتا ایجاد می شود اما تصور می شود که در آلفا یا آلفاپریم مارتنزیتی، بتا پراکنده شده باشد. بتا از نظر ماهیتی، با درنظرگیری استحکام، متفاوت از آلفا نیست. اما تاثیرگذاری اصلی استحکام دهی در آلیاژهای تیتانیوم در تعداد و ریزسازی مرزهای فاز آلفا- بتا به نظر می رسد. آنیل کاری و تبرید سریع که مرزهای آلفا- بتای مربوط به یک مقدار آلفای اولیه ثابت را بیشینه می کنند علاوه بر پیرسازی- که می تواند موجب ساختار اضافی در مرز شود- می توانند به طور محسوسی استحکام آلیاژ را افزایش دهند (جدول 12-7).
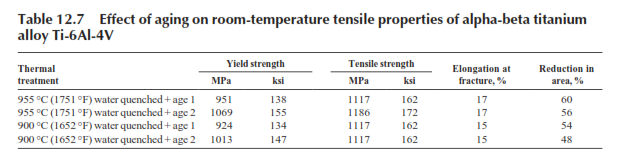
جدول 12-7 تاثیر پیرسازی بر خواص کششی در دمای اتاق مربوط به آلیاژ تیتانیوم آلفا- بتای Ti-6Al-4V
شایان ذکر است که به دلیل تغییرات در دمای عملیات انحلالی، استحکام مربوط به آلیاژ Ti-6Al-4V ممکن است تا حدود 10 درصد تغییر کند درحالیکه داکتیلیته بدون تغییر باقی می ماند. همچنین، می تواند یک تغییر اندک در استحکام پس از عملیات پیرسازی وجود داشته باشد. کلید پاسخ به پیرسازی، قابلیت تبرید همه موقعیتهای مقطع برای ایجاد یک ساختار مارتنزیتی ریز قبل از پیرسازی است. بخش " قابلیت سخت گردانی آلیاژ آلفا- بتا" را ببینید.
پیرسازی آلیاژهای آلفا- بتای تیتانیوم را می توان برای پایدارسازی آلیاژ در حین سرویس دهی در برابر استحاله بیشتر مارتنزیت ناپایدار و بتای باقیمانده به کار برد. در حالیکه پیرسازی حقیقی در دماهایی در محدوده °C 593-538 (°F 1100-1000) تمایل به رخ دادن دارد، پایدارسازی می تواند در همان نقطه یا تا °C 38 (°F 100) رخ دهد.
خواص طولی در مقابل خواص عرضی
دیگر عامل موثر درباره استحکام دهی آلیاژهای تیتانیوم، تاثیر جهت تست است. بافت و تاثیرات کار مکانیکی ساختار بویژه در میله، ورق ضخیم یا نازک می توانند محسوس باشند. جدول 12-8 تاثیر جهت تست را بر خواص ورق آلیاژ Ti-6Al-2Sn-4Zr-6Mo نشان می دهد. تفاوت های محسوسی با تغییر جهت تست بدست می آیند.
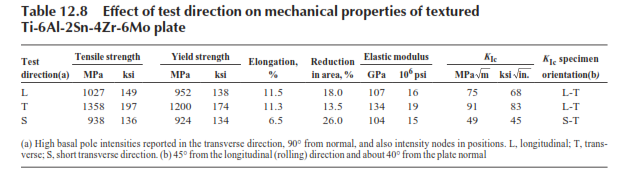
جدول 12-8 تاثیر جهت تست بر خواص مکانیکی ورق بافت دار Ti-6Al-2Sn-4Zr-6Mo
آلیاژهای بتا
اگر آلیاژی دارای مقادیر کافی عنصر آلیاژ پایدارساز بتا برای حفظ فاز بتا بدون استحاله به مارتنزیت در کوئنچ تا دمای اتاق باشد، آن آلیاژ، آلیاژ بتا درنظر گرفته می شود. تعدادی از آلیاژهای تیتانیوم (جدول 2-2 را ببینید) دارای مقدار بیشتری از این مقدار کمینه از افزودنی آلیاژی پایدارساز بتا هستند. آلیاژهای دارای مقادیر زیاد پایدارساز بتا، آلیاژهایی نظیر Ti-3Al-8V-6Cr-4Mo-4Zr (Beta-C) و Ti-15V-3Cr-3Al-3Sn هستند. آلیاژهای بتای غنی از عنصر حل شونده، گاهی به صورت آلیاژهای آلفا- بتای غنی از بتا طبقه بندی می شوند و این دسته شامل Ti-10V-2Fe-3Al و آلیاژهای انحصاری نظیر Ti-17 (Ti-5Al-2Sn-2Zr-4Mo-4Cr) و Beta CEZ (Ti-5Al-2Sn-4Zr-4Mo-2Cr) می شود.
نکاتی درباره ساختارها و استحکام دهی
به معنای دقیق کلمه، هیچ آلیاژ بتای حقیقتا پایداری وجود ندارد زیرا حتی بتایی با بیشترین مقدار عناصر آلیاژی نیز در نگهداری در دماهای بالا، بسته به دما، زمان و ترکیب آلیاژی، شروع به رسوب امگا، آلفا، Ti3Al یا سیلیسایدها خواهد کرد. همه آلیاژهای بتا دارای مقدار کمی آلومینیوم- یعنی پایدارساز بتا- برای استحکام دهی آلفایی هستند که ممکن است پس از عملیات حرارتی وجود داشته باشد. ترکیب آلفای در حال رسوب ثابت نیست و به دمای عملیات حرارتی بستگی دارد. هرچه دما در منطقه فازی آلفا- بتا بالاتر باشد، مقدار آلومینیوم آلفا بیشتر است.
برای این آلیاژها، فرآوری معمولا دارای محدودیت های بیشتری نسبت به دیگر انواع آلیاژها (آلفا و آلفا- بتا) است. برای آلیاژهای با مقدار کمتر پایدارساز بتا نظیر Ti-10V-2Fe-3Al ، فرایند ترمومکانیکی برای ترکیب های بدست آمده از خواص مهم است زیرا این فرآیند دارای تاثیر زیادی بر میکروساختار نهایی و استحکام کششی نهایی و چقرمگی شکست حاصل است. کنترل دقیق فرآوری ترمومکانیکی (TMP) تا حدی از اهمیت کمتری در آلیاژهای با مقدار پایدارساز بتای بسیار بیشتر نظیر Ti-3Al-8V-6Cr-4Mo-4Zr و Ti-15V-3Cr-3Al-3Sn برخوردار است. در این آلیاژها، میکروساختار نهایی- آلفای رسوب کرده در فاز بتا- چنان ریز است که کنترل میکروساختار از طریق TMP چندان موثر نیست. در مورد این آلیاژها، پارامترهای عملیات های حرارتی پیرسازی از جمله ترتیب و دما، مهمتر هستند. راه حل، حصول یک سطح یکنواخت از رسوب گذاری است. با یک ترتیب پیرسازی بالا- پائین، این سطح یکنواخت را می توان به دست آورد یا با کارسرد پسماند یا کار گرم که احتمالا یک ترتیب پیرسازی بالا- پائین است. در هنگام انجام کار سرد قبل از پیرسازی روی آلیاژهای بتای با مقدار عناصر آلیاژی زیاد نظیر Beta C، استحکام بالایی را با داکتیلیته مناسبی می توان به دست آورد زیرا کار سرد موجب ایجاد رسوبات ریزتر و یکنواخت تر می شود.
اما TMP را باید برای ایجاد یک میکروساختار یکنواخت در کل مقطع ماده کنترل کرد و علاوه بر آن، بوسیله عملیات حرارتی، باید از وقوع گسترده آلفای مرزدانه ای یا یک ناحیه عاری از رسوب در نزدیکی مرزدانه جلوگیری کرد.
در مورد آلیاژهای غنی از عنصر حل شونده نظیر Ti-10V-2Fe-3Al، اهداف میکروساختاری از ساختارهای کاملا استحاله شده و بتای پیرسازی شده تا مقادیر کنترل شده ای از آلفای اولیه کشیده در زمینه بتای پیرسازی شده- که با آلفای ثانویه (پیرشده) بینهایت ریز مشخص می شود- متغیر هستند. میکروساختار یاد شده اخیر برای بیشتر کاربردهای هوافضایی ترجیح داده می شود و بیشترین کاربرد تجاری از این آلیاژ را در قطعات فورج شده می توان دید.
ارتباط بین خواص و ساختارها
آلیاژ آلفا- بتای Ti-6Al-4V
در شرایط آنیل شده، آلیاژ آلفا- بتای Ti-6Al-4V، استحکام آنیل شده خود را از چند منبع می گیرد: منبع اصلی، آلیاژسازی جانشینی و بین نشینی با عناصر در محلول جامد در فازهای آلفا و بتا می باشد. اکسیژن، نیتروژن، هیدروژن و کربن عناصر بین نشینی هستند که معمولا استحکام را افزایش و داکتیلیته را کاهش می دهند. آلومینیوم، مهمترین استحکام دهنده به صورت جانشینی در محلول جامد است. تاثیر آن بر استحکام خطی است. دیگر منایع کم اهمیت تر استحکام دهی عبارتند از استحکام دهی به صورت بین نشین در محلول جامد، تاثیرات اندازه دانه، تاثیرات فاز ثانویه (بتا)، نظم دهی در آلفا، پیرسختی و تاثیرات بافت کریستالوگرافی.
آلومینیوم در Ti-6Al-4V منجر به ایجاد مقداری تمایل به نظم بخشی در فاز آلفا می شود. محصول نظم دهی شده عبارتست از Ti3Al و آلفا-2. نظم بخشی در فاز آلفا، احتمالا MPa 35-15 (ksi 5-2) به استحکام Ti-6Al-4V استاندارد و کمتر از این مقدار به استحکام گرید ELI کمک می کند. همچنین به نظر می رسد نظم بخشی، چقرمگی را تضعیف می کند.
تاثیر بافت کریستالوگرافی، وارد کردن جهت در معادله استحکام است. نسبت به محور هگزاگونال در آلفا، استحکام (و مدول) در جهت موازی بالا و در جهت نرمال، پائین است. چون فرآیندهای کار روی فلز تمایل به ایجاد جهت گیری های کریستالوگرافی ترجیحی در دانه های آلفا دارند، در بیشتر شکل های محصول، استحکام تبدیل به یک مقدار ناهمسانگرد می شود. این مشخصه را می توان با فرآوری درست کمینه نمود و به ندرت از اهمیت مشخصی برخوردار است. در برخی مواقع، این موضوع می تواند یک مزیت باشد.
در دمای اتاق، Ti-6Al-4V حدود 90 درصد حجمی آلفا دارد و در نتیجه، فاز آلفا در خواص فیزیکی و مکانیکی آلیاژ غالب است. اما، تاثیرات کلی پیشینه فرآوری و عملیات حرارتی روی میکروساختار پیچیده هستند. میکروساختار به پیشینه فرآوری و عملیات حرارتی بستگی دارد و میکروساختاری که استحکام استاتیک بیشینه و داکتیلیته را ترکیب می کند لزوما میکروساختاری نیست که موجب چقرمگی شکست، استحکام خستگی یا مقاومت در برابر رشد ترک بهینه شود.
از آنجا که فاز بتای موجود در آلیاژ Ti-6Al-4V را می توان با عملیات حرارتی از نظر مقدار و ترکیب کنترل کرد، آلیاژ به عملیات حرارتی پاسخ می دهد. واکنش تبدیل بتا به آلفا بعلاوه بتا در دمای کم منجر به استحکام زیاد می شود. راه حل آن، کوئنچ از بالای منطقه فازی آلفا بعلاوه بتا و سپس پیرسازی در دمای کمتر می شود. عملیات حرارتی استحکام دهی از گرمایش به مدت 1 ساعت در °C 955 (°F 1750) و کوئنچ در آب و به دنبال آن، گرمایش به مدت 4 ساعت در °C 540 (°F 1000) و تبرید در هوا تشکیل می شود. اما پاسخ به عملیات حرارتی بوسیله دو عامل محدود می شود: مقدار کم بتا در Ti-6Al-4V و اندازه مقطع (بخش قابلیت سخت گردانی آلیاژ آلفا- بتا را در بالا ببینید). عامل اول موجب ایجاد یک سقف ذاتی برای افزایش استحکام دهی یعنی مقدار MPa 280 (ksi 40) در ماده نازک می شود. عامل دوم به عمق سخت شدگی مربوط می شود زیرا Ti-6Al-4V در مقاطعی با ضخامت بیش از mm 25 (in. 1) قابلیت سختگردانی موثری ندارد. در نتیجه، Ti-6Al-4V پرکاربردترین آلیاژ در حالت آنیل شده است.
در هنگامی که آلیاژ Ti-6Al-4V پس از گرمایش در ناحیه بتا به طور نادرست فرآوری گردد، فاز آلفا می تواند در راستای دانه های اولیه بتا بطور ترجیحی تشکیل شود. کار داغ گسترده برای شکستن چنین ساختارهایی لازم است. چون ترکها به انتشار یافتن در فصل مشترکها یا در نزدیکی آنها تمایل دارند این نوع ساختار می تواند موجب ایجاد موقعیت هایی برای آغاز ترک و انتشار آن و در نتیجه گسیختگی پیش از موعد شود.
دیگر آلیاژهای آلفا- بتا
دو آلیاژی که در دسته آلفا- بتا با استحکام بالا قرار می گیرند عبارتند از Ti-6Al-6V-2Sn که در بدنه هواپیما بکار می رود و Ti-6Al-2Sn-4Zr-6Mo که در موتورهای جت بکار می رود. هر دو آلیاژ مستحکم تر بوده و نسبت به Ti-6Al-4V با سهولت بیشتری تحت عملیات حرارتی قرار می گیرند. این مشخصات از استحکام دهی بیشتر حاصل از محلول جامد است که بوسیله قلع و زیرکونیوم ایجاد می شوند. این دو عنصر تاثیرات نسبتا کمی بر دمای استحاله دارند و مقادیر بیشتری از فاز بتا را تشکیل می دهند. فاز بتا حاصل از افزودن مقادیر بیشتری وانادیوم و مولیبدن است. (وانادیوم و مولیبدن پایدارسازهای بتا هستند.) آلیاژ Ti-6Al-6V-2Sn دارای پایدارسازهای مس و آهن است که مجموع آنها تا 1.4 درصد وزنی برای ارتقای استحکام و پاسخ به پیرسازی به کار می رود. آلیاژ Ti-6Al-2Sn-4Zr-6Mo نیز نه تنها در دماهای کم بلکه در دماهای نسبتا بالا از °C 425 تا 480 (°F 900-800) مفید است. این آلیاژ، استحکام کششی بالا را با مقاومت خزشی خوب ترکیب می کند. فاز آلفا در این آلیاژها تمایل به نظم گیری آسانتری نسبت به آلیاژ Ti-6Al-4V دارد. بعلاوه، پلاکت های آلفای استحاله شده در Ti-6Al-2Sn-4Zr-6Mo نسبت به Ti-6Al-4V باریک تر بوده و تشکیل بسته های کوچک از پلاکت های موازی احتمال کمتری دارد. برای آلیاژهای Ti-6Al-6V-2Sn و Ti-6Al-2Sn-4Zr-6Mo، در شرایط معمول مارتنزیت تشکیل نمی شود. آلفا در این آلیاژها فاز غالب است اما نسبت به Ti-6Al-4V این برتری کمتر است. متالورژی این آلیاژها بسیار شبیه به Ti-6Al-4V است.
آلیاژهای آلفا و شبه آلفا
آلیاژ Ti-8Al-1Mo-1V در دسته آلیاژهای شبه آلفاست. این آلیاژ دارای بالاترین مدول و کمترین چگالی در بین آلیاژهای تجاری تیتانیوم است. آلیاژ Ti-6Al-2Sn-4Zr-2Mo-0.08Si یکی از مقاوم ترین آلیاژها در برابر خزش است و دارای ترکیبی عالی از استحکام کششی، استحکام خزشی، چقرمگی و پایداری در دمای بالا می باشد که مربوط به کاربردهای بلندمدت در دماهایی تا °C 425 (°F 800) می شود. آلیاژ Ti-6Al-2Sn-4Zr-2Mo را می توان با افزودن سیلیسیم تا 0.1 درصد اصلاح کرد و در هنگام آنیل کردن بتا (یعنی آنیل کردن با گرمایش در بالاتر از دمای استحاله)، آلیاژ اصلاح شده حاصل برای سالهای طولانی، دارای یکی از بالاترین استحکام های خزشی و ظرفیت های دمایی در آلیاژهای تجاری تیتانیوم در ایالات متحده بوده است. هر یک از این آلیاژها به نظم گیری در فاز آلفا به طور آسان تری نسبت به Ti-6Al-4V تمایل دارد. در هر یک از این آلیاژها، مارتنزیت به طور ساده تری نسبت به Ti-6Al-4V تشکیل می شود.
بنابراین، این آلیاژها معمولا در حالت عملیات انحلالی شده و پایدارسازی شده به کار می روند. در دماهای بالا، پیرکرنشی حاصل از آلومینیوم، سیلیسیم و قلع و شاید اکسیژن و زیرکونیوم در مقاومت خزشی این مواد سهم دارد. فاز آلفا بیشترین سهم را در خواص این آلیاژها نسبت به Ti-6Al-4V دارد. متالورژی آلیاژهای شبه آلفا شبیه به Ti-6Al-4V است.
آلیاژهای بتا
هیچ آلیاژ تک فاز بتایی با کاربردپذیری گسترده ای مانند Ti-6Al-4V وجود ندارد. در نتیجه، آلیاژهای خاص بتا به دلیل اینکه خواص آنها مناسب با یک کاربرد خاص است بکار می روند. بطور کلی، آلیاژهای بتا به دلیل کارپذیری، مقاومت به خوردگی و قابلیت انجام عملیات حرارتی مقاطعی با اندازه بزرگتر نسبت به آلیاژهای آلفا- بتا مورد استفاده قرار می گیرند. آلیاژهای بتا و آلفا- بتای غنی از بتا موجب فرصتی برای مناسب سازی ترکیب های استحکام و چقرمگی برای یک کاربرد خاص می شوند. یعنی، می توان به استحکام متوسط با چقرمگی بالا یا استحکام بالا با چقرمگی متوسط دست یافت. این موضوع به طور کلی برای دیگر انواع آلیاژهای تیتانیوم ممکن نیست زیرا نمی توان این آلیاژها را در گستره زیادی تحت عملیات حرارتی قرار داد. آلیاژهای بتا نیز به داشتن چگالی های بالاتر و مدولهای الاستیک کمتر نسبت به آلیاژهای آلفا یا آلفا- بتا تمایل دارند.
یک پایگاه داده برای آلیاژهای تیتانیوم بتا ایجاد شده که با Ti-13V-11Cr-3Al شروع شده و با تلاشهای جدیدی درباره Ti-10V-2Fe-3Al به عنوان یک آلیاژ فورج شده و Ti-15V-3Al-3Sn-3Cr به عنوان یک آلیاژ به شکل ورق نازک ادامه یافته است. آلیاژ Ti-15V-3Al-3Sn-3Cr نیز به صورت ریخته گری بعلاوه HIP و HIP پودر فرآوری شده است. دیگر آلیاژهای بتا نیز ارزیابی شده اند؛ Ti-13V-11Cr-3Al یکی از چند آلیاژ به جز Ti-10V-2Fe-3Al است که دارای پایگاه داده ای منتشر شده قابل توجهی است.
Ti-10V-2Fe-3Al یک آلیاژ شبه بتای با عمق سختی زیاد شبه پایدار است که می توان آن را تا دامنه ای از سطوح استحکام بعلاوه چقرمگی شکست عالی به صورت ترمومکانیکی فرآوری نمود. فرایند فورج کاری ترجیحی برای برآورده سازی معیارهای خواص مکانیکی عبارتست از استفاده از فورج کاری کنترل شده بتا و به دنبال آن، فورج کاری کنترل شده آلفا- بتا. این ترتیب، همراه با عملیات حرارتی نهایی موجب ترکیب بهینه ای از استحکام، چقرمگی، داکتیلیته، خستگی و خواص مرتبط با شکست می شود. Ti-10V-2Fe-3Al را می توان بطور متداول تحت فورج کاری آلفا- بتا و عملیا حرارتی قرار داد. با چنین فرآیندهای متداولی، آلیاژ به استحکام و خواص خستگی بالا و داکتیلیته عالی بالا می رسد اما به طور همزمان، چقرمگی و خواص مرتبط با شکست ضعیفی به دست می آیند.
با توجه به قابلیت سخت گردانی بالاتر آلیاژهای بتا نسبت به آلیاژهای آلفا- بتا، ادعا شده است که قطعات فورج شده Ti-10V-2Fe-3Al به استحکام های معادلی با اندازه مقطع بزرگتر از آلیاژ Ti-6Al-4V آلفا- بتا دست پیدا کرده اند. برخی آلیاژهای بتای با اهمیت در جدول 12-9 نشان داده شده اند.
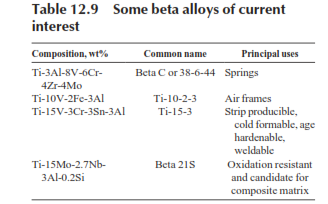
جدول 12-9 برخی آلیاژهای بتای با اهمیت
خواص استاتیک آلیاژها
خواص کششی و گسیختگی ناشی از خزش
سطح خواص مربوط به محصولات اولیه از آلیاژ تیتانیوم در جدول 12-10 فهرست شده اند. تاثیرات دما بر استحکام برای برخی آلیاژها در جدول 12-11 نشان داده شده اند. داده های مربوط به تیتانیوم غیرآلیاژی در جدول 12-11 آورده شده اند تا نشان دهند که این آلیاژها نه تنها دارای استحکام در دمای اتاق بالاتر هستند بلکه درصدهای بیشتری از آن استحکام را در دماهای بالا حفط می کنند.
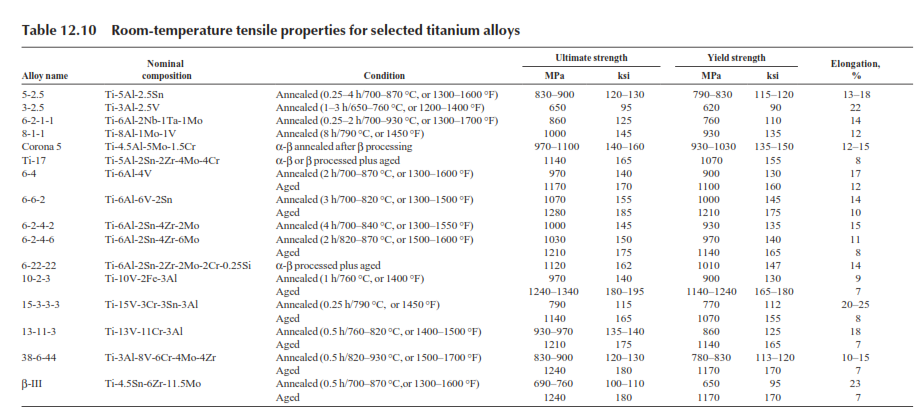
جدول 12-10 خواص کششی در دمای اتاق مربوط به آلیاژهای تیتانیوم برگزیده
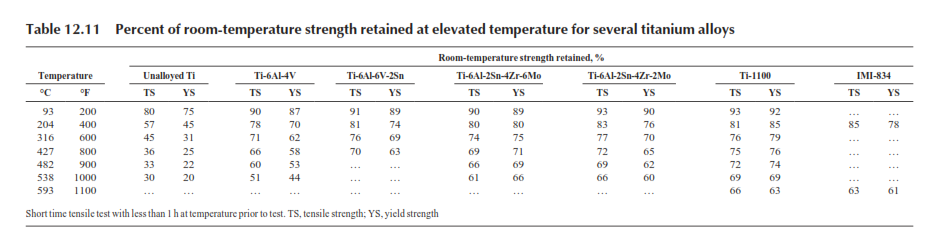
جدول 12-11 درصد استحکام در دمای اتاق باقیمانده در دمای بالا برای برخی آلیاژهای تیتانیوم
بر حسب عملیات های حرارتی اصلی به کار رفته برای تیتانیوم، آنیل کاری بتای آلیاژهای آلفا- بتا، استحکام را به میزان MPa 35 تا 100 (ksi 15-5) بسته به اندازه دانه اولیه، بافت کریستالوگرافی متوسط و جهت انجام تست، کاهش می دهد. عملیات انحلالی و پیرسازی را می توان برای ارتقای استحکام به ازای از دست دادن چقرمگی شکست در آلیاژهای دارای مقدار کافی از پایدارساز بتا (یعنی 4 درصد وزنی یا بیشتر) به کار برد.
استحکام های کششی و استحکام های خزشی 0.1 درصدی به عنوان توابعی از دمای برخی آلیاژهای برگزیده، به ترتیب در شکلهای 12-13 و 12-14 نشان داده شده اند.
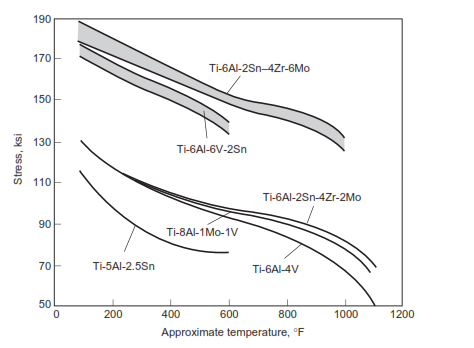
شکل 12-13 مقایسه استحکام های کششی نهایی آلیاژهای تیتانیوم برگزیده به عنوان تابعی از دما
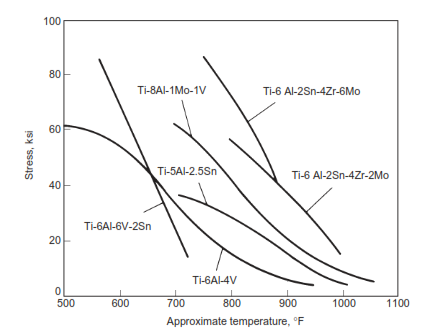
شکل 12-14 مقایسه استحکام های خزشی 0.1 درصد 150 ساعته برای آلیاژهای تیتانیوم برگزیده
چقرمگی شکست
تفاوت های محسوسی در چقرمگی شکست آلیاژهای تیتانیوم وجود دارد اما هم پوشانی قابل توجهی نیز در خواص این آلیاژها وجود دارد. جدول 12-5 مثال هایی از دامنه های چقرمگی شکست کرنش صفحه ای برای آلیاژهای تیتانیوم آلفا- بتا ارائه می دهد. از این داده ها، واضح است که ترکیب آلیاژ پایه بر ارتباط بین استحکام و چقرمگی اثر می گذارد. از جدول 12-5، همان طور که قبلا ذکر شد، واضح است که میکروساختارهای استحاله شده می توانند به شدت چقرمگی را ارتقا دهند در حالیکه فقط به میزان کمی از استحکام می کاهند. آشکار است که چقرمگی به TMP برای ایجاد ساختار دلخواه وابسته است. رفتار چقرمگی شکست قطعات فورج شده از جنس آلیاژ تیتانیوم بتای غتی از عنصر حل شونده (Ti-10V-2Fe-3Al) در جدول 12-12 و شکل 12-15 نشان داده شده است.
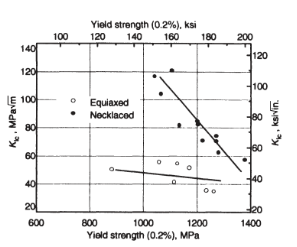
شکل 12-15 چقرمگی برحسب استحکام تسلیم آلیاژ تیتانیوم Ti-5Al-2Sn-4Zr-4Mo-2Cr فرآوری شده به دو ساختار مختلف
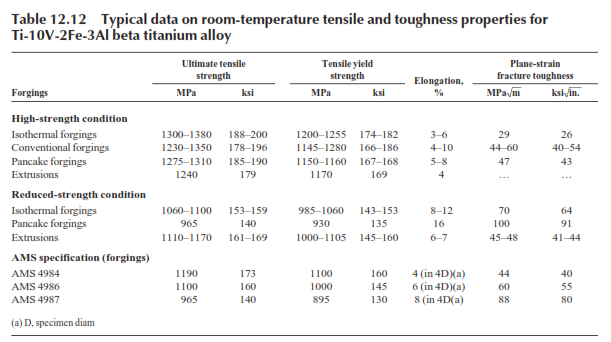
جدول 12-12 داده های مربوط به خواص کششی و چقرمگی برای آلیاژ تیتانیوم بتای Ti-10V-2Fe-3Al
چقرمگی شکست را در یک آلیاژ اسمی آلفا- بتا، می توان به میزان 2 یا 3 برابر تغییر داد. این امر را می توان با تغییر ترکیب، میکروساختار و بافت آلیاژ انجام داد. ممکن است از دست دادن برخی دیگر خواص دلخواه برای حصول چقرمگی شکست بالا ضروری باشد. چقرمگی شکست کرنش صفحه ای، KIC، از اهمیت خاصی برخوردار است زیرا اندازه ترک بحرانی ای که در آن رشد ناپایدار می تواند رخ می دهد متناسب با 2(KIC) است. استحکام در آلیاژهای تیتانیوم غالبا به ازای از دست دادن KIC به دست می آید.
اهداف میکروساختاری در آلیاژهای تیتانیوم بتا از ساختارهای کاملا استحاله شده، پیرسازی شده بتا تا مقادیر کنترل شده ای از فاز آلفای ممتد در زمینه پیرسازی شده بتا که به وسیله آلفای ثانویه بسیار ریز (پیرسازی شده) مشخصه یابی می شوند متغیر است. این مورد اخیر از دیدگاه چقرمگی برای بیشتر کاربردهای هوافضا ترجیح داده می شود. به نظر می رسد که مقدار بهینه ای از آلفای اولیه برای حصول چقرمگی بیشینه وجود داشته باشد. انجام TMP روی Ti-10V-2Fe-3Al موجب دستیابی به میکروساختار مطلوب نهایی بوسیله کنترل مورفولوژی فاز آلفا می شود. در سطوح متوسط استحکام- برای نمونه MPa 965 (ksi 140) و بیشتر- آلیاژهای بتا را برای دستیابی به مقادیر چقرمگی شکست بالاتر نسبت به مقادیر ممکن برای دیگر گونه ها (آلیاژهای آلفا و آلفا- بتا) می توان فراوری نمود. تاثیر ساختار بر چقرمگی به ازای کاهش استحکام در آلیاژهای غنی از عنصر حل شونده در شکل 12-15 نشان داده شده است. در این شکل KIC به ازای استحکام تسلیم برای آلیاژ Ti-5Al-2Sn-4Zr-4Mo-2Cr ارائه شده است. این شکل نشان می دهد که ساختار گردنبندی (یعنی با مرزدانه های بیشتر) ساختاری چقرمه تر در استحکام های تسلیم کمتر است.
در دامنه مجاز ترکیب شیمیایی مربوط به یک آلیاژ و گرید خاص تیتانیومی، اکسیژن مهمترین متغیر موثر در چقرمگی است. اساسا، اگر نیاز به چقرمگی شکست بالایی باشد، اکسیژن در سطحی اندک و دیگر موارد در سطحی متوازن باید حفظ شوند. کاهش نیتروژن مانند Ti-6Al-4V-ELI، نیز نشان داده شده اما تاثیر آن مانند تاثیر اکسیژن چندان قوی نیست.
بهبود KIC را می توان با ایجاد دو نوع اساسی از میکروساختارها بدست آورد:
-
- ساختارهای استحاله شده Ti-6Al-4V یا ساختارهای تا حد امکان استحاله شده چراکه چنین ساختارهایی موجب مسیرهای پیچ در پیچی می شوند.
-
- ساختارهای هم محور Ti-6Al-4V که عمدتا از آلفای بازرشدیافته ای که دارای چگالی کمی از نابجایی- نقص و غلظت کمی از نیتروژن و اکسیژن هستند تشکیل شده اند (این ساختارها اصطلاحا ساختارهای تبلور- آنیل نامیده می شوند).
به نظر می رسد ساختارهای استحاله شده عمدتا به دلیل اینکه شکست ها در چنین ساختارهایی باید در راستای مسیرهای پیچ در پیچ ترک فراوانی به پیش بروند، باید چقرمه باشند.
مطابق با کارهای انجام شده روی آلیاژهای آلفا- بتا، KIC متناسب با کسری از ساختار است که از بتا در آلیاژ، استحاله شده است. موضوع، ایجاد یک ساختار پیچیده بدون قواعد عملی مشخص است. به علاوه، ارتقای چقرمگی شکست در یک گام عملی- برای نمونه، فورج کردن یک بیلت- به قطعه فورج شده منتقل نمی شود. چون جوشها در Ti-6Al-4V دارای محصولات استحاله شده هستند می توان انتظار داشت که چنین جوشهایی دارای چقرمگی بالایی باشند. این موضوع در شکل 12-13 نشان داده شده است.
علاوه بر جوشکاری، عوامل فراوان دیگری نظیر محیط، نرخ تبرید در مقاطع بزرگ (یعنی قابلیت سخت گردانی که عاملی موثر بر ریزبودن ساختار است) و مقدار هیدروژن می توانند بر KIC موثر باشند.
خواص چرخه ای در آلیاژها
خستگی تیتانیوم غیرآلیاژی
خستگی، تخریب چرخه ای ظرفیت استحکام یک ماده است. آسیب خستگی به ترکیب آلیاژ، ساختار آلیاژ، عملیات سطحی، سطوح تنش و حالت اعمال تنش بستگی دارد. به چرخه های گسیختگی در دامنه کمتر از حدود 104 * 5 چرخه خستگی در چرخه کم (LCF) اطلاق می شود در حالی که گسیختگی های در تعداد چرخه تقریبی 106 یا بیشتر از آن، خستگی در چرخه بالا (HCF) نامیده می شوند. چرخه های خستگی را می توان بوسیله ابزارهای مکانیکی، ابزارهای گرمایی و ترکیبی از این دو یعنی ابزارهای ترمومکانیکی ایجاد کرد. این مورد اخیر بنام TMF شناخته می شود. خستگی ای که صرفا بطور گرمایی ایجاد گردد به عنوان خستگی گرمایی نامیده می شود. LCF و HCF نواحی خستگی غالب در آلیاژهای تیتانیوم هستند.
عمر خستگی در تیتانیوم غیرآلیاژی به اندازه دانه، سطح بین نشین و میزان کارسرد مطابق با شکل 12-16 بستگی دارد که در آن عنصر بین نشین، اکسیژن است. کاهش اندازه دانه در تیتانیوم غیرآلیاژی از μm 110 تا 6، حد خستگی چرخه ای را به میزان 107 چرخه یعنی 30 درصد بهبود می دهد. محدوده های HCF تیتانیوم غیرآلیاژی به مقادیر عنصر بین نشین و TYS و UTS بستگی دارند. نسبت حد خستگی HCF و TYS در دمای محیط تقریبا ثابت به نظر می رسد زیرا تغییرات TYS با مقدار عنصر بین نشین تغییر می کند اما یک وابستگی دمایی نشان می دهد. تاثیرات دما بر تیتانیوم غیرآلیاژی تاحدی به وسیله تیتانیوم آلیاژی گرید 2 (با مقدار آهن کم) در دو دما روی ناحیه 104*5 تا 107 چرخه ای مربوط به گسیختگی در شکل 12-17 نشان داده شده اند.
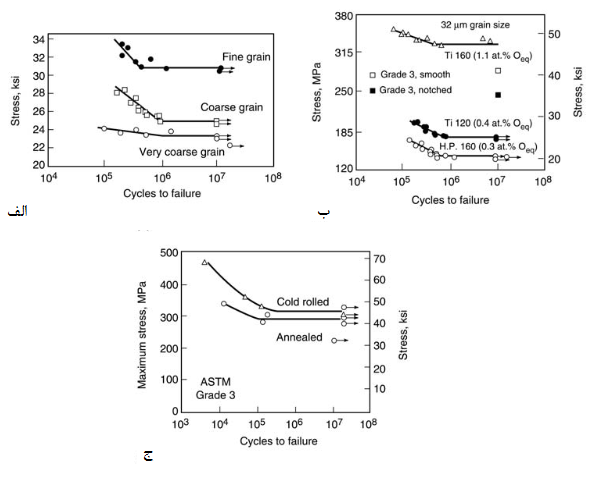
شکل 12-16 منحنی های نشان دهنده تنش بر حسب تعداد چرخه لازم تا شکست برای تیتانیوم خالص که با
الف- اندازه دانه ب- مقدار اکسیژن ج- کار سرد
تحت تاثیر قرار می گیرد.
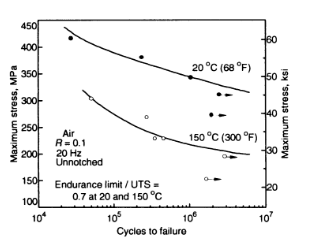
شکل 12- 17 منحنی های نشان دهنده تنش در دمای اتاق بر حسب تعداد چرخه لازم تا شکست برای تیتانیوم گرید 2 (0.03 درصد وزنی آهن) در دو دما.
UTS استحکام کششی نهایی
خستگی در آلیاژهای تیتانیوم. علاوه بر اندازه دانه آلفا، میزان پیرسازی و مقدار اکسیژن برای آلیاژهای شبه آلفا و آلیاژهای آلفا- بتا، خواص خستگی به شدت تحت تاثیر مورفولوژی و آرایش فازهای آلفا و بتا قرار می گیرند. در واقع، هرچند خواص استاتیک به همین مشخصات بستگی دارند، خستگی تیتانیوم (و چقرمگی) می توانند حتی به ساختار، بیش از خواص استاتیک وابسته اند.
پارامترهای مهم میکروساختار که بر خستگی آلیاژهای تیتانیوم موثرند عبارتند از اندازه دانه بتای اولیه یا اندازه کلونی آلفا و لایه های بتا و پهنای لایه های آلفا در میکروساختارهای کاملا لایه ای. شکل 12-18 منحنی های نشاندهنده تنش به ازای چرخه های لازم تا شکست را برای میکروساختارهای مختلف و گونه های مختلف آلیاژ تیتانیوم آلفا- بتای Ti-6Al-4V ارائه داده است. ساختارهای لایه ای از تجزیه استحاله ای فاز بتای دمابالا ناشی می شوند. هرچه لایه ها در فاز بتای استحاله شده ظریفتر باشند، آلیاژ از نظر خستگی استحکام بالاتری دارد (شکل 12-18 الف). هرچه اندازه دانه بتای اولیه کوچکتر باشد، اندازه کلونی قابل تحقق کوچکتر است.
مکان های جوانه زنی ترک برای ماده Ti-6Al-4V تست شده در شکل 12-18، در شکل 12-19 نشان داده شده اند. به دلیل مقدار بالای سیلیسیم (0.45 درصد وزنی) در یک آلیاژ مختلف یعنی آلیاژ Ti 1100 دمابالا استحکام بالا، می توان اندازه دانه بتای اولیه کوچکتر و اندازه کلونی لایه ای کوچکتری را به دست آورد. این ساختارها در استحاله یعنی در حین تبرید از دمای عملیات انحلالی یا دمای آنیل بتا در آلیاژ ایجاد می شوند. منحنی های نشان دهنده تنش به ازای چرخه های لازم تا شکست مربوط به Ti 1100 در شکل 12-20 نشان داده شده اند. کاهش اندازه دانه بتای اولیه در یک ساختار کاملا لایه ای (شکل 12-20 الف) و نیز کسر حجمی کمتر آلفای اولیه در ساختارهای دوپلکس (شکل 12-20 ب) موجب بهبود عمر خستگی در محدوده های LCF و HCF می شوند.
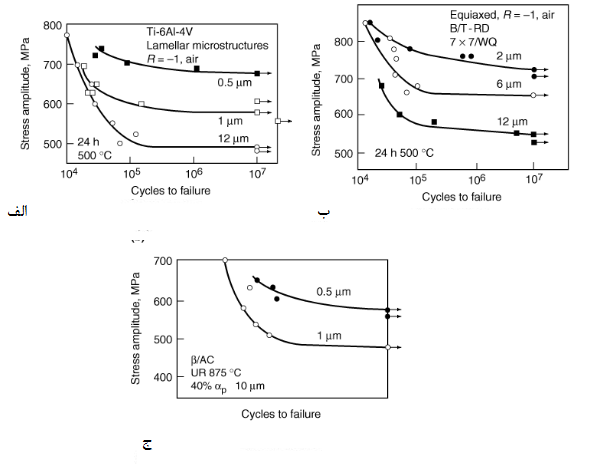
شکل 12-18 منحنی های نشان دهنده تنش در دمای اتاق برحسب تعداد چرخه لازم تا شکست برای آلیاژ تیتانیوم آلفا- بتای Ti-6Al-4V در شرایط مختلف
الف- ساختار کاملا لایه ای ب- ساختار کاملا هم محور ج- میکروساختار دوپلکس
در الف، پهنای لایه های آلفا محل مناقشه است، در ب- تاثیر اندازه دانه آلفا محل مناقشه است و در ج- پهنای لایه آلفا در مناقشه است.
توجه کنید که 1-R=؛ B/T-RD بافت قاعده ای/ عرضی، جهت نورد؛ WQ کوئنچ در آب؛ AC تبریدشده در هوا
با در نظرگیری انواع منحنی S-N، نتایج مطالعه LCF روی آلیاژ آلفا- بتا Ti-6Al-4V در شکل 12-21 نشان داده شده اند. همان طور که نشان داده شده است، زمان لازم برای نخستین ترک (در یک کرنش ثابت) با میکروساختار آلیاژ آلفا- بتا تغییر می کند. توجه کنید که زمان لازم برای شروع ترک با ساختاری که دارای مقادیر زیادی بتای استحاله شده اما هنوز دارای تقریبا 10 درصد آلفای اولیه است بهینه می شود. (اما باید توجه کرد که مقاومت در برابر گسترش ترک در ساختار فراوری شده دارای بتا باز هم بیشتر ماده دارای آلفاست.)
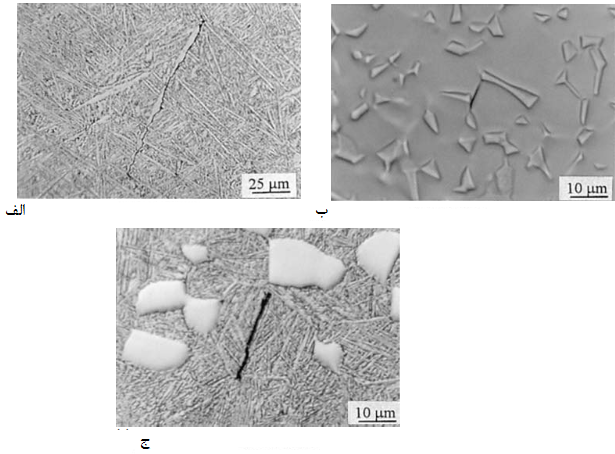
شکل 12-19 مکان های جوانه زنی ترک خستگی در آلیاژ آلفا- بتای Ti-6Al-4V.
الف- میکروساختار کاملا لایه ای. ب- میکروساختار کاملا هم محور ج- میکروساختار دوپلکس
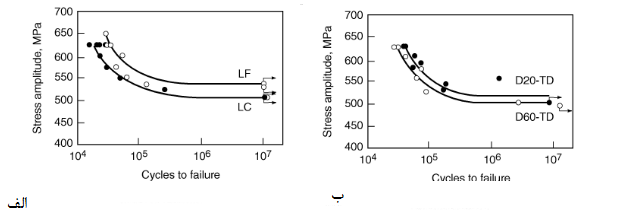
شکل 12-20 منحنی های نشان دهنده تنش برحسب چرخه لازم تا شکست (1- = R) برای آلیاژ تیتانیوم شبه آلفای Ti-1100.
الف- میکروساختارهای کاملا لایه ای که نشان دهنده تاثیرات اندازه دانه بتای اولیه است ب- میکروساختارهای دوپلکس که نشان دهنده دامنه تاثیرات مقدار آلفای اولیه است
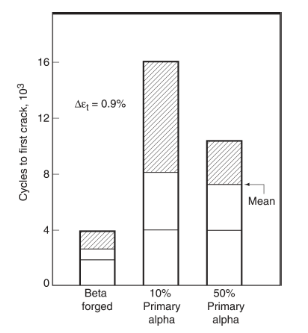
شکل 12-21 عمر خستگی در چرخه کم مربوط به آلیاژ تیتانیوم بتای Ti-6Al-4V با ساختارهای مختلف:
بتای فورج شده (100 درصد بتای استحاله شده)؛ 10 درصد آلفای اولیه ( بتای استحاله شده متوازن)؛ آلفای اولیه 50 درصدی
عمر خستگی آلیاژهای تیتانیوم کاملا در پاسخ به مقدار R آنها یعنی پیش بار کاملا جذاب است. (1- = R نشان دهنده تنشهای مشابه کششی و فشاری است.) همچنین، میزان شیار و شرایط سطح نقش نقش بسیار مهمی را ایفا می کنند. جنبه های مفید چکش کوبی و شیشه پاشی روی Ti-6Al-4V LCF در °C 21 (°F 70) در شکل 12-22 نشان داده شده اند. تاثیرات فاکتور شیار، Kt، و انتشار ترک بر عمر Ti-6Al-4V پیش بارگذاری شده در °C 204 (°F 400) در محدوده LCF در شکل 12-23 نشان داده شده اند. (تاثیرات فرآوری سطح و نقایص سطحی بر رفتار خستگی آلیاژهای تیتانیوم بعدا به بحث گذارده خواهد شد.)
شکل 12-22 تاثیرات شرایط سطح بر عمر خستگی در چرخه کم مربوط به Ti-6Al-4V در °C 21 (°F 70)
مقداریابی رفتار LCF آلیاژهای تیتانیوم، به دلیل دامنه گسترده متغیرها و مقدار محدود داده های منتشرشده دشوار است. به طور کلی، داده های موجود مربوط به تست های با بار کنترل شده و بدون کنترل کرنش هستند. تست بیشتر در آزمایشگاه های تولیدکننده روی محصولات اولیه نظیر میلگرد انجام شد. در آزمایشگاه های مربوط به مشتریان، تمایل به استفاده از نمونه های ماشینکاری شده از قطعات فورج شده وجود داشت. نتایج حاصل از میله با نتایج بدست آمده از قطعات فورج شده متفاوت بودند. این موضوع می تواند یک مسئله مهم باشد زیرا تیتانیوم یک ماده نسبتا گران قیمت است و تخریب قطعات فورج شده نظیر قطعات به کار رفته در صنعت هوافضا، وزن کمی ندارد. ساختارهای ایجاد شده در قطعات فورج شده واقعی با ساختارهای حاصل در میله ها متفاوت هستند. ساختار و تنش پسماند سطحی می توانند در قطعات فورج شده یا پرداخت شده با موارد مشابه در میله متفاوت باشند. نتایج خواص مربوط به خستگی تیتانیوم را باید از نظر شرایط سطح و نیز میکروساختار، در هنگام ایجاد خواص یک طراحی در نظر گرفت. هرچند نتایج مربوط به قطعات میله ای و فورج شده، لزوما تطابق ندارند اما چنین نتیجه گیری شده است که نتایج مربوط به قطعات فورج شده معمولا با نتایج تست روی نمونه های ماشینکاری شده از قطعات فورج شده که موجب عملیاتی روی سطح (مانند ماشینکاری و چکش کوبی) می شود یکسان هستند.
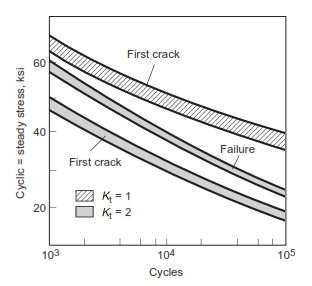
شکل 12-23 خواص خستگی در تعداد چرخه کم برای آلیاژ تیتانیوم آلفا- بتای Ti-6Al-4V که نشان دهنده تاثیرات تیزی شیار و زمان لازم برای نخستین ترک است
تاثیر دما به ندرت گزارش شده است؛ ظرفیت تنشی Ti-6Al-4V در 0= R (چرخه پایا، تنش از پیش بارگذاری شده) در °C 204 (°F 400) تقریبا 11 درصد کمتر از °C 21 (°F 70) بود.
در HCF، بسته به آلیاژ، مطابق با شکل 12-24، تمایل حد خستگی آن است که تا °C 316 (°F 600) یا بیشتر، تغییر نسبتا پایایی با دما داشته باشد. این شکل همچنین، مزایای آلیاژهای تیتانیوم را بر فولادها از جنبه ظرفیت استحکام خستگی نشان می دهد. این شکل تا حد زیادی تائید می کند که داده های پراکنده ای را می توان در یک آلیاژ معین در یک Kt و دما پیدا کرد. همچنین، آشکارا نشان می دهد که شرایط سطح بر HCF موثر است.
بحث پیشین غالبا بر آلیاژهای تیتانیوم شبه آلفا و آلفا- بتا تمرکز یافت. خستگی آلیاژهای بتا نیز بوسیله میکروساختار تحت تاثیر قرار می گیرد. بسته به دسته آلیاژ (یعنی آلیاژی غنی از عنصر حل شونده یا تقریبا تهی از عنصر حل شونده)، پارامترهای میکروساختاری زیر در تعیین خستگی آلیاژهای بتا مهم هستند: اندازه دانه بتا، میزان پیرسختی و نواحی عاری از رسوب در آلیاژهای غنی از عنصر حل شونده. همچنین، آلفای مرزدانه ای، اندازه آلفای اولیه و کسر حجمی آلفای اولیه در آلیاژهای تقریبا تهی از عنصر حل شونده نظیر Ti-10V-2Fe-3Al مهم هستند. Ti-10V-2Fe-3Al دسته ای از آلیاژهای تقریبا تهی از عنصر حل شونده را نشان می دهد که می توانند دارای میکروساختارهایی با شدت کنترل بیشتر نسبت به دیگر آلیاژهای بتا باشند. این موضوع با وجود محتمل الفای اولیه در کسر حجمی هایی شبیه به کسرحجمی آلفا در آلیاژهای آلفا- بتا رخ داده است. منحنی های نشان دهنده تنش به ازای چرخه های لازم تا شکست برای میکروساختارهای مختلف در Ti-10V-2Fe-3Al در شکل 12-25 نشان داده شده اند. عملکرد بسیار بهتر این میکروساختارها با مقادیر آلفای اولیه کمتر به نبودن هم زمان آلفای مرزدانه ای نسبت داده شد. خواص خستگی مربوط به Ti-10V-2Fe-3Al نیز با آلیاژ آلفا- بتای Ti-6Al-4V تحت عملیات انحلالی قرار گرفته و آنیل شده در شکل 12-26 مقایسه شده اند.
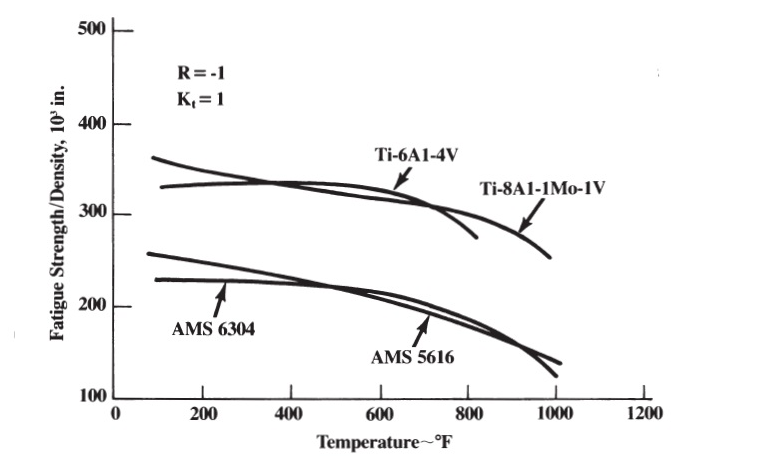
شکل 12-24 مقایسه نسبت مقاومت خستگی (سیکل بالا) به دانسیته آلیاژهای مختلف تیتانیوم با برخی استیل ها که در بخش کمپرسور توربین های گاز استفاده شده اند
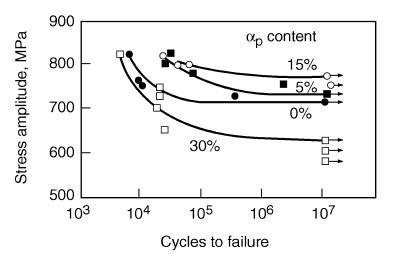
شکل 12-25 نمودارها میزان تنش به سیکل تا مرز شکست را برای میکروساختارهای متفاوت با مقدار آلفای متفاوت نشان می دهند
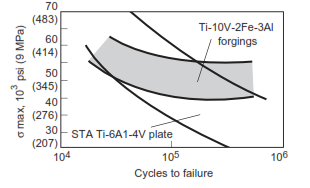
شکل 12-26 مقایسه منحنی های خستگی شیاری برای آلیاژ بتای Ti-10V-2Fe-3Al و آلیاژ آلفا- بتای Ti-6Al-4V. برای Ti-10V-2Fe-3Al، 05/0= R،9/2 F=Kt=. برای ورق STA Ti-6Al-4V، 01/0= R، 3 Kt=.
بحث بالا و داده های ارائه شده نشان دهنده روندهای موجود در عملکرد آلیاژ هستند. اما، بویژه به دلیل تنوع میکروساختارها و حساسیت بالقوه به شرایط سطح در خستگی، کاربردهای آلیاژهای تیتانیوم در قطعات با خستگی محدود باید شامل اعتبارسنجی استحکام خستگی تحت شرایط سرویس دهی مورد انتظار باشد.
عملیات سطحی و خستگی
از بحث پیشین درباره خستگی، اکنون باید واضح باشد که ظرفیت خستگی آلیاژهای تیتانیوم، می توانند به طور قابل توجهی، نه فقط با میکروساختار، بلکه با شرایط سطح یا عملیات حرارتی نیز تحت تاثیر قرار بگیرند. داده های خستگی گزارش شده در مقالات، غالبا درباره ماده ای با تنش پسماند سطحی مناسب ناشی از فرایندهایی نظیر تراشکاری و فرزکاری می باشد. سطوحی که به طور کامل تنش گیری شده اند یا به طور شیمیایی فرزکاری شده اند به طور کلی دارای استحکام های خستگی ای کمتر از ظرفیت گزارش شده آلیاژ می باشند زیرا بیشتر داده های گزارش شده ناشی از تنش های سطحی فشاری و بیشتر از مقدار واقعی بوده اند.
عملیات های سطحی مکانیکی نظیر پاشش ساچمه، پولیش کاری یا نورد سطحی را برای بهبود حد خستگی در مواد پایه تیتانومی با تغییر ناهمواری سطح، میزان کار سرد (چگالی نابجایی) و تنشهای پسماند می توان به کار برد. ناهمواری سطح تعیین می کند که آیا استحکام خستگی عمدتا با جوانه زنی ترک (صاف) یا انتشار ترک (ناهموار) کنترل می شود یا خیر. برای سطوح صاف، یک لایه سطحی کارسخت شده می تواند جوانه زنی ترک را به دلیل افزایش استحکام به تاخیر بیندازد. روی سطوح ناهموار، مرحله آغاز ترک می تواند موجود نباشد و لایه سطحی کارسخت شده به دلیل کاهش داکتیلیته، در معرض انتشار ترک خواهد بود. تنش های فشاری پسماند نزدیک به سطح آشکارا مفید هستند زیرا می توانند به طور محسوسی رشد ترکها را در صورت وجود ترک کند کنند (هرچند آزادسازی تنش پس از آن، یا تغییرشکل پلاستیک چرخه ای می توانند تنشهای پسماند فشاری مفید را کاهش دهند).
در آماده سازی سطوح تیتانیوم، احتیاط بسیاری باید در نظر داشت به طوریکه نباید هیچ نقصی به شکل مثلا خراش های گسترده یا سوختگی های قوسی که ممکن است موجب جوانه زنی ترکهای خستگی و کاهش ظرفیت خستگی آلیاژ شوند وارد شوند. به نظر می رسد ماشینکاری معمولی برای استحکام خستگی مفید باشد همانطور که اصلاح سطح با پاشش ساچمه برای اعمال تنشهای پسماند مطلوب، مفید هستند.
دیگر روش عملیات سطحی، اصلاح میکروساختار سطح با فراوری ترمومکانیکی (TMP) است. عملیات هایTMP به طور گسترده ای برای بهینه سازی خواص مکانیکی کلی آلیاژهای با استحکام بالای تیتانیم به کار می روند. تغییرات میکروساختاری از سطح تا درون قطعه برای برآورده کردن الزامات مختلف (مانند کربوره کردن فولادها) منطقی است. کارسرد ناشی از عملیات های سطحی مکانیکی را برای ایجاد یک میکروساختار سطحی که متفاوت با میکروساختار کلی ماده است می توان به کار برد. این فرآوری استفاده از خصوصیات TMP را حتی در مواردی مانند مقاطع ضخیم که TMP معمولی قابل اعمال نیست، ممکن می نماید. یک مزیت مشخص تغییر میکروساختار سطح، آن است که چنین تغییراتی نسبت به تغییرات اعمال شده با عملیات های سطحی مکانیکی صرف، پایدارتر است.
در مورد آلیاژهای آلفا، یک عملیات سطحی مکانیکی همراه با تبلور مجدد پس از آن، امکان ترکیب استحکام ها و حدهای خستگی بالا که مربوط به دانه های ریز می باشند را با رفتار مطلوب رشد ترک خستگی و چقرمگی شکست دانه های درشت فراهم می نماید. برای بیشینه کردن عمر خستگی نهایی در مقاطع ضخیمتر، دانه های ریز روی سطح - یعنی جایی که مقاومت خوب در برابر آغاز ترک، مهم است- مورد نیاز هستند. اما در داخل- یعنی جایی که درشت دانگی از نیروی محرکه مربوط به رشد طولانی ترک می کاهد- دانه های درشت لازم می باشند.
برای انجام این موضوع، ساچمه پاشی و پس از آن، یک عملیات حرارتی یک ساعته در °C 820 (°F 1510) روی Ti-8Al درشت دانه برای انجام کارسرد و تبلور مجدد سطح انجام شد. شکل 12-27 بهبود محسوس حد خستگی را به میزان تقریبا MPa 50 (ksi 25/7) در °C 350 (°F 665) به دلیل ایجاد دانه ریز در سطح نشان می دهد.
از آنجا که آلیاژهای آلفا- بتا و شبه آلفا غالبا برای کارکردهای دمابالا (برای نمونه در توربینهای گازی) ساخته می شوند، مقاومت خزشی یک ملاحظه مهم به حساب می آید. بر این اساس، میکروساختارهای لایه ای ترجیح داده می شوند. اما این میکروساختارها دارای مقاومت خستگی ضعیفی بویژه در LCF هستند. در LCF، رشد ترک سطحی موجب تعیین عمر خستگی می شود. در چنین مواردی، تغییر در مورفولوژی فازی بین سطح و مغز قطعه می تواند مطلوب باشد. برای یک آلیاژ آلفا- بتا و آلیاژ شبه آلفا، میکروساختارهای سطحی ریزی با کار مکانیکی روی سطح به وسیله ساچمه پاشی و سپس عملیات حرارتی حاصل شدند. بهبود در رفتار S-N (در دمای بالا) که با این عملیات سطحی ترمومکانیکی حاصل شد در شکل 12- 28 برای میکروساختار Ti-6Al-2Sn-4 Zr-2Mo با یک مغزه لایه ای ظریف مقاوم به خزش و یک لایه سطحی مقاوم به خزش هم محور ظریف نشان داده شده است.
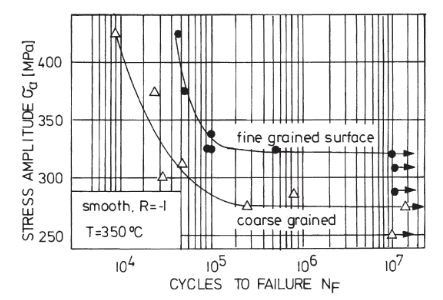
شکل 12-27 منحنی های نشان دهنده تنش برحسب تعداد چرخه لازم تا شکست برای آلیاژ آلفای درشت دانه Ti-8Al با و بدون فرآوری ترمومکانیکی برای ایجاد اصلاح اندازه دانه به طور موضعی در سطح
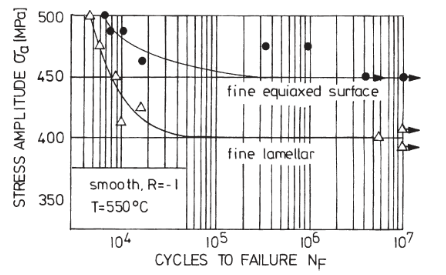
شکل 12-28 منحنی های نشان دهنده تنش برحسب تعداد چرخه لازم تا شکست برای آلیاژ Ti-6Al-2Sn-4Zr-2Mo با و بدون فرآوری ترمومکانیکی برای ایجاد اصلاح اندازه دانه به طور موضعی در سطح
در مورد آلیاژهای بتا، سندبلاست و نورد سطحی همراه با عملیات های سطحی خاص به آلیاژ Ti-3Al-8V-6Cr-4Mo-4Zr اعمال شده اند تا به طور انتخابی، فقط سطح را پیرسخت نمایند.
انتشار ترک خستگی
همان طور که KIC در محاسبه بارهایی که یک عضو سازه ای می تواند با وجود یک نقص حمل کند مهم است، در بسیاری از موارد، دانستن بقیه عمر خستگی در حضور یک ترک خستگی یا یک ترک تیز دیگر نیز مهم است. به صورتی بسیار کلی، رفتار انتشار ترک خستگی (FCP) در تیتانیوم به موازات چقرمگی شکست است، یعنی برای یک آلیاژ معین، شرایطی که موجب بالاترین چقرمگی می شود، تمایل دارد که تحت بارگذاری خستگی، موجب کمترین نرخ رشد چرخه ای شود.
در اندازه گیری های FCP، پراکندگی داده محسوسی می تواند وجود داشته باشد. مثال نشان داده شده در شکل 12-29 یکی از حالات حداکثری است و موجب نیاز به شرایط میل آنیل شده می شود چرا که در آن، عدم قطعیت درباره میکروساختار، بافت و استحکام می تواند وجود داشته باشد. بخشی از پراکندگی داده به دلیل قابلیت تکرار تست است. همچنین، قابلیت تغییر ماده از یک نقطه به نقطه دیگر به دلیل فراوری و ناهمگنی در ماده می تواند وجود داشته باشد. تغییراتی در ترکیب شیمیایی، میکروساختار و تاثیرات بافت در برخی موارد تحت شرایط کنترل شده می توانند افزوده شوند. البته تفاوت هایی از یک قطعه تا قطعه دیگر وجود دارند. برای مقاصد طراحی، به کاربردان توصیه می شود تا از داده های آماری حاصل از اطلاعات مربوط به چند قطعه استفاده کنند.
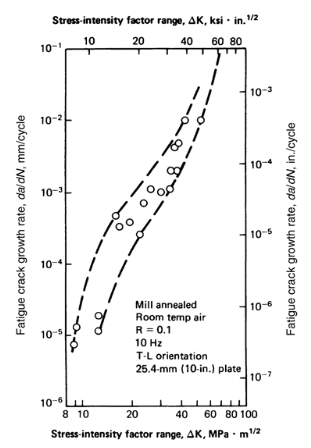
شکل 12-29 داده های مربوط به انتشار ترک خستگی برای آلیاژ آلفا- بتای میل آانیل شده Ti-6Al-4V که نشان دهنده پراکندگی داده هاست. داده ها مربوط به 6 دسته از Ti-6Al-4V میل آنیل شده هستند.
T-L عرضی- طولی.
آلیاژهای تیتانیوم دارای مشخصه های مختلف FCP هستند زیرا دارای KIC مختلفی هستند. داده های منتخب نشان می دهند که ترکهای خستگی در Ti-6Al-2Sn-4Zr-6Mo با سرعت بیشتری نسبت به Ti-8Al-1Mo-1V یا Ti-6Al-2Sn-4Zr-2Mo تحت شرایط یکسان آزمایش، منتشر می شوند. این موضوع می تواند تاثیر ساده ای از استحکام باشد. اما مقادیر نسبی فاز بتا می تواند منجر به مشخصات ذاتا متفاوتی در انتشار ترک خستگی شوند. آلیاژ Ti-6Al-2Sn-4Zr-6Mo نیز با سهولت بیشتری بافت دار می شود. به علاوه، فازهای مختلفی نظیر مارتنزیت دابل پریم اورتورومبیک می توانند وجود داشته باشند و می توانند موجب مشکلاتی در FCP پس از پیرسازی شوند. نرخهای FCP در مقایسه یک آلیاژ آلفا- بتا و یک آلیاژ بتا در شکل 12-30 نشان داده شده اند.
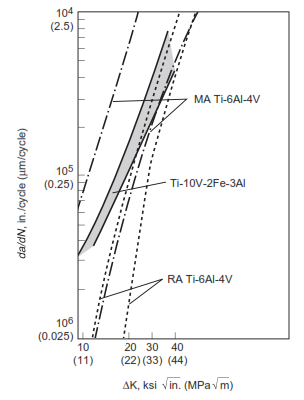
شکل 12-30 مقایسه نرخ رشد ترک خستگی برای آلیاژ بتای Ti-10V-2Fe-3Al و آلیاژ آلفای Ti-6Al-4V. برای Ti-10V-2Fe-3Al، 05/0= R؛ Hz 30-1 = F. برای MA Ti-6Al-4V، 08/0= R؛ Hz 25-1= F. برای RA Ti-6Al-4V، 08/0= R؛ Hz 6= F. MA
میل آنیل شده؛ RA آنیل شده تبلور مجددی
تغییرات میکروساختاری نیز موجب تغییرات موازی KIC و FCP می شوند. همان طور که در مورد KIC صادق است، FCP به طور مطلوبی با میکروساختار استحاله و نیز با اعمال چرخه های گرمایی از نوع آنیل- تبلورمجدد تحت تاثیر قرار می گیرند.
میکروساختار در یک قطعه معین از Ti-6Al-4V می تواند بر FCP با ضریبی بزرگتر از 10 تاثیر گذاشته و می تواند بر ΔK به میزان 5 تا 30 ( 27-4) تاثیر بگذارند. میزان این تاثیر به محل اندازه گیری این پارامتر روی منحنی da/dN بستگی دارد. به طور کلی، میکروساختارهای بتاآنیل شده در آلیاژهای آلفا- بتا و شبه آلفا دارای کمترین نرخ رشد ترک خستگی هستند درحالیکه میکروساختارهای میل آنیل شده دارای بالاترین نرخ رشد ترک می باشند. نمونه ای از چنین رفتاری برای یک آلیاژ آلفا- بتا در شکل 12-31 نشان داده شده است.
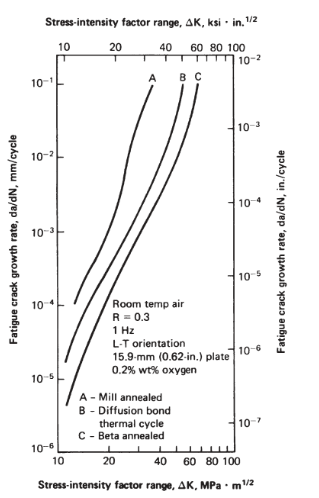
شکل 12-31 تاثیر عملیات حرارتی بر نرخ رشد ترک خستگی در آلیاژ Ti-6Al-4V.
L-T، طولی- عرضی
جای شگفتی نیست که محیط بر نرخ FCP در تیتانیوم اثر می گذارد همان طور که بر چقرمگی شکست موثر است. تنها شگفتی درباره داده های موجود این است محیط شیمیایی تاثیر بیشتری نسبت به آنچه انتظار می رود ندارد. به طور کلی، محیط های باشدت بیشتر (نظیر محلول 3.5 درصد NaCl) بر نرخ FCP به میزان 10 برابر یا بیشتر موثر هستند. اتمسفرهای گازی نیز نقشی کلیدی در تاثیر بر نرخ های FCP ایفا می کنند. همه تاثیرات شیمیایی یا محیطی گازی بدون شک تا حدی از نظر میکروسکوپی و شیمیایی مهم هستند.
با کاربرد فزاینده معیارهای طراحی وابسته به آسیب، داده های مربوط به نرخ رشد ترک خستگی در سازه های جوشکاری شده از اهمیت بیشتری برخوردار هستند. مقایسه نرخ انتشار ترک خستگی بین قوس ناشی از جوشکاری قوس با الکترود تنگستن تحت پوشش گاز، جوشکاری پرتوی لیزری و پرتوی الکترونی در آلیاژ آلفا- بتای Ti-6Al-4V و آلیاژ بتای Ti-15V-3Al-3Cr-3Sn نشان داد که نرخ رشد ترک خستگی در مناطق جوشی که تحت عملیات حرارتی پساجوشکاری قرار گرفته اند به طور قابل توجهی با تغییر فرایند جوشکاری تفاوت نکرده است (شکل 12-32). نوارهای پراکندگی برای چگالی انرژی بالا، باریک تر بودند. برای آلیاژ آلفا- بتای Ti-6Al-4V، چنین نتیجه گیری شد که نرخ متوسط رشد ترک کمتر از فلز پایه بود در حالی که در آلیاژ بتای Ti-15V-3Al-3Cr-3Sn نرخ رشد ترک در فلز جوش و فلز پایه تقریبا معادل بودند (شکل 12-32).
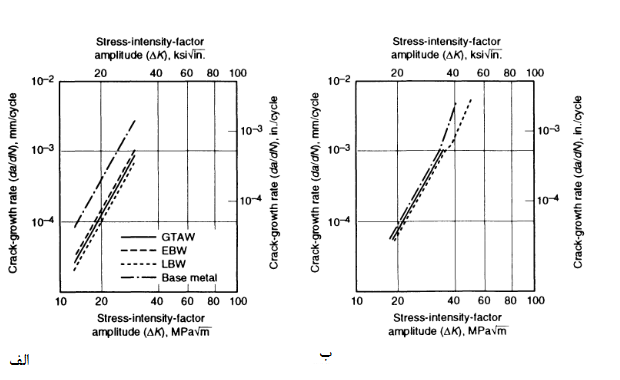
شکل 12-32 تاثیر فرآیندهای جوشکاری بر نرخ رشد ترک خستگی آلیاژهای تیتانیوم با جهت گیری طولی، الف- آلیاژ آلفا- بتای Ti-6Al-4V. ب- آلیاژ بتای Ti-15V-3Cr-3Al-3Sn.
جوشکاری قوس با الکترود تنگستن تحت پوشش گاز GTAW؛ EBW جوشکاری پرتوی الکترونی؛ LBW جوشکاری پرتو لیزری
خواص آلیاژهای ریختگی تیتانیوم
خواص استاتیک
آلیاژهای ریختگی تیتانیوم معمولا از نوع آلفا- بتا هستند. این آلیاژها از نظر استحکام، معادل یا نزدیک به آلیاژهای کارشده با ترکیب یکسان هستند. خواص کششی در دمای اتاق برخی آلیاژهای ریختگی تیتانیوم در جدول 12-14 آمده است.
هرچند تعدادی از آلیاژهای تیتایوم به شکل ریختگی بررسی شده اند (جدول 12-15)، اما در واقع همه داده ها از آلیاژ Ti-6Al-4V بi دست آمده اند. متعاقبا، پایه بیشتر داده های مربوط به خواص نیز مربوط به Ti-6Al-4V است. توزیع خواص کششی در دمای اتاق برای میله های به طور جداگانه ریخته گری شده برای تست از جنس آلیاژ Ti-6Al-4V در شکل 12-33 نشان داده شده است. توجه کنید که اکسیژن- که یک افزودنی با مقدار به شدت کنترل شده است که می تواند استحکام کششی را افزایش دهد- در دامنه 0.16 تا 0.20 درصد وزنی است. این دامنه برای بسیاری از مقررات هوافضایی مرسوم است. برخی مقررات، مقدار بیشینه 0.25 درصد وزنی را برای اکسیژن مجاز می دانند. خواص کششی حاصل با اکسیژنی در دامنه 0.20 تا 0.25 درصد وزنی معمولا حدود MPa 69 تا 83 (ksi 12-10) بیشتر از مقادیر نشان داده شده در شکل 12-33 می باشند. اما همانطور که از سطح بالای عنصر بین نشین انتظار می رود، داکتیلیته اندکی کاهش می یابد.
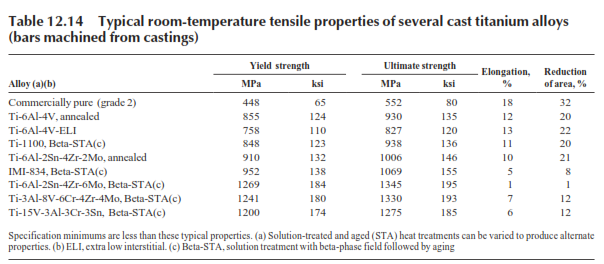
جدول 12-14 خواص کششی در دمای اتاق مربوط به آلیاژهای تیتانیوم ریختگی (میله های ماشین کاری شده از قطعات ریختگی)
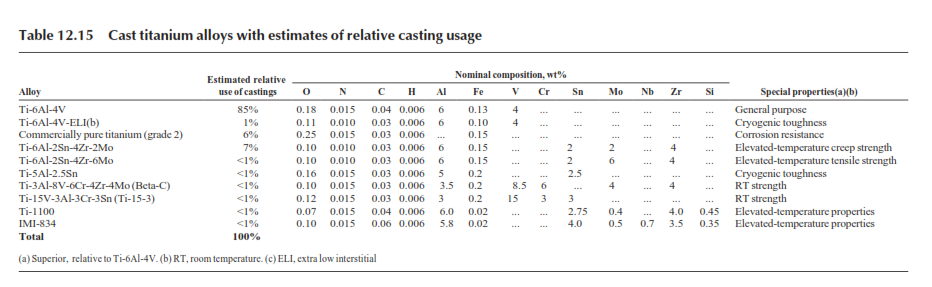
جدول 12-15 آلیاژهای تیتانیوم ریختگی با ارزیابی هایی از کاربرد نسبی قطعه ریختگی
چون میکروساختار قطعات از جنس آلیاژ تیتانیوم قابل مقایسه با ماده کارشده است، بسیاری از خواص قطعات ریخته گری شده به علاوه HIP مشابه با خواص آلیاژهای کارشده است. این خواص عبارتند از استحکام کششی، استحکام خزشی، چقرمگی شکست و FCP. خواص کششی در دمای اتاق و چقرمگی شکست قطعات ریختگی Ti-6Al-4V که پس از ریخته گری به شکل های مختلفی فرآوری شده اند (جدول 6-1 را ببینید) در جدول 6-3 با ماده بتاآنیل شده مقایسه شده اند.
شایان ذکر است که نتایج تست نشان داده شده در جدول 6-3 مربوط به کوپنهای کوچک تست جداگانه ریختگی بودند و لزوما خواص قابل دستیابی با فرآوری مشابه روی یک قطعه ریختگی را بازتاب نمی دهند. سطح خواص قطعات ریختگی واقعی بویژه قطعات بزرگتر احتمالا تاحدی پائین تر خواهند بود که نتیجه ساختار دانه درشت تر یا نرخ کوئنچ آهسته تر می باشند.
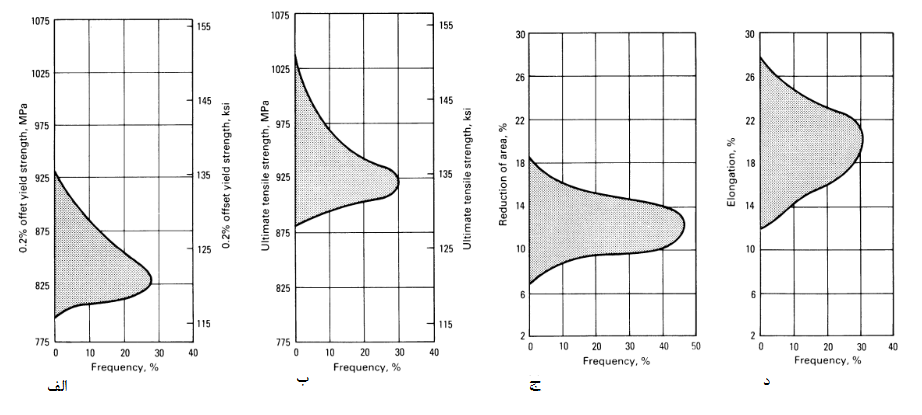
شکل 12-33 توزیع خواص کششی در دمای اتاق مربوط به آلیاژ Ti-6Al-4V ریخته گری شده به علاوه پرسکاری شده در شرایط ایزواستاتیک گرم
خواص کششی دمابالای مربوط به Ti-6Al-4V در شکل 12-34 نشان داده شده اند. خواص کششی مربوط به آلیاژ Ti-6Al-2Sn-4Zr-2Mo ریختگی و کارشده در شکل 12-35 نشان داده شده اند. شکل 12-36 گستره خواص کششی قابل حصول در آلیاژهای ریختگی دمابالا نظیر IMI 834 را با آلیاژ Ti-6Al-4V مقایسه می کند. به تازگی، آلیاژ آلفا- بتای Ti-6Al-2Sn-2Zr-2Mo-2Cr+Si به شکل ریختگی ارزیابی شده است. جدول 12-16 خواص این آلیاژ را برای برخی شرایط عملیات حرارتی نشان می دهد. مقایسه با جدول 12-14 نشان می دهد که Ti-6Al-2Sn-2Zr-2Mo-2Cr+Si می تواند موجب استحکام هایی بهتر از Ti-6Al-4V ریختگی و نیز توازن خوبی از چقرمگی گردد.
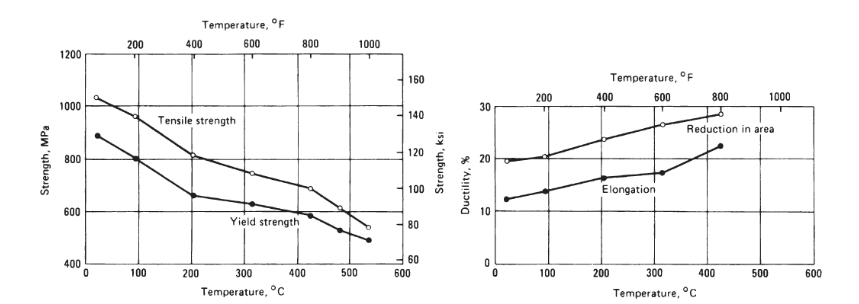
شکل 12-34 خواص کششی دما بالای آلیاژ Ti-6Al-4V ریختگی
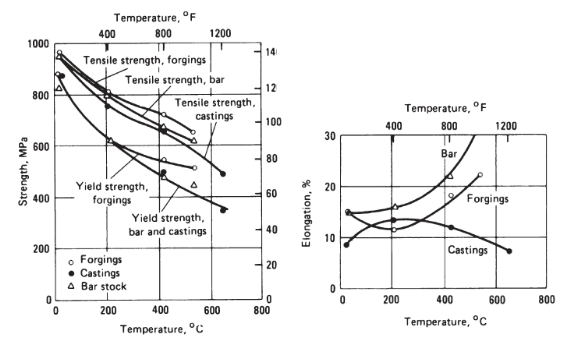
شکل 12-35 مقایسه خواص کششی در زمان کوتاه برای صورت های کارشده و ریختگی Ti-6Al-2Sn-4Zr-2Mo. میله های تست از قطعات ریختگی ای برش داده شدند که آنیل دوپلکس شده بودند: 1 ساعت در °C 900 (°F 1650) و تبرید در هوا بعلاوه 1 ساعت در °C 790 (°F 1450) و تبرید در هوا. داده های منتشرشده درباره قطعات فورج شده برای شرایط آنیل شده و پیرسازی شده هستند: 1 ساعت در °C 900 (°F 1650) و تبرید در هوا بعلاوه 8 ساعت در °C 595 (°F 1100) و تبرید در هوا. داده های متشرشده درباره مواد میله ای به قطر mm 57 (2.25 اینچ) در شرایط آنیل شده و پیرسازی شده می باشند: 1ساعت در °C 955 (°F 1750) و تبرید در هوا بعلاوه 8 ساعت در °C 595 (°F 1100) و تبرید در هوا.
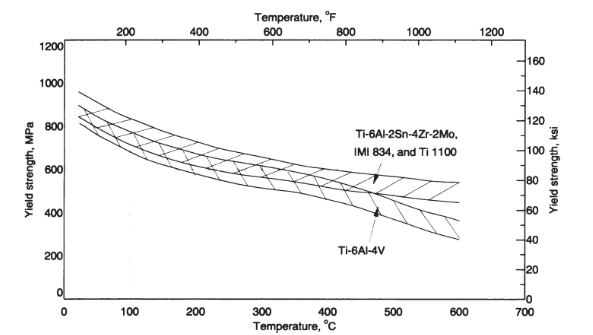
شکل 12-36 نوار پراکندگی برای استحکام تسلیم برحسب دما مربوط به برخی آلیاژهای تیتانیوم ریختگی دما بالا (Ti-6Al-2Sn-4Zr-2Mo, IMI 834 و Ti-1100) در مقایسه باTi-6Al-4V ریختگی
مقادیر چقرمگی شکست کرنش صفحه ای قطعات ریختگی Ti-6Al-4V با مقادیر ورق Ti-6Al-4V و دیگر آلیاژهای کارشده تیتانیوم در شکل 12-37 مقایسه شده اند.
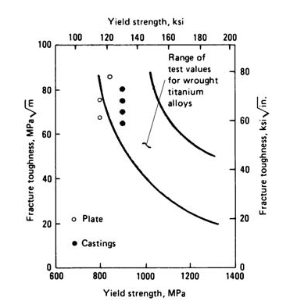
شکل 12-37 چقرمگی شکست آلیاژ ریختگی و ورق Ti-6Al-4V با محدوده مقادیر برای آلیاژهای تیتانیوم کارشده
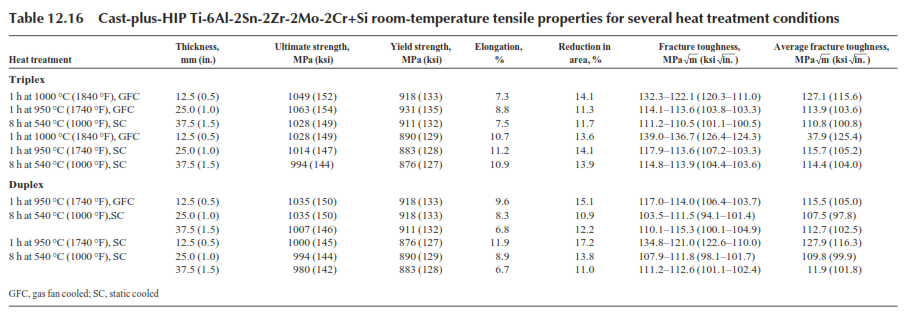
جدول 12-16 خواص کششی در دمای اتاق مربوط به Ti-6Al-2Sn-2Mo-2Cr+Si ریخته گری شده بعلاوه HIP برای برخی شرایط عملیات حرارتی
خواص شکست ناشی از خزش آلیاژهای ریختگی بسیار پراکنده هستند. جدول 12-17 استحکام خزشی Ti-6Al-4V ریخته گری شده بعلاوه HIP در نمونه های برش یافته از ایمپلرهای کمپرسور ریخته گری شده گریز از مرکزی را نشان می دهد. ایمپلرها به طور ایزواستاتیک، در °C 900 (°F 1650) به مدت 2 ساعت در فشار MPa 103.5 (ksi 15) پرس گرم شدند و سپس به مدت 1.5 ساعت در °C 675 (°F 1250) پیرسازی شدند. خواص نشان داده شده ممکن است برای همه اشکال ریخته گری و عملیات های حرارتی پساریخته گری بهینه نباشند.
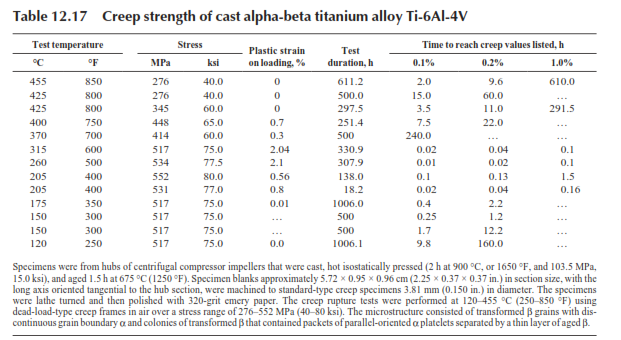
جدول 12-17 استحکام خزشی آلیاژ تیتانیوم آلفا- بتای Ti-6Al-4V ریختگی
خواص چرخه ای
هرچند خواص قطعات ریختگی از جنس آلیاژ Ti-6Al-4V معمولا خواص مطلوب برای محصولات کارشده فورج شده بتاآنیل شده را برآورده می کنند اما ماده فورج شده دارای خواص HCF بهتری است. روتورهای ریختگی بالگرد، حد خستگی حدود 63 درصد حد خستگی روتورهای فورج شده نشان دادند.
محصولات فورج شده معمولا در حوزه فازی آلفا- بتا فرآوری می شوند که منجر به یک میکروساختار آلفا- بتای ریزشده با مقاومت به خستگی بالا می شود. در مقابل، قطعات ریختگی با سرعتی آهسته از حوزه فازی بتا سرد می شوند که موجب یک میکروساختار درشت می شود؛ این موضوع با درشت شدگی بیشتر در حین HIP بدتر نیز می شود.
بطور کلی، بهبود مقاومت به خستگی با HIP ماده ریختگی عمدتا بوسیله بستن یا کاهش تخلخل هایی که می تواند موجب گسیختگی ناشی از خستگی شود حاصل می شود. بعلاوه، نتایج پژوهش بیان می کنند که بهبود قابل توجهی در مقاومت به FCP را می توان با عملیات حرارتی بتا و فراپیرسازی آلیاژهای ریختگی بدست آورد. نرخ واقعی رشد ترک با کیفیت قطعه ریختگی و عملیات حرارتی پساریخته گری شامل HIP تحت تاثیر قرار خواهد گرفت.
میکروساختار مبنای قطعات ریخته گری شده بعلاوه HIP از کلونی هایی از بشقابهای آلفا و فاز آلفای مرزدانه ای تشکیل می شود. داده های مبنا معمولا مربوط به HIP در °C 900 (°F 1650) به مدت 2 ساعت تحت فشار MPa 103.5 (ksi 15) می باشند. هردو مشخصه میکروساختاری اشاره شده در بالا مقاومت به شروع ترک را کاهش می دهند. عملیات حرارتی پس از HIP (جدول 6-1) برای شکستن این ساختار به کار می رود. عملیات های حرارتی شامل عملیات انحلالی بتا با نرخ های مختلف تبرید از دمای انحلال می شوند. بدنبال آن، آنیل کاری یا پیرسازی در ناحیه آلفا- بتا انجام می شود هرچند دماهای عملیات حرارتی نهایی می تواند از °C 540 تا 845 (°F 1550-1000) متغیر باشد. استحکام خستگی (و استحکام کششی) بطور محسوسی با همه عملیات های حرارتی بیش از ریخته گری بعلاوه HIP افزایش می یابد ( جدول 6-3 را برای خواص کششی ببینید). اما این امر با از دست دادن داکتیلیته کششی بدست می آید.
کوئنچ در آب و تبرید در گاز بوسیله پنکه از دمای انحلال بتا در °C 1025 (°F 1880) موجب بهترین ترکیب از استحکام و داکتیلیته با استحکام کششی MPa 1035 (ksi 150) یا بهتر از این و داکتیلیته 7 درصدی یا بهتر می شود. مارتنزیت ریز ایجادشده با یک کوئنچ بتا به ساختار آلفای ریز سبدی- موجی عدسی شکل استحاله می شود که ساختار شکسته شده (BUS) نامیده می شود. این ساختار را می توان با یک چیدمان از کلونی آلفا در یک محصول ریخته گری بعلاوه HIP شناخت. هرچند آلفای مرزدانه ای همچنان وجود دارد اما مانند شرایط ریخته گری بعلاوه HIP پیوسته نیست. در حالیکه آلفای مرزدانه ممکن است منبع بالقوه ای برای آغاز ترک خستگی باشد (شکل 12-38) اما بدلیل نبودن فصل مشترک های آلفا- بتای پیوسته، عمر خستگی بهبود می یابد.
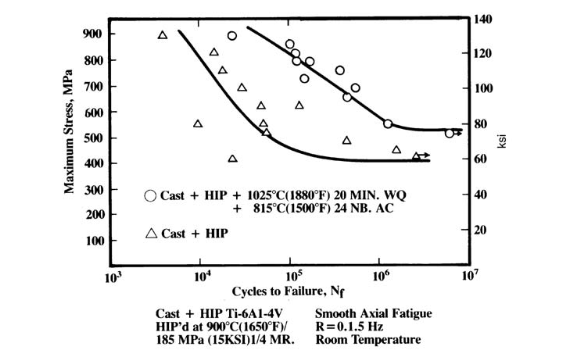
شکل 12-38 منحنی های نشان دهنده تنش در دمای اتاق برحسب تعداد چرخه لازم تا شکست مربوط به Ti-6Al-4V ریخته گریشده بعلاوه HIP که نشان دهنده تاثیر عملیات حرارتی پسا ریخته گری است که موجب ساختاری شکسته گردید.
WQ کوئنچ در آب؛ AC تبرید در هوا
ظرفیت خستگی کلی آلیاژ Ti-6Al-4V ریخته گری شده بعلاوه HIP در شکل 6-8 تا 6-10 و در شکل 12-39 و 12-40 نشان داده شده است. هرچند داده های HCF قطعات ریختگی صاف و شیاردار پائینتر از داده های صاف محصولات کارشده می باشند اما داده های HCF مربوط به قطعات ریختگی صاف و شیاردار، نزدیک به داده های محصولات کارشده شیاردار هستند (شکل 12-40).
با تکنولوژی های کنونی ریخته گری که پس از HIP و عملیات حرارتی پسا HIP انجام می شوند، خواص استحکام استاتیک ماده ریخته گری شده بعلاوه HIP نزدیک به خواص ماده کارشده بوده و حد خستگی قطعه صاف به حد خستگی محصولات کارشده نزدیک گردید. اما قابلیت اعتبارسنجی همه خواص تیتانیوم ریخته گری شده بعلاوه HIP که نشاندهنده مقادیر مربوط به قطعه باشند چالشی مستمر بوده است. (گاهی اوقات، این مسئله درباره ماده شمش کارشده نیز وجود دارد.)
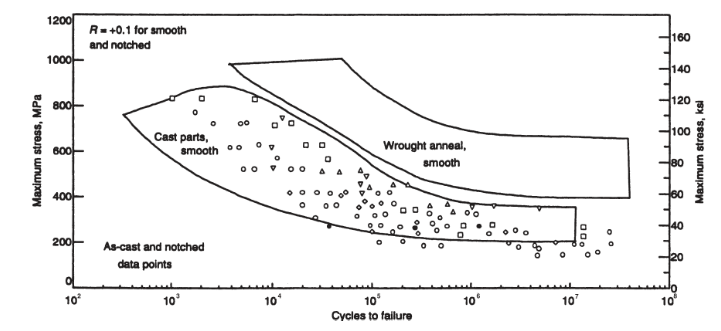
شکل 12-39 داده های مربوط به خستگی در نمونه های ریختگی صاف و شیاردار
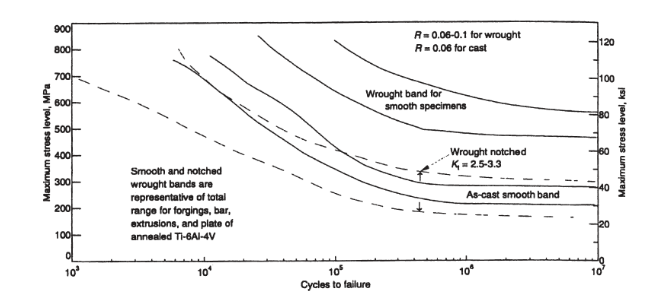
شکل 12-40 داده های مربوط به خستگی نمونه صاف در مقایسه با نمونه های Ti-6Al-4V آنیل شده کارشده
خواص آلیاژ تیتانیوم حاصل از متالورژی پودر
خواص استاتیک
داده های خواص برای آلیاژهای تیتانیوم P/M موجودند اما علیرغم کار گسترده روی روشهای فرآوری پودر همچنان محدودند. انتخاب منبع پودر – پودر عنصری مخلوط (BE) یا پودر پیش آلیاژشده (PA)- و روش های فرآوری – برای نمونه پرسکاری ایزواستاتیک سرد (CIP) + تفجوشی یا CIP + تفجوشی + HIP- و عملیات حرارتی پس از فرآیند شکل دهی همگی به شدت بر ظرفیت خواص مکانیکی تاثیر می گذارند. خواص مکانیکی ماده سازه ای P/M به ترکیب، چگالی و قابلیت انجام عملیات حرارتی روی ماده و نیز به ملاحظات فرآوری و طراحی بستگی دارند.
چگالی نهایی دارای بیشترین تاثیر روی خواص مواد P/M هستند. قطعات P/M با چگالی های نظری ای کمتر از 75 درصد، با چگالی کم، بیش از 90 درصد با چگالی بالا و بین این دو مقدار، با چگالی متوسط محسوب می شوند. (چگالی نظری نسبت چگالی ماده P/M به چگالی همتای کارشده خود می باشد.) به طور کلی، قطعات حساس به خستگی و با کیفیت بالا نیاز به چگالی 100 درصدی دارند. نقش چگالی در شکل 12-41 واضح است. این شکل، افزایش شدید چقرمگی با افزایش چگالی از 95 درصد تا 99.5 درصد را در نمونه های Ti-6Al-4V ساخته شده از پودرهای BE نشان می دهد.
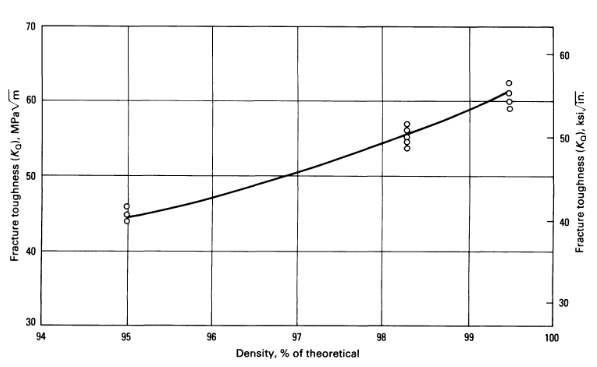
شکل 12-41 چقرمگی شکست بر حسب چگالی برای نمونه های پرسکاری شده و تفجوشی شده از پودرهای مخلوط عنصری آلیاژ Ti-6Al-4V.
توجه کنید که مقادیر چقرمگی، KIC اعتبارسنجی شده نیستند و در نتیجه با عنوان KQ نشان داده شده اند.
چقرمگی کششی و چقرمگی شکست نمونه های Ti-6Al-4V ساخته شده از پودرهای BE در جدول 12-18 نشان داده شده اند. یکی از ملاحظات مهمتر در تولید یک محصول P/M تیتانیومی، کنترل مقدار اکسیژن است، زیرا اکسیژن دارای تاثیراتی روی خواص قطعات P/M است چراکه بر خواص محصولات ریختگی و کارشده موثر است. پودرهایی را که نسبت سطح به حجم بالایی دارند باید بسیار محتاطانه جابجا کرد زیرا دارای تمایل زیادی به اکسیژن هستند. جدول 12-19 خواص کششی در دمای اتاق را برای نمونه های ساخته شده از پودرهای Ti-6Al-4V که دارای مقدار اکسیژن متغیری هستند ارائه می دهد. نتایج ارائه شده اهمیت کم بودن مقدار اکسیژن را در دستیابی به داکتیلیته مطلوب در نمونه های پودری پرس گرم شده نشان می دهند. تستهای کششی انجام شده روی نمونه های Ti-6Al-4V تحت HIP قرارگرفته با پودر فرآوری شده با الکترود چرخان، خواص فوق العاده ای مطابق با جدول 12-20 از خود نشان دادند. جدول 12-21 داده های بیشتری درباره خواص کششی و چقرمگی نمونه پودر PA ارائه می نماید.
پودر PA یا پودر PA یا BE با کلرید کم، مواد اولیه بهینه ای برای قطعات تیتانیومی با بالاترین کیفیت هستند اما عامل هزینه موجب استفاده از پودر با کیفیت کمتر می شود. HIP موجب بهترین شکل دهی برای قطعات با بالاترین استحکام می شود اما از روشهای دیگری نیز استفاده می شود. هنگامی که هیچ عملیات خاصی برای کاهش مقدار کلرید انجام نمی شود، پودرهای HIP شده PA با عملیات حرارتی پساHIP دارای خواص بهتری در بین محصولات P/M می باشند.
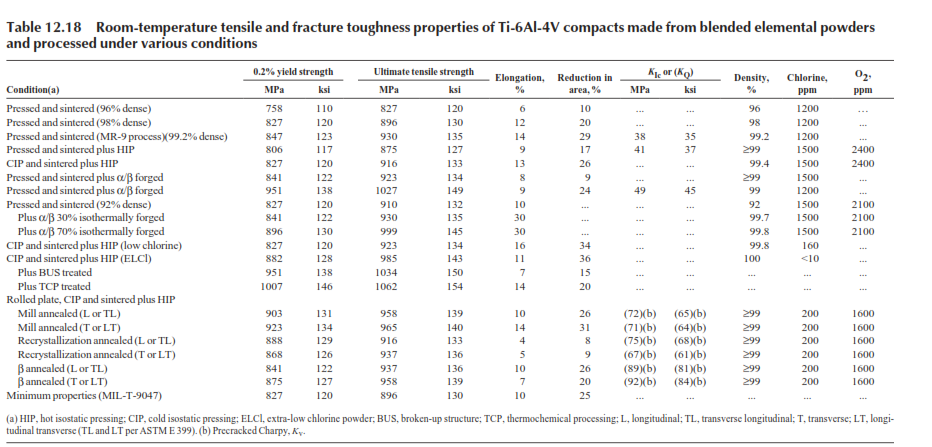
جدول 12-18 خواص کششی و چقرمگی شکست برای نمونه های Ti-6Al-4V ساخته شده از پودرهای مخلوط عنصری و پرسکاری شده تحت شرایط مختلف
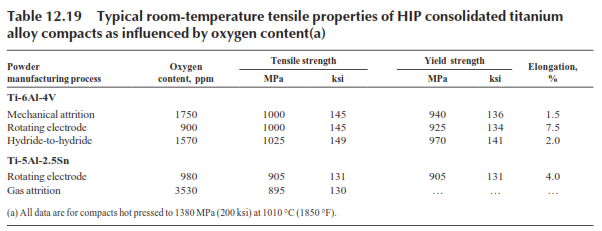
جدول 12-19 خواص کششی نمونه های آلیاژی تیتانیوم پرسکاری شده به صورت HIP در دمای اتاق تحت تاثیر مقدار اکسیژن
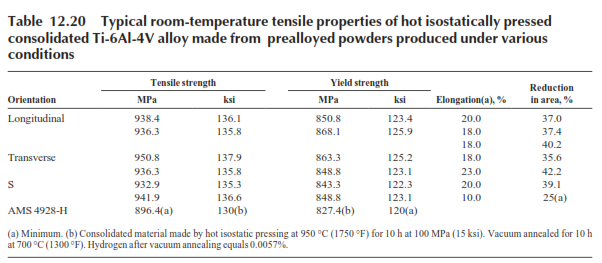
جدول 12-20 خواص کششی آلیاژ تیتانیوم Ti-6Al-4V پرسکاری شده به صورت HIP در دمای اتاق ساخته شده از پودرهای پیش آلیاژی شده تولید شده تحت شرایط مختلف
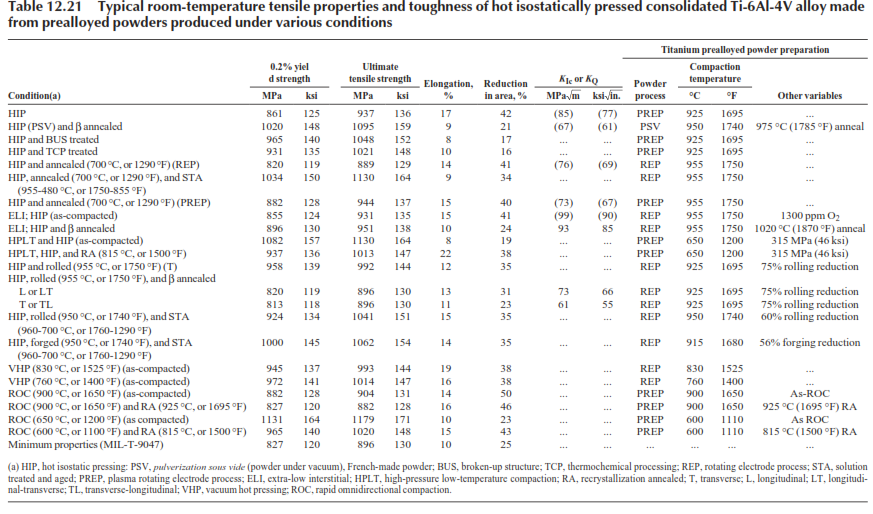
جدول 12-21 خواص کششی و چقرمگی آلیاژ تیتانیوم Ti-6Al-4V پرسکاری شده به صورت HIP در دمای اتاق ساخته شده از پودرهای پیش آلیاژی شده تولیدی تحت شرایط مختلف
خواص چرخه ای
پودرهای BE یا PA عمل آوری شده برای کاهش کلر، خواصی در انتهای بالایی نوار پراکندگی مربوط به رفتار خستگی محصولات P/M و شمش از خود نشان می دهند (شکل 12-42). بهبود در فرایندهای ساخت پودر که شامل ذوب مشعلی پلاسما می شود موجب ساخت نمونه های P/M فرآوری شده با الکترود چرخان پلاسما از جنس Ti-6Al-4V می شود که همچنین دارای خواص خستگی ای هستند که به خواص مواد ریختگی و کارشده نزدیک یا بهتر از آنها می باشند.
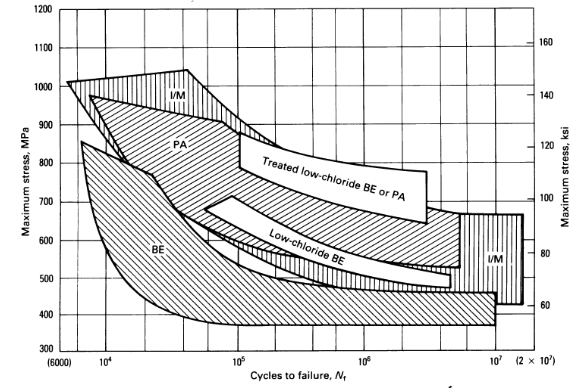
شکل 12-42 مقایسه نوارهای پراکندگی مربوط به عمر خستگی در دمای اتاق برای آلیاژ Ti-6Al-4V مربوط به نمونه های پودری مختلف (پودرهای پیش آلیاژی شده، PA، عنصری مخلوط، BE) در شرایط میل آنیل شده کارشده
برای یک ترکیب آلیاژی معین، کنترل چگالش و ساختار عوامل اصلی موثر بر خواص چرخه ای هستند. مدت زمان لازم برای شکست ناشی از خستگی در نمونه های پودری می تواند با محصول کارشده قابل مقایسه باشد و مشخصه های FCP می توانند به مشخصه های مربوط به مواد کارشده با ترکیب شیمیایی و ساختار یکسان نزدیک باشند (شکل 12-43). چگالی یک عامل اصلی در خستگی است که پیشتر نیز از آن یاد شد. تاثیر چگالی بر استحکام خستگی در دمای اتاق نمونه های پودری از جنس Ti-6Al-4V در شکل 12-44 ارائه شده است. در این شکل خواص نمونه هایی با چگالی متغیر با آلیاژ کارشده مقایسه شده اند. چقرمگی شکست نمونه های ساخته شده از پودر عنصری مخلوط شده و پودر الکترود چرخان پلاسما غالبا برابر با قطعات فورج شده میل آنیل شده بوده یا بهتر از آنها می باشد. تساوی یا برتری خواص پودر نسبت به محصول کارشده احتمالا فقط هنگامی حاصل می شود که پودری با مقدار کلرید کم به کار رود.
آلیاژهای تیتانیوم پودری در مقابل آلیاژهای ریختگی و کارشده. خواص محصولات P/M، ریختگی و کارشده تیتانیومی از آلیاژهایی با جنس مختلف در جدول 12-22 ارائه شده اند. مقایسه خواص خستگی سه صورت ماده برای Ti-6Al-4V در شکل 12-45 نشان داده شده است. رفتار نمونه های شیاردار برای کاربردهای نرمال تیتانیوم یک نگرانی محسوب می شود و نتایج نمونه های بدون شیار – در شکل 12-45- ممکن است ظرفیت خستگی آلیاژ را به خوبی نشان ندهند. شکل 12-46 مقایسه رفتار نمونه های شیاردار و بدون شیار هر سه شکل محصول (کارشده، ریختگی و P/M) را نشان می دهد.
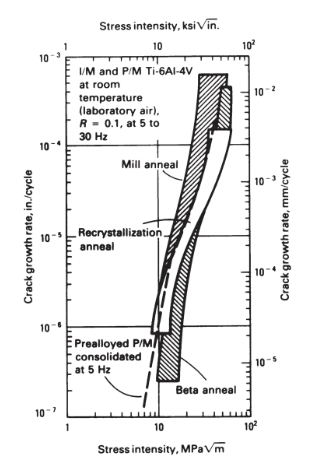
شکل 12-43 مقایسه نرخ انتشار ترک خستگی در دمای اتاق برای نمونه Ti-6Al-4V با نوار پراکندگی مربوط به محصولات شمش کارشده از این آلیاژ.
I/M متالورژی شمش و P/M متالورژی پودر.
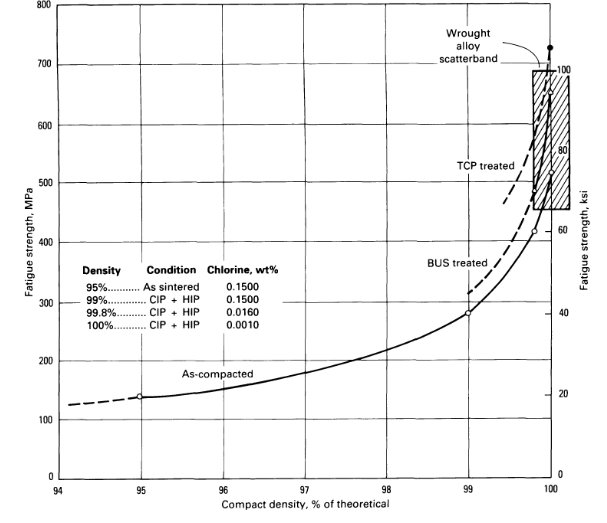
شکل 12-44 تاثیر چگالی بر استحکام خستگی در دمای اتاق نمونه های Ti-6Al-4V پرسکاری شده ایزواستاتیک سرد (CIP) و تفجوشی شده ساخته شده از پودرهای مخلوط عنصری.
توجه کنید که چگالی های بالاتر فقط در ماده با کلرید کم با ساختار شکسته شده (BUS) ممکن هستند.
TCP فراوری ترمومکانیکی؛ HIP پرسکاری ایزواستاتیک گرم
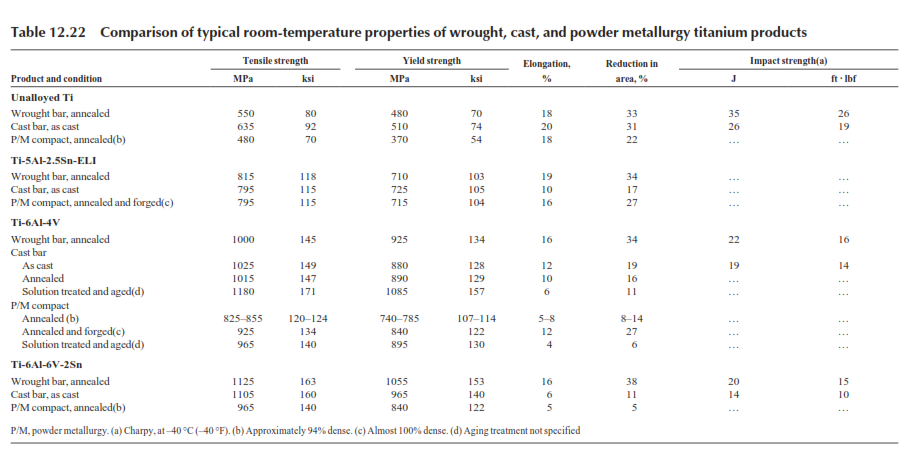
جدول 12-22 مقایسه خواص در دمای اتاق محصولات تیتانیومی کارشده، ریختگی و متالورژی پودر
مقایسه شانه به شانه هر آلیاژ دشوار است بنابراین مقایسه خواصی نظیر اینها باید شامل مثلا نحوه فرآوری، نحوه انجام تست و غیره باشد. در شرایط ایده آل، خواص مکانیکی Ti-6Al-4V ریختگی، P/M حاصل از PA می توانند نزدیک به محصول کارشده باشند. تاثیرات عملیات حرارتی، از جمله چرخه های HIP پس از ریخته گری یا چرخه های HIP روی پودر و نیز نرخ تبرید در یک قطعه تاثیر محسوسی بر خواص می گذارد. هنگامی که میکروساختارهایی قابل مقایسه ایجاد می شوند، خواص قطعات ریختگی یا P/M با چگالی کامل باید برابر با ماده کارشده باشد. معمولا فقط ساختارهای بتاآنیل شده را می توان با خواصی نزدیک در هر سه صورت، تولید کرد. اما توجه کنید که شرایط فرآوری شده آلفا- بتا برای آلیاژهایی نظیر Ti-6Al-4V بسیار بیشتر مورد استفاده قرار می گیرد. مقایسه محصولات ریختگی یا P/M با بهترین آلیاژهای کارشده آلفا- بتا در حال حاضر در دسترس نیست.
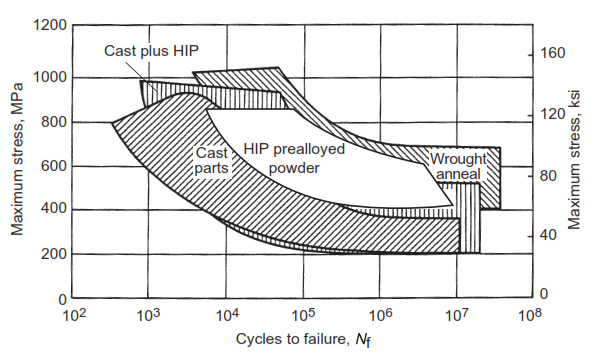
شکل 12-45 نوارهای پراکندگی مربوط به محصولات متالورژی شمش، قطعات ریختگی و متالورژی پودر آلیاژ Ti-6Al-4V
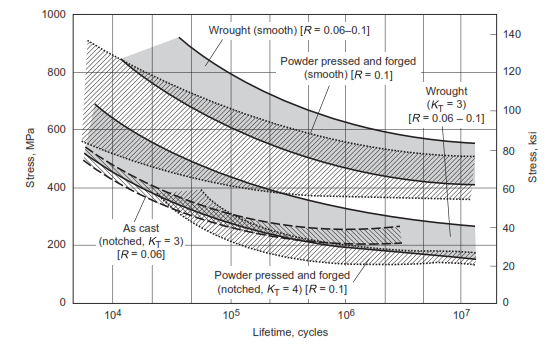
شکل 12-46 تاثیر شیار بر صورت های کارشده، ریختگی و متالورژی پودر آلیاژ Ti-6Al-4V
کارکرد در دمای کم
هنگامی که تبرید از دمای اتاق تا دماهایی زیر °C 0 (°F 32) رخ می دهد، همه فلزات سازه ای دستخوش تغییراتی در خواص در دامنه زیرصفر می شوند. بیشترین تغییرات در خواص هنگامی رخ می دهند که فلز در کاربردهای دما پائین (کرایوژنیک) به کار رود و تا دماهایی بسیار کم نزدیک نقطه جوش هیدروژن مایع و هلیوم مایع سرد شود. کاربردهای کرایوژنیک مربوط به آلیاژهای تیتانیوم شامل قطعاتی مربوط به فضاپیما و موتورهای پرفشار راکت می شود.
بیشتر فلزات و آلیاژهای دارای ساختار بلوری مکعبی مرکز پر (ساختار فاز بتا در تیتانیوم) دستخوش یک استحاله داکتیل به ترد در دماهای بسیار کم می شوند. آلیاژهای تیتانیوم بتا، شبه پایدار بوده و تمایل به برگشت به آلفا و دیگر فازها را دارند در نتیجه، ممکن است در دماهای کم، کاملا ترد نباشند. اما داکتیلیته در دمای کم آلیاژهای تیتانیوم بتا محدود خواهد بود. متعاقبا، آلیاژهای تیتانیوم که به طور کلی بتا هستند یا دارای مقادیر قابل توجهی فاز بتا هستند برای استفاده در دماهای کم، مفید محسوب نمی شوند.
داکتیلیته یک ملاحظه مهم است و جدول 12-23 نشان می دهد که چگونه داکتیلیته آلیاژهایی که داکتیل محسوب می شوند در دماهای کرایوژنیک کاهش می یابد.
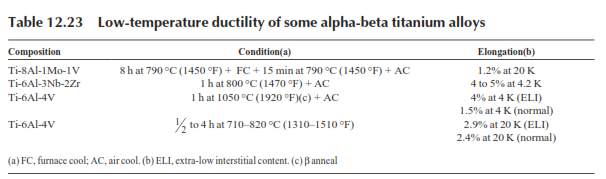
جدول 12-23 داکتیلیته در دمای کم مربوط به برخی آلیاژهای تیتانیومی آلفا- بتا
بسیاری از آلیاژهای تیتانیوم آلفا و آلفا- بتای موجود در دماهای زیرصفر ارزیابی شده اند اما تجربه استفاده در چنین دماهایی فقط مربوط به تعداد کمی از این آلیاژهاست. Ti-5Al-2.5Sn و Ti-6Al-4V دارای نسبتهای استحکام به وزن بالایی در دماهای کرایوژنیک هستند و برای کاربردهای مربوط به دمایی از °C 196- تا 269- (°F 320- تا 452-) ترجیح داده می شوند. در میان این کاربردها، محفظه های تحت فشارکروی قرار دارند که بخشی از سیستمهای کنترل پیشرانش و واکنش در راکتها و تقویت کننده های پرتاب هستند. این محفظه های تحت فشار با جوشکاری قطعات فورج شده نیمکره ای که تا ضخامت دلخواه ماشینکاری شده اند تولید شدند. آلیاژ Ti-5Al-2.5Sn نیز برای پیشرانه های پمپ سوخت برای پمپ کردن هیدروژن مایع استفاده شده اند. تیتانیوم CP برای لوله سازی و دیگر کاربردهای کرایوژنیک در مقیاس کوچک که با تنشهای کمی در حین کارکرد درگیر می شوند به کار می رود.آلیاژ Ti-5Al-2.5Sn معمولا در شرایط میل آنیل شده به کار می رود و دارای میکروساختار 100 درصد آلفاست. آلیاژ Ti-6Al-4V را می توان در شرایط آنیل شده یا در شرایط عملیات انحلالی شده و پیرشده به کار برد. برای بیشینه چقرمگی در کاربردهای کرایوژنیک، شرایط آنیل شده معمولا ترجیح داده می شود.
ناخالصی ها نظیر آهن و بین نشین های اکسیژن، کربن، نیتروژن و هیدروژن تمایل به کاهش چقرمگی این آلیاژها در دمای اتاق و دماهای زیرصفر دارند. برای بیشینه چقرمگی، گریدهای با بین نشین فرا اندک (ELI) برای کاربردهای حساس تعیین می شوند. توجه کنید که مقادیر آهن و اکسیژن گریدهای ELI بسیار کمتر از گریدهای با بین نشین نرمال (NI) می باشند. آهن یک پایدارساز قوی فاز بتاست. گریدهای NI برای کاربردهایی تا °C 196- (°F 320-) مناسب هستند. برای دمایی کمتر از این، معمولا گریدهای ELI بکار میروند. برای گریدهای ELI، استحکام کمتر در دمای اتاق را باید در طراحی مخازن تحت فشار در نظر گرفت.
دو اقدام احتیاطی که باید در کاربرد تیتانیوم و آلیاژهای تیتانیوم در دماهای کرایوژنیک در نظر گرفت عبارتند از:
-
تیتانیوم و آلیاژهای آن را نباید برای انتقال یا ذخیره سازی اکسیژن مایع به کار برد.
-
تیتانیوم را نباید در جاهایی به کار برد که در معرض هوا در دمایی قرار می گیرد که اکسیژن روی سطوح متراکم شود.
هر سایش یا ضربه به تیتانیومی که در تماس با اکسیژن مایع است موجب احتراق می شود. ( برای جلوگیری از این مشکل، مخازن تحت فشار در تماس با اکسیژن مایع در آپولو، بجای Ti-6Al-4V از اینکونل 718 ساخته شدند.)
خواص کششی
تیتانیوم و آلیاژهای تیتانیوم Ti-5Al-2.5Sn و Ti-6Al-4V در دمای اتاق و دماهای زیر صفر در جدول 12-24 ارائه شده اند. افزایش محسوس در استحکام های تسلیم و کششی تیتانیوم و آلیاژهای تیتانیوم تجاری مشهود است زیرا دمای تست از دمای اتاق به °C 253- (°F 423-) کاهش یافت. در دامنه دمایی کرایوژنیک، این آلیاژها دارای بالاترین نسبت های استحکام به وزن در بین همه آلیاژهای با قابلیت جوشکاری ذوبی ای هستند که دارای استحکام تقریبا یکسانی در فلز جوش و فلز پایه می باشند. استحکام های تسلیم و کششی یک جوش ایجادشده با پرتوی الکترونی در ورق نازک از Ti-5Al-2.5Sn-ELI نیز در جدول 12-24 ارائه شده اند.
استحکام های نمونه های شیاردار در جدول 12-24 نشان می دهند که آلیاژهای Ti-5Al-2.5Sn و Ti-6Al-4V چقرمگی شیاری کافی را برای کاربرد در دماهایی به کمی °C 253- (°F 423-) حفظ می نمایند. اما داده های کششی هیچ بهبود محسوسی در داکتیلیته یا چقرمگی شیاری را برای گرید ELI ورق Ti-5Al-2.5Sn نسبت به گرید دارای بین نشین نرمال – مگر در دماهای بسیار کم نشان نمی دهند. عملیات آنیل کاری تبلور مجدد بکار رفته برای قطعه فورج شده از جنس Ti-6Al-4V-ELIبه عنوان راهی برای بهبود چقرمگی شکست در قطعات فورج شده بزرگ و ورق با ضخامت زیاد ایجاد شد.
مقادیر مدول یانگ آلیاژهای تیتانیوم به طور قابل توجهی با کاهش دمای تست مطابق با جدول 12-24 و داده های ترسیم شده در شکل 12-47 افزایش می یابند. مقادیر نسبت پواسون برای آلیاژهای Ti-5Al-2.5Sn و Ti-6Al-4V در شکل 12-48 ترسیم شده اند.
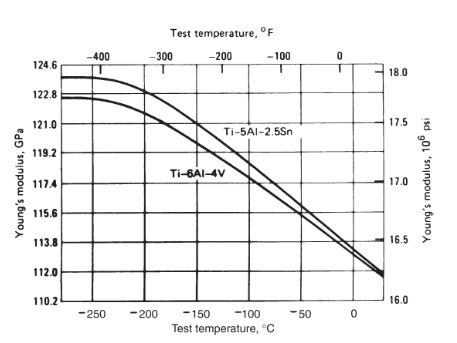
شکل 12-47 مدول یانگ مربوط به آلیاژهای Ti-5Al-2.5Sn و Ti-6Al-4V برحسب دما در محدوده دمای کم
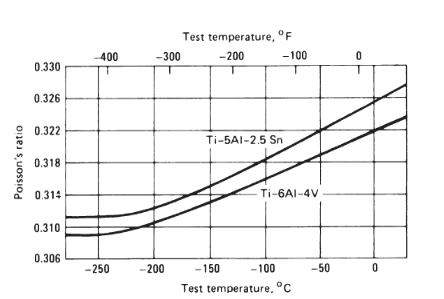
شکل 12-48 ضریب پواسون برای آلیاژهای Ti-5Al-2.5Sn و Ti-6Al-4V برحسب دما در محدوده دمای کم
چقرمگی شکست
داده های موجود درباره چقرمگی شکست کرنش صفحه ای، KIC، در دماهای زیرصفر برای آلیاژهای Ti-5Al-2.5Sn و Ti-6Al-4V در جدول 12-25 به همراه داده های مربوط به سازه های جوشکاری شده ارائه گردیده اند. این داده ها نشان می دهند که یک کاهش متوسط در چقرمگی شکست با کاهش دمای تست از دمای اتاق تا دماهای زیرصفر وجود دارد. اما، گریدهای ELI دارای چقرمگی بهتری نسبت به گریدهای متناظر با بین نشین نرمال در دماهای زیرصفر هستند. این داده های محدود برای سازه های جوشکاری شده با پرتوی الکترونی نشان می دهند که در °C 196- (°F 320-) کاهش اندکی در نواحی گدازش و متاثر از گرما در مقایسه با فلز پایه در جوش های Ti-6Al-4V-ELIوجود دارد.
استحکام خستگی
مقادیر استحکام خستگی در تعداد چرخه 106 برای فلز پایه و سازه های جوشکاری شده از آلیاژ تیتانیوم در دمای اتاق و دماهای زیرصفر بر پایه نتایج تست های خستگی محوری و پیچشی در جدول 12-26 ارائه شده اند. برای نمونه های بدون شیار از فلز پایه، در هنگام کاهش دمای تست از دمای اتاق تا °C 196- (°F 320-) استحکام خستگی به طور محسوسی افزایش یافت. هنگامی که دمای تست تا °C 253- (°F 423-) کاهش یافت، استحکام های خستگی برای برخی سری های آلیاژهای تیتانیوم کمتر از °C 196- (°F 320-) در نمونه های بدون شیار، بسیار کمتر از نمونه های شیاردار بودند. در °C 196- و 253- (°F 320- و 423-)، نمونه های جوشکاری شده دارای استحکام های خستگی کمتری نسبت به نمونه های فلز پایه بودند.
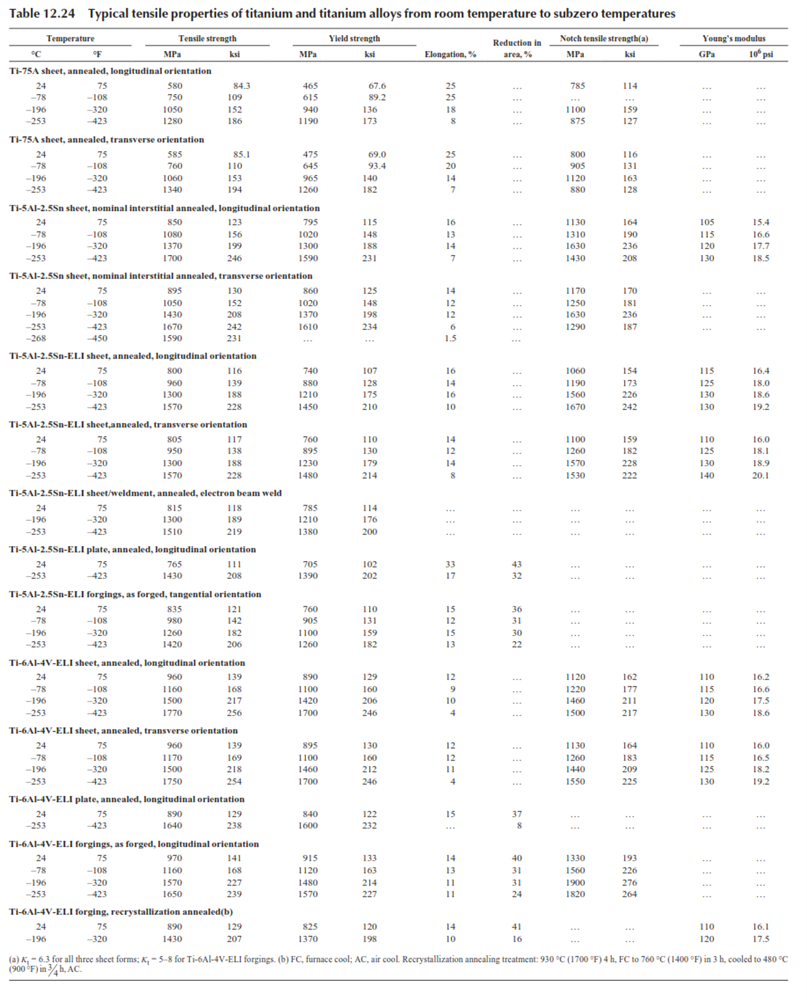
جدول 12-24 خواص کششی تیتانیوم و آلیاژهای تیتانیوم از دمای اتاق تا دماهای زیرصفر
بنابراین، در طراحی سازه های جوشکاری شده، آلیاژهای تیتانیومی که در دماهای زیرصفر در معرض بارگذاری خستگی قرار می گیرند نواحی جوش معمولا باید ضخیمتر از دیگر نواحی باشند. نیمکره های مربوط به مخازن تحت فشار کروی طوری ماشینکاری می شوند که مقاطع جوشکاری شده لب به لب در جوشهای استوایی کره، ضخیمتر از دیگر مقاطع بجز پورت های ورودی و تخیله باشند.
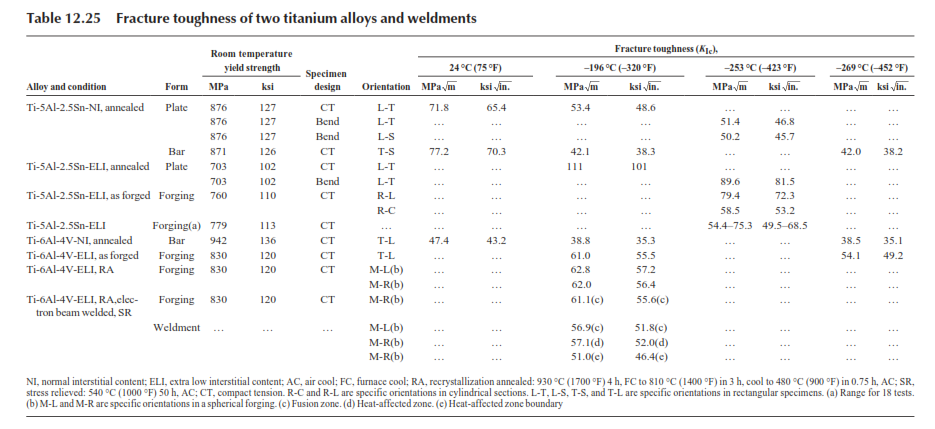
جدول 12-25 چقرمگی شکست دو آلیاژ تیتانیوم و سازه های جوشکاری شده
نرخ رشد ترک خستگی
داده های مربوط به نرخ FCP برای آلیاژهای Ti-5Al-2.5Sn و Ti-6Al-4V در دمای کم در شکل 12-49 ترسیم شده اند. در بخشی از دامنه شدت تنش، نرخ رشد ترک خستگی مربوط به Ti-6Al-4V-ELI در دماهای کرایوژنیک نسبت به دمای اتاق در مقادیر یکسان ΔK، بیشتر هستند.
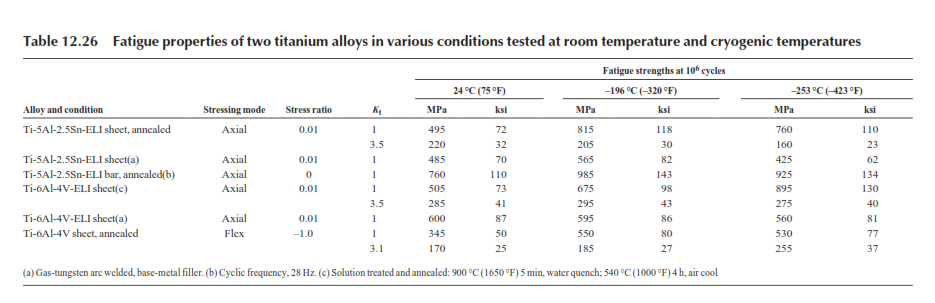
جدول 12-26 خواص خستگی دو آلیاژ تیتانیوم در شرایط مختلف تست شده در دمای اتاق و دماهای کرایوژنیک
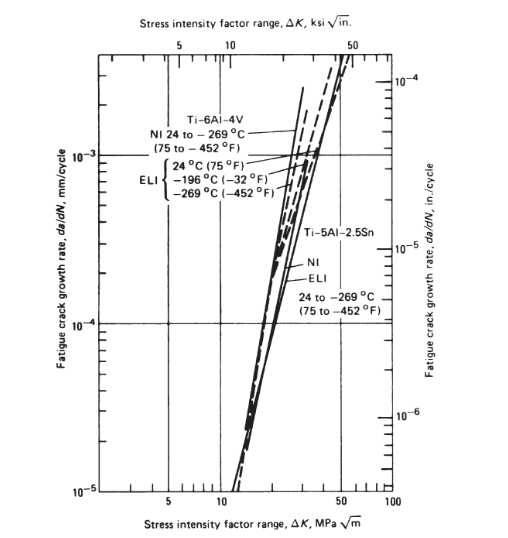
شکل 12-49 نرخ انتشار ترک خستگی مربوط به آلیاژهای Ti-6Al-4V و Ti-5Al-2.5Sn در ناحیه با دمای پائین.
NI مقدار بین نشین نرمال و ELI مقدار بین نشین فرا اندک
پایان فصل دوازدهم