مطابق با جدول 7-1 برای سه هواپیمای نظامی اخیر ایالات متحده یک تفاوت نسبتا زیاد بین مقدار تیتانیوم برنامه ریزی شده و مقدار واقعی آن وجود دارد.
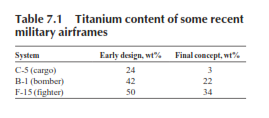
جدول 7-1 مقدار تیتانیوم برخی بدنه های هواپیمای اخیرا ساخته شده
بنابراین برای کاهش هزینه استفاده از تیتانیوم با تولید تکنولوژیهای نزدیک به شکل نهایی (NNS) و با شکل نهایی انگیزه کافی وجود دارد. نتیجه حاصل از این تلاشهای مربوط به کاهش قیمت، بکارگیری و پذیرش بیشتر قطعات ریختگی تیتانیوم است. (فصل 6 را برای اطلاعات بیشتر درباره قطعات ریختگی ببینید.)
تکنولوژی متالورژی پودر (P/M) بعنوان فرایندی جایگزین برای تولید قطعات ایجاد شد. محصولات P/M دارای خواصی مشابه با دیگر روش های در حال تولید هستند. جدول 7-2 خواص تیتانیوم و برخی آلیاژهای تیتانیوم به شکل های کارشده، ریختگی و پودر را در دمای اتاق نشان می دهد. اما فرایندهای مربوط به تولید پودرهای تیتانیومی آهسته و پرهزینه هستند و این امر منجر به رشد آهسته متالورژی پودر بعنوان یک روش تولید قطعات تیتانیومی شده است.
مهمترین ملاحظات در تولید قطعات P/M عبارتند از مقدار اکسیژن، خلوص و موارد آلوده کننده. پودرها بویژه پودرهای بسیار ریز را بابد با دقت بسیار زیاد مدیریت کرد زیرا این پودرها تمایل زیادی به اکسیژن دارند و می توانند بشدت آتش زا باشند. خلوص برای همه محصولات پودری مهم است و برای متراکم سازی پودرهای عنصری مخلوط شده که مقدار جای خالی ها باید در کمینه مقدار خود باشد عاملی حساس محسوب می شود. مقدار کلرید پسماند یک عامل اصلی در مقدار تخلخل پسماند محصول نهایی است. آلوده سازها برای عملکرد خستگی مضر هستند و برای خواص خستگی قابل حصول، عاملی کلیدی به حساب می آیند.
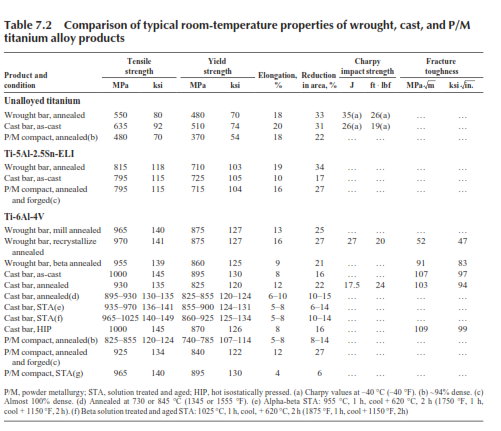
جدول 7-2 مقایسه خواص محصولات کارشده، ریختگی و P/M از آلیاژ تیتانیوم در دمای اتاق
تولید تیتانیوم P/M باعث ایجاد قابلیتی برای تولید واقعی نزدیک شکل نهایی علاوه بر خواص مکانیکی می شود که معادل با محصول کارشده یا حتی برتر از آن می باشند. این بدلیل نبودن بافت و جدایش و نیز بدلیل ساختار دانه ذاتا ریز و یکنواخت در محصولات P/M تیتانیوم است. سطوح استحکام برابر با محصولات کارشده همراه با ماشین کاری و قراضه سازی کمتر باعث می شوند که محصولات P/M تیتانیومی جایگزین هایی جذاب برای آلیاژهای کارشده و قطعات ریختگی تیتانیومی باشند.
برای بکارگیری کامل قابلیت P/M تیتانیوم، تلاش قابل توجهی برای کاهش هزینه قطعات پودری و پایه پودری صورت گرفته است. هزینه های مربوط به پودر بهینه و متراکم سازی برای تولید نمونه های متراکم با چگالی کامل و کیفیت بالا، به عنوان مانعی بر سر راه استفاده از پودر در حوزه آلیاژ تیتانیوم باقی مانده اند. تولید بهتر پودری با هزینه کم و روشهای تولید کم هزینه همراه با روشهای آزمون غیرمخرب (NDT) و استانداردهای NDT واقعی هنوز هم به عنوان یک نیاز مورد احتیاج هستند.
آلیاژهای به کار رفته در کاربردهای متالورژی پودر
ترکیبات آلیاژی زیادی به شکل پودر تولید شده اند، این آلیاژها عبارتند از:
-
Ti-6Al-4V
-
Ti-6Al-6V-2Sn
-
Ti-5Al-5Mo-1/5 Cr
-
Ti-5Al-2Sn-2Zr-4Cr-4Mo
-
Ti-6Al-2Sn-4Zr-2Mo
-
Ti-6Al-2Sn-4Zr-6Mo
-
Ti-10V-2Fe-3Al
-
Ti-11/5Mo-6Zr-4/5Sn
بیش از 90 درصد تلاش های توسعه ای در P/M فقط از آلیاژ آلفا- بتای Ti-6Al-4V استفاده کرده اند و بیشتر ارجاعات در این فصل شامل این آلیاژ می شود.
ترکیب های تیتانیومی P/M به کار رفته بر مبنای ترکیب های آلیاژهای کارشده مرسوم هستند به طوری که هیچ آلیاژ مشخصی به طور ویژه برای P/M وجود ندارد. این موضوع برای قطعات ریختگی نیز صادق است. به کارگیری یک ترکیب شیمیایی جدید و یک فرایند جدید در چرخه تولید بینهایت دشوار است. این دشواری به ویژه مربوط به کاربردهای حساس نظیر صنعت هوافضا می شود و از آغاز پیدایش تجارت تیتانیوم در حدود میانه قرن بیستم، باعث پیشرفت آن شده است. این موضوع همچنین منجر به محصولاتی جدا از محصولات شمشی و ایجاد داده هایی شده است که جایگزینی مستقیم را بر اساس ترکیب شیمیایی محصول تشویق می کند. دلیل دیگر برای این موضوع، در دسترس بودن مواد اولیه و محصولات کارشده کارخانه می باشد که غالبا به عنوان منبع خام در تولید پودر به حساب می آیند.
یکی دیگر از خصوصیات مهم فراوری P/M، قابلیت ایجاد ترکیب های منحصربفرد و غیراستانداردی است که ممکن است نتوان با روشهای دیگر آنها را فراوری کرد. فراوری انجماد سریع برای نزدیک به دو دهه بررسی شده و باعث ایجاد فرصت های منحصربفرد اما با هزینه بالا شده است. فصل 14 برخی جنبه های پژوهش مستمر مربوط به خواص بهتر ایجاد شده توسط روش انجماد سریع را تشریح می کند.
روشهای تولید متالورژی پودر تیتانیوم
تکنولوژی P/M آلیاژ تیتانیوم به عنوان یک روش شکل نهایی در یک ربع قرن اخیر توسعه یافته است هرچند روشهای P/M برای فلزات صنعتی متداول تر نظیر آلیاژهای آهنی، آلیاژهای آلومینیوم و آلیاژهای مس برای سالهای طولانی به کار رفته است. بطور کلی، قطعات تیتانیوم P/M به دو روش مختلف تولید می شوند. در روش اختلاط عنصری (BE)، مخلوطی از پودرهای عنصری همراه با آمیژان یا دیگر افزودنی های دلخواه بصورت سرد به شکل مورد نظر پرس شده و متعاقبا تا چگالی بالاتر و ترکیب شیمیایی یکنواخت تفجوشی شدند. در روش پیش آلیاژی (PA) شکل دهی داغ روی پودر تولیدی از ماده پیش آلیاژی شده اجرا می شود.
روش BE قطعاتی با خواص پائین تر اما در یک قیمت کمتر تولید می کند. اساسا روش BE یک روش پرس سرد (CP) یا پرس ایزواستاتیک سرد (CIP) و فرآیند تفجوشی در خلا است که منجر به ماده ای با چگالی ای کمتر از چگالی کامل می شود. در نتیجه، این روش باعث محصولاتی با قیمت نسبتا کمتر می شود که دارای استحکام کششی، چقرمگی شکست و نرخ رشد ترک خستگی خوب هستد. پیشرفت در انتخاب پودر، روشهای فشرده سازی و فراوری پسا فشرده سازی امکان ایجاد نمونه های متراکم BE با چگالی کامل را فراهم کرده و ادعا شده است که خواصی معادل با محصولات شمشی یا بالاتر از آن را می توان بدست آورد.
از طرف دیگر، نمونه های متراکم پودری PA همواره دارای چگالی کامل و خواص مکانیکی خوب از جمله استحکام خستگی می باشند. قطعات BE نسبتا ارزان بوده و می توانند برای کاربردهای غیرحساس مناسب باشند. هدف از روش PA، تولید قطعاتی با عملکرد عالی در شکل های پیچیده با خواصی قابل مقایسه با قطعات شمشی همان آلیاژ یا برتر از آن می باشد.
فرآیند ساخت پودر
پودر عنصری. فرایندهای تولید پودر مربوط به تیتانیوم و آلیاژهای آن با توسط واکنش پذیری ذاتی بالای این فلز محدود می شوند. در نتیجه، فرایندهای غیرسنتی و پرهزینه تبدیل به اصل پذیرفته شده در صنعت در آمده اند. نرمه های اسفنج تیتانیوم و پودر آمیژان آلومینیوم- وانادیوم تولید شده توسط روشهای متداول P/M در فرایند BE برای تولید قطعات آلیاژی تیتانیومی P/M استفاده شده اند. نرمه های اسفنج تیتانیومی به عنوان محصولات جانبی فرآیند احیای منیزیم کرول مربوط به تیتانیوم بدست می آیند. نرمه های اسفنج پیش از متراکم سازی له می شوند و هرچند بیشتر این نرمه های اسفنجی دارای اندازه ای قابل قبول هستند اما نرمه هایی وجود دارند که مناسب فرایند متراکم سازی از طریق بازذوب قوسی در خلا (VAR) نیستند. بنابراین، این نرمه ها یک منبع نسبتا کم هزینه از پودر تیتانیوم عنصری را تشکیل می دهند. نرمه های اسفنجی احیاشده با سدیم از نرمه های اسفنجی تولید شده توسط منیزیم خالصتر بودند اما احیای سدیم، در حال حاضر یک روش تولید برای تیتانیوم بحساب نمی آید و پودرهای حاصل از این منبع دیگر وجود ندارند. پودر حاصل از احیای منیزیمی اسفنج که در خلا تقطیر می شود خالصتر از نرمه های اسفنجی قبلی است. بدلیل تعطیلی کارخانه های درگیر در صنعت تیتانیوم در اواخر دهه 1980 و دهه 1990، نرمه های اسفنج نسبت به سالهای قبل کمتر در دسترس هستند و منابع جایگزین پودر تیتانیوم عنصری در حال توسعه یافتن هستند. البته، پودرهای عنصری را همچنین، می توان به همان روشهای بکار رفته برای تولید پودر پیش آلیاژی شده به کار برد. پودر برپایه نرمه های اسفنج دارای شکلی بی قاعده است که در تولید اشکال خام (پرسکاری شده اما تفجوشی نشده) دارای استحکام کافی برای جابجایی در عملیات های تفجوشی بعدی یک مزیت محسوب می شود.
قطعات تولید شده با پودرهای BE در شکل 7-1 نشان داده شده اند.
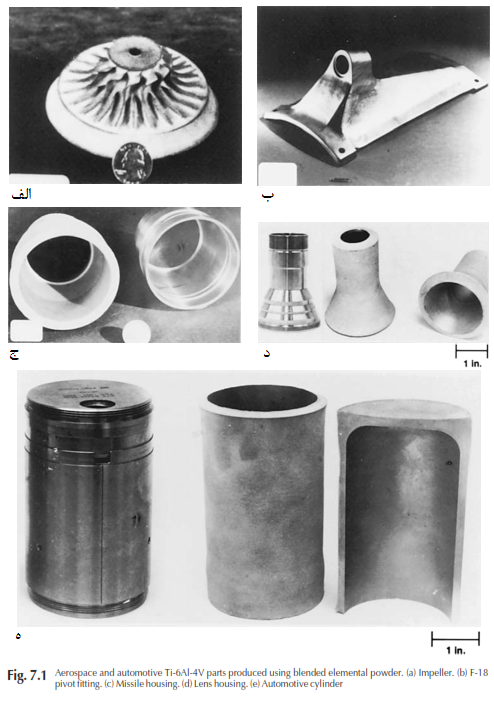
شکل 7-1 قطعات مربوط به هوافضا و خودرو از جنس Ti-6Al-4V تولید شده با استفاده از پودر عنصری مخلوطشده
الف- پیش برنده ب- اتصال محوری در F-18 ج- روکش موشک د- روکش عدسی ه- سیلندر خودور
پودر پیش آلیاژ شده. هر ذره از یک پودر PA، ترکیب آلیاژی مشابهی با آلیاژ دلخواه نشان می دهد. این بدان علت است که مواد اولیه فرایند تولید پودر PA از ماده ریخته گری شده یا آلیاژ کارشده استفاده می کند. هرچند صنعت سوپرآلیاژ اتمیزاسیون گازی را در تولید پودر به کار گرفته است اما آلیاژهای تیتانیوم نه تنها بر اتمیزاسیون گازی بلکه بر سایر فرایندهای منحصر به ترکیب و متالورژی تیتانیوم نیز تکیه دارند چرا که تیتانیوم یک فلز بسیار واکنش پذیر است. برخی از فرایندهای تولید پودر PA عبارتند از:
-
فرایند الکترود چرخان (REP) که یک فرایند اتمیزاسیون گریز از مرکزی است.
-
فرایند الکترود چرخان پلاسمایی (PREP) که یک فرایند اتمیزاسیون گریز از مرکزی است.
-
فرایند هیدروکسید شدن/دی هیدروکسید شدن (HDH).
-
فرایند اتمیزاسیون گازی (GA).
فرآیندهای دیگری نیز وجود دارند یا درحال توسعه هستند اما در حال حاضر استفاده تجاری ندارند. این روشهای ارزیابی شده عبارتند از:
-
پودر تحت خلا (PSV)
-
ریخته گری ساچمه ای پیوسته (CSC)
-
قطره آویخته (P-D)
-
احیای سریع بخارهای (آلیاژ) تیتانیوم
تلاشهای بیشتری به سمت تولید تیتانیوم عنصری و پودر PA توسط روشهای شیمیایی و دیگر روشهای کاملا مختلف پرداخته شده است. توسعه روش جدید که باعث تولید یک پودر اولیه ارزان و با کیفیت عالی شود پیش نیاز گسترش بازار محصولات P/M تیتانیوم است.
تولید کنونی پودر PA توسط فرایند HDH از خردکردن مواد ترد برای تولید پودر استفاده می کند. تیتانیوم و مرسوم ترین آلیاژهای آن با گرمایش در یک اتمسفر هیدروژنی دچار تردی هیدرژنی می شوند. جامدهای مختلفی را می توان به عنوان ماده اولیه به کار برد هرچند مواد با ضخامت کم دارای نسبت سطح به حجم بالاتر بوده و با سرعت بیشتری تبدیل به هیدروکسید می شود. پس از هیدروکسید شدن، محصول به شدت شکننده است و بطور خودبخودی به پودر احیا می شود یا به سادگی ساییده شده و تبدیل به پودر می شود. سپس پودر با گرمایش در خلا دی هیدروکسید می شود.
مورفولوژی پودر HDH به مورفولوژی نرمه های اسفنج شبیه است. هر دو مورد ذراتی بی قاعده هستند که دارای چگالی انباشتگی کم و نرخ کم جریان پودر در قالب ها یا قوطی ها هستند. فرایند HDH به افزایش مقدار اکسیژن تمایل دارد و آلوده کننده های دیگری نیز ممکن است وجود داشته باشند. در نتیجه، پودرهای HDH ممکن است برای کاربردهای حساس مناسب نباشند.
فرایندهای GA و الکترود چرخان (یعنی REP و PREP) ذراتی کروی تولید می کنند. چنین پودرهایی به سادگی جریان پیدا می کنند و تا چگالی پایدار بسیار بالایی انباشته می شوند اما در پرسکاری سرد بخوبی اتصال دهی نمی شوند. در GA از اتمیزاسیون گریز از مرکزی استفاده نمی شود اما از REP و PREP استفاده می کنند. در GA، یک فلز مذاب از درون حلقه ای از جریان شدید گاز خنثی جریان می یابد که در این حلقه، جریان فلز توسط فشار گاز اتمیزه می شود.
REP از یک قوس تنگستنی برای ذوب کردن تیتانیوم یا آلیاژهای آن از یک ماده خام در حال چرخش استفاده می کند. مذاب سریعا به شکل قطراتی در می آید تا در اتمسفر خنک شود. در یک شکل سخت شده، این قطرات در انتهای یک اتاقک جمع می شوند. PREP از یک قوس پلاسما برای ذوب کردن آلیاژ از یک ماده خام درحال چرخش برای تولید یک پودر استفاده می شود که در REP نیز همین گونه است. (اگر اطلاعات بیشتری مورد نیاز باشد GA، REP و PREP در متون مختلف متالورژی پودر پوشش داده شده اند. GA نیز در کتابهای مربوط به سوپرآلیاژها- که این فرایند بطور گسترده ای برای آنها به کار می رود- توضیح داده شده است.)
مشخصه اصلی REP و PREP قابلیت حفظ مقدار عنصر بین نشین با حداقل آلودگی است. یک مزیت PREP بر REP حذف آخال های تنگستنی است که در فرایند REP توسط منبع گرمای الکترود تنگستنی تولید می شوند. هر دو فرایند دارای مزیت تمیزی نسبت به GA هستند که در آن، آخال ها ممکن است از هر سرامیک به کار رفته در نازل محفظه تولید شوند.
برای پودرهای PA، برای بهبود عملکرد محصول نهایی با حذف آلوده کننده ها یا با تنظیم کردن میکروساختار نهایی، چند فرایند ایجاد شده اند که عبارتند از:
-
دسته بندی جت (جریان سریع)
-
جداسازی الکترواستاتیک
-
گاززدایی الکترودینامیک
مشخصه یابی ذرات پودر تولید شده و ذرات خارجی احتمالی در مرحله پودر سست می تواند به کنترل کیفیت کمک کند. به وضوح نشان داده شده است که میکروساختار پایه و آلوده کننده ها بر خواص مکانیکی به ویژه خستگی اثر می گذارند. روشی که در جداسازی ذرات خارجی مربوط به دسته بندی بعد از آن (ولی نه به عنوان یک روش تمیزسازی برای تیتانیوم) مفید است خاکشویی است که بین ذرات برمبنای چگالی آنها تمایز قائل می شود.
پودر تولیدی توسط فرایندهایREP و PREP از لحاظ مشخصات، درشت تر از پودرهای سوپرآلیاژی GA است. آنالیز شیمیایی و الک پودر Ti-6Al-4V حاصل از REP به کار رفته برای قطعات هوافضایی در جدول 7-3 الف و ب ارائه شده اند. شکل 7-2 برخی قطعات ساخته شده از پودر PA را نشان می دهد.
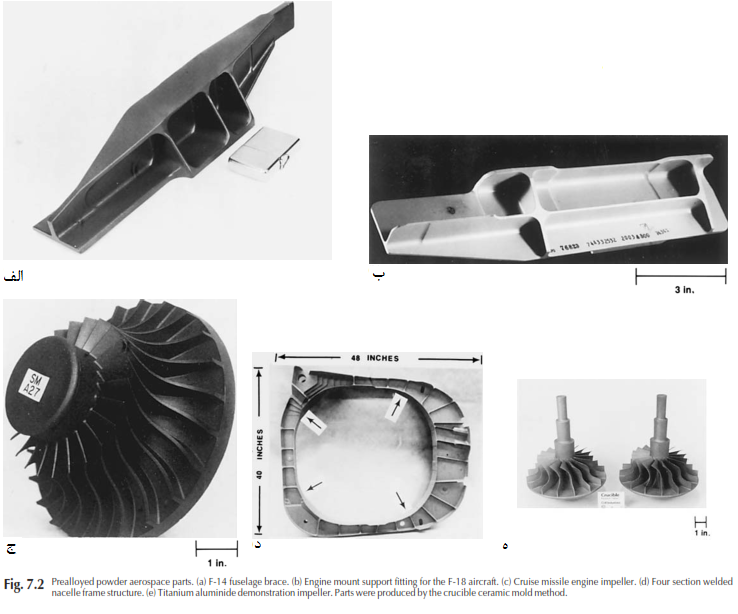
شکل 7-2 قطعات هوافضایی از پودر پیش آلیاژی شده
الف- تقویت بدنه F-14 ب- ساپورت موتور برای هواپیمای F-18
ج- پیش برنده موتور موشک کروز د- سازه چهارچوب گهواره ای جوشکاری شده از 4 مقطع ه- پیش برنده از جنس آلومیناید تیتانیوم
قطعات توسط روش قالب سرامیکی بوته ای تولید شدهاند.
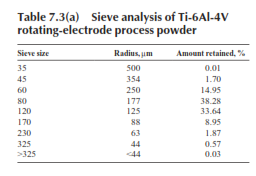
جدول 7-3 الف - آنالیزالک پودر فرایند الکترود چرخان Ti-6Al-4V
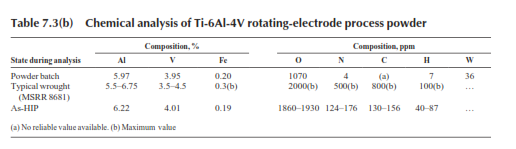
جدول 7-3 ب - آنالیز شیمیایی پودر فرایند الکترود چرخان Ti-6Al-4V
متراکم سازی و شکل دهی
فرایندهای متراکم سازی و شکل دهی مختلفی وجود دارند. فرایندهای متراکم سازی عبارتند از:
-
پرسکاری مکانیکی در قالب (CP) بعلاوه تفجوشی در خلا
-
پرسکاری ایزواستاتیک سرد (CIP) بعلاوه تفجوشی
-
پرسکاری گرم در خلا (VHP)
-
پرسکاری ایزواستاتیک گرم (HIP)
-
CIP بعلاوه تفجوشی در خلا بعلاوه HIP (CHIP)
در این میان، ادعا شده است که سه مورد آخر قابلیت تولید نمونه های متراکم با چگالی کامل را دارند. در بین این سه روش، HIP در یک مخزن تحت فشار گرم شده یا اتوکلاو، مرسومترین روش برای قطعات حساس است. با اعمال همزمان دما و فشار ایزواستاتیک، چگالی کامل در قطعه حاصل می شود.
متراکم سازی از طریق پرس باعث فشرده سازی سریع (یا دمای کمتر) پودر درون یک قوطی شکل داده شده دارای خلا می شود. فشارهای بسیار بالایی قابل دستیابی است و با طراحی های مشخص قالب، ادعا می شود که پس از پرسکاری و تفجوشی در خلا، چگالی نزدیک به 100 درصد حاصل می شود.
پودر را می توان توسط NHP فشرده ساخت. در این فرآیند، پودر بصورت گرم در یک پرس فورج وفق داده شده با سیستم خلا، فشرده سازی می شود. قالب ها پودر را تا چگالی 100 درصد به شکل لازم پرس می کنند. به نظر می رسد معایب عمده این فرآیند، فقدان انعطاف پذیری در شکل های قابل پرس کاری و اندازه قطعات قابل تولید باشند.
با توجه به HIP، این فرایند از تجهیزات متراکم سازی یکسانی مشابه با تجهیزات مربوط به بستن تخلخل ریخته گری استفاده می کند هرچند شرایط دما و فشار متفاوت هستند. بیشتر فرایندهای HIP از فناوری قوطی فلزی استفاده می کنند و شکلهای تقریبا پیچیده ای را می توان بدست آورد. ماشین کاری محدودی در طراحی قوطی ها یا قالب ها به کار می رود اما ضرورت انجام NDT گستره دستیابی به شکل نزدیک به نهایی (NNS) قابل حصول را محدود می کند. ملاحظات عملی در باره پیچیدگی قطعه همچنین بر هندسه و حجم نمونه های متراکم نهایی اثر می گذارد. قوطی فلزی توسط جدیدترین روشهای مربوط به فلز ورقی شکل به پیکربندی مطلوب تبدیل می شوند. این روشها شامل خمکاری برک، شکل دهی پرسی، ریسندگی و شکل دهی سوپرپلاستیک می شوند. فولاد کربنی بهترین ماده برای محفظه است زیرا کمترین واکنش پذیری را با تیتانیوم دارد. در نتیجه واکنش، کاربید تیتانیوم تشکیل می شود و در نتیجه از واکنش بیشتر جلوگیری می کند. یک محدودیت مربوط به همه کاربردهای HIP، اندازه بزرگترین اتاقک HIP است. قطر بیشینه موجود، اندکی بیش از m 1.2 (ft 4) است درحالیکه طول بیشینه تقریبا m 2.4 (ft 8) است.
گونه ای از فرایند HIP، فرایند قالب سرامیکی بوته ای (CCMP) دارای مشابهت هایی با تکنولوژی به کار رفته برای فرایند ریخته گری دقیق است. الگوهای مومی شکل گرفته ساخته شده و قالب سرامیکی تولید می شود. پس از موم زدایی و پخت، قالب تخلیه شده، پرشده، گاززدایی و آب بندی می شود. (این امر به شیوه کاربرد قوطی های فلزی در فرایند استاندارد عمل آوری HIP بستگی دارد.) سپس قالب آب بندی شده تحت پرسکاری گرم ایزواستاتیک قرار می گیرد. HIP-CCMP قادر به تولید شکل های پیچیده تری نسبت به شکل های تولیدشده توسط HIP به روش تکنولوژی قوطی استاندارد می باشد.
شکل ها را نیز می توان توسط پرسکاری ایزواستاتیک سرد (CIP) تولید کرد و قالبها نیز نسبت به قالبهای HIP، ارزانتر هستند. درحالیکه CIP مشابه با HIP است اما دقت کمتری داشته و نسبت به HIP ارزانتر است. در CIP، تفجوشی در خلا (گرمایش دمابالا برای یک دوره طولانی)، برای رسیدن به چگالی 95 تا 99 درصد لازم است. به طور کلی، فرایندهای HIP برای رسیدن به چگالی 100 درصد ضروری است.
پودرهای عنصری مخلوط شده. روشهای فشرده سازی پودر BE پایه عبارتند از CIP و متراکم سازی توسط پرس سرد (CP). پس از این روشها، تفجوشی در خلا را می توان برای رسیدن به چگالی 95 درصد انجام داد. همچنین می توان از HIP برای رسیدن به چگالی تقریبا 100 درصدی استفاده کرد. تاکید قابل توجهی بر CIP، CIP بعلاوه تفجوشی در خلا و CIP بعلاوه HIP انجام شده است.
کاهش قیمت تحقق یافته در فشرده سازی و شکل دهی از کاهش قیمت ماده خام و زمان کمتر چرخه جابجایی و فرایند نتیجه می شود. استفاده از BE موجب می شود چگالی کمتر از 100 درصد قابل قبول باشد. نمونه های متراکم BE معمولا دارای چگالی قبل از تفجوشی (چگالی خام) بیش از 85 درصدی هستند. تفجوشی در خلا می تواند باعث چگالی های حدود 95 درصدی شود و کنترل دقیق اندازه پودر و توزیع اندازه پودر می تواند باعث چگالیهای 99 درصدی شود.
تخلخل در نمونه های متراکم BE، نتیجه پسماندهای کلریدی در اسفنج است. ادعا شده است که استفاده از نرمه های اسفنج تقطیرشده در خلا یا دیگر اسفنجهای با کلرید کم، باعث تولید نمونه های متراکم 100 درصد چگال می شود. تفجوشی در دماهایی در محدوده °C 1100 تا 1315 (°F 2400-2100) در خلا برای جلوگیری از آلایندگی گاز انجام می شود. برای ایجاد پیوندهای خوب بین ذرات و برای همگن سازی ترکیب، دمای تفجوشی بالایی لازم است. در همه آلیاژهای متداول تیتانیوم دمای تفجوشی بسیار بالاتر از دمای تحول بتا است.
CP بعلاوه تفجوشی در حال حاضر روش ترجیحی برای تولید قطعات از چگالی کم تا چگالی 80 درصدی برای کاربردهای غیرحساس می باشد. قطعات با چگالی بالاتر با استفاده از CIP بعلاوه تفجوشی ساخته می شوند. قالبهای الاستومتری برای تولید قطعاتی با اشکال بسیار پیچیده نظیر پیش برنده نشان داده شده در شکل 7-3 بکار می روند. اندازه قطعه به قطر بیشینه تقریبا cm 60 (in. 24) محدود می شود؛ طول با توجه به نوع CIP مورد استفاده محدود می شود. تلرانس بعد طولی با استفاده از CIP بعلاوه تفجوشی تقریبا mm/mm 0.02± (in/in. 0.02±) است. برای چگالی بیشینه BE و خواص بهینه در قطعه پرداخت شده، فرایند CHIP استفاده می شود. یک قطعه به وزن kg 15.3 (lb 34) و با چگالی 100 درصد از بدنه هواپیما که به روش CHIP از پودر BE Ti-6Al-4V (با مقدار کلرید بسیار کم) ساخته شده در شکل 7-4 نشان داده شده است. در مقابل، یک بیلت کارشده به وزن kg 45 (lb 100) در صورت استفاده از روشهای سنتی مرتبط با شمش مورد نیاز می بود.
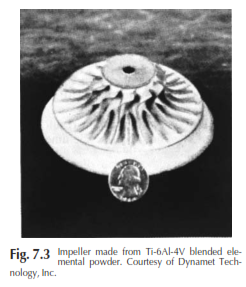
شکل 7-3 پیش برنده ساخته شده از پودر عنصری مخلوط شده Ti-6Al-4V
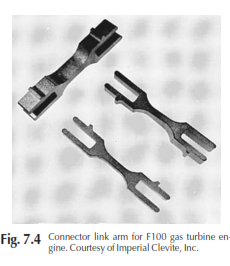
شکل 7-4 بازوی اتصال مربوط به موتور توربین گازی F100
پودرهای پیش آلیاژی شده. به نظر می رسد روش اصلی برای متراکم سازی پودرهای PA فرایند HIP باشد. هرچند روشهای CCMP و VHP نیز در این مورد امتحان شده اند. فراوری مستقیم پودرهای PA به محصولات میل را می توان انجام داد.(این امر درباره پودرهایBE نیز ممکن است.) هرچند از نظر مقرون به صرفه بودن محل تردید است اما ورق ضخیم و میله به این صورت تولید شده اند. پیش شکل های مربوط به فورجکاری بعدی نیز درنظر گرفته شده اند. ( استفاده از پیش شکل در حوزه P/M متداول است؛ بیلت های پیش متراکم شده حاصل از HIP یا اکستروژن در حوزه سوپرآلیاژها مرسوم هستند.) بیلت های پیش متراکم شده به عنوان ماده اولیه برای فورجکاری همدمای قطعات توربین گازی هواپیما استفاده می شوند.
CP معمولی به علاوه تیتانیوم BE P/M تفجوشی شده ممکن است به چگالی نظری 94 تا 96 درصد دست یافته شود. کار یا فرآوری بیشتری برای دستیابی به چگالی کامل و برای بیشینه سازی خواص لازم است. استفاده از آلیاژهای تیتانیوم با چگالی بالا (اما کمتر از چگالی کامل) بعنوان پیش شکل می تواند موجب فوایدی شود. پیش شکل تیغه کمپرسور نمونه سازی شده بصورت ایزواستاتیک سرد با پودرهای عنصری مخلوط شده Ti-6Al-4V پرس و تفجوشی شدند تا چگالی تقریبا 95 درصدی بدست آید. محصول فورج شده پرداخت شده ای فقط با یک بار پرسکاری و تفجوشی بدست آمد که منجر به کمینه حرارت دهی شد (شکل 7-5). بنابراین، حداقل ضایعات نیز به دست آمد. فورج کاری معمولی این قطعه به مقدار قابلتوجهی شمش بیشتر و چندین مرحله قطع فرایند نیاز داشت. بهبود قابلتوجه در قیمت نیز با فراوری P/M تحقق یافت.
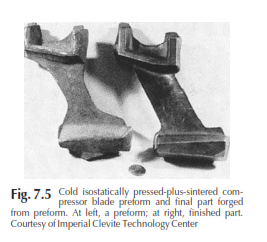
شکل 7-5 پیش شکل تیغه کمپرسور پرس کاری شده بصورت ایزواستاتیک سرد بعلاوه تفجوشی. در سمت چپ پیش شکل، در راست قطعه پرداخت شده
برای کنترل بهتر ریرساختار و کمینه سازی واکنشهای احتمالی با قوطی، فشرده سازی توسط HIP معمولا در دمایی کمتر از دمای تحول بتا انجام می شود. تمیزی پودر یک عامل اصلی در کنترل خواص قطعات PA متراکم سازی شده است. حتی سطحی بسیار کم از ذرات خارجی می تواند منجر به کاهش محسوس خواص خستگی گردد.
عملیات پسا فشرده سازی
آلیاژهای P/M تیتانیوم گاهی در معرض عملیات پسا فشرده سازی قرار می گیرند. به این نمونه های متراکم که قرار است بعدا روی آنها کار انجام شود پیش شکل گویند. کاربرد پیش شکلهای P/M میتواند موجب ارتقای سطح خواص محصولات تیتانیوم آلیاژی شود زیرا مهندسان بسیاری احساس می کنند که سطحی از انجام کار (یعنی تغییرشکل) روی نمونه های متراکم، قابلیت بازرسی محصول را ارتقا داده و یکنواختی محصولات را افزایش می دهد. متاسفانه، افزایش هزینه فرایند اجازه انجام کار بعدی را نمی دهد زیرا این کار اهداف تکنولوژی پودر را با افزایش هزینه ها خنثی می کند.
پاسخ به عملیات حرارتی پس از فشرده سازی به آلیاژ مورد نظر و روش فراوری P/M بستگی دارد. برای مثال در مورد آلیاژ BE ، Ti-6Al-4V، تنها عملیاتحرارتی موفق به کار رفته عبارت بوده است از عملیات حرارتی ساختار شکسته شده (BUS) که در آن کوئنچ از ناحیه بتا و پس از آن آنیل طولانی مدت در °C 850 (°F 1560) انجام می شود. پس از چنین عملیات حرارتی ای، میکروساختار آلیاژ، یک فاز آلفای شکسته شده در زمینه ای از بتا نشان می دهد. این میکروساختار باعث بهبود محسوس استحکام های کششی و خستگی نسبت به عملیات های حرارتی استاندارد یعنی عملیات انحلالی و پیرسازی(STA) یا عملیات انحلالی، فراپیرسازی (STOA) می شود.
کاربردها
هرچند تکنولوژی P/M تیتانیوم معمولا با صنعت هوافضا مرتبط می شود اما در دیگر صنایع نیز مورد توجه واقع شده است. این تکنولوژی در صنایع شیمیایی برای فیلترها، چفت و بستها، ابزارها و اجزای شیرها استفاده شده است. همچنین برای استفاده احتمالی در خودروها نیز مورد توجه قرار گرفته است.
عوامل هزینه ای
در حال حاضر، داده های کافی برای استفاده با اطمینان ازنمونه های متراکم پودری PA و BE در دسترس هستند. قیمت هنوز هم چالش اصلی است. فرایندهای BE P/M می توانند برای قطعات با حساسیت کمتر یعنی هنگامی که قطعاتی با چگالی غیرکامل قابل قبول هستند، مقرون به صرفه باشند.
جدول 7-4 وزن قطعه فورج شده، وزن محصول P/M وزن قطعه نهایی و در نتیجه، قابلیت پیش بینی شده برای صرفه جویی در هزینه را برای برخی قطعات تولید شده با استفاده از پودر PA و روش فراوری CCMP نشان می دهد. این تخمین ها بیان می کنند که صرفه جویی در هزینه تحقق یافته توسط فراوری P/M درمقایسه با قطعات فورج شده می تواند بین 20 و 50 درصد بسته به اندازه و پیچیدگی قطعه و کیفیت محصول تغییر نماید.
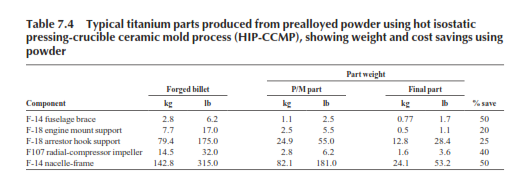
جدول 7-4 قطعات تیتانیومی تولید شده از پودر پیش آلیاژی شده با استفاده از پرسکاری ایزواستاتیک گرم- فرایند قالب سرامیکی بوته ای (HIP-CCMP) که نشان دهنده صرفه جویی در وزن و هزینه با استفاده از پودر است.
هزینه های قطعات تیتانیومی به شدت تحت تاثیر حجم تولید (که در همه کاربردهای P/M مشترک است) قرار دارد. به این عامل باید هزینه های دستیابی به خواص حساس توسط پودرهای بسیار تمیز و حتی روشه ای پرهزینه تر فشرده سازی (مانند HIP و VHP) را اضافه کرد. هزینه های پودر هنوز هم قابلیت رقابت با ریخته گری یا فراوری کار مکانیکی را برای بسیاری از کاربردهای تیتانیوم ندارند. همانطور که پیشتر گفته شد، کاهش هزینه غالبا دلیل اصلی برای فراوری P/M بجای روشهای مرسوم تولید آلیاژ است. بطور کلی، فراوری P/M می تواند برای قطعات بزرگ و پیچیده هنگامی که با روشهای تولیدی معمولی ساخته می شوند جذاب باشد، اما ریخته گری یک روش رقابتی و ثابت شده است. فقط یک هزینه بسیار بالاتر برای نمونه های متراکم PA P/M باعث می شود که آنها با قطعات ریختگی رقابت کرده و جایگزین آلیاژهای کار شده شوند. برای کاربردهای خاص که در آنها پودری با نرخ انجمادی سریع لازم است، هزینه ها احتمالا بالاتر از تکنولوژی پودر هستند. اما ممکن است از نظر عملکردی استفاده از پودر در برخی موارد توجیه پذیر باشد.
خواص مکانیکی
خواص مکانیکی قطعات P/M تیتانیومی توسط نوع پودر بکار رفته (PA یا BE) و نیز پیچیدگی روش متراکم سازی به کار رفته تعیین می شوند. در فرایندهای دمابالا و با زمان طولانی دارای نرخ تبرید آهسته مانند HIP، میکروساختار خشن تر از حد مطلوب است. هنگامی که میکروساختار توسط عملیات حرارتی یا کار مکانیکی و یا ترکیبی از این دو و دیگر روشها، ریزسازی و اصلاح می شود، خواص بهینه ای به دست می آیند.
هنگامی که چگالشی کمتر از چگالش کامل حاصل می شود خواص کششی و خزشی نیز به طور متوسط تحت تاثیر قرار می گیرند. تخلخل و آخال های کوچک در حدی که میکروساختار موثر است بر خواص استاتیک تاثیر نمی گذارند. خواص چرخه ای نظیر خستگی بطور حساسی به نقایصی مانند آخال ها یا تخلخل در قطعات P/M و نیز به میکروساختار وابسته اند.
خواص کششی برخی آلیاژهای تیتانیوم تولید شده از پودرهای BE فشرده شده توسط پرس کاری سرد و تفجوشی در شکل 7-6 نشان داده شده اند. سطوح استحکام و داکتیلیته مواد پرس کاری شده و تفجوشی شده با مواد کارشده قابل مقایسه هستند. خواص کششی و خستگی نمونه های متراکم متالورژی پودر و پیش آلیاژی تولید شده در شرایط مختلف فرآوری در جدول 7-5 نشان داده شده اند.
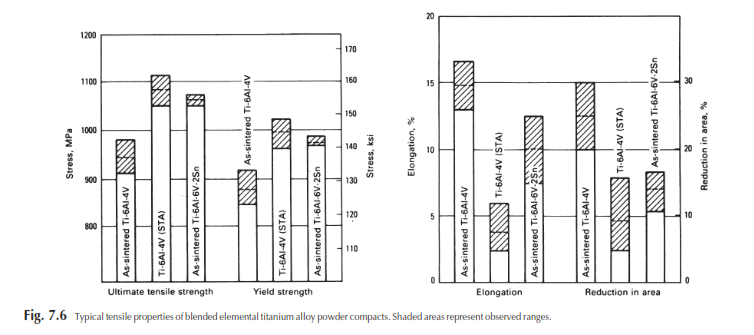
شکل 7-6 خواص کششی پودر آلیاژی تیتانیوم مخلوط شده عنصری
نواحی هاشورزده شده نشان دهنده محدوده های مشاهده شده می باشند
خواص خستگی نمونه های متراکم پودر BE و پودر PA پرسکاری شده ایزواستاتیک داغ با ماده کارشده آنیل شده در شکل 7-7 مقایسه شده اند و خواص خستگی پودر PA هنگامی که تا چگالی 100درصد و با میکروساختاری بهینه شده پرس کاری شوند با محصول آلیاژی کارشده متناظر است. نمک و تخلخل پسماند در نمونه های متراکم پودر BE عادی منجر به خواص خستگی کمتری می شود. اعمال CHIP به پودر BE و کاهش مقدار نمک استحکام خستگی را افزایش می دهد.
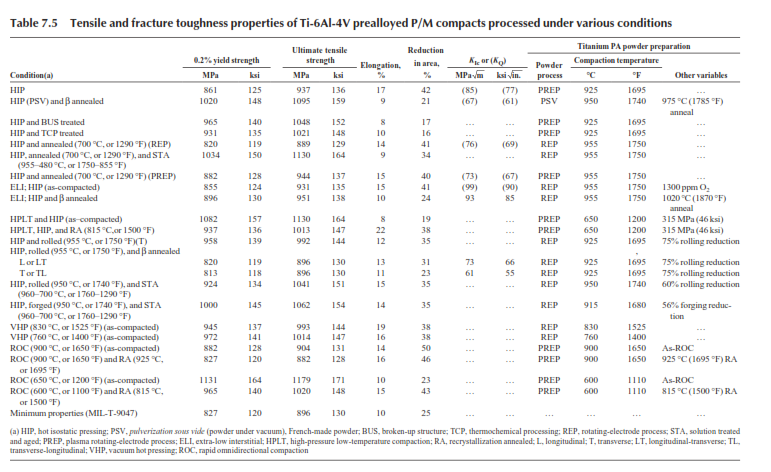
جدول 7-5 خواص کششی و چقرمگی شکست نمونه های متراکم Ti-6Al-4V پیش آلیاژی شده P/M فراوری شده تحت شرایط مختلف
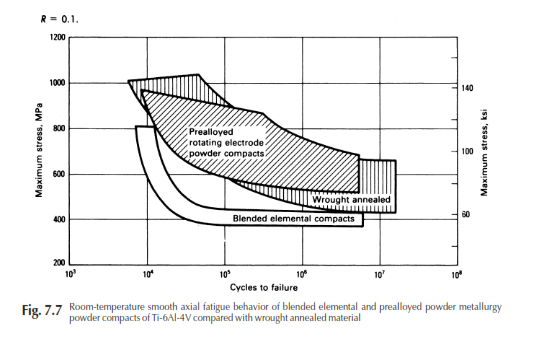
شکل 7-7 رفتار خستگی محور نمونه های متراکم متالورژی پودر Ti-6Al-4V از پودر عنصری مخلوط شده و پیش آلیاژی شده در مقایسه با ماده آنیل شده کارشده در دمای اتاق
پایان فصل هفتم