میلگرد تیتانیوم گرید 1، میلگرد تیتانیوم گرید 2، میلگرد تیتانیوم گرید 5، فورجکاری تیتانیوم
نکات کلی
قطعات فورج شده آلیاژهای تیتانیوم همگی توسط روشهای کنونی فورج کاری انجام می شوند. این روش ها شامل فورج کاری در قالب باز، در قالب بسته و چرخشی می باشد. انتخاب روش بهینه فورج کاری برپایه شکل دلخواه برگزیده شده برای قطعه و نیز خواص مکانیکی و میکروساختار دلخواه (که عمدتا خواص پس از تنظیم ترکیب آلیاژ را تعیین می کند) بستگی دارد. عملیات های فورج کاری متوالی ممکن است برای حصول نتایج دلخواه لازم باشند. برای نمونه، فورج کاری blocker-type ممکن است برای انجام مرحله لازم برای فورج کاری نهایی مرسوم در قالب بسته یک قطعه لازم باشد. یکی از اهداف اصلی فورج کاری- علاوه بر کنترل شکل- دستیابی به ترکیبی از خواص مکانیکی است که معمولا در میله یا بیلت وجود ندارد. استحکام کششی، مقاومت به خزش، استحکام خستگی و چقرمگی همگی ممکن است در قطعات فورج کاری شده بهتر از میله یا سایر اشکال باشند.
آلیاژهای تیتانیوم به شکل های کارشده مختلفی برای کاربردهای متفاوت بویژه در حوزه هوافضا فورج کاری می شوند. فورج کاری در این حوزه معمولا با استفاده از قالب انجام می شود. هرچند فورج کاری آلیاژهای تیتانیوم دشوار است اما به دشواری فلزات دیرگداز و سوپرآلیاژها نیست. پیشینه کار و پارامترهای فورج کاری بکار رفته در فورج کاری آلیاژهای تیتانیوم تاثیر زیادی بر میکروساختار و خواص قطعات نهایی دارد. متعاقبا، فورج کاری متوالی و عملیات حرارتی بعد از آن را می توان برای کنترل میکروساختار و خواص نهایی محصول بکار برد. در تولید قطعات فورجکاری شده تیتانیوم، شکل های غالب بکار رفته، بیلت و میله هستند که توسط فرایندهای کارگرم اولیه تولید شده اند. به ندرت، شمش آلیاژی تیتانیوم بطور مستقیم به شکل قطعات نهایی فورج می شود. حتی در این صورت نیز، فورج کاری چند مرحله ای برای ریزسازی ساختار شمش استفاده می شود. الزامات مربوط به فورج کاری معمولا توسط فورج کننده تعیین می شوند یا توسط مذاکره با تامین کننده فلز و مشتری نهایی قطعه فورج شده تعیین می گردند.
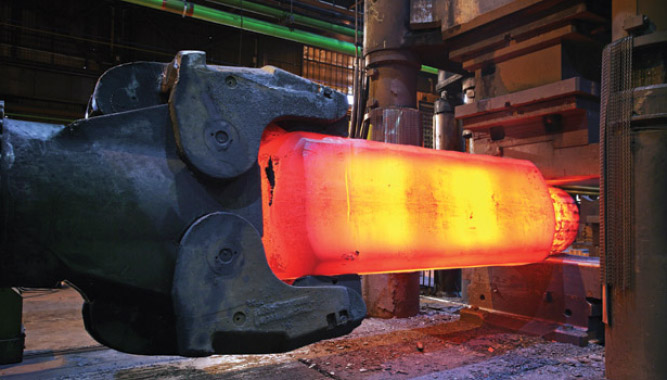
آماده سازی سطح بیلت یا شمش آلیاژ تیتانیوم مهم است. آماده سازی مناسب نه تنها برای عملکرد رضایتبخش ماده در فورج کاری بعدی بلکه برای تست غیرمخربی که غالبا روی قطعه فورج انجام می شود نیز بعنوان بخش مهم اطمینان از کیفیت کلی قطعه ضروری است.
دمایی که قطعه فورج کاری شده تیتانیومی در معرض آن قرار می گیرد نیز علاوه بر میکروساختار و خواص مکانیکی نهایی قطعه برای مشخصات تیتانیوم فورج شده مهم است. محدود کردن آلیاژهای تیتانیوم در قرارگیری در معرض دماهای بالا برای جلوگیری از تشکیل پوسته و کمینه سازی تشکیل پوسته آلفا بدلیل برهمکنش با عناصر بین نشین اکسیژن و نیتروژن، مفید است.
برای هر آلیاژ تیتانیوم معین، الزامات فشار برای فورج کاری در یک محدوده وسیع متغیر است که به ترکیب واقعی آلیاژ، فرایند فورج کاری بعلاوه دما، نرخ کرنش و دیگر عوامل فرایند فورج کاری وابسته است. شکل 5-1 تفاوت تنش سیلان مربوط به تیتانیوم CP و برخی آلیاژها را نشان می دهد. به تنش بسیار بالاتر لازم برای تعییرشکل اساسی تیتانیوم و آلیاژهای آن در مقایسه با فولاد توجه کنید.
شکل 5-1 تنش سیلان برخی آلیاژهای مرسوم تیتانیوم در مقایسه با فولاد (AISI 4340).
الزامات مربوط به فشار فورج کاری به تنش سیلان مربوط هستند و مطابق با رفتار تنش سیلان فلزات با دما تغییر می کنند (شکل 5-2).
شکل 5-2 تاثیر دمای فورج کاری بر فشار فورجکاری مربوط به برخی آلیاژهای تیتانیوم و فولاد (AISI 4340).
فورج کاری در قالب
هنگامی که حجم و/یا اندازه ماده، استفاده از قالبهای بسته را برای یک کاربرد خاص تضمین نمی کند فورجکاری در قالب باز برای تولید برخی شکل های تیتانیومی بکار برده می شود. اما فورج کاری در قالب بسته برای ایجاد بالاترین مقدار آلیاژهای تیتانیوم فورج شده بکار می رود. فورج کاری در قالب بسته را می توان بعنوان blocker type (مجموعه تک قالب)، متداول (مجموعه دو یا چند قالب) یا high definition (مجموعه دو یا چند قالب) دسته بندی کرد. فورجکاری در قالب دقیق نیز انجام می شود که در آن معمولا از روشهای فورجکاری قالب داغ/همدما استفاده می شود. قطعات فورج شده در قالب بسته هزینه بیشتری نسبت به blocker type دارند اما بدلیل هزینه کمتر ماشینکاری و کنترل بهتر خواص، افزایش قیمت توجیه پذیر است. قالب های بکار رفته قطعات فورج شده تیتانیومی برای تسهیل فرایند فورج کاری و کاهش سردی سطح و اتلاف دمای فلز حرارت می بینند که می تواند منجر به پرشدن ناکافی قالب و/یا ترک خوردگی بیش ازحد قطعه فورج شده می شود. فورجکاری در قالب داغ/همدما باعث بردن دمای قالب به سطوح بالاتر می شود.
فورج کاری، بیش از یک فرایند شکل سازی است. کلید موفقیت در فورج کاری و عملیات حرارتی، دمای تحول بتاست. اساسا دو روش عمده برای فورج کاری آلیاژهای تیتانیوم وجود دارد:
در این روشها برای حصول خواص دلخواه در آلیاژهای تجاری می توان تغییراتی را انجام داد. در آلیاژهای کاملا پایدارسازی شده بتا، کنترل فاز آلفا با تغییر پارامترهای فورج کاری مسئله ای محسوب نمی شود. آلیاژهای کاملا پایدارسازی شده بتا معمولا در بالای دمای تحول بتای آلیاژ فورج می شوند. آلیاژهای آلفا، شبه آلفا و آلفا- بتا غالبا توسط تغییراتی در فرایند فورج کاری (و عملیات حرارتی) اصلاح می شوند.
فورج کاری متداول آلفا- بتا به بهترین شیوه به این شکل تعریف می شود که یک فرایند فورج کاری ای است که در آن، کل تغییرشکل یا بیشتر آن در زیر دمای تحول بتا انجام می شود. فازهای آلفا و بتا همیشه در میکروساختار وجود خواهند داشت. مقادیر نسبی هر فاز موجود در حین فرایند فورجکاری، تابعی از فاصله دمایی از دمای تحول بتاست. ساختارهای ناشی از فورج کاری آلفا- بتا توسط فاز آلفای تغییرشکل یافته یا هم محور اولیه (آلفای موجود در حین فرایند فورج کاری) و فاز بتای استحاله شده مشخص می شوند.
شکل 5-3 موقعیت های ممکن برای دمای فورج کاری در قالب و/یا دماهای عملیات حرارتی یک آلیاژ آلفا-بتا نظیر Ti-6Al-4V را بطور تصویری نشان می دهد. هرچه دمای فراوری در ناحیه آلفا+بتا بیشتر باشد بتای بیشتری برای استحاله در تبرید موجود خواهد بود. در کوئنچ از بالای دمای تحول بتا، یک ساختار کاملا استحاله شده سوزنی پدید می آید. شکل دقیق آلفای گلبولی (هم محور) و ساختارهای بتای استحاله شده ایجاد شده توسط فراوری به موقعیت دقیق تحول بتا که در یک آلیاژ معین، از یک نوبت به نوبت دیگر متفاوت بوده و نیز به میزان و ماهیت تغییرشکل ایجادشده علاوه بر نرخ تبرید بستگی دارد. دماهای حقیقی فورج کاری بکار رفته برپایه تجربه و میکروساختار مطلوب تعیین می شوند. جدول 5-1 دماهای پیشنهادی برای تعدادی از آلیاژهای تیتانیوم آلفا، آلفا- بتا و بتای فورج شده را نشان می دهد. بعنوان یک راهنمای کاری، دماهای تحول بتا منهای °C 28 (°F 50) برای قطعات فورج شده و دمای تحول بتا بعلاوه °C 42 (°F 75) پیشنهاد می شوند. فورجکاری در قالب سوپرپلاستیک همدما را می توان در دماهایی متفاوت از این پیشنهادها انجام داد.
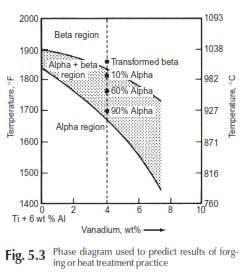
شکل 5-3 نمودار فازی بکار رفته برای پیش بینی نتایج فورج کاری یا فرایند عملیات حرارتی.
فورج کاری بتا یک روش فورج کاری است که در آن، تغییرشکل آلیاژ در بالای دمای تحول بتا انجام می شود. در عملیات تجاری، فورج کاری بتا در حقیقت شامل تغییرشکل اولیه در بالای دمای تحول بتاست اما پرداخت نهایی با مقادیر کنترل شده تغییرشکل در زیر دمای تحول بتای آلیاژ انجام می شود. در فورج کاری بتا، بدلیل دمای بالا و تغییرشکل دانه های جدید توسط تبلور مجدد تاثیرات کار مکانیکی (تغییرشکل) ضرورتا انباشته نمی شوند زیرا در هر مرتبه، دمای تحول بتا در فورج کاری افزایش می یابد. فورج کاری بتا بویژه فورج کاری آلیاژهای آلفا و آلفا- بتا منجر به کاهشهای محسوس در فشارهای فورج کاری و تمایل کمتر به ترک خوردگی بیلت در حین فورج کاری می شود. از طرف دیگر، کار مکانیکی غیریکنواخت، رشد دانه بیش از حد و/یا ساختارهای کارشده ضعیف که منجر به خواص مکانیکی بسیار متغیر می شوند می توانند ناشی از اجرای نامناسب فورج کاری بتا باشند.
جدول 5-1 محدوده های دمایی پیشنهاد شده برای آلیاژهای تیتانیوم فورج کاری شده
اندازه مقطع در فورج کاری در قالب مهم است و تعداد عملیات های مکانیکی نیز با اهمیت است. فورج کاری معمولی در قالب ممکن است به دو یا سه عملیات مکانیکی نیاز داشته باشد درحالیکه فورج کاری همدما ممکن است فقط به یک مورد عملیات نیاز داشته باشد. طرح واره نشان دهنده توالی عملیات حرارتی در شکل 5-4 نشان داده شده است. عملیات حرارتی انحلالی فرصتی برای اصلاح میکروساختار فراهم می کند درحالیکه چرخه پیرسازی، ساختارهای بتای استحاله شده را برای یک پراکندگی بهینه اصلاح می نماید.
شکل 5-4 طرح واره یک فورج کاری متداول در قالب و عملیات حرارتی پس از آن برای ایجاد یک ساختار آلفا- بتا
ساختارهای نامطلوب (آلفا در مرزدانه، رگه بتا، اسپاگتی یا آلفای کشیده شده) می توانند با در تکامل خواص بهینه تداخل ایجاد کنند. متعاقبا، کنترل میکروساختاری برای فراوری موفقیت آمیز آلیاژهای تیتانیوم ضروری است.
ساختارهای شمش تیتانیوم می توانند به محصول نهایی منتقل شوند. فراوری بتا، علیرغم اثرات مخرب آن بر خواص مکانیکی می تواند از قیمت قطعه فورج شده بکاهد درحالیکه فورج کاری همدما باعث کاهش فشارهای فورج کاری و/یا بهبود پرکنندگی قالب می شود. فورجکاری بتای همدما در تولید قطعاتی با مقاومت خزشی بالاتر از آلیاژهای تیتانیوم بکار می رود. برخی آلیاژها در دهه های پایانی قرن بیستم با هدف انجام فورج کاری بتا برای پیشرفت مطلوب در خواص مکانیکی نهایی مورد نظر توسعه یافتند (فصل 12 بحث بیشتری درباره تاثیرات فورج کاری بر خواص ارائه می دهد).
بازگرمایش آلیاژهای تیتانیوم آلفا- بتا پس از کار گرم می تواند بطور قابل توجهی میکروساختار را تغییر دهد. توجه کافی به تحول صحیح میکروساختار در طی مراحل عملیات حرارتی لازم است. میکروساختارهای ظاهرا مشابه ممکن است باعث سطوح یکسانی از خواص مکانیکی نشوند. عملیات حرارتی انحلالی و پیرسازی ساختارهایی که روی آنها کار انجام نشده یا کار انجام شده کافی نبوده باعث استحکام یا چقرمگی بهینه در آلیاژهای تیتانیوم نخواهد شد.
تاثیرات فراوریهای مختلف ترمومکانیکی بر خواص مکانیکی و ساختارهای آلیاژهای تیتانیوم آلفا-بتا نظیر Ti-6Al-4V، Ti-6Al-6V-2Sn-4Zr-6Mo را می توان برای تشریح تاثیرات این فراوریها بر خواص بکار برد. جدول 5-2 چهار فرایند ترمومکانیکی را که باعث ترکیبات بهینه ای از خواص یعنی استحکام کششی عالی، استحکام خستگی شیاری، استحکام خستگی چرخه ای و چقرمگی شکست خوب تا عالی در قطعات فورج شده آلیاژ آلفا-بتای Ti-6Al-4V شد خلاصه می کند. همچنین در این جدول، سه فرایندی که باعث خواص کمتر از معمول شدند آمده است.
جدول 5-2 فرایندهای ترمومکانیکی برای ایجاد ترکیباتی مختلف از خواص در یک آلیاژ تیتانیوم آلفا- بتا (Ti-6Al-4V)
میکروساختارهای Ti-6Al-4V نشان داده شده در شکل 5-5 مربوط به فرایندهایی که ترکیب هایی مناسب از خواص و نیز دو فرایند که ترکیباتی نامناسب از خواص ایجاد کردند می باشند. توجه کنید که تقاوت محسوس در میکروساختار در محصول نهایی یکسان در ترکیب با خواص حاصل نشان می دهد که کنترل فراوری ترمومکانیکی می تواند میکروساختارها و خواص نهایی مربوطه قطعات فورج شده را کنترل کند.
شکل 5-6 نتایج یک مطالعه گسترده روی فورج کاری آلفا- بتا را به ازای فورج کاری مربوط به چند آلیاژ تیتانیوم نشان می دهد. هرچند استحکام تسلیم پس از فورج کاری بتا همواره به میزان مقدار استحکام تسلیم پس از فورج کاری آلفا- بتا نبود اما مقادیر استحکام کششی شیاری و چقرمگی شکست مربوط به ماده فورج شده بتا بدون هیچ تناقضی بالاتر بود.
آلیاژهای فورج شده بتا تمایل به داشتن یک میکروساختار بتای استحاله شده یا سوزنی دارند که در آن، آلیاژهای آلفا-بتای فورج شده یک ساختار هم محور نشان دهند. این ساختار هم محور در شکل 5-5 الف نشان داده شده است. هر نوع میکروساختار دارای مزایا و معایبی است (بعنوان نمونه سوزنی در برابر هم محور) چرا که هر ساختار قابلیت های خاص خود را داراست. جدول 5-3 مزایای نسبی میکروساختارهای هم محور و سوزنی را نشان میدهد.
شکل 5-5 میکروساختار مربوط به ترکیبات خواص حاصل از فورج کاری یک آلیاژ تیتانیوم آلفا- بتا (Ti-6Al-4V).
الف- 6درصد آلفای هم محور بعلاوه آلفای پلاکتی ریز در آلفا- بتایTi-6Al-4V فورج شده و آنیل شده در °C 705 (°F 1300) بمدت 2 ساعت
ب- ازدیاد طول یافته به میزان 23 درصد، آلفای اولیه بطور جزئی شکسته شده بعلاوه آلفای مرزدانه ای در Ti-6Al-4V، آلفا- بتای فورج شده و کوئنچ شده در آب و سپس آنیل شده در °C 705 بمدت 2 ساعت و خنک کاری شده در هوا
ج- صفحات آلفای (اسپاگتی) توده ای به میزان 25 درصد بعلاوه آلفای پلاکتی بسیار ریز در Ti-6Al-4V آلفا- بتای فورج شده از یک ساختار اولیه و بعد از آن عملیات انحلالی شده بمدت 1 ساعت و °C 955 (°F 1750) و بازآنیل شده بمدت 2 ساعت در °C 705
د- ساختار سبدی- موجی در بتایTi-6Al-4V فورج شده و سپس آهسته سردشده و بعد از آن، آنیل شده در °C 705 بمدت 2 ساعت.
شکل 5-6 مقایسه خواص مکانیکی بدست آمده در آلیاژهای تیتانیومی شبه آلفا، آلفا- بتا و بتای فورج شده.
جدول 5-3 مزایای نسبی میکروساختارهای آلیاژ تیتانیوم هم محور و سوزنی
فورج کاری تیتانیوم در قالب دقیق
روش جایگزین فورج کاری در قالب برای تیتانیم شامل استفاده از روشهای فورج کاری هم دمای دقیق (گاهی سوپرپلاستیک) می شود. روش های فورج کاری دقیق باعث تولید شکلی از محصول می شود که به ماشینکاری بسیار کمتری برای دستیابی به ابعاد نهایی قطعه نیاز دارد. تیتانیوم فورج کاری شده دقیق یک عامل برجسته در استفاده از تیتانیوم در حوزه های هواپیما و توربینهای گازی است. بیشتر تیتانیوم فورج کاری شده دقیق به شکل محصول نزدیک به شکل نهایی (NNS) تولید می شود بدان معنا که قطعه فورج شده به ابعاد نهایی نزدیک است اما به مقداری ماشینکاری نیاز دارد.
فورج کاری هم دما فرایندی است که در آن، ماده فورج شده در شرایط دمای ثابت نگهداری شده و در نتیجه دستخوش نوسانات دمایی گرمایش و تبرید نمی شود. این نوسانات دمایی در فورج کاری معمولی چندین مرتبه تجربه می شوند. پرسهای فورج کاری مشابهی با فورج کاری در قالب معمولی ممکن است کار روند هرچند ممکن است پرسی نیز به فورج کاری هم دما اختصاص یابد. اما در قالبهای بکار رفته تفاوتی وجود دارد. مواد بلوک قالب همواره یک چالش در توسعه فرایندهای فورج کاری هم دما بحساب می آمده اند. فورج کاری هم دما را می توان در حوزه آلفا- بتا یا فاز بتا انجام داد. میکروساختارها را می توان کاملا بدقت کنترل کرد. در نتیجه، یکنواختی خواص باید بهتر خواص حاصل از فورج کاری معمولی باشد. ظهور آلیاژهای بتا و شبه پایدار بتا با قابلیت فورج ساده تر (نظیر Ti-10V-2Fe-3Al) به تبدیل شدن فورج کاری دقیق NNS هم دمای آلیاژهای تیتانیوم به یک فرایند مرسوم کمک کرد که البته برای آلیاژهای مناسب با هزینه بالاتری انجام شد.
مفهوم NNS پایه انگیزشی برای فرایند فورج کاری هم دما بوده است. این به معنای میل برای کمینه سازی مقدار ماشینکاری پرهزینه ای است که باید برای تولید قطعه پرداخت شده انجام شود. همچنین به معنای میل برای نداشتن هزینه ای تحت نام مواد قراضه یا تراشه است. هرچند فورج کاری هم دمای آلیاژ آلفا- بتا آسان است اما هزینه فرایند و ابزارها، شکست ناگهانی قالب و سایر مشکلات مربوط به دماهای بالای فرایند باعث ایجاد ترکیبی برای کمینه سازی استفاده از آن در آلیاژهای آلفا- بتای مرسوم شده است. آلیاژهای آلفا- بتای برگزیده نظیر Ti-6Al-4V و Ti-6Al-6V-2Sn به شکل NNS تولید می شوند.
هرچند در ابتدا فورج کاری هم دما به ماده بیلت اعمال می شد اما اکنون این فرایند به شمشها P/M یا پیش شکلها نیز اعمال شده است.(یک پیش شکل، عبارتست از یک شکل تثبیت شده حاصل از P/M که دارای شکلی طراحی شده تقریبا شبیه به شکل نهایی برای بیشینه سازی قابلیت پرکردن قالب در فرایند فورج کاری و برای کمینه سازی فشارها و ماده اضافی است.)
شکل دهی تیتانیوم
نکات کلی. شکل دهی تیتانیوم دشوارتر از فولاد یا آلیاژهای آلومینیوم است و آلیاژهای تیتانیوم نسبت به فولاد یا آلیاژهای آلومینیوم دارای مشخصات شکل دهی با قابلیت پیش بینی کمتری هستند. اما تا زمانیکه محدودیتهای مشخص درباره آلیاژهای تیتانیوم شناخته شوند و دستورالعملهای ایجادشده برای شکلدهی داغ و سرد پیروی شوند، تیتانیوم و آلیاژهای تیتانیوم را می توان با موفقیت به شکل قطعات پیچیده شکل دهی کرد.
تیتانیوم و آلیاژهای تیتانیوم را در ماشینهای استاندارد تا تلرانسهایی شبیه به تلرانسهای حاصل در شکل دهی فولاد ضدزنگ می توان شکل دهی کرد. چون تیتانیوم میزان زیادی بازگشت در شکل دهی سرد نشان می دهد تیتانیوم را باید بشدت فرا شکل دهی کرد یا پس از شکلدهی سرد روی آن سایزینگ گرم باید انجام داد. اما برای کاهش تاثیر بازگشت روی دقت و برای حصول مزیت داکتیلیته بیشتر، عمده قطعات تیتانیومی توسط شکلدهی داغ یا پیش شکل سازی سرد و سپس سایزینگ داغ ساخته می شوند.
شکلدهی آلیاژهای بتا بطور کلی ساده تر از آلیاژهای آلفا و آلفا- بتا می باشد. توجه زیادی در دهه گذشته به قابلیت استفاده از آلیاژهای ورق بتا نظیر Ti-15V-3Sn-3Cr-3Al شده است.
شکل دهی داغ و سرد تیتانیوم
ورق های نازک و ضخیم حاصل از تیتانیوم و آلیاژهای تیتانیوم توسط شکل دهی سرد دستخوش کرنش سختی می شوند. این موضوع، معمولا استحکام کششی و تسلیم را افزایش داده و سبب کاهش اندک در داکتیلیته می شود. شکل دهی داغ بر خواص نهایی تاثیر زیادی ندارد. شکلدهی در دماهایی از °C 595 تا 815 (°F 1100 تا 1500) باعث می شود ماده با سهولت بیشتری تغییرشکل می دهد و همزمان، باعث آزادسازی تنش در ماده تغییرشکل یافته و نیز میزان بازگشت را کمینه می کند. تیتانیوم تمایل به خزش در دماهای بالا دارد. نگه داشتن تحت بار در دمای شکل دهی (شکل دهی خزشی) یک جایگزین برای دستیابی به شکل مطلوب بدون نیاز به جبران بازگشت شدید می باشد.
در همه فرایندهای شکل دهی، تیتانیوم و آلیاژهای تیتانیوم در معرض اثر باوشینگر هستند. این پدیده، افت در استحکام تسلیم در یک جهت بارگذاری است که توسط افزایش استحکام کششی در جهت دیگر بدلیل کرنش سختی همراه می شود. اثر باوشینگر در دمای اتاق مشهودتر است. تغییرشکل پلاستیک (1 تا 5 درصد ازدیاد طول کششی) در دمای اتاق همواره باعث افت محسوس در استحکام تسلیم فشاری بدون توجه به عملیات حرارتی ابتدایی یا استحکام آلیاژها می شود. در 2درصد کرنش کششی، استحکام های تسلیم فشاری Ti-4Al-3Mo-1V و Ti-6Al-4V به کمتر از نصف مقادیر مربوط به ماده عملیات انحلالی شده کاهش می یابد. افزایش دما، اثر باوشینگر را کاهش می دهد؛ آزادسازی تنش کامل بصورت گرمایی، این اثر را کاملا از بین می برد. دماهایی به کمی دمای پیرسازی، غالب اثر باوشینگر را در آلیاژهای تیتانیوم عملیات انحلالی شده از بین می برد. گرمایش یا تغییرشکل پلاستیک در دمایی بالاتر از پیرسازی نرمال برای Ti-6Al-4V عملیات انحلالی شده باعث رخ دادن فراپیرسازی می شود و در نتیجه، کل خواص مکانیکی کاهش می یابند.
تیتانیوم خالص تجاری و بیشتر آلیاژهای تیتانیوم داکتیل (نظیر Ti-15V-3Sn-3Cr-3Al و Ti-3Al-8V-6Cr-4Zr-4Mo) را می توان به شکل سرد به میزان محدودی تغییرشکل داد. آلیاژ سوپرآلفای Ti-8Al-1Mo-1V را می توان توسط روشهای استاندارد تا شکلهای نه چندان عمیق شکل دهی نمود. شکلدهی سرد دیگر آلیاژها بطور کلی منجر به بازگشت بیش از حد شده و نیاز به آزادسازی تنش بین عملیاتهای مورد نظر دارد. برای شکل دهی سرد همه آلیاژهای تیتانیوم، قابلیت شکل دهی در سرعتهای شکل دهی پائین، بهترین نتیجه را در پی دارد.
برای بهبود دقت، معمولا پس از شکلدهی سرد، سایزینگ داغ انجام می شود. سایزینگ داغ و آزادسازی تنش برای کاهش تنش و جلوگیری از ترک خوردگی تاخیری و خوردگی تنشی مورد نیاز هستند. آزادسازی تنش نیز برای ذخیره سازی تنش تسلیم فشاری لازم است. سایزینگ داغ غالبا با آزادسازی تنش ترکیب می شود. عملیات های حرارتی مربوط به تیتانیوم CP و برخی آلیاژهای تیتانیوم در جدول 5-4 ارائه شده اند. اطلاعات بیشتر در فصل 8 ارائه شده است.
جدول 5-4 عملیات های برگزیده آزادسازی تنش مربوط به تیتانیوم و برخی آلیاژهای تیتانیوم
گرمایش آلیاژهای تیتانیوم باعث افزایش قابلیت شکل دهی و کاهش بازگشت شده و از تغییرات کمتر در استحکام تسلیم بهره می برد و باعث تغییرشکل بیشینه و آنیل کمینه بین عملیات های شکل دهی می شود. شکل دهی شدید باید در قالبهای داغ و مواد پیشگرم شده انجام شود.
بالاترین بهبود در داکتیلیته و یکنواختی خواص برای بیشتر آلیاژهای تیتانیوم در دماهایی بالاتر °C 540 (°F 1000) حاصل می شود. در دماهای بالاتر، برخی آلیاژها پدیده ای بنام سوپرپلاستیسیته نشان می دهند. رفتار سوپرپلاستیک بطور گسترده ای در شکل دهی و اتصال دهی تیتانیوم استفاده شده است. در بالاتر از دمای تقریبی °C 650 (°F 1200)، پیشنهاد می شود که شکل دهی در یک اتمسفر محافظ برای کمینه سازی اکسیداسیون انجام شود. جدول 5-5 برخی دماهای مربوط به شکل دهی داغ تیتانیوم و آلیاژهای تیتانیوم برگزیده را فهرست می کند. برای کاربردهایی که در آن بیشینه داکتیلیته لازم است، معمولا از دماهایی کمتر از °C 315 تا 425 (°F 600 تا 800) اجتناب می شود.
جدول 5-5 دماهای شکل دهی داغ تیتانیوم و برخی آلیاژهای تیتانیوم
درحالیکه برای جلوگیری از تخریب محسوس خواص مکانیکی، بطور کلی دما باید زیر °C 815 (°F 1500) حفظ شود، شکل دهی سوپرپلاستیک در °C 870 تا 925 (°F 1600 تا 1700) برای برخی آلیاژهای آلفا-بتا نظیر Ti-6Al-4V انجام می شود. باید مراقب بود که دما از دمای تحول بتا فراتر نرود چرا که خواص تحت تاثیر قرار خواهند گرفت. بدلیل امکان ایجاد پوسته و تردی در شکل دهی داغ آلیاژهای تیتانیوم در دماهایی بیش از °C 540 (°F 1000)، زمان قرارگیری در دمای بالا باید محدود باشد. بطور کلی، برای گرمایش در هوا، طولانی ترین زمان مجاز در °C 705 (°F 1300) 1 ساعت و در °C 870 (°F 1600) فقط 20 دقیقه است. غالبا از گاز آرگون بعنوان اتمسفری برای شکل دهی پلاستیک در انتهای محدوده دمایی مجاز استفاده می شود.
پیرسازی در شکلدهی
برخی دماهای شکل دهی داغ برای پیرسازی آلیاژهای تیتانیوم بحد کافی زیاد هستند. آلیاژهای قابل عملیات حرارتی بتا و آلفا- بتا معمولا باید پس از شکل دهی داغ دوباره تحت عملیات حرارتی قرار بگیرند. آلیاژهای آلفا- بتا را نباید در بالای دمای تحول بتا شکل دهی کرد. بدلیل پیرسازی، تشکیل پوسته و تردی و نیز هزینه بالاتر شکل دهی در دماهای بالا، شکل دهی داغ معمولا در کمترین دمای ممکن که باعث تغییرشکل دلخواه می شود صورت می گیرد.
شکل دهی سوپرپلاستیک
شکل دهی سوپرپلاستیک تیتانیوم، در حال حاضر بطور گسترده ای در صنعت هواپیمایی و به میزان کمتری در صنعت توربین گازی استفاده می شود. مزایای شکل دهی سوپرپلاستیک در مقایسه با سایر روشها عبارتند از:
-
قطعات بسیار پیچیده ای را می توان شکل دهی کرد.
-
سازه های سبکتر و با کارامدی بیشتر را می توان طراحی و شکل دهی نمود.
-
شکل دهی در یک عملیات تک مرحلهای انجام می شود.
-
ممکن است بتوان بیش از یک قطعه در یک چرخه دستگاه تولید کرد.
-
فشار (نیرو) بطور یکنواختی به همه نواحی قطعه کار اعمال می شود.
شکل دهی سوپرپلاستیک دارای محدودیت هایی نیز هست که عبارتند از:
مستحکم ترین آلیاژ تیتانیوم سوپرپلاستیک، آلیاژ آلفا-بتای Ti-6Al-4V است. ویژگی شکلدهی سوپرپلاستیک تیتانیوم نتیجه کار بر روی این آلیاژ است هرچند بسیار از آلیاژها رفتار سوپرپلاستیک نشان می دهند. متغیرهای متالورژیکی که بر رفتار سوپرپلاستیک در آلیاژهای تیتانیوم اثر می گذارند عبارتند از اندازه دانه، توزیع اندازه دانه، مشخصات نفوذی اتمهای پایه و آلیاژ، نسبت مقادیر فاز آلفا به بتا و بافت آلیاژی که تحت شکل دهی سوپرپلاستیک قرار می گیرد. ترکیب آلیاژ دارای تاثیر بسیار قابل توجهی بر رفتار سوپرپلاستیک در آلیاژهای تیتانیوم می باشد. شکل دهی سوپرپلاستیک با اتصال دهی نفوذی برای ایجاد یک فرایند انعطاف پذیر ترکیب می شود تا نیاز به جوشکاری و لحیم کاری قطعات پیچیده را حذف نماید (جزئیات بیشتر را می توان در فصل 9 یافت).
کشش عمیق و دیگر فرایندهای شکل دهی
کشش عمیق آلیاژهای تیتانیوم بطور گسترده ای توسط شکل دهی سوپرپلاستیک جایگزین شده اند. تیتانیوم را بطور داغ می توان بسیار عمیقتر کشید و شکل دهی های دشوارتری را می توان نسبت به حالت سرد انجام داد که در تطابق با اطلاعات کلی بدست آمده درباره آلیاژهای تیتانیوم است. بطور کلی، عمق کشش به ترکیب، شکل قطعه کار، شعاعهای لازم، دمای شکلدهی، طراحی قالب و روانساز بستگی دارد. دماهایی تا °C 675(°F 1250) در کشش عمیق بکار رفته اند.
آلیاژهای تیتانیوم را با فرایندهای دیگری نظیر شکل دهی پرس برک، شکل دهی اسپینینگ، شکل دهی با بالشتک لاستیکی و شکل دهی خزشی نیز می توان شکل دهی نمود.